As manufacturers and makers worldwide continue to refine and innovate in the realm of 3D printing software, hardware, and materials, scientists too are motivated to continually create new processes for building geometries that are becoming increasingly complex. Dr. James Q. Feng, Principal Engineer at Optomec, has published new findings in Mist Flow Visualization for Round Jets in Aerosol Jet® Printing, as he further explores direct write technology and explains the uses for light scattering particles in the manufacturing process.
Previous challenges in jet flow during production have been examined, evaluating issues with instability and focusing on turbulent impinging jets. Feng believes there needs to be more focus on mist flow visualization—and specifically from microscale round nozzles. Visualization is made possible by adding particles like smoke or other microspheres so that the flow pattern is illuminated. Details regarding the Aerosol Jet® direct-write system, produced by Optomec, are at the heart of Feng’s discussion. The digital dispensing technology makes up a series of platforms that dispense electronic materials, and small particles are provided naturally during the printing process.
“For simplicity, the ink used here is just the deionized (DI) water, and the small particles are water microdroplets in the diameter range of 1 to 5 microns when arriving at the deposition nozzle, out of which the flow visualization is taking place,” says Feng. “With those mist microdroplets being illuminated, a gas jet flow field under investigation becomes visible.”
The direct-write system consists of the following components:
- Atomizer
- Deposition head
- Mist transport-conditioning channel
- Substrate holding stage (includes motion control and mist flow switching device)
The atomizer is responsible for producing ink microdroplets, with mist wrapped in a sheath gas and funneled through a channel in the nozzle.
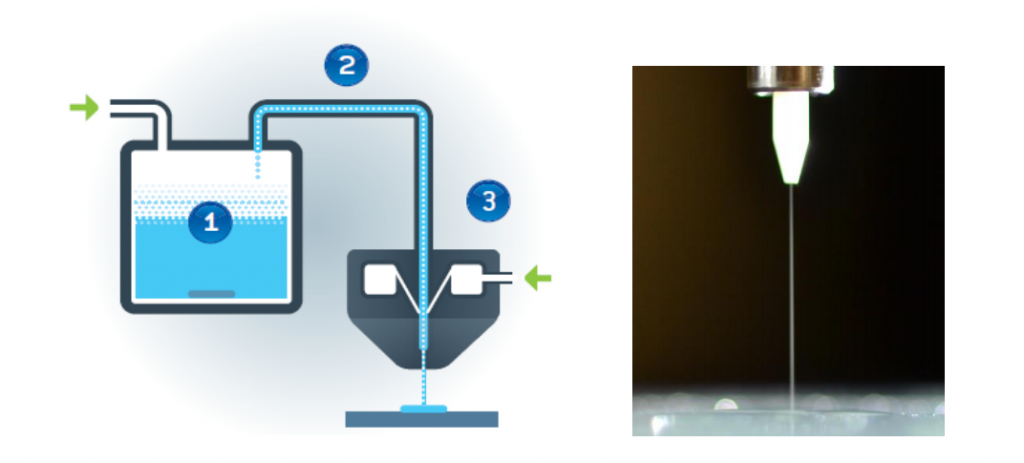
Schematics of the Aerosol Jet® direct-write system: (1) Atomizer that generates mist of
microdroplets of functional inks; (2) Mist transport-conditioning channel that delivers a concentrated
mist of ink microdroplets; (3) Deposition head to form high-speed collimated mist stream through an
aerodynamic focusing nozzle with sheath gas (with arrows indicate the mist carrier gas inlet and nozzle
sheath gas inlet). The photography on right shows visualized mist stream from the deposition nozzle.
“With a standoff of several millimeters, noncontact printing of various patterns on substrates of complex geometries is enabled with CAD-driven relative motions between the substrate and deposition head,” explains Feng.
An interior channel tapers inside the printing nozzle, accelerating the mist flow slowly, with aerodynamic focus. The sheath gas flows alongside the mist stream as it is pushed toward the center. Feng explains that as the mist stream becomes narrower than the channel size, the resulting printing features are finer than the nozzle output diameter. The size can be varied as sheath gas and mist flow rate are adjusted. The sheath gas prevents the nozzle from clogging by keeping the mist droplets and channel wall from touching.
The AJ200 Aerosol Jet® system, as an example, is equipped with mass flow controllers manipulating the mass flow rate within one percent of the set value. Nozzles are available in different sizes, but Feng points out that mist streams can vary due to changes in momentum; for instance, in larger nozzles widening may occur because of viscous diffusion. This is more common than in small nozzles being used for fine feature printing.
