In 3D Printing News Briefs today, four graduate students received $10,000 scholarships from ASTM International, and 3DPRINTUK announced the first commercial launch of the Stratasys SAF printer in the UK. The University of Wisconsin-Madison is leading a $9.1 million project funded by the Office of Naval Research to improve laser powder bed fusion, and B&T USA has introduced the next generation of its 3D printed gun suppressor. Rains has launched its second footwear collaboration with Zellerfeld, and one man used an ingenious 3D printed solution to keep his pool clean.
ASTM International Awards Scholarships to Graduate Students
ASTM International is proud to announce the four 2024 graduate students to whom it has awarded $10,000 scholarships. The pool of applicants this year was very competitive, as students apply for awards for their studies in fields where technical standards play a key part. There are more than 5,000 student members of the organization, at varying levels of education, who don’t have to pay to belong. Undergraduate and graduate student members have a great opportunity to see the standards development process firsthand, network with technical experts, and participate in discussions about standards. Each year, ASTM offers its student members multiple grant and scholarship opportunities.
The candidates receiving the 2024 ASTM International graduate scholarships are as follows:
- Lane Flora, an applications engineer at Jacobi Carbons, pursuing a Master of Science in chemical engineering from The Ohio State University. She will soon start as technical director at Jacobi Carbons, and use ASTM standards to advance high quality standards. Flora is a member of several ASTM committees, including activated carbon (D28), air quality (D22), and water (D19).
- Melissa Armistead, a PhD student in fiber and polymer science at North Carolina State University. As a member of ASTM’s personal protective clothing and equipment committee (F23), Armistead uses ASTM standards to improve comfort and safety for textiles used in firefighting.
- Pandora K. Picariello, a PhD student in materials science at Colorado School of Mines. Picariello will soon begin her career in the field at an internship with Canopy Aerospace, where she will use her experience in additive manufacturing with ASTM and the National Institute of Standards and Technology (NIST).
- Vishnu Ramasamy, a PhD student graduate research assistant in materials science and engineering at Case Western Reserve University. After working with ASTM’s additive manufacturing committee (F42), Ramasamy is pursuing a career in AM, and hopes to develop standards for hybrid AM processes.
3DPRINTUK Adds First Commercially Available SAF Printer in the UK
London 3D printing service bureau 3DPRINTUK has added the first commercially available SAF H350 production printer from Stratasys in the UK to its portfolio, growing its manufacturing capacity and capabilities for 3D printing high-quality polymer powder bed fusion parts. SAF, or Selective Absorption Fusion, is based on the high-speed sintering process developed by Professor Neil Hopkinson, VP of Additive Manufacturing Technology at Stratasys. The H350, with its high nesting density capability, was developed to produce efficient part part volumes. Additionally, SAF technology allows 3DPRINTUK to add sustainable biopolymer Polyamide 11 (PA11) to its materials line. This durable Nylon material is stronger and less rigid than PA12, with high impact resistance, excellent thermal resistance, and a lower environmental impact. It’s suited to a number of applications, including electrical enclosures and drone components. 3DPRINTUK will focus on 3D printing PA11 with its SAF printer, and is offering free sample parts with each order.
“We have built our reputation as a service provider of high-quality polymer 3D printed parts on demand over many years. This means that we have extensive expertise and experience in this area. When Stratasys introduced the SAF process, it was a new and interesting proposition that we could not ignore and the addition of the SAF H350 machine slots comfortably into our extensive portfolio,” explained Nick Allen, the CEO of 3DPRINTUK. “Incidentally, the SAF H350 system is the first one of its kind being used by a service provider in the UK, so we are looking forward to showing our clients what it is capable of. And, in the tradition of 3DPRINTUK, we have tested the system to the extreme over an 18-month period to ensure that the consistency and quality of parts meets the standards of 3DPRINTUK. Launching the machine as part of our service will significantly extend our output and capacity.”
