Metal 3D printing is becoming invaluable for many manufacturers today worldwide, and the research regarding processes and materials continues as researchers from both Singapore Institute of Manufacturing Technology and Nanyang Technological University explore metal powders being used in electron beam melting (EBM) technology today in ‘Additively manufactured CoCrFeNiMn high-entropy alloy via pre-alloyed powder.’
Most studies regarding serious manufacturing practices and their interest in 3D printing with metal center around the best ways to produce strong, complex geometries. Here, the authors review whether CoCrFeNiMn high entropy alloy (HEA) parts produced through EBM—very similar to the popular selective laser sintering (SLS) process—is a realistic improvement over conventional casting techniques.
CoCrFeNiMn is known as an equiatomic alloy powder made through vacuum induction via atomization with argon gas. As a single face-centered-cubic (FCC) crystal structure, CoCrFeNiMn has been the focus of a wide variety of research throughout the years due to:
- Strong mechanical properties
- Corrosion resistance
- Wear resistance
- Excellent ductility
The scientists point out that while HEAS like CoCrFeNiMn perform well in cryogenic temperatures, melting, casting, and mechanical alloying are the ‘dominant preparation methods,’ often leading to issues with both voids and porosity. Powder bed fusion additive manufacturing (PBFAM) offers potential for fabricated HEAs due to the following features:
- Short processing time
- Geometrical accuracy
- Reduced waste
- Customization possibilities
EBM relies on high energy preheating up to 1100 °C, offers reduced stress on reactive parts, and has been known to be successful in production of HEA parts previously. Along with evaluating CoCrFeNiMn in terms of its microstructure and mechanical properties, researchers were able to produce it through gas atomization for this study, producing further analysis in powder flow, particle size, density, defect, printability, and more. For better ease in 3D printing, the atomized powder was separated into four different categories: ≤25 μm, 25–45 μm, 45–105 μm and 105–300 μm. Respectively, this allows for spark plasma sintering/injection molding, selective laser melting (SLM), EBM, and laser-aided AM.
Flowability is one of the important features in PBFAM, and can be determined in different ways, but for this study was evaluated through the Hall flowmeter funnel and pronounced excellent. Particle size was evaluated, with good printability proven, and parts were inspected for defects based on Archimedes principle and OM observation. Further, microhardness was evaluated as follows:
“The microhardness was examined on the polished specimen by using Matsuzawa MMT-X3 Vickers hardness tester at 1 kg for 15 s. Dog-bone specimens with a cross-section of 1 × 3 mm2 and a gauge length of 5 mm were cut from the cuboid sample. An Instron 5982 universal tensile testing machine with a 10 kN load cell was used for the tensile test with an initial strain rate of 3.3 × 10−4 s−1 at room temperature. A video extensometer was applied to record the strain. Three specimens were examined to obtain the yield strength (YS), ultimate tensile strength (UTS), and elongation to failure.”
Chemical composition analysis revealed ‘spherical morphology’ and only a few irregular particles, with all particles overall created as solidifying droplets collided in the ‘turbulent flow’ of atomization.
“In addition to the satellites, the spherical pores corresponding to entrapped gas during the atomization process was revealed by cross-sectioned observation. In contrast to the occasional appearance in the fine powder, these spherical pores prevailed in the coarse powder. These entrapped gas pores not only influence the true density but also cause defects in the AM parts.”
“A relative narrow ranged powder was obtained after the sieving process. The average particle size is 10.3, 36.2, 63.3 and 129.8 μm for the P1, P2, P3, and P4, respectively. The size distribution overlap is caused by non-perfect sieving process, such as plugged mesh by spherical powder, which can be improved by modifying the sieving process.”
