Space and advanced technology certainly go hand-in-hand, and additive manufacturing is certainly taking its place among the stars. Well–at least near-space. We’ve seen developments in AM techniques lead to prototypes as well as end-use components fit for use (and fabrication!) in space, and the “final frontier” is becoming an ever-widening application for 3D printing to prove its concept.
The European Space Agency has been taking its place in the momentous and still-developing history of space exploration and discovery, including working with 3D printing techniques to develop viable components for use in space. Just last month, the ESA successfully performed “hot fire” trials of a 3D printed platinum combustion chamber and nozzle through work with Airbus Defence & Space. Their work continues as they continue to work toward tried-and-tested components ready to hit the skies–and beyond.
Research funded by the ESA, led by Lecturer in Advanced Manufacturing Dr. Khamis Essa with development work performed by Research Fellow in the School of Mechanical Engineering Dr. Hany Hassanin, of the UK’s University of Birmingham, has now led to confirmed success in further hot fire testing of more newly developed 3D printed components for use in space-ready rocket engines.
The research, several years in the making, has developed the world’s first 3D printed ceramic catalyst bed. The 3D printed component works flawlessly with the ESA’s monopropellant based on hydrogen peroxide, which offers a ‘green’ alternative to the previously ubiquitous hydrazine, which is toxic and unstable.
This advanced combination presents an “extremely reactive” catalyst bed that offers substantial potential to enhance the design of catalyst beds, as well as thrusters’ size and performance efficiencies. It also reduces cost and time of production and material waste, all while ‘greening’ the profile of the entire system.
To make the 3D printed catalyst bed thrusters, the researchers pioneered a technique to manufacture and coat complex, high-resolution ceramics. The parts, created with a resolution of less than 100 microns and with a high surface area to unit mass ratio, stood up to performance-ready parameters in testing at high levels, with repeatable results.
“These results are truly impressive,” noted Dr. Essa. “The testing team indicated that they have never seen performance like this. I’m excited about developing such revolutionary new technology and look forward to seeing it make high impacts on the space industry.”
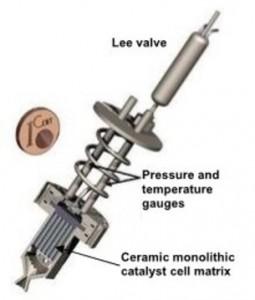
ESA: Schematic cutaway showing advanced thrusters internal design and location, above nozzle, of the monolithic catalyst cell matrix. Note size of thruster compared to 1 EuroCent coin
Tests for the parts were developed by the University of Birmingham team in conjunction with partners at DELTACAT and the University of Southampton. The 3D printed monolithic catalyst beds created using this newly developed technique showed, in several areas, superior results in hot fire testing compared to the ceria pellets catalyst beds used as a baseline.
The catalyst beds produced favorable results in the testing, which, according to the researchers, included testing of the new design with engine performance was a 20N thrust at 700oc, 3.5bar Pressure drop and 909m/s C* with 99% C* efficiency recorded.
Join the discussion on the latest in AM for rockets in the 3D Printed Ceramic Catalyst Bed forum thread over at 3DPB.com.
Subscribe to Our Email Newsletter
Stay up-to-date on all the latest news from the 3D printing industry and receive information and offers from third party vendors.
You May Also Like
3DPOD Episode 198: High Speed Sintering with Neil Hopkinson, VP of AM at Stratasys
Neil Hopkinson, a pioneering 3D printing researcher, played a pivotal role in developing a body of research that is widely utilized today. He also invented High Speed Sintering (HSS), also...
GE Additive Transforms into Colibrium Additive in New Brand Move
One of the largest and most compelling companies in the 3D printing industry, GE Additive, has undergone a rebrand. Now, known as Colibrium Additive, the company and its new name...
HP & INDO-MIM Collaborate to Boost Metal 3D Printing in India
HP Inc. and INDO-MIM, a US- and India-based supplier of metal injection molding (MIM) powders and contract manufacturer, have announced that the two companies will collaborate to accelerate additive manufacturing...
Nylon 3D Printed Parts Made More Functional with Coatings & Colors
Parts 3D printed from polyamide (PA, Nylon) 12 using powder bed fusion (PBF) are a mainstay in the additive manufacturing (AM) industry. While post-finishing processes have improved the porosity of...