UW-Madison Leading ONR-Funded Project to Improve LPBF
A $9.1 million project funded by the U.S. Office of Naval Research (ONR) is being led by the University of Wisconsin-Madison. LPBF can print parts with complex geometries, but there’s too much part variation in microstructure, dimensional accuracy, residual stress, porosity, and fatigue life, and from different printers. Adoption of LPBF is thus slowed, as this variability gets in the way of efficient and effective qualification of 3D printed parts. So the overall goal is to improve LPBF technology, and “enable broader usage” of AM, particularly in manufacturing mission-critical components for defense applications. Hopefully, the research will result in LPBF better part performance. Lead principal investigator on the project is UNW Mechanical Engineering Professor Xiaoping Qian, and the team includes mechanical engineering faculty Curt Bronkhorst, Lianyi Chen, Shiva Rudraraju, Krishnan Suresh and Jinlong Wu. Researchers from Colibrium Additive, Intact Solutions, and GE Aerospace Research are also participating.
“The goal of this project is to develop computational methods for efficient qualification of additive manufactured parts and to exploit mechanical property variability in additive manufacturing, such as changes in microstructures and porosity, as increased design freedom for process-part co-design,” Adam Malecek, UW-Madison Department of Mechanical Engineering, wrote. “Such process-part co-design will essentially treat process variability as a feature instead of an obstacle in quality control. The researchers aim to simultaneously optimize process control variables, part geometry and material properties in which material properties will be varied through additive manufacturing process control.”
B&T USA Introduces New 3D Printed Gun Suppressors
Florida-based firearms, suppressor, and accessories manufacturer B&T USA, which operates under the license of B&T AG SWITZERLAND, introduced the next generation of its 3D printed Rotex and SRBS models. Part of its Print-X family, these suppressors are easy to identify because of B&T’s signature bead blasted gray finish and new tube texturing. The company uses LPBF technology to print its Rotex and SRBS suppressors out of 718 Inconel or titanium. These models are completely weldless, which reduces failure points and weight, have industry-leading flash suppression, and feature B&T’s patent-pending high-performance Star Baffle system, which offer greater sound suppression, less backpressure, and is now available in 3D printed form. There is no change to pricing, and both models are available for purchase in 5.56 NATO and 7.62 NATO calibers through authorized distributors and dealers.
“The improvements made to our 3D printed SRBS and Rotex suppressors within the Print-X family are examples of how our customers and end-users continue to reap the benefits of our R&D team continually pushing what is possible in both material and design. As a suppressor manufacturer with nearly 700 different suppressors, it’s safe to say our engineering team refuses to leave well enough alone and our products are in a perpetual state of advancement to ensure our customers receive the most cutting-edge technology possible, providing them with a substantial advantage in the field,” said Chris Mudgett, Vice President of Marketing for B&T USA.
You can learn more about the 3D printed small arms silencer market in this new report by AM Research.
Rains & Zellerfeld Launch 3D Printed Sculptural Zip Mules
Scandinavian urban outerwear and lifestyle brand Rains has launched its second 3D printed shoe with German 3D printed footwear company Zellerfeld, just months after the latter moved its platform out of beta. The first was last year’s 3D printed Puffer Sneaker, and now the duo is back with the 3D printed Zip Mule, with a sculptural shape inspired by the oversized zippers on Rains’ signature puffer jackets. The slip-on shoes come in orange, oat, and black colorways, and are 3D printed to order. TPU is used to print the mule, due to its odor-resistance and quick drying. This material also makes it possible to wash the shoes, and reduce footwear maintenance. The new Rains Zip Mule features the TextureMap innovation from Zellerfeld, which combines different texture finishes across multiple sections of the shoe’s silhouette.
