We’re starting with research in today’s 3D Printing News Briefs, first about filament diameter-adjustable 3D printing and then about 3D printed sensors. Then, we’re moving on to personalized 3D printed medical models, metal 3D printing sales, and internal combustion engines.
Filament Diameter-Adjustable 3D Printing for Gradient Matters
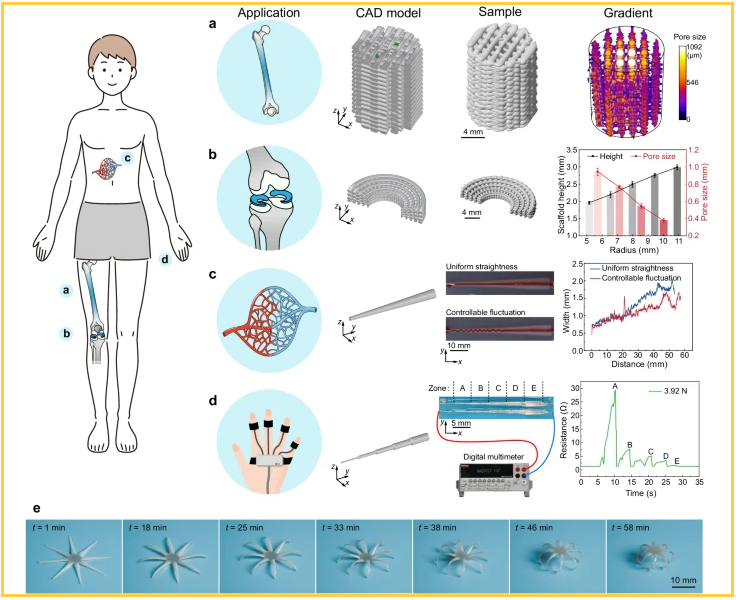
a) Cancellous-cortical bone-mimicking scaffold with radial gradient in pore sizes. b) Wedge-shaped meniscus-mimicking scaffold fabricated in one step without post-processing (mean ± s.d., n = 3). c) Vascular scaffold with continuously controllable width and deposition state based on coaxial FDA-3D printing. d) Flexible electronics. A pressure sensor was obtained from liquid metal (LMs) and polydimethylsiloxane (PDMS) based on coaxial FDA-3D printing. e) 4D printing. After calcium ion (Ca2+) cross-linking, the octopus-like alginate sample could support itself as the water evaporates at room temperature (25 °C) (Supplementary Video 9).
Natural matters, like bone and bamboo, have unique properties thanks to the hierarchical architecture of gradient structure. Scientists have made a lot of progress implementing bionic designs of gradient structures, but it’s still hard to precisely fabricate complex architectures like pore gradients. Direct ink writing (DIW) 3D printing has potential, as it can adjust the angle, spacing, and diameter between filaments to fabricate 1D and 2D hierarchical structures, but fixed parameters make it difficult to manufacture complex 3D gradient matters. A team of researchers from the Chinese Academy of Sciences and Harbin Institute of Technology in China and Radboud University in the Netherlands developed a filament diameter-adjustable 3D printing (FDA-3DP) strategy for fabricating DIW structures “with controllable gradients in pore sizes using variable filling density” using extrusion 3D printers.
“Here, we report a filament diameter-adjustable 3D printing strategy that enables conventional extrusion 3D printers to produce 1D, 2D, and 3D gradient matters with tunable heterogeneous structures by continuously varying the volume of deposited ink on the printing trajectory. In detail, we develop diameter-programmable filaments by customizing the printing velocity and height. To achieve high shape fidelity, we specially add supporting layers at needed locations. Finally, we showcase multi-disciplinary applications of our strategy in creating horizontal, radial, and axial gradient structures, letter-embedded structures, metastructures, tissue-mimicking scaffolds, flexible electronics, and time-driven devices. By showing the potential of this strategy, we anticipate that it could be easily extended to a variety of filament-based additive manufacturing technologies and facilitate the development of functionally graded structures,” the team wrote in their abstract.
