In 3D Printing News Briefs today, we’re focusing first on robotics, as Carnegie Mellon University’s new Robotics Innovation Center will house several community outreach programs, and Ugogo3D is now working with KUKA Robotics. Next, Taika3D and Mosaic are combining their technologies for improved orthotics design and manufacturing, and Purdue University researchers are working on a full-scale, operational, 3D printed scramjet prototype. Finally, Stratasys launched two new GrabCAD software packages, and 1000 Kelvin launched AMAIZE as a plug-in for Autodesk´s Fusion integrated CAD/CAM software platform.
CMU’s Robotics Innovation Center Anchors Community Programs
Researchers at Carnegie Mellon University look for new ways that robotics can benefit everyday life, which includes its new Robotics Innovation Center (RIC), set on the 178-acre site of the former Hazelwood Green still mill and set to be completed in 2025. The planned 150,000-square-foot RIC, located next to CMU’s discovery workplace Mill 19, will include an outdoor robot “running room” for testing, as well as window views into other labs so the public can see the researchers. But most importantly, it will anchor several well-established community outreach programs that connect the university and the Hazelwood community. One future tenant is the Girls of Steel K-12 robotics team, which reaches about 300 students a year, and another is the Carnegie Mellon Robotics Academy (CMRA), which trains high school teachers and students. Construction of the RIC has begun, and plans for the space are continuing to evolve, which could hopefully create further outreach opportunities.
“I hope that the whole area will benefit and we can all be part of making more opportunities become feasible in reality. I hope that some of our current outreach activities or new ones also reach younger people in the community and get them excited about engineering and technology,” said Jonathan Cagan, head of CMU’s Mechanical Engineering Department.
Ugogo3D Customers Can Now Access KUKA Robots for Automation
3D printing services provider Ugogo3D announced that it’s working with robotic solutions leader KUKA Robotics, which is well-known for its advanced automation and robotics technologies. Now, Ugogo3D customers can access KUKA’s versatile robots, which are engineered with precision to reliably complete everything from intricate 3D prints to complex assembly tasks. KUKA robots have a variety of models and configurations available, and their control systems offer seamless operation and programming abilities, enabling users to increase their productivity. Plus, with their advanced sensors and collision detection systems, KUKA robots can enable a safe working environment.
One great combination is large-format 3D printing pioneer Caracol, another Ugogo3D partner. KUKA’s robots can definitely improve the capabilities of Caracol’s Heron AM system. Manufacturers that use Caracol printers can improve their efficiency and automation by integrating KUKA robots, as they easily integrate with Caracol’s printers to complete tasks such as material handling and part manipulation. Plus, pairing the two technologies together can facilitate human-robot interaction in AM workflows, which is obviously great for safety. KUKA Robotics, Caracol, and Ugogo3D all complement each other very well, and can help manufacturers in multiple industries deliver the best AM solutions.
Taika3D & Mosaic Collaborate for Orthotics Design & 3D Printing
Orthotic design technology leader Taika3D is collaborating with 3D printing solutions provider Mosaic to improve the design and manufacturing of orthoses, at scale and less cost. Together, the two companies worked to develop a solution for automatic FFF 3D printing of orthotics by optimizing Taika3D’s design automation software for the Mosaic Array printer. The result is the TaikaCreate solution, which can be tweaked for self-generating supports and nested build volumes. Taika’s software can be used to quickly design and validate complex foot orthosis models, which are then exported to the high-volume Array, which offers continuous 3D printing.
“We believe that the future of orthotic design and manufacture hinges on collaborative partnerships and innovative technologies. Our optimization for the Mosaic Array signifies our support for customers manufacturing FFF at high volume, and we are excited to explore this market with Mosaic. Furthermore, we remain open to exploring collaborations with printing companies and those employing alternative methods for manufacturing, as we strive to continually expand the horizons of personalized healthcare solutions,” stated Steve Cook, Co-Founder and CEO of Taika3D.