“Working with Rains is always thrilling. Their commitment to innovation sets them apart in the industry, and their continued trust in 3D-printed footwear and our platform inspires us to keep pushing,” said Cornelius Schmitt, CEO and Co-Founder of Zellerfeld. “The Rains Zip Mule is just another product that showcases our synergies: a never-before-seen mule style combined with incredibly soft uppers. We’re excited for what’s next and look forward to creating more groundbreaking designs together!”
DIY 3D Printed Pool Maintenance
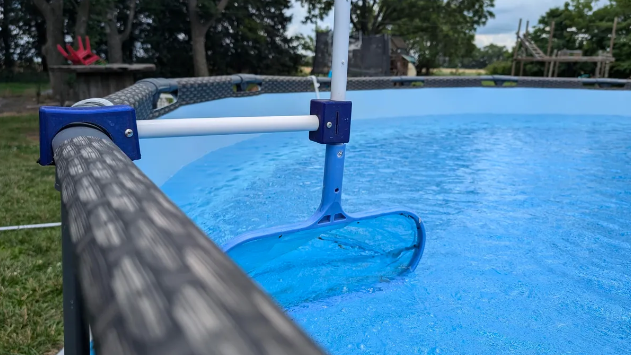
Using a 3D printer, PETG filament, a pool skimmer net and some PVC, my pool is cleaner than ever.
Chris Wedel/CNET
On hot days, taking a dip in the swimming pool can feel like heaven. But it can be hell maintaining your own pool, especially when it comes to removing all the leaves, bugs, and other debris that end up in the water. Chris Wedel, Home Tech Editor for CNET, turned to 3D printing to keep his at-home pool clean. He found a hack for a commonly used pool skimmer on Printables, and 3D printed it on his Bambu Lab A1 Mini out of PETG, which has great resistance to UV rays and can withstand direct sunlight and high temperatures. He also found and printed another Printables design, which directs filtered water coming into the pool in a circular flow. The model fits right onto the nozzle attachment for a pool filter, and actually helps the pool skimmer work better. Once everything was printed, Wedel screwed some 1″ pieces of PVC pipe from his pool net to one 3D printed piece, and another 3D printed piece to the frame of the pool. Then, Velcro cable ties were used to attach the updated skimmer to the frame.
“Finally, I switched off the pool pump, removed the filter outlet that came with the filter, and then threaded it into the 90-degree outlet I had printed. Now, for the moment of truth: it was time to turn the pump back on, and fortunately, it worked,” Wedel wrote.
“Water flowed and began swirling around the pool, and little bits of debris and bugs on the water’s surface started going into the net. Now, at the end of each day, I simply remove the Velcro and use a garden hose to rinse out the net and then reattach it for the next day.”
What a great idea!
Subscribe to Our Email Newsletter
Stay up-to-date on all the latest news from the 3D printing industry and receive information and offers from third party vendors.
Print Services
Upload your 3D Models and get them printed quickly and efficiently.
You May Also Like
Havaianas Collaborates with Zellerfeld to Launch 3D Printed Flip-Flops
The shoe of the summer is undoubtedly the flip-flop. Easy on, easy off, your feet won’t get sweaty because there’s not much material, and they’re available in a veritable rainbow...
UCLA Researchers Develop 3D Printed Pen that May Help Detect Parkinson’s Disease
Diagnosing Parkinson’s disease is difficult. Often, early symptoms of the progressive neurological condition may be overlooked, or mistaken for signs of aging. Early diagnosis can help save lives and improve...
Printing Money Episode 30: Q1 2025 Public 3D Printing Earnings Review with Troy Jensen, Cantor Fitzgerald
Printing Money is back with Episode 30, and it’s that quarterly time, so we are happy and thankful to welcome back Troy Jensen (Managing Director, Cantor Fitzgerald) to review the...
Heating Up: 3D Systems’ Scott Green Discusses 3D Printing’s Potential in the Data Center Industry
The relentless rise of NVIDIA, the steadily increasing pledges of major private and public investments in national infrastructure projects around the world, and the general cultural obsession with AI have...