3D printing has thoroughly overhauled the prosthetics industry. We write about 3D printed prosthetic devices all the time, as they become cheaper, more functional, more attractive and overall better. What if, however, prosthetics suddenly became obsolete? It’s not likely to happen anytime soon, but the seemingly impossible – regrowing an entire missing body part – may be possible in as little as three years, according to researchers at Morriston Hospital in Swansea, Wales.
“In simple terms, we’re trying to grow new tissue using human cells,” said Professor Iain Whitaker, consultant plastic surgeon at the hospital’s Welsh Centre for Burns and Plastic Surgery. “We want to try and help people who were born with defects, or who have lost parts of their ear or nose as a result of trauma or cancer. We are using human cells, growing them up, to combine them with a printable material, 3D print them and implant them into the human body.”
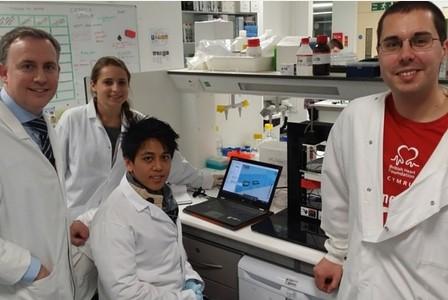
(L to R) Professor Iain Whitaker; Zita Jessop, Jasper Sison and Dr Daniel Thomas (South Wales Evening Post)
Whitaker also serves as the chairman of plastic and reconstructive surgery at Swansea University, which has made some major strides in 3D bioprinting this year, including the development of bioprinted tissue for the purpose of pharmaceutical research and, only a few months later, a bioprinted tissue scaffold. The work being developed at Morriston Hospital is another step towards 3D printing entire body parts out of human cells.
The process would involve taking a small sample of cartilage from a patient and placing it into an incubator, where the cells will grow and multiply over the course of several weeks, until they are ready to be combined with a liquid formula that will create a jelly-like structure. That jelly-like material is then used to 3D print the missing body part, such as an ear or nose, using scans taken from the patient. The printed part is then strengthened with reagents and placed back into the incubator, where it is given nutrients that will enable the cells to grow and form their own cartilage.
“This work is at the relatively early stages of development and requires combining many areas of expertise; but we already have proof of concept that human cells can survive within the printable structures we’ve made so far, and will survive the printing process,” said Whitaker. “We’re currently working on growing up large numbers of cells in order to print larger constructs, and undertake a number of tests to ensure it will be stable enough to be used to implant into a patient.”
The process will need to be tested on animals before human patients can be involved, and an ethics review will be required, but the team hopes to be able to start clinical trials in as little as 3 or 4 years. The prosthetics industry can relax, as the process is being developed for cartilage-based parts, mainly facial features, that cannot be replaced by prosthetic devices. As Whitaker said, however, this is only the first step, and once the process is finalized and approved, things will likely move very quickly.
“The good news in the future is, if our research is successful, within two months you’d be able to recreate a body part which was not there without having to resort to taking it from another part of the body which would cause another defect or scar elsewhere,” Whitaker added.
Imagine losing your nose in a terrible accident, and, within two months, having it replaced with your own tissue. Disfiguring injuries will no longer carry sentences of lifetime, or even year-long, embarrassment. I read every day about the myriad ways in which 3D printing is changing medicine, but when I hear about permanent, irreversible, and traumatic conditions being reduced to temporary setbacks, it still gives me the chills. Let’s hear your thoughts on this story in the 3D Printed Cartilage forum on 3DPB.com.
Subscribe to Our Email Newsletter
Stay up-to-date on all the latest news from the 3D printing industry and receive information and offers from third party vendors.
Print Services
Upload your 3D Models and get them printed quickly and efficiently.
You May Also Like
Nikon SLM Solutions Sells SLM 500 to Primary Weapon Systems to Expand Suppressor Production
Primary Weapons Systems (PWS) is a Boise, Idaho-based manufacturer of suppressors, firearms, and related components. A subsidiary of Vigilant Gear and a sister company to aftermarket Glock slide manufacturer Lone...
3DPOD 261: Tooling and Cooling for AM with Jason Murphy, NXC MFG
Jason Murphy´s NXC MFG (Next Chapter Manufacturing) is not a generalist service; instead, the company specializes in making tooling. Using LPBF and binder jet, the company produces some of the...
HP and Firestorm Labs Form Partnership to Use Multi Jet Fusion 3D Printers in Deployable Factories
HP Inc., maker of a range of additive manufacturing (AM) solutions including the Multi Jet Fusion (MJF) ecosystem, has announced a partnership with Firestorm Labs, a developer of containerized, deployable...
3D Printing News Briefs, July 2, 2025: Copper Alloys, Defense Manufacturing, & More
We’re starting off with metals in today’s 3D Printing News Briefs, as Farsoon has unveiled a large-scale AM solution for copper alloys, and Meltio used its wire-laser metal solution to...