The Western hemisphere’s largest manufacturing trade show, the International Manufacturing Technology Show (IMTS), returned to Chicago for another year, graciously including a 3D printing section once again in its West Building. There, additive manufacturing (AM) firms were able to showcase their wares to the broader world of production.
Despite the fact that the AM exhibition was smaller than two years prior, largely due to the overall economic slump that machine manufacturers have experienced, the industrialization of 3D printing was largely on display. This was evidenced by some unique trends that the sector showcased at IMTS, including a focus on tooling, new methods of integrating the technology into other workflows, management changes, and the broadened focus of some suppliers.
3DPrint.com was on the show floor and on the Formnext Stage to analyze and reflect the state of the AM sector through the frame of IMTS 2024.
AM for Tooling
In the past, AM companies, particularly manufacturers of metal powder bed fusion (PBF), equipment have neglected the tooling sector to some degree. That isn’t to say that original equipment manufacturers (OEMs) weren’t selling machines to toolmakers or even exploring how conformal cooling could be worked into 3D printed tools for better performance. However, it was the extremely high-performance applications that seemed to be driving their marketing and sales activities. Metal PBF manufacturers specifically were selling machines to aerospace and new space companies, knowing that these were the firms that could afford high-priced PBF equipment.

A large-format composite molding tool created by Thermwood.
In contrast, this year demonstrated that legacy OEMs were turning their attention to various kinds of tooling once more, whether that be metal tools for injection molding or burnout patterns for investment casting. It seemed to me that, even before the event took place, the focus of the AM exhibition’s marketing on large-format polymer printing for tooling foreshadowed this emphasis. On the ground, it was clear that everyone was becoming aware of general industry’s adoption of AM as an indirect manufacturing method.
Mantle
The script was flipped in 2022, where Bay Area startup Mantle debuted its P-200 Printer, which combines metal paste extrusion with CNC machining to create injection molding tools featuring +/- 0.001″ per inch accuracy. In 2024, it seemed to me that legacy AM OEMs were taking a cue from Mantle’s decision not to focus on 3D printing series of individual end parts, but instead on the tools that enable the production of millions of components.
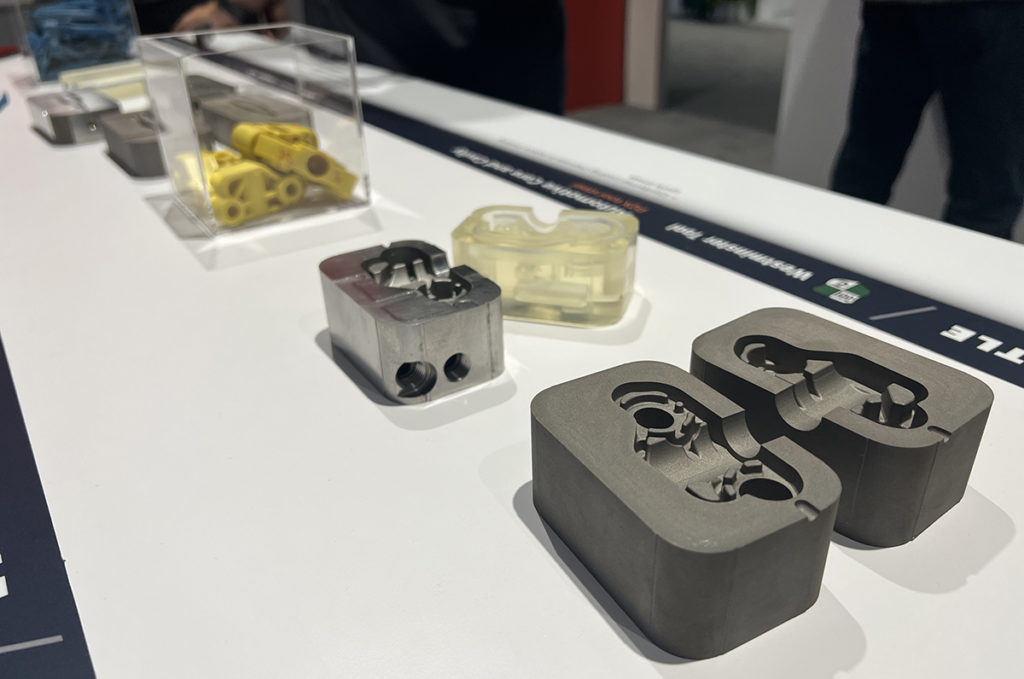
3D printed metal molds made by Mantle for injection molding.