In some cases, instability can be controlled by increasing the amount of gas sheath in comparison to the mist—extending the breakdown length and allowing for improved printing in AM processes. Because the sheath to mist ratio can be controlled so easily, Feng points out that it is a good research tool for examining jet flow.
“With the Aerosol Jet® direct-write system, the flow pattern of jet core can be visualized with the scattered light from water microdroplets in the mist stream. The adjustable sheath-to-mist flow ratio offers a “peeling the onion” capability for visualizing jet flow structures. The images of mist flow visualization for free jets exhibit a laminar potential core extending some distance downstream from the nozzle, before developing turbulent eddies signaled as rapid widening of mist stream due to turbulent diffusion,” concludes Feng.
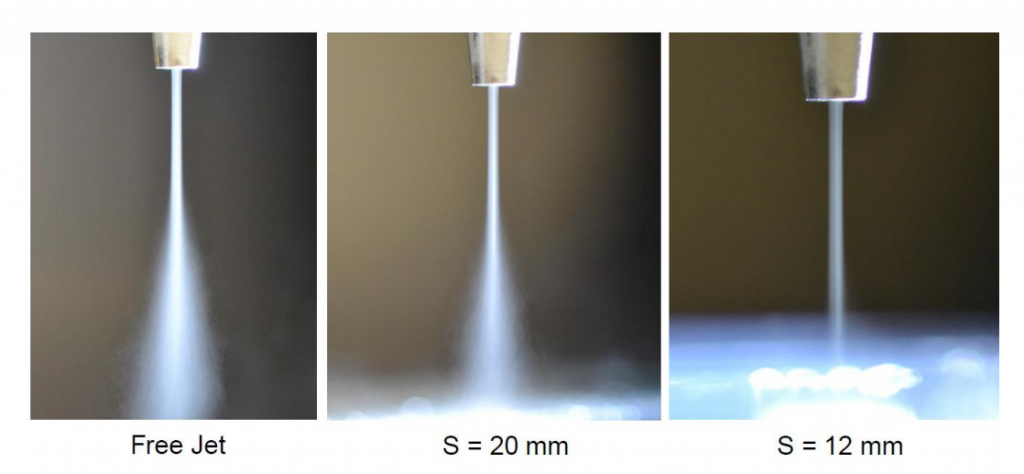
Mist flows of D = 1.0 mm at Re = 1464 (for Q = 1000 sccm) with sheath-to-mist ratio Y = 1:1
for different standoff distances. The outer diameter of the nozzle tip is 2.75 mm, which can effectively
serve as a scale reference.
If you are interested in learning about Optomec’s other recent milestones, check out recent stories we have published, following as they performed other benchmarch additive manufacturing studies, developed hybrid 3D printing processes, and worked in partnership with NASA.
What do you think of this news? Let us know your thoughts; join the discussion of this and other 3D printing topics at 3DPrintBoard.com.
[Source / Images: Mist Flow Visualization for Round Jets in Aerosol Jet® Printing]Subscribe to Our Email Newsletter
Stay up-to-date on all the latest news from the 3D printing industry and receive information and offers from third party vendors.
Print Services
Upload your 3D Models and get them printed quickly and efficiently.
You May Also Like
3D Printing News Briefs, June 11, 2025: Sustainability, Automotive Tooling, & More
We’re starting with sustainability news in today’s 3D Printing News Briefs, as EOS has strengthened its commitment on climate responsibility, and Zestep is making 3D printing filament out of eyewear...
3D Printing 50 Polymer Stand-In Parts for Tokamaks at the PPPL & Elytt Energy
Of all the world’s things, a tokamak is one of the hardest, most complex, expensive and exacting ones to make. These fusion energy devices make plasma, and use magnets to...
3D Printing News Briefs, May 17, 2025: Color-Changing Materials, Humanoid Robot, & More
We’re covering research innovations in today’s 3D Printing News Briefs! First, Penn Engineering developed 3D printed materials that change color under stress, and UC Berkeley researchers created an open source,...
Firehawk Aerospace Partners with JuggerBot 3D, Gets $1.25M from AFWERX for 3D Printed Propellants
Texas-based Firehawk Aerospace, an advanced energetic materials firm that works with aerospace and defense applications, announced a strategic partnership with JuggerBot 3D, an Ohio-based large-format 3D printer manufacturer. Together, the...