There are multiple methods of manufacturing ceramic materials, including powder injection molding (PIM) and, of course, 3D printing. While ceramics are still considered to be a decently new 3D printing material, it’s been catching on over the last few years in all sorts of applications, from art and electronics to military, aerospace, and medical.
Stereolithography (SLA), selective laser sintering (SLS), direct ceramic ink-jet printing, and fused filament fabrication (FFF), the most common extrusion-based method, have all been used to 3D print ceramics. However, FFF is most often used with thermoplastics, and there have been a few attempts to modify, and even improve, the properties of this material by adding small amounts of diverse powder or fiber materials, and even ceramic fillers.
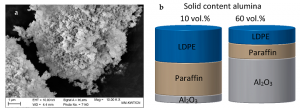
(a) SEM image of Al2O3; (b) scheme of the feedstock composition exemplarily for 10 and 60 vol % alumina.
A team of researchers from the Karlsruhe Institute of Technology (KIT) and the University of Freiburg recently published a paper, titled “Fused Filament Fabrication of Small Ceramic Components,” about their work developing a new ceramic composite material and a new process chain for efficient, cost-effective rapid prototyping of 3D printed ceramics.
The abstract reads, “With respect to rapid prototyping of ceramic components, there are known only a few processes (stereo lithography, binder jetting). In this work, a new process chain is described in detail, showing that ceramics can be printed in a very cost-efficient way. We developed a ceramic–polymer composite as filament material that can be printed on a low-cost fused filament fabrication (FFF) desktop printer, even with very small nozzle sizes enabling very small geometric feature sizes. The thermal post-processing, with debinding and sintering, is very close to the ceramic injection molding (CIM) process chain.”
One can feasibly 3D print objects that can be debinded and sintered to dense ceramic parts by filling thermoplastics with high solid ceramic powder. The researchers developed a process chain detailing how to use inexpensive FFF 3D printers to fabricate small ceramic components, using sub-micron-sized alumina (Al2O3, TM-DAR) as the ceramic powder.
“Even if the final components consist of pure ceramic, the thermoplastic binder system is a temporary vehicle to enable shaping and stabilization of the ceramic particles,” the researchers explained.
The filaments were prepared with a one-screw extruder, and the sample components were printed on a slightly modified X350pro desktop FFF 3D printer by German RepRap.
The researchers explained, “The modifications concern the filament size of 3 mm instead of 1.75 mm, as well as a Titan extruder with a gear ratio of 3:1.”
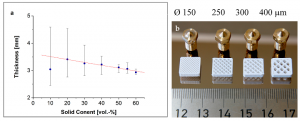
(a) Filament diameter as function of solid content, and (b) open test structures printed with different nozzle sizes.
Filament diameters must be within a very small tolerance range to achieve exact 3D printing results; fine nozzle diameters are also important for 3D printing small components with geometric features that are around or smaller than 100 µm.
The researchers report that the filament with “a solid content of 50 vol % alumina” displayed a good 3D printing behavior, while the one with 55 vol % solid content needs to be printed with a 400 µm nozzle size. The material with the highest fill of 60 vol % must be manually extruded, but the viscosity is too high for 3D printing. Since the extruder gear can’t move the filament along, the researchers experienced surface grinding, but did not report any nozzle clogging as the solid content increased.
“We developed a very highly-filled filament material and introduced a complete process chain to print ceramic components via FFF,” the researchers wrote.
“The mixing torque and the viscosity of the materials increased with increasing solid content. Filament diameters and standard deviations decreased with increasing solid content. Materials with a solid content of 50 vol % are very printable with nozzle sizes down to 150 µm. Layer thicknesses of 80 µm and bar widths of 160 µm could be realized with open demonstrator structures. Open structures have sintering densities of 98.4% of theoretical density; test discs have only 97.3%, while ceramic injection molded samples reach 99.7%. Probably during printing process, pores and cavities are introduced, due to not completely filling tool path generation by the slicing programs.”
The researchers stated that because their process chain does not require tools, it could be a very promising method for manufacturing prototypes and small amounts of ceramic objects.
“According to these results, it is feasible to generate prototypes and design studies in a simple and cost-efficient way,” the researchers concluded.
Co-authors include Dorit Nötzel, Ralf Eickhoff, and Thomas Hanemann.
Discuss this research and other 3D printing topics at 3DPrintBoard.com or share your thoughts below.
Subscribe to Our Email Newsletter
Stay up-to-date on all the latest news from the 3D printing industry and receive information and offers from third party vendors.
Print Services
Upload your 3D Models and get them printed quickly and efficiently.
You May Also Like
3D Printing News Briefs, June 11, 2025: Sustainability, Automotive Tooling, & More
We’re starting with sustainability news in today’s 3D Printing News Briefs, as EOS has strengthened its commitment on climate responsibility, and Zestep is making 3D printing filament out of eyewear...
3D Printing 50 Polymer Stand-In Parts for Tokamaks at the PPPL & Elytt Energy
Of all the world’s things, a tokamak is one of the hardest, most complex, expensive and exacting ones to make. These fusion energy devices make plasma, and use magnets to...
3D Printing News Briefs, May 17, 2025: Color-Changing Materials, Humanoid Robot, & More
We’re covering research innovations in today’s 3D Printing News Briefs! First, Penn Engineering developed 3D printed materials that change color under stress, and UC Berkeley researchers created an open source,...
Firehawk Aerospace Partners with JuggerBot 3D, Gets $1.25M from AFWERX for 3D Printed Propellants
Texas-based Firehawk Aerospace, an advanced energetic materials firm that works with aerospace and defense applications, announced a strategic partnership with JuggerBot 3D, an Ohio-based large-format 3D printer manufacturer. Together, the...