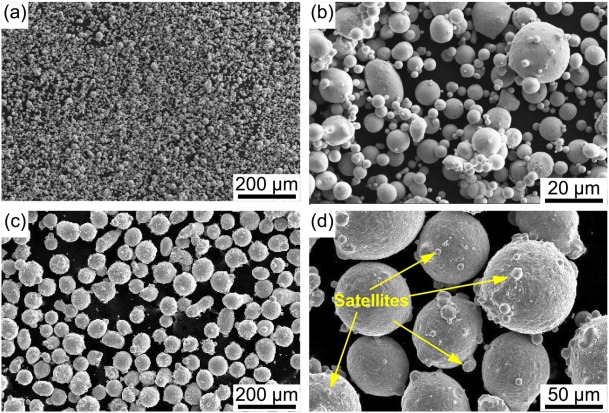
SEM images showing typical HEA powder morphology with different magnifications. (a) and (b) for powder size ≤25 μm (P1); (c) and (d) for powder size ranged from 45 to 105 μm (P3).
The scientists agree that while previous processes may have led to obstacles in using HEA powder, gas optimization makes such materials a definite consideration for mass production, stating that the powders offered all the following:
- Desirable and apparent density
- Tapped density
- Flowability
- Particle size distribution
The researchers do point out, however, that there could be safety issues due to the ‘high density of satellites,’ although it does not seem to affect the EBM printing process. Porosity is a concern however, and the researchers tentatively suggest the hot isostatic press process for elimination of such issues in additive manufacturing, but it is costly and can be limiting for most applications.
“It is suggested that powder with low porosity, for example, produced by plasma rotated electrodes process, would be an ideal choice for critical industrial parts that needs to be exposed in high operating temperature,” said the researchers.
Ultimately, the team concluded that all important features of the process studied here deem it suitable for PBFAM technology and new materials, further stating:
“… the EBM-built CoCrFeNiMn HEA parts had comparable mechanical properties (microhardness and tensile properties) to their conventional cast counterparts.”
As 3D printing with metal in a variety of different methods begins to infiltrate industries focused on intense manufacturing processes, the study of the materials and powders that accompany this technology continues to grow, as exemplified in the automobile industry, aerospace, military and ammunitions endeavors—and far more. Find out more about the PBFAM process and the use of new materials in 3D printing here.
What do you think of this news? Let us know your thoughts! Join the discussion of this and other 3D printing topics at 3DPrintBoard.com.
[Source / Images: ‘Additively manufactured CoCrFeNiMn high-entropy alloy via pre-alloyed powder’]
(a) Image of EBM-built part. (b) SEM of the rough surface from the side view. (c) Typical top surface appearance of the cuboid samples with different extent of swelling and lack of fusion. The yellow and red arrows reveal the swelling and lack of fusion, respectively. (For interpretation of the references to colour in this figure legend, the reader is referred to the web version of this article.)
Subscribe to Our Email Newsletter
Stay up-to-date on all the latest news from the 3D printing industry and receive information and offers from third party vendors.
Print Services
Upload your 3D Models and get them printed quickly and efficiently.
You May Also Like
Johns Hopkins University Researchers Develop HyFAM Technology
Two scientists from Johns Hopkins University, Nathan C. Brown and Jochen Mueller, have developed a hybrid manufacturing technology they call HyFam, or Hybrid Formative Additive Manufacturing. Their work on this technology...
3D Printing G-Code Gets an Upgrade: T-Code
Good old G-Code still manages many 3D printers, great and small. Just like the STL, it’s a standard that enables collaboration while also holding the additive manufacturing (AM) industry back....
AM Rewind: The Biggest News and Trends of 2024
After a sluggish 2023, driven by persistent inflation and geopolitical tensions, 2024 has seen some recovery. Economic growth climbed from about 2.8 percent in 2023 to a modest 3.2 percent...
Metal Wire 3D Printer OEM ValCUN Announces Plans for 2025 Expansion
ValCUN, a Belgian original equipment manufacturer (OEM) of wire-based metal additive manufacturing (AM) hardware, has announced that the company has entered the next phase of its growth trajectory, making key...