“’Tooling’ used to be sort of a bad word. Everybody was like, ‘you’ve got to have direct part production to be successful in additive,’ but I think there’s a lot more interest in it because people have started to realize that we stopped drinking the Kool-Aid, that we’re not going to 3D print everything. 99% of plastic parts are made with injection mold. Way less than 1% is done with 3D printing. So, the bigger application area in today’s market is supporting existing ways of making things like a tooling product,” said Mantle CEO Ted Sorom. “Everyone can throw a tool steel in their printers and print tool steel. I think what it comes down to is understanding enough about the [tooling] industry to know what tool makers actually care about and that’s who we spend most of our time on. Whether it is the metal quality, the surface finish, or all of the other processing afterwards—welding and EDM and other things—we’ve gone so much deeper than everybody else to understand those needs, so we know what tool makers want.”
For that reason, Mantle has seen immense success, most recently a $20 million funding round in July. With the investment, the company is focusing primarily on scaling up the production of its machines in order to meet the high demand the startup has seen, as well as taking on new staff to service them.
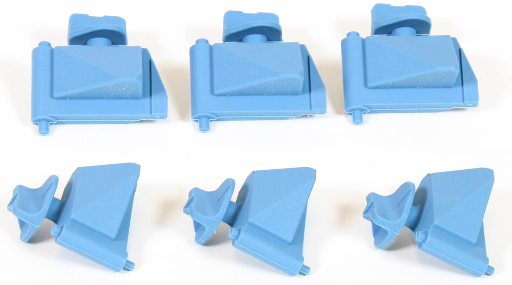
Molded parts for Gamber-Johnson. Image courtesy of Mantle.
“We have done all of the product development needed to get the system that delivers strong value to customers,” Sorom said. “Most of the innovation we do for the next few years will be on the software side: Improving our process, speeding it up. We’ve made it so that we can deliver a 30% speed improvement to the machine with software alone. I don’t think there’s many other people out there that can say they can increase the speed of their machine by 30% without a hardware change.”
3D Systems
With a sweeping portfolio that covers nearly every technology and material, 3D Systems (NYSE: DDD) is well-positioned in nearly every market. This includes the semiconductor sector, where AM’s penetration is growing at a rapid clip. However, in addition to parts for semiconductors, 3D Systems’ primary focus at IMTS was on tools for such traditional production technologies as investment casting.
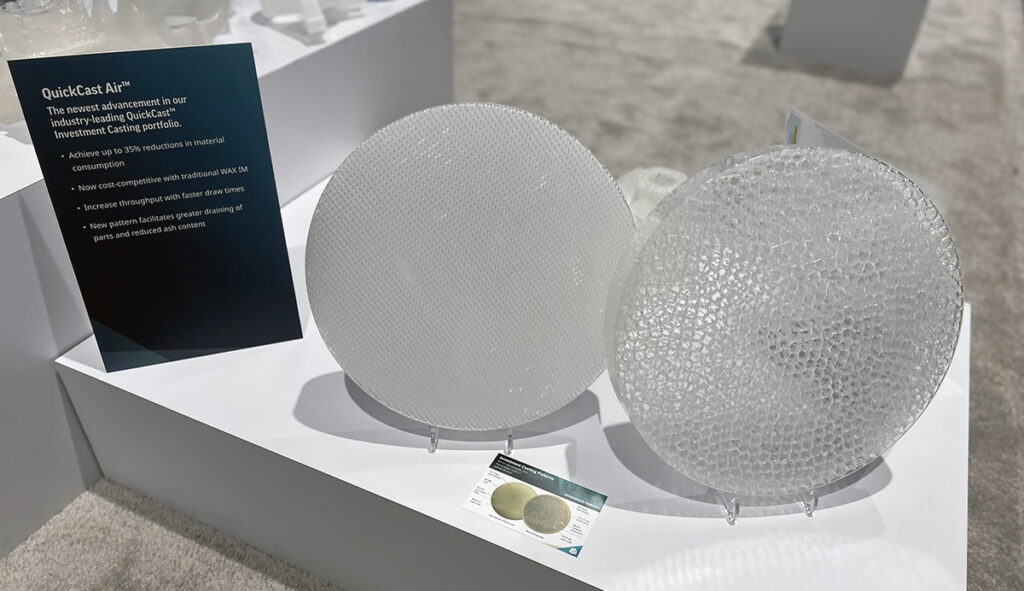
3D printed QuickCast Air parts from 3D Systems.
