Maker and self-professed “polygeek” Todd Schlemmer combined his love of Japanese monster films, cameras and photography, 3D design and printing, and open sharing to create what he calls his “terraPin Kaiju 6×18 Pinhole Gamera,” for which Schlemmer has shared instructions and .stl files on Thingiverse.
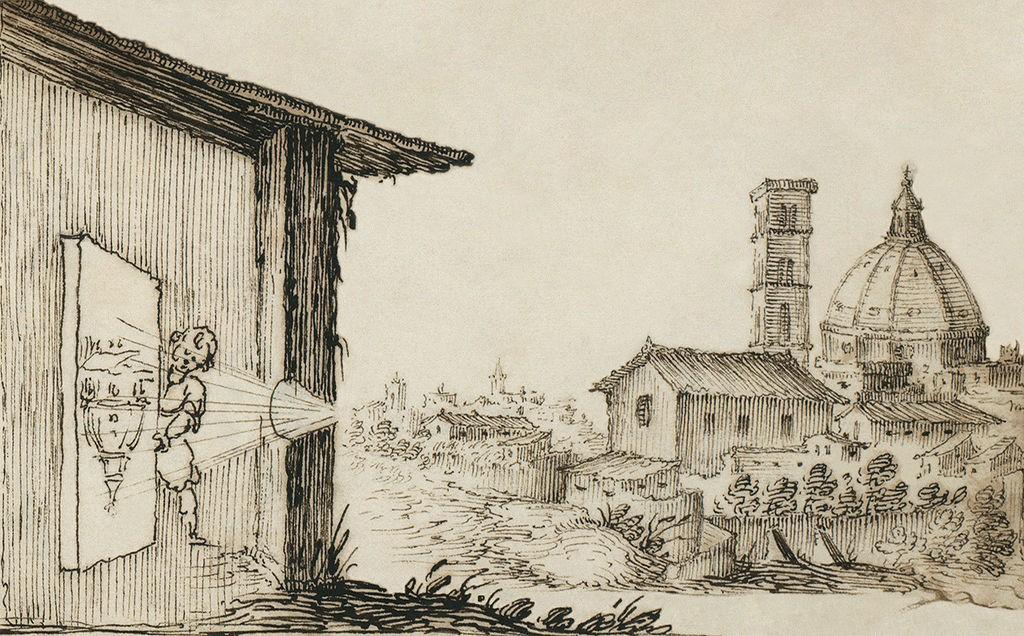
Camera Obscure, from a manuscript of military designs, Illustration of camera obscura from “Sketchbook on military art, including geometry, fortifications, artillery, mechanics, and pyrotechnics,” possibly Italian, c. Library of Congress.
“Kaiju” is a Japanese word that means “monster.” It refers to a genre of tokusatsu, or special effects entertainment. Kaiju films typically feature monsters of all kinds and the monsters are most often laying siege to a major Japanese city. Or, they’re fighting other monsters. Think Godzilla and Megalon, for example. Schlemmer grew up watching Kaiju movies and his favorite monster was Gamera, a rocket-powered flying turtle beast. And that’s the inspiration for the camera. In his words:
“The terraPin Kaiju is a giant, mutant pinhole Gamera!”
What’s a pinhole camera, though? It’s the most basic kind of camera there is. It is a variation on the camera obscura (in Latin that’s “dark chamber”), the earliest camera–but smaller and super minimalist. It’s an optical device that consists of a box (larger ones can even be entire rooms) with a hole in one side of it. Light from a scene outside of the box passes through the hole and strikes an interior surface. There it is reproduced upside down but with the color and perspective of the scene preserved. The image can be projected on light-sensitive paper or can be traced by hand onto a piece of paper. Exposure time can range from about five seconds to several hours. The best photos are of static scenes.
Schlemmer’s Pinhole Gamera uses 120 film, which is good for still photos. He shared several examples of photos he’s taken with it and they are surprisingly good–although none (so far!) capture the kind of creatures for whom the camera is named.
As for the appearance of the Gamera itself, it’s probably obvious that the embellishment on the exterior is purely decorative, albeit pretty cool.
Some finishing of the 3D printed parts is required to ensure that the pieces fit together properly as, it probably goes without saying, even the smallest amount of light that gets in from somewhere other than the pinhole is unwelcome.
Once you’ve made your own Pinhole Gamera, you’ll want to refer back to the Thing page for Schlemmer’s instructions for using the device, including loading the film onto the spools and winding it. He’s more than happy to respond to questions as well via the comments section so that others can benefit from the Q&A as well.
According to Schlemmer, it’s his “mission to share and promote open source cameras and related parts created with CAD applications and 3D printing.” We love the way that this camera, the Pinhole Gamera, combines the latest technology–3D design and printing–with the long-standing technology of the first, rudimentary camera. Let us know what you think of this fun take on photography in the 3D Printed Gamera forum thread over at 3DPB.com.
Subscribe to Our Email Newsletter
Stay up-to-date on all the latest news from the 3D printing industry and receive information and offers from third party vendors.
Print Services
Upload your 3D Models and get them printed quickly and efficiently.
You May Also Like
The Market and Industry Potential of Multi-Material 3D and 4D Printing in Additive Electronics
Additive manufacturing leverages computer-based software to create components for products by depositing either dielectric or conductive materials, layer by layer, into different geometric shapes. Since its birth in the 1980s,...
3DPOD 262: Bio-inspired Design for AM with Dhruv Bhate, Arizona State University
Dhruv Bhate is an associate professor at Arizona State University. There, he looks at structures, materials, and design. Previously, he worked at PADT as well as in the semiconductor and...
3DPOD 261: Tooling and Cooling for AM with Jason Murphy, NXC MFG
Jason Murphy´s NXC MFG (Next Chapter Manufacturing) is not a generalist service; instead, the company specializes in making tooling. Using LPBF and binder jet, the company produces some of the...
3DPOD 260: John Hart on VulcanForms, MIT, Desktop Metal and More
John Hart is a Professor at MIT; he´s also the director of the Laboratory for Manufacturing and Productivity as well as the director of the Center for Advanced Production Technologies....