Interview with Scott Schiller Global Head of Market Development at HP 3D Printing About Manufacturing Using 3D Printing
Scott Schiller is the Global Head of Market Development at HP. He’s also brilliant and has a long history of building HP businesses in Inkjet and digital press. HP is, of course, a huge company with an incredible degree of technical prowess which they’re bringing to bear on 3D printing. But, in our industry, in terms of installed base, they’re a startup. They have to be agile and bring new strategies to win in our market. If they stick it out and keep pouring on their research capacity then I think we can all agree that HP will stay a major player in our market. But, large corporations can be capricious and visions like dreams can change. So for HP, were always looking to see how permanent HP’s commitment to 3D printing is. A good sign of this is HP eating its own dogfood. If the company truly internally uses 3D printing widely then the technology will permeate the entire organization and hopefully make them more competitive and cost-efficient in many fields. The 3D printing idea is that it will speed up time to market and make organizations more agile. So every time a large company engages with the technology we would expect for them to use it internally as well to consolidate parts, make more niche products, save weight and do all the things the technology is supposed to do. That’s, why it is extremely good news that HP is using over 140 3D printed parts on its 300 and 500 series 3D Printers. The company truly is eating its own dog food and using 3D printing to save money and be more competitive. We interviewed Scott about this and also learned that they have 80% powder reusability and are speeding up time to market in various products. Scott is also the first person to go on the record to claim that “The question isn’t if 3D printing will be the new platform for global mass-production, it’s when.”
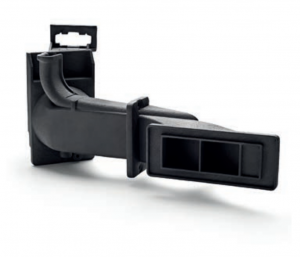
A PA 12 Part
What material are you using?
“Our Multi Jet Fusion printers use thermoplastic materials — PA12 and PA11 — which can also be recycled, both as a powder and as a printed part. HP’s 3D High Reusability PA12, which is developed to allow reuse of surplus powder batch after batch, delivers consistent performance while achieving 80 percent surplus powder reusability. In addition, our PA11 material is a 100 percent bio-based content polymer derived from the oil of the castor bean.”
What kinds of parts do you print?
“One of my favourite examples is the 140-plus parts in our 300/500 series which we printed on our very own Multi Jet Fusion.
“Some other examples include spare parts we’ve produced for our Large Format Printing business, HP inkjet printheads, and a part for the HP Z 3D Camera in which we were able to reduce the design cycle by six weeks.
“Another great example is how our team based in Israel used Multi Jet Fusion to come up with unthinkable new design possibilities for our large format printers with cost savings of up to 90 percent per part.”
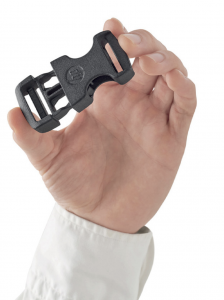
An HP PA 11 part
Why do you do this?
“HP is one of the world’s largest and most advanced technology companies: a $50 billion global business that produces over 100 million products per year in 170 countries via one of the biggest and most sophisticated design, engineering, and supply chains ever created. HP’s use of Multi Jet Fusion illustrates how 3D printing technology is digitally transforming large enterprises and reinventing the global manufacturing industry. We believe strongly in our innovations and could think of no better way to reinvent our own company than by digitally transforming our design, manufacturing, and supply chain operations across all business units using our own Multi Jet Fusion 3D printing technology.
“Most importantly, we’re using our 3D printing technology to reinvent our own models because it makes economic sense. Since using our 3D printing technology, we’ve already seen efficiencies in the time it takes to get products to market, we’ve seen performance increase and economic advantages, and 3D printing allows us to do more in the way of personalization.
“Finally, all of these benefits are underscored by something that is near and dear to us at HP, which is sustainability. By weaving 3D printing into our supply chain operations, we can lower our impact on the environment by producing components locally (which reduces the carbon footprint), reducing production time (which means less energy is spent creating products and parts), and sleep easy knowing the recyclability and reusability of the materials we use is industry-leading.”
What would you advise a company that wants to explore manufacturing with 3D printing?
“3D printing technology can have a major impact on industries from automotive to healthcare to heavy industry, and huge global brands are beginning to reinvent their businesses for the digital manufacturing future. The question isn’t if 3D printing will be the new platform for global mass-production, it’s when. And production is just one piece of it. A huge component of 3D printing adoption is mastering digital workflows. On a base level, the similarities between industrial 2D printing and 3D printing are really striking – digital production all comes down to providing unique value as a function of better supply and demand management. With respect to capital, the basic cost structures between industrial 2D and 3D look similar, but the physics of 3D printing are obviously much different and should not be underestimated when considering long-term value. In terms of timing, it’s still early enough in the broad adoption of 3D printing that there’s plenty of time for learning, and plenty of competitive advantages for organizations that want to transform their business with digital manufacturing.”
Is this also a useful technology for tens of thousands of identical parts?
“3D printing is absolutely a solution for mass production. We recently announced HP Metal Jet, a ground breaking, voxel-level binder jetting 3D printing technology designed to withstand high volume printing.
“One of the key benefits of HP Metal Jet is the increase in productivity, providing up to 50 times more productivity than other 3D printing methods.”
Does it make your development more agile?
“Absolutely, one of my favorite examples of this program helping our engineering teams respond more quickly to required redesign during manufacturing was a physical subsystem for the Jet Fusion 3D printer. Minimized tooling reduced the development time of a new subsystem by half and allowed the team to stay on the production cycle.”
Do you have any parts where you reduced part count as well?
“One example is a recreated tool used in the HP printheads manufacturing line – called a ‘drill extraction shoe’ – using Multi Jet Fusion. We were able to consolidate the original tool from 7 parts to just 1. Additionally, we saw a 95 percent cost reduction, 90 percent weight reduction, and can now produce the part in 1-2 days versus 3-5 days.”
What were some of the stumbling blocks to adopting 3D printing internally?
“When it comes to rethinking the way you approach design and manufacturing, there’s a massive cultural shift that needs to happen at an organizational level. For example, historically design engineering and manufacturing engineering teams worked separately. However, when it comes to rethinking parts, these two groups need to work together from start to finish. There’s a lot to be said about the organizational behavior changes that need to occur for companies to be successful in truly reinventing their manufacturing.”
Subscribe to Our Email Newsletter
Stay up-to-date on all the latest news from the 3D printing industry and receive information and offers from third party vendors.
Print Services
Upload your 3D Models and get them printed quickly and efficiently.
You May Also Like
3D Printing News Briefs, July 2, 2025: Copper Alloys, Defense Manufacturing, & More
We’re starting off with metals in today’s 3D Printing News Briefs, as Farsoon has unveiled a large-scale AM solution for copper alloys, and Meltio used its wire-laser metal solution to...
Etsy Design Rule Change Reduces Selection of 3D Printed Goods
Online marketplace Etsy has implemented a rule change requiring all 3D printed goods on the site to be original designs. The update to the site’s Creativity Standards states, ¨Items produced using...
Siraya Tech Introduces New Elastomer 3D Printing Materials, Including Foaming TPU
California company Siraya Tech, founded in 2019 with a focus on material science, customer focus, and agility, develops high-quality 3D printing materials that meet the needs of creators, hobbyists, and...
3D Printing News Briefs, April 12, 2025: RAPID Roundup
The news from last week’s RAPID+TCT in Detroit just keeps on coming! That’s why today’s 3D Printing News Briefs is another RAPID Roundup of more exciting announcements from the trade...