3D printing is turning the world on its head, as the disruptive technology streamlines and modernizes the processes behind some of the most intricate, detailed components in a bevy of applications from desktop doodads to the highest-tech bioprinted human tissues. The technology is taking the world by storm–including the land Down Under.
This week, 4WEB Medical has announced its first success story in Australia with a patient-specific segmental bone defect procedure completed in Brisbane, supported by LifeHealthcare, the company’s Australian partner.
4WEB Medical, which specializes in truss implants, has reached several milestones lately in its provision of 3D printed orthopedic implants, with more than 3,000 spine truss implants in use by late 2014. The world’s first FDA-approved provider of 3D printed orthopedic implants, 4WEB has clearly been taking its global focus seriously.
“We are very excited about 4WEB’s first Australian patient specific implant procedure,” said the company’s President and CEO, Jessee Hunt. “While this is our first custom implant procedure completed in Australia, 4WEB has completed nearly 100 custom truss implant procedures performed worldwide dating back to 2011. 4WEB has produced patient specific implants in a variety of orthopedic procedures such as spinal fusions, hemi-pelvectomies, distal tibial osteotomies, humeral and femoral segmental bone defects, ankle revisions, sternectomies as well as many others.”
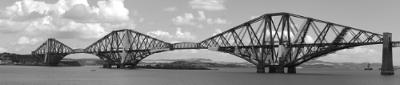
4WEB Medical uses the concept of structural engineering, such as the truss design in this bridge, for the development of patient-specific structural implants
Comparable to the truss structure of bridges, which have been trusted to support traffic for centuries, 4WEB Medical’s orthopedic implants provide for high-tech solutions to neurosurgeons as well as orthopedic, and foot and ankle surgeons. Patient-specific implants are becoming more prevalent in the medical field, which is coming to realize that made-to-order devices will serve individual patients far better than yesterday’s off-the-shelf, one-size-fits-some models. The use of 3D printing to create the implants allows for a single unit to be created at a significantly lower cost and with no waste.
“The ability to customize the truss implant to match the unique anatomy of an individual patient is a significant advancement in orthopedics,” notes LifeHealthcare COO Matt Muscio. “Current porous metal technologies rely on bone attachment which has shown some drawbacks over time. The open architecture truss implant technology provides a robust scaffolding for structural support while allowing for osseous incorporation.”
For the implant procedure performed this week in Brisbane, 4WEB Medical and LifeHealthcare worked together with the patient’s surgeon, via a web-based meeting between medical staff and engineers. Through their high-tech chat, the engineers were able to gauge the needs of the patient as well as the surgical staff’s proposed approach to the procedure.
CT scan data from the patient is used in 3D software reconstruction in order to ensure the precision needed to custom-fit an individual. With this 3D model, the surgeon is able to anticipate the best plan for the operation, and then to convey that intent to 4WEB Medical’s engineers who, in turn, design a custom truss implant. The implant is designed to exactly fit the void left by the resection, supporting bone growth in the patient as healing occurs. Once the surgeons approve the design, the implant is 3D printed and then is ready for the OR.
Do you know anyone who has benefited from a 3D printed implant? What do you think of 4WEB’s Australian operation? Join the discussion in the 4WEB Medical First Australian Implant forum thread over at 3DPB.com.
Subscribe to Our Email Newsletter
Stay up-to-date on all the latest news from the 3D printing industry and receive information and offers from third party vendors.
Print Services
Upload your 3D Models and get them printed quickly and efficiently.
You May Also Like
Reinventing Reindustrialization: Why NAVWAR Project Manager Spencer Koroly Invented a Made-in-America 3D Printer
It has become virtually impossible to regularly follow additive manufacturing (AM) industry news and not stumble across the term “defense industrial base” (DIB), a concept encompassing all the many diverse...
Inside The Barnes Global Advisors’ Vision for a Stronger AM Ecosystem
As additive manufacturing (AM) continues to revolutionize the industrial landscape, Pittsburgh-based consultancy The Barnes Global Advisors (TBGA) is helping shape what that future looks like. As the largest independent AM...
Ruggedized: How USMC Innovation Officer Matt Pine Navigates 3D Printing in the Military
Disclaimer: Matt Pine’s views are not the views of the Department of Defense nor the U.S. Marine Corps Throughout this decade thus far, the military’s adoption of additive manufacturing (AM)...
U.S. Congress Calls Out 3D Printing in Proposal for Commercial Reserve Manufacturing Network
Last week, the U.S. House of Representatives’ Appropriations Committee moved the FY 2026 defense bill forward to the House floor. Included in the legislation is a $131 million proposal for...