It can be you, or your family member, neighbor, coworker, or friend — but odds are, you know someone affected by diabetes. The International Diabetes Federation puts current estimates of diabetics across the world at 387 million, and expects to see that number increase to 592 million within the next two decades. Type 1 diabetes can cause blindness, cardiac disease, kidney failure, neuropathy, retinopathy, and other -opathies that sufferers can only ward off through intensely calculated control of their glucose levels, often utilizing internal insulin pumps. Maintaining proper, healthy glucose levels requires constant monitoring, expensive equipment, and a level of discomfort from physical equipment needs.
But that could all change, thanks to additive manufacturing-focused research from Oregon State University.
In a paper published in the ECS Journal of Solid State Science and Technology and supported by the National Institutes of Health, titled “Fabrication of a Flexible Amperometric Glucose Sensor Using Additive Processes,” researchers look into the possibility of bringing additive manufacturing techniques to work for an enhanced glucose sensor for Type 1 diabetics. Combined with an artificial pancreas system, the goal is to create a lower-cost, more comfortable management of diabetes, which will provide benefits to patients and providers alike.
OSU already has a patent application in for the system, and Pacific Diabetes Technologies will commercialize it once it becomes market viable. Testing is taking place now with animals, and signs are good that progress into human subjects will commence in the near future.
“These are disposable devices that only last about a week and then need to be replaced,” Associate Professor of Chemical Engineering Dr. Greg Herman said. “Some other approaches used to make them might waste up to 90 percent of the materials being used, and that’s a problem in a throw-away sensor. It’s also important to keep costs as low as possible, and printing systems are inherently low-cost.”
Through use of additive manufacturing techniques, researchers were able to improve upon current designs of glucose monitoring systems. “E-jet” (electrohydrodynamic jet) printing is to create the system’s sensor. This type of printing, reminiscent of inkjet printing techniques, uses biomaterials rather than ink, thus creating printed objects made of, for example, enzymes. In addition to the bio-“ink” material, incredibly thin substrates are key to the success of this design. Through use of fine plastic substrates — about as thin as familiar cling wrap seen in kitchen drawers everywhere — with the biomaterial, a sensor could be created that wraps around a catheter serving as the artificial pancreas system. This all-in-one system would need just one single point of entry into the body to serve its function, whereas those in use now require four different points of entry.
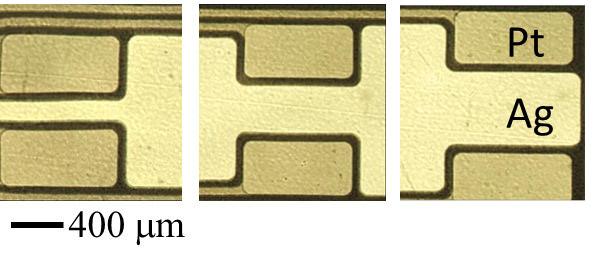
Gold films patterned on substrate via microcontract printing and etching (credit: Oregon State University)
“The challenges of making these sensors on such thin plastic films were difficult to overcome, but we found that additive manufacturing approaches simplified the process, and should lead to much lower costs,” said Dr. John Conley, Jr., an OSU professor of electrical and computer engineering.
Once the high-tech thin systems are created, their purpose is to constantly monitor glucose levels in the blood, sending that data to portable infusion pumps to provide proper levels of hormones (insulin and glucagon) into the bloodstream and maintain blood glucose levels in a safe range.
While the initial work focuses on Type 1 diabetes, this system is designed as a springboard from which to grow, ultimately intended to be helpful as well for Type 2 diabetes — and for the monitoring of other biological markers.
“This technology and other work that could evolve from it should improve a patient’s health, comfort and diabetes management,” said Dr. Herman.
Research on this front appears to be headed in the right direction, and the use of 3D printing technology is now on its way to making quite a splash in the day-to-day life of Type 1 diabetics.
You can read the whole study on the ECS website. The summary findings of the conclusion in particular are attention-grabbing for the promise they hold for the results of the work at hand and its implications for the future:
“This study demonstrates that a continuous glucose sensor can be fabricated on a flexible polyimide substrate using additive technologies. We were able to use electrohydrodynamic printing to deposit and pattern a biological ink (containing glucose oxidase, bovine serum albumin, and glutaraldehyde as a cross-linking agent) with high resolution on the sensors working electrodes. The GOx enzyme was found to be active after e-jet printing. PFSA was used as a permselective membrane and its thickness was optimized to obtain a linear response for glucose concentrations up to 32 mM, as well as to minimize the detection of interfering molecules (e.g., acetaminophen). The flexible sensor design developed in these studies can ultimately be used within a closed loop artificial pancreas control system thereby reducing the number of components in such a system.”
Does additive manufacturing truly hold the key to diabetes research and patient health? Let us know what you think in the Diabetes Maintenance forum thread over at 3DPB.com.
Subscribe to Our Email Newsletter
Stay up-to-date on all the latest news from the 3D printing industry and receive information and offers from third party vendors.
Print Services
Upload your 3D Models and get them printed quickly and efficiently.
You May Also Like
Reinventing Reindustrialization: Why NAVWAR Project Manager Spencer Koroly Invented a Made-in-America 3D Printer
It has become virtually impossible to regularly follow additive manufacturing (AM) industry news and not stumble across the term “defense industrial base” (DIB), a concept encompassing all the many diverse...
Inside The Barnes Global Advisors’ Vision for a Stronger AM Ecosystem
As additive manufacturing (AM) continues to revolutionize the industrial landscape, Pittsburgh-based consultancy The Barnes Global Advisors (TBGA) is helping shape what that future looks like. As the largest independent AM...
Ruggedized: How USMC Innovation Officer Matt Pine Navigates 3D Printing in the Military
Disclaimer: Matt Pine’s views are not the views of the Department of Defense nor the U.S. Marine Corps Throughout this decade thus far, the military’s adoption of additive manufacturing (AM)...
U.S. Congress Calls Out 3D Printing in Proposal for Commercial Reserve Manufacturing Network
Last week, the U.S. House of Representatives’ Appropriations Committee moved the FY 2026 defense bill forward to the House floor. Included in the legislation is a $131 million proposal for...