At the show, 3D Systems unveiled a solution dubbed QuickCast Air, a stereolithography workflow for 3D printing casting patterns. Via the company’s 3D Sprint software, users are able to 3D print lightweight, hollow casting patterns with enhanced burnout and drainage efficiency, making it cost-competitive with traditional wax patterns.
“Historically, 3D printing has presented a long list of value propositions, including that it’s faster and there’s no tooling. You have flexibility to change your design on the fly. There is very little constraint in geometric complexity, so you can design and engineer in step changes in performance and, and efficiency,” Patrick Dunne, Vice President of Advanced Application Development at 3D Systems Corporation, told 3DPrint.com. “However, there’s always been that question about part per pound economics. If you ask a 3D printing company how much their material is, it’s typically $90 to $120 per pound, which compares to $10 per pound for injection molding material.”
Dunne continued, “The realization was that, because 3D printing is really good at making complex shapes, we could turn the part inside out and start making investment casting patterns hyper efficient, potentially so efficient that we could get to a scenario where the part cost is less. You take a CAD file in 3D Sprint, and, in the pulldown menu, you select QuickCast Air. It produces a part that is 5% plastic and 95% air, essentially, so, even though the material is 10 times more expensive, the material in the actual part is $5, half the price of wax.”
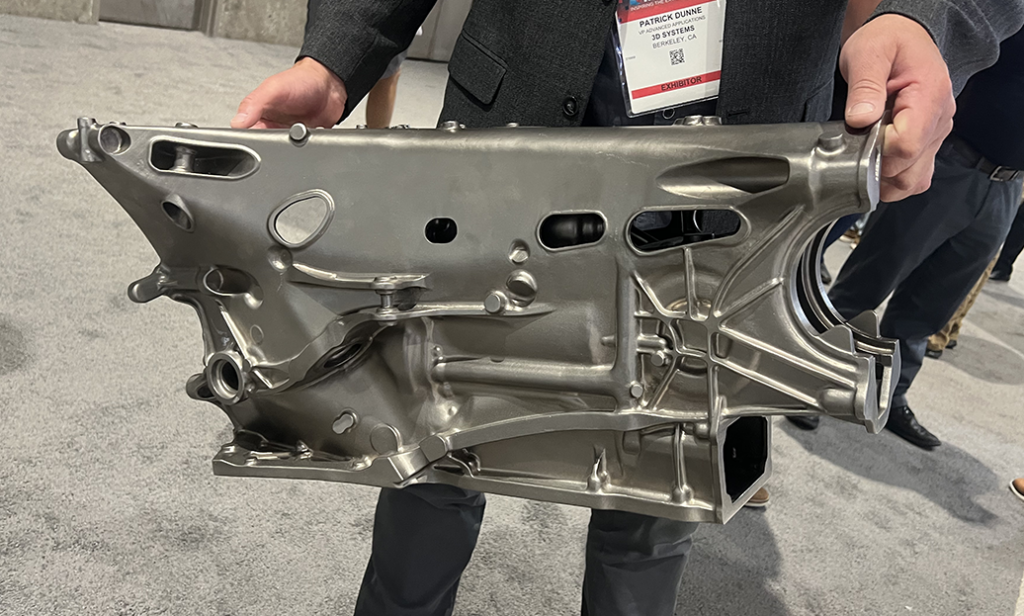
An investment casted metal part made using a 3D printed QuickCast Air pattern.
By printing hollow casting patterns, QuickCast Air is able to change the material economics of pattern production. The solution optimizes material removal, reducing consumption by up to 50% and significantly shortening build times. In turn, 3D Systems is hoping to conquer a chunk of the investment casting market, projected to reach $33.9 billion by 2034.
Additive Industries
The trend was also echoed by Additive Industries, a Dutch manufacturer of high-end, highly automated laser PBF machines. Fatos Derguti, Product Manager at the company, highlighted the evolving focus of AM companies, particularly in the US, toward more practical, real-world applications, such as tooling.
