The worlds of 3D printing and robotics often collide, as we’ve seen continually—and most recently—with everything from nearly invisible hydrogel robots to those capable of doing pushups and sweating. And while scientists predict that one day you may see robots walking right out of your 3D printer, today we are taking a look at bio-bots that seem like they may have walked right out of a sci-fi movie.
Created by researchers at the University of Illinois at Urbana-Champaign, these bio-bots locomote via a true system of muscle cells, powered by electronics. The team, headed by Rashid Bashir, has shared their recipe for building these futuristic machines in a recent Nature Protocols article. In ‘A modular approach to the design, fabrication, and characterization of muscle-powered biological machines,’ by Ritu Raman, Caroline Cvetkovic, and Rashid Bashir, you can take an entirely new DIY approach to the world of bots.
“The protocol teaches every step of building a bio-bot, from 3D printing the skeleton to tissue engineering the skeletal muscle actuator, including manufacturers and part numbers for every single thing we use in the lab,” explained Ritu Raman, a postdoctoral fellow in the Department of Bioengineering and the study’s first author.
“This protocol is essentially intended to be a one-stop reference for any scientist around the world who wants to replicate the results we showed in our PNAS 2016 and PNAS 2014 papers, and give them a framework for building their own bio-bots for a variety of applications.”
As the authors discuss in their paper, these biological machines can adapt to their environment. They also point out that 3D printing has been a major impetus for the progress seen here in robotics, through allowing such advances in tissue engineering and regenerative medicine. The biomaterials of today now allow for the creation of what the researchers call “smart responsive machines,” able to work in a range of different applications.
The team has been working on their bio-bots for years, also dabbling in hydrogels, accompanied by live tissue. They unveiled their walking bots in 2012, with the stunning information that they were powered by live heart tissue gleaned from rats. While this was quite a leap, the researchers kept refining their bots and the tissue they were using as the heart cells contracted too much to allow for optimum control over the electronics.“The 3D printing revolution has given us the tools required to ‘build with biology’ in this way. We re-designed the 3D-printed injection mold to produce skeletal muscle ‘rings’ that could be manually transferred to any of a wide variety of bio-bot skeletons. These rings were shown to produce passive and active tension forces similar to those generated by muscle strips,” Raman said.
“Using optogenetics techniques, we worked with collaborators at MIT to genetically engineer a light-responsive skeletal muscle cell line that could be stimulated to contract by pulses of 470-nm blue light. The resultant optogenetic muscle rings were coupled to multi-legged bio-bot skeletons with symmetric geometric designs. Localized stimulation of contraction, rendered possible by the greater spatiotemporal control of light stimuli over electrical stimuli, was used to drive directional locomotion and 2D rotational steering.”
In writing the paper and releasing their bio-bot ‘recipe,’ the researchers are hoping to see others not only appreciate and re-create their work—but to improve on it as well. The team hopes this is just the beginning as scientists everywhere are able to begin meeting current challenges in medicine and science. Discuss in the 3D Printed Bio-Bots forum at 3DPB.com.
[Source: Phys.org]
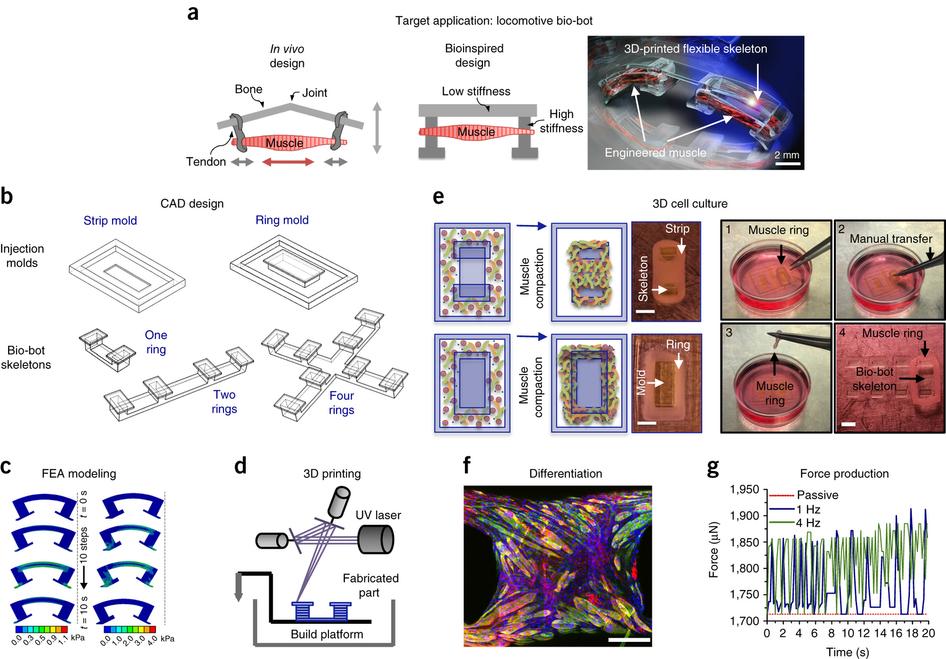
Bio-bot process overview, from ‘A modular approach to the design, fabrication, and characterization of muscle-powered biological machines.’ (a) Bio-bot design is inspired by biological design in the body. (b) Bio-bot skeletons and muscle bioactuator injection molds are designed using computer-aided design (CAD) software (Steps 1 and 2), (c) tested using finite element analysis (FEA) software (Steps 20–25), and (d) manufactured via stereolithographic 3D printing (Steps 3–10). (e) Muscle rings are tissue-engineered and coupled to bio-bot skeletons (Steps 11–16), and assessed via (f) immunohistochemical staining (Step 26) and (g) externally stimulated force production (Step 19). Each step of the design process (a–g) is iterative, and feedback from each step is used to improve the functionality of the bio-bot with each iteration. Scale bars, 2 mm (e); 500 μm (f). a,c,f adapted with permission from ref. 13, National Academy of Sciences; b,d,e adapted with permission from ref. 14, National Academy of Sciences.
Subscribe to Our Email Newsletter
Stay up-to-date on all the latest news from the 3D printing industry and receive information and offers from third party vendors.
Print Services
Upload your 3D Models and get them printed quickly and efficiently.
You May Also Like
Making Space: Stratasys Global Director of Aerospace & Defense Conrad Smith Discusses the Space Supply Chain Council
Of all the many verticals that have been significant additive manufacturing (AM) adopters, few have been more deeply influenced by the incorporation of AM into their workflows than the space...
EOS in India: AM’s Rising Star
EOS is doubling down on India. With a growing base of aerospace startups, new government policies, and a massive engineering workforce, India is quickly becoming one of the most important...
PostProcess CEO on Why the “Dirty Little Secret” of 3D Printing Can’t Be Ignored Anymore
If you’ve ever peeked behind the scenes of a 3D printing lab, you might have caught a glimpse of the post-processing room; maybe it’s messy, maybe hidden behind a mysterious...
Stratasys & Automation Intelligence Open North American Tooling Center in Flint
Stratasys has opened the North American Stratasys Tooling Center (NASTC) in Flint, Michigan, together with automation integrator and software firm Automation Intelligence. Stratasys wants the new center to help reduce...