Kengoro: 3D Printed Robot Works Up a Sweat at the IEEE/RSJ International Conference on Intelligent Robots & Systems
We’ve certainly spent a lot of time considering what might happen when robots truly can think like us, but very likely not a lot (on the part of the layman, anyway) has been put into considering how they might also be able to move and even show off their stamina like we do one day. And while we so often borrow from nature to find inspiration and the key to innovation—from butterfly wings to salamanders in 3D design of all sorts—now we see that also instilled in a recent project emerging from Japan as robots not only beat us in phys ed now, they’ve got the perspiration to prove it.
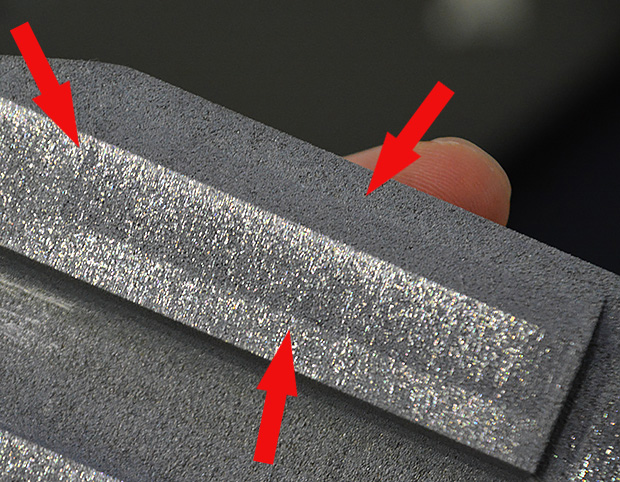
The 3D printed metal offers varying levels of permeability that enable the ‘sweating’ concept. [Image: JSK Lab/University of Tokyo]
The team is from JSK Lab at the University of Tokyo. Led by Professor Masayuki Inaba, they have created Kengoro as their third robot, with Kojiro and Kenshiro preceding him. The bio-inspired machine boasts 108 motors, along with a variety of circuit boards, gears, and more. With so many components, the research team was forced to innovate in terms of a cooling mechanism simply due to a lack of room. They chose to look at the 3D printed metal frame of the robot as its ‘skeleton’ and sought a way to make a much more creative cooling system than ever seen before. And it’s the 3D printed element that allows for this sweating mechanism to begin with, due to the varying levels of permeability allowed in the metal material working as microchannels for the fluid (water) to act as sweat when things get hot—ultimately cooling off Kengoro.
“Usually the frame of a robot is only used to support forces,” lead author Toyotaka Kozuki said in a recent interview. “Our concept was adding more functions to the frame, using it to transfer water, release heat, and at the same time support forces.”
As you can see from the images and the video below, Kengoro is definitely operating on a much different level from the robots we’re using to seeing. He can do push-ups continuously for 11 minutes with this new cooling system which the researchers state is three times better than traditional air cooling. Just one cup of deionized water is enough to keep him cooled for half a day.
This is all outlined at the conference in “Skeletal Structure with Artificial Perspiration for Cooling by Latent Heat for Musculoskeletal Humanoid Kengoro,” authored by Toyotaka Kozuki, Hirose Toshinori, Takuma Shirai, Shinsuke Nakashima, Yuki Asano, Yohei Kakiuchi, Kei Okada, and Masayuki Inaba. IROS was held in Daejeon, South Korea October 9-14. Discuss in the Kengoro forum at 3DPB.com. [Source: IEEE Spectrum]
Subscribe to Our Email Newsletter
Stay up-to-date on all the latest news from the 3D printing industry and receive information and offers from third party vendors.
Print Services
Upload your 3D Models and get them printed quickly and efficiently.
You May Also Like
The Dental Additive Manufacturing Market Could Nearly Double by 2033, According to AM Research
According to an AM Research report from 2024, the medical device industry, specifically in dentistry, prosthetics, and audiology, is expected to see significant growth as these segments continue to benefit from...
Heating Up: 3D Systems’ Scott Green Discusses 3D Printing’s Potential in the Data Center Industry
The relentless rise of NVIDIA, the steadily increasing pledges of major private and public investments in national infrastructure projects around the world, and the general cultural obsession with AI have...
AM Research Webinar Explores Continuum’s Sustainable Metal Additive Manufacturing Powders
Metal additive manufacturing (AM) powder supplier Continuum Powders is working to develop solutions that empower industries to reduce waste and optimize their resources. An independent life cycle assessment (LCA) of...
3D Printed Footwear Startup Koobz Lands $7.2M in Seed Round
California-based Koobz is focused on reshoring the U.S. footwear supply chain with advanced manufacturing processes, including 3D printing. The startup just announced that it has added $6 million to its...