While traditionally many AM companies emphasized high-end applications like turbines and rocket engines, there is now a growing trend to revisit tooling due to its potential profitability and practicality. Derguti mentioned that industries, especially automotive, benefit from the flexibility offered by AM in quickly adapting to regulatory changes and production demands. “Tooling is obviously, especially in the automotive industry, a key area, given the configurability of machines and the constant need for rapid changes in engine size and design,” Derguti explained.
He also noted that many established industries are hesitant to invest in innovative AM technologies due to the associated costs. However, as newer companies demonstrate successful use cases, more traditional manufacturers are starting to recognize the benefits. “We’re seeing a shift as established companies are now dipping their toes into AM once they witness others doing better and more advanced work,” he added.
This was one of the reasons Additive Industries developed the MetalFab 300 Flex system. The Dutch company jumped into the market with essentially the most sophisticated and automated laser PBF machine imaginable, ideal for aerospace companies with the budget for extremely high-throughput metal 3D printers. However, as companies at large begin to understand the benefits of AM to their own verticals, Additive Industries introduced a more cost-effective machine.
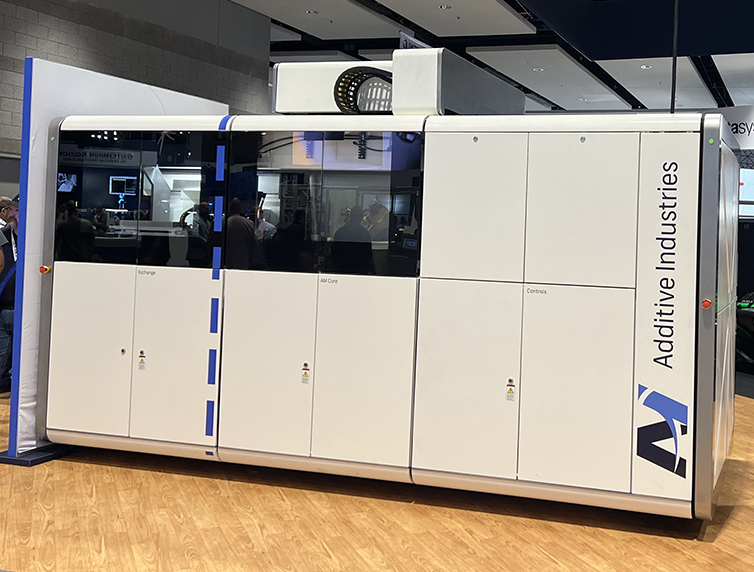
The MetalFab 3D printer at IMTS.
Derguti explained that the firm developed the Flex to help customers, particularly those who need automation but face limited budgets, transition into AM more easily. He stated, “We soften the blow of CapEx by starting with something small, and as companies grow, they can expand into more advanced automation.” This approach aims to meet the needs of various users, from contract manufacturers to universities and startups, by offering compact, highly efficient machines. Interestingly, the first client to purchase one was an existing customer in the industrial baking sector, K3D.
The maturation of AM was also evidenced by the expansion of material suppliers into other, non-additive sectors, management changes at unique 3D printing startups, and the integration of AM into broader manufacturing workflows, all of which will be discussed in greater depth in the next article in this series.
Subscribe to Our Email Newsletter
Stay up-to-date on all the latest news from the 3D printing industry and receive information and offers from third party vendors.
Print Services
Upload your 3D Models and get them printed quickly and efficiently.
You May Also Like
The Dental Additive Manufacturing Market Could Nearly Double by 2033, According to AM Research
According to an AM Research report from 2024, the medical device industry, specifically in dentistry, prosthetics, and audiology, is expected to see significant growth as these segments continue to benefit from...
Heating Up: 3D Systems’ Scott Green Discusses 3D Printing’s Potential in the Data Center Industry
The relentless rise of NVIDIA, the steadily increasing pledges of major private and public investments in national infrastructure projects around the world, and the general cultural obsession with AI have...
AM Research Webinar Explores Continuum’s Sustainable Metal Additive Manufacturing Powders
Metal additive manufacturing (AM) powder supplier Continuum Powders is working to develop solutions that empower industries to reduce waste and optimize their resources. An independent life cycle assessment (LCA) of...
3D Printed Footwear Startup Koobz Lands $7.2M in Seed Round
California-based Koobz is focused on reshoring the U.S. footwear supply chain with advanced manufacturing processes, including 3D printing. The startup just announced that it has added $6 million to its...