DEVCOM CBC Researchers Receive Grant to Investigate 3D Printed Sensors
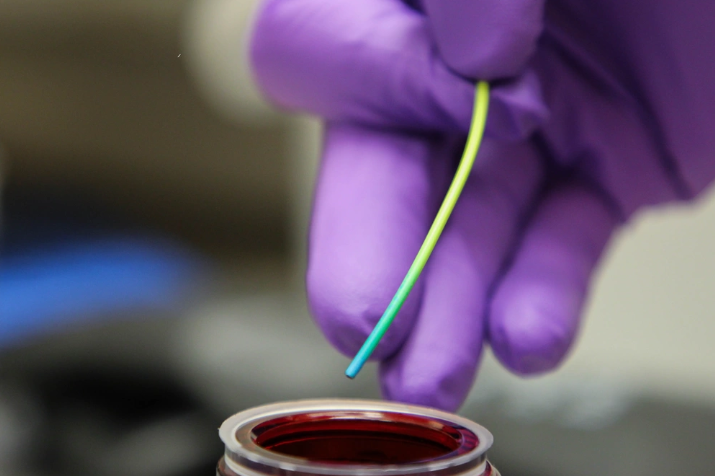
The DEVCOM CBC research team used Design of Experiment to determine which material used in 3D-printing a plastic filament best changes color in the presence of a chemical agent. (U.S. Army photo by Ellie White)
What if you could make 3D printed sensors that would change color in the presence of a chemical agent? That’s what Dr. Brian Hauck, a research chemist with the U.S. Army Combat Capabilities Development Command Chemical Biological Center (DEVCOM CBC), and his team wanted to know. They received a $30,000 grant from DEVCOM CBC’s Quick Empowerment leads to Successful Tomorrows (QUEST) program to find the answer, as if they were successful, these could be created inexpensively and on-demand as small, lightweight field sensors for warfighters or first responders to use.
They used commercially available FDM filament, and worked to embed a colorimetric indicator into it that would change its color, like a pH strip. The team experimented with how long to soak a sample of filament in a liquid indicator, how long to dry it out, finding the material with the best color change when exposed to chemical vapor, and other variables. The researchers found that the ideal conditions were white Nylon that had been soaked for 15 minutes and dried for four hours. Now that they’ve proven the concept, they hope to experiment with novel colorimetric chemistries and form factor. The Defense Logistics Agency (DLA) has already expressed interest in their system, which they call Chemically Reactive On-demand Materials, or ChROMa. Dr. Hauck’s team plans to submit their work to the DLA’s Emergent IV Broad Agency Announcement, a funding program for scientific study and experimentation for advancing knowledge or understanding in AM.
Ricoh & SimBioSys Develop AI-Powered 3D Printed Medical Models
Techbio company SimBioSys and Ricoh USA, via its Ricoh 3D for Healthcare business, are collaborating to explore the potential of AI and 3D printing to create personalized medical models to help improve breast cancer surgeries and patient care. SimBioSys leverages AI and computational modeling to redefine medicine and fight cancer, and is best known for TumorSight, its digital precision medicine platform. Ricoh 3D for Healthcare is a leader in patient-specific medical device manufacturing, so this seems like a match made in heaven, given their vision to integrate SimBioSys’ AI capabilities with Ricoh’s 3D printing know-how to fabricate accurate, patient-specific breast cancer models. The two unveiled some of their AI-generated models at last month’s American Society of Breast Surgeons (ASBrS) conference to showcase their combined capabilities and potential. However, their integrated workflow is still only for educational purposes, as it’s not been cleared by the FDA or any other organization for diagnostic use.
“Through a collaboration with SimBioSys, we hope to not just envision a new future for medical treatment but help actively create it,” stated Gary Turner, the Managing Director at Ricoh USA.
