In 3D Printing News Briefs today, A3D Manufacturing received an important aerospace certification, and Photocentric introduced its new large-format 3D printer array, called JENI. Black Diamond is using Formlabs technology to speed up production of its high-performance gear. Finally, the first 3D printed house in Central Asia was constructed in Kazakhstan.
IAQG Grants AS9100 Certification to A3D Manufacturing
Manufacturing as a Service (MaaS) provider A3D Manufacturing received AS9100 certification from the International Aerospace Quality Group (IAQG), which ensures that all of the company’s procedures, components, and technologies meet the IAQG’s most rigorous safety and quality standards, and gives its customers peace of mind. In the aviation, defense, and space industries, every single component installed in the final product is designed to withstand extreme conditions like high speeds, atmospheric pressures, and quickly shifting temperatures, and so have to meet the highest quality standards and be manufactured with extreme precision. To become certified to the AS9100 standard, manufacturers like A3D Manufacturing must undergo a comprehensive audit and have its procedures and processes evaluated for precision and quality.
“A3D Manufacturing is a trusted source of components and parts for many customers in the aerospace sector. The sector is unique in that components are designed to withstand extreme conditions such as atmospheric pressures, rapidly shifting temperatures, and high speeds that could otherwise affect performance, durability, and safety. Our customers rely on us to deliver the highest-quality components every time, and the AS9100 certification assures them that we are up to the task,” said Jon Toews, Senior Vice President of A3D Manufacturing.
Photocentric’s New Large Automated JENI 3D Printer Array
Four years ago, LCD screen 3D printing company Photocentric set up a print farm, which produced 50,000 parts per day while it was in operation. Now, the company presents the culmination of that experience in its latest system: JENI, a fully automated, modular, resin 3D printer array. It’s not just a printer—JENI includes printing, washing, rinsing, and curing nodes, and a super-fast robot gantry moves parts seamlessly between them. JENI is adaptable and scalable, as users can customize the number and type of nodes they want to best fit production needs, and adjust the system’s build volume to fit their output requirements. The company says the array prints high-quality parts at an impressive rate of one platform every 20 seconds, without tooling, and it works with BASF Ultracur3D resins. Depending on the configuration, it offers a single or three phase power input, uses Photocentric Conductor software, and achieves 25-350µm layer thickness. It sounds like an excellent way to achieve true mass manufacturing.
“We’re taking 3D printing intelligently into mass production with unmatched efficiency and scalability,” Photocentric’s Managing Director Paul Holt said in a video.
“We’ve 3D printed millions of objects, and we’ve learned how to truly mass manufacture, and we’re bringing that ability to you with JENI.”
Black Diamond & Formlabs 3D Printing High-Performance Sporting Gear
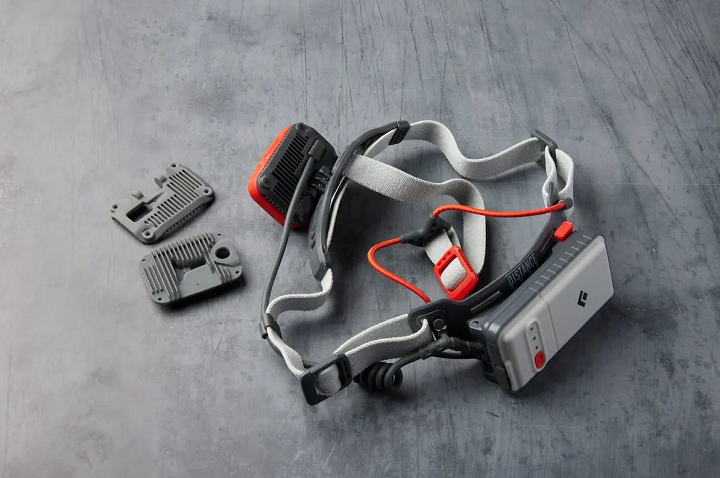
Form 4’s speed enabled Tetzl to run three different iterations of this headlamp component (left, Grey Resin V5) in one day.
Black Diamond Equipment manufactures high-performance gear for climbing, skiing, and mountain sports, and is working with Formlabs to ramp up its production, while keeping costs down. Over the years, its design team has added many Formlabs machines to its 3D printing fleet. The super-fast speed of the plug and play Form 4 gave Black Diamond a great incentive to switch from SLS printing back to resin, as it enables the company to speed up important testing time for climbing gear, including helmets, ice tools, and trekking poles by achieving same-day delivery of early prototypes and end-use functional test prints. The company has also moved from just using the Form 3L to print helmet prototypes—now they use it to print full-size prototypes of detailed footwear midsoles and ice tool grips as well. Black Diamond also put the Formlabs Form 4 and new Grey Resin V5 to the test making a lightweight trekking pole, which lasted over a million cycles with 35 pounds of pressure each cycle.
“On one lighting project, we did three iterations in a single day — designed and printed three different parts before we had a meeting in the afternoon,” Black Diamond’s Product Design Lab Manager Matt Tetzl said about the Form 4.
“It’s been plug and play. As soon as you get it connected to the network, it’s the familiar Formlabs ecosystem — upload parts, push a button, get your parts back.
“99% of the time, I know I’ll have a successful print. And the other 1%, I know I can fix it myself. If a printer were to go down, I can get it operating on the same day. It’s super nice to have that reliability.”
First 3D Printed House in Central Asia Built in Kazakhstan
Finally, the first 3D printed home in Central Asia has been completed, and was built by BM Partners 3D Print in Almaty, Kazakhstan using COBOD 3D printers. The walls of the house were 3D printing in five days, with the entire 100-square-meter building constructed in less than two months. Because the city is prone to earthquakes, extra strong concrete by COBOD was used to construct the home so it’s able to withstand tremors of up to seven on the Richter scale. This special concrete mix has a compression strength of nearly 60 megapascals (MPa), and is typically used when building highly loaded structures, like skyscrapers and bridges. The home also features expanded polystyrene concrete for insulation, as the temperature variations in Kazakhstan are quite extreme. The total cost of this new 3D printed is about $21,800.
“Embracing modern technologies is essential in today’s world. Our company is committed to staying at the forefront of technological advancements with 3D construction printing within our country,” said Marat Oshakhtiev, the CEO of BM Partners. “With this project, our company has confidently stepped into the future, addressing Kazakhstan’s urgent need for earthquake resistant modernized, efficient and resilient housing solutions.”
Subscribe to Our Email Newsletter
Stay up-to-date on all the latest news from the 3D printing industry and receive information and offers from third party vendors.
Print Services
Upload your 3D Models and get them printed quickly and efficiently.
You May Also Like
The Market and Industry Potential of Multi-Material 3D and 4D Printing in Additive Electronics
Additive manufacturing leverages computer-based software to create components for products by depositing either dielectric or conductive materials, layer by layer, into different geometric shapes. Since its birth in the 1980s,...
3DPOD 262: Bio-inspired Design for AM with Dhruv Bhate, Arizona State University
Dhruv Bhate is an associate professor at Arizona State University. There, he looks at structures, materials, and design. Previously, he worked at PADT as well as in the semiconductor and...
3DPOD 261: Tooling and Cooling for AM with Jason Murphy, NXC MFG
Jason Murphy´s NXC MFG (Next Chapter Manufacturing) is not a generalist service; instead, the company specializes in making tooling. Using LPBF and binder jet, the company produces some of the...
3DPOD 260: John Hart on VulcanForms, MIT, Desktop Metal and More
John Hart is a Professor at MIT; he´s also the director of the Laboratory for Manufacturing and Productivity as well as the director of the Center for Advanced Production Technologies....