LLNL Researchers Isolate Enzymes with 3D Printing to Convert Methane to Methanol, Harnessing & Controlling Emissions
Give them the tools and they will create. Give them a 3D printer and they will innovate. Over and over–and in areas where you least expect it–as is the case at the Lawrence Livermore National Laboratory, where it would certainly seem that you won’t meet your typical scientists. While there are many examples of their breakthroughs via 3D printing, recently the team at LLNL has been responsible for the development of 3D printed football helmets, new bio-inks for electronics, 3D printed blood vessels, and much more.
But now, they are using the 3D printer not only to perform chemistry, but to control it and make it work to our benefit–and even more importantly–to that of the environment. In their recent paper, ‘Printable enzyme-embedded materials for methane to methanol conversion,’ published in Nature Communications, researchers Craig D. Blanchette, Jennifer M. Knipe, Joshuah K. Stolaroff, Joshua R. DeOtte, James S. Oakdale, Amitesh Maiti, Jeremy M. Lenhardt, Sarah Sirajuddin, Amy C. Rosenzweig, and Sarah E. Baker explain how the team actually created their own reactor where they are able to selectively activate methane and then convert it to methanol.
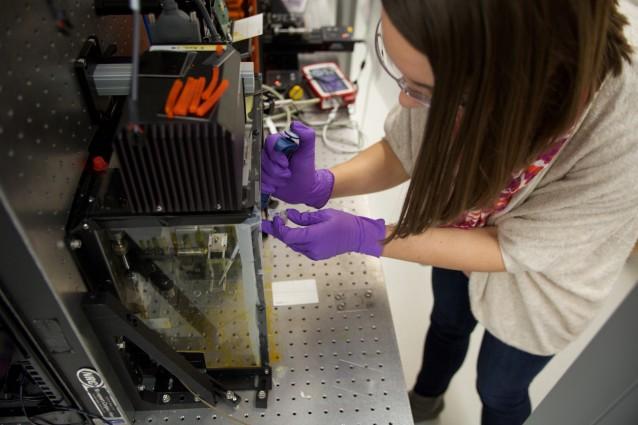
LLNL material scientist Jennifer Knipe loads a prepolymer-protein resin onto the stage of the large area projection microstereolithography system to be cured as a 3D printed polymer. [Photo: George Kitrinos/LLNL]
Previously the only way to complete this methane conversion was through the use of a particular agent, the enzyme methane monooxygenase (MMO).
“Partial methane oxidation by MMO enzymes can be carried out using engineered methanotroph organisms; however, this approach inevitably requires energy for upkeep and metabolism of the organisms, which reduces conversion efficiency,” state the researchers. “Engineered organisms that carry out more efficient methane activation have been proposed to overcome some of these challenges.”
“An additional challenge to whole-cell biocatalysis is that the reactions are typically carried out in low-throughput unit operations with mass transfer limitations, such as stirred tank reactors.”
The researchers point out that the industry has been in search of a way to convert methane as it would be profitable for making use of currently unused or ‘stranded’ sources. In examining the current processes, they saw that improvement could be achieved in isolating that MMO enzyme from the host.
“Isolated enzymes offer the promise of highly controlled reactions at ambient conditions with higher conversion efficiency and greater flexibility of reactor and process design,” stated the researchers in their paper.
The idea, in very basic form, was to put the isolated enzymes in their 3D printed polymers and allow them to convert the methane. Keeping these isolated enzymes alive was, however, a challenging process at first. As they worked to create their polymer and integrate all the correct ‘ingredients,’ they experimented with using a surfactant for the materials. Ultimately, through trial and error, they discovered that activity of the enzymes decreased with similar treatments of any kind. Retaining the enzyme activity was a priority, and as they discovered low levels of PEGDA 575 seemed to work without negative results, they continued with success.
“Remarkably, the enzymes retain up to 100 percent activity in the polymer,” said Sarah Baker, LLNL chemist and project lead. “The printed enzyme-embedded polymer is highly flexible for future development and should be useful in a wide range of applications, especially those involving gas-liquid reactions.”

LLNL chemist Sarah Baker holds a gas chromatography vial used to measure the amount of methanol produced by the enzyme-embedded polymer. [Photo: George Kitrinos/LLNL]
“Up to now, most industrial bioreactors are stirred tanks, which are inefficient for gas-liquid reactions. The concept of printing enzymes into a robust polymer structure opens the door for new kinds of reactors with much higher throughput and lower energy use,” said environmental scientist Joshuah Stolaroff.
The polymer itself is a hybrid material made of active pMMO (particulate forms of the aforementioned MMO) and associated lipids entrapped within a PEG-based hydrogel that is then cured, allowing for the biocatalytic material that the researchers see as a unique and successful way for improving mass transfer of the natural gases. Essentially, these biocatalytic polmers can be viewed as a new type of bio-ink, despite not being used for the more common applications in the medical field as we see so often today.
“A bioreactor that optimizes mass transfer, diffusion-limited and kinetic-limited reactions is similarly complex, and precise control over the 3D spatial distribution of enzymes is beneficial in optimizing product production,” state the researchers in their paper.
The team also sees the potential for the 3D printing of reactor components in the future, or prototypes, with the potential for a further evolution of the 3D printed polymers that currently contain the enzymes. They point out that while 3D printing is allowing them to make progress and innovate in this area where not previously possible–through printing new geometries, enzyme gradients, and controlling materials–cost-effectiveness would still need to be proven to make it truly viable.
Undoubtedly this new process has huge potential for the future, and can offer benefit to numerous industries and point toward other applications. The researchers do cautiously point out though that aside from the cost issue, there are several other hurdles including costs, enzyme longevity, the use of appropriate reductants. While this is an exciting breakthrough, there are other challenges to work though and options to examine.
“With these challenges in mind, the application of biological tools to address the need to convert fugitive and remote methane streams requires that biologists and materials scientists work together to optimize biocatalysts through protein engineering and to develop accompanying bioreactor materials,” states the team in their paper, in final conclusion.
Do you see this new process as having real-world use? Discuss further in the LLNL Researchers 3D Printing to Convert Methane forum over at 3DPB.com.
[Source: LLNL / Images: George Kitrinos/LLNL]Subscribe to Our Email Newsletter
Stay up-to-date on all the latest news from the 3D printing industry and receive information and offers from third party vendors.
Print Services
Upload your 3D Models and get them printed quickly and efficiently.
You May Also Like
Johns Hopkins University Researchers Develop HyFAM Technology
Two scientists from Johns Hopkins University, Nathan C. Brown and Jochen Mueller, have developed a hybrid manufacturing technology they call HyFam, or Hybrid Formative Additive Manufacturing. Their work on this technology...
3D Printing G-Code Gets an Upgrade: T-Code
Good old G-Code still manages many 3D printers, great and small. Just like the STL, it’s a standard that enables collaboration while also holding the additive manufacturing (AM) industry back....
AM Rewind: The Biggest News and Trends of 2024
After a sluggish 2023, driven by persistent inflation and geopolitical tensions, 2024 has seen some recovery. Economic growth climbed from about 2.8 percent in 2023 to a modest 3.2 percent...
Metal Wire 3D Printer OEM ValCUN Announces Plans for 2025 Expansion
ValCUN, a Belgian original equipment manufacturer (OEM) of wire-based metal additive manufacturing (AM) hardware, has announced that the company has entered the next phase of its growth trajectory, making key...