Meltio Announces New Partner for Wire-Laser Metal AM in Norway
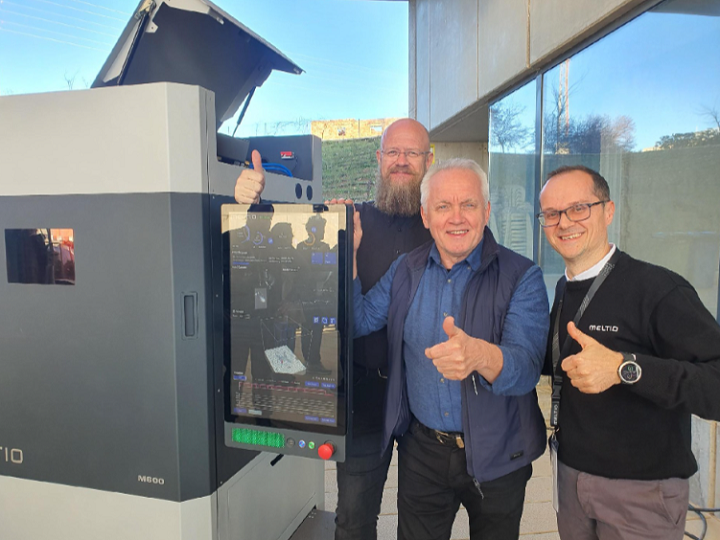
Arild Fotland, Technical Salesman at LTS Maskin AS, Leif Tore Solberg, Technical manager and owner at LTS Maskin AS
Laser metal deposition manufacturer Meltio announced that LTS MASKIN AS is its first official sales partner in Norway, and will help boost its growth in the Norwegian metal AM market. Meltio’s process is built around clean, safe, and affordable welding wire and can enable industrial applications. With LTS Maskin AS on board, a supportive ecosystem will be built for its solutions in the territory. The well-known Norwegian machines and equipment retailer will help with distribution and support of Meltio’s 3D printers in Norway by partnering with academia, industry, technology centers, tooling machine companies, and robotic integrators to drive more business opportunities for the technology.
“We are thrilled to be working with companies like LTS Maskin AS as their expertise as well as customer-technological approach is exactly what we are looking for when incorporating partners in the Meltio partner ecosystem,” said Francisco González, Sales Manager for EMEA at Meltio. “Together, we will be able to cater to the ever-growing needs of the market in Norway for, and ease the adoption of wire-laser metal additive manufacturing.”
Sandia National Labs 3D Printing Engine Parts with Markforged
Finally, Sandia National Labs, funded through the U.S. Department of Energy (DOE), works on a range of projects, including a body of research focused on improving the efficiency of internal combustion engines. As part of their work, the team creates physical simulations of various diesel fuel flow scenarios, to help design fuel nozzles that provide optimal flow for the engines. But, these nozzles have intricate internal geometries, so Sandia uses third parties for CNC machining and 3D printing, which is expensive and time-consuming. But working with Markforged, which can print metal in-house while also conforming to Sandia’s Environmental Health & Safety (EHS) requirements, has enabled the research lab to skip the third party vendors and simplify their workflow.
To test the parameters set by the Engine Combustion Network (ECN), Sandia 3D printed a diesel fuel injector adapter out of 17-4 PH Stainless Steel on a Markforged printer. The adapter holds a spray “D” nozzle configuration, allowing the lab to contribute to ECN research data. To achieve internal flow lines with the part’s internal geometry, non-traditional techniques are needed, but instead of shipping the adapter out for processing with specialized equipment, its critical surfaces and mating features are completed on an internal CNC mill. The new workflow enables more high-quality iterations and shorter lead times, and Sandia is now looking into the feasibility of 3D printing other high-impact engine components with different Markforged materials, such as nozzles and Inconel 625.
Subscribe to Our Email Newsletter
Stay up-to-date on all the latest news from the 3D printing industry and receive information and offers from third party vendors.
Print Services
Upload your 3D Models and get them printed quickly and efficiently.
You May Also Like
Johns Hopkins University Researchers Develop HyFAM Technology
Two scientists from Johns Hopkins University, Nathan C. Brown and Jochen Mueller, have developed a hybrid manufacturing technology they call HyFam, or Hybrid Formative Additive Manufacturing. Their work on this technology...
3D Printing G-Code Gets an Upgrade: T-Code
Good old G-Code still manages many 3D printers, great and small. Just like the STL, it’s a standard that enables collaboration while also holding the additive manufacturing (AM) industry back....
AM Rewind: The Biggest News and Trends of 2024
After a sluggish 2023, driven by persistent inflation and geopolitical tensions, 2024 has seen some recovery. Economic growth climbed from about 2.8 percent in 2023 to a modest 3.2 percent...
Metal Wire 3D Printer OEM ValCUN Announces Plans for 2025 Expansion
ValCUN, a Belgian original equipment manufacturer (OEM) of wire-based metal additive manufacturing (AM) hardware, has announced that the company has entered the next phase of its growth trajectory, making key...