Purdue Researchers 3D Printing Operational Scramjet Prototype
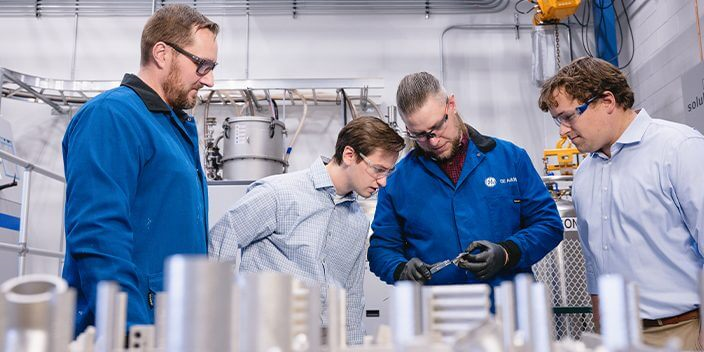
At the PARI Hypersonics Advanced Manufacturing Technology Center (HAMTC), from left: Nate Humbert, lead additive manufacturing engineer, GE Additive; Will DeVerter, aeronautics and astronautics graduate research assistant; Gregg Lubas, HAMTC processing engineer; Nick Strahan, HAMTC senior test engineer. Here they examine dimensional tolerances of a completed X Line print with calipers. This printer, used for large-scale metal manufacturing, has been instrumental in the group’s scramjet work. (Image: Purdue/Charles Jischke)
A scramjet is a supersonic combustion ramjet—an engine that enables aircraft to travel at Mach 5 speeds and beyond. It’s expensive, and time-consuming, to 3D print scramjets for testing, and small, scaled-down versions, which are printed in individual parts and assembled, are usually all that’s possible for applied research labs with AM capabilities. But a team at the Purdue Applied Research Institute (PARI) is using its advanced 3D printing equipment to fabricate a full-scale, operational scramjet prototype, funded by the Office of the Secretary of Defense Manufacturing Science and Technology Program. Researchers in PARI’s Hypersonic Advanced Manufacturing Technology Center (HAMTC), believe their design could lead to more efficient and affordable prototyping and manufacturing for the hypersonics industry.
According to PARI’s President and CEO Mark Lewis, while scramjets are still fairly new, they “are generally regarded as the best way to power a missile or aircraft through the atmosphere at speeds above five times the speed of sound.” The principle is simple, but the design is very complex, which is why AM has been helpful. PARI also houses the Hypersonics and Applied Research Facility (HARF), which offers a “one-stop shop” for advanced manufacturing innovations that can eventually be transitioned to the defense industry—like the scramjet prototype. The team uses a GE Concept Laser X Line 2000R to reduce the number of parts and weight of the prototype, while still accomplishing the necessary functionality and geometric complexity. The prototype also serves as a test bed for new technologies and experiments, integrating PARI’s manufacturing capabilities with the high-speed propulsion test facilities at the adjacent Maurice J. Zucrow Laboratories.
Stratasys Softwares Gets More Efficient with New GrabCAD Packages
Stratasys has launched two new packages for its GrabCAD software, which should reduce costs and improve efficiency for 3D printing. The first of these is a new version of GrabCAD Print Pro for PolyJet 3D printing, which builds on the success of the previous version for FDM and SAF. The software offers manufacturers advanced capabilities for more large-scale 3D printing, and also has features that support workflow automation. The second new package is GrabCAD Streamline Pro, which can make it easier to manage a fleet of printers and, thus, scale up production. It’s a comprehensive workgroup suite, powered by GrabCAD Print to enable the integration of Stratasys printers with GrabCAD software partners and users’ business systems. Features include advanced dashboards and analytics for AM managers, real-time monitoring and customizable alerts, automatic estimation and build preparation, cybersecurity capabilities, open APIs, and more.
“Our software provides essential capabilities for scaling up additive manufacturing workflows. We are connecting users with a centralized platform, giving them more information to make data-driven decisions and providing them with the precision and detailing that can only come from additive manufacturing,” said Victor Gerdes, Vice President, Software, Stratasys. “Throughput, efficiency and applications are key to manufacturing, and these GrabCAD software packages will further advance adoption of additive manufacturing by delivering measurable results that display real business value.”
1000 Kelvin’s AMAIZE Available as Plug-In for Autodesk Fusion
1000 Kelvin develops artificial intelligence (AI) co-pilots for additive manufacturing, and commercially launched its signature AMAIZE platform at Formnext 2023. At AMUG 2024, it announced that AMAIZE is now available as a plug-in for the Autodesk Fusion CAD/CAM software platform. AMAIZE uses machine learning models, informed by physics and manufacturing data, to efficiently predict any design or printing issues, and then output optimal files for successful prints. This means that users can get rid of physical, time-consuming trial and error cycles, and take on more complex parts. The platform is especially helpful for precision additive manufacturing companies that are dealing with an aging workforce and rising costs.
“One of AI’s greatest benefits is its ability to simplify complex processes, expanding access to powerful technology beyond a small circle of domain experts. By automating the setup and programming of industrial-grade print processes, 1000 Kelvin’s AI, integrated with Autodesk Fusion in the cloud, unlocks the opportunity for a much broader pool of professionals to be successful with additive manufacturing,” said Stephen Hooper, Autodesk Vice President, Design & Manufacturing Product Development. “I’m very excited to be offering AMAIZE to Fusion users.”
You can download AMAIZE from the Autodesk App Store here.
Subscribe to Our Email Newsletter
Stay up-to-date on all the latest news from the 3D printing industry and receive information and offers from third party vendors.
Print Services
Upload your 3D Models and get them printed quickly and efficiently.
You May Also Like
Making 3D Printing Personal: How Faraz Faruqi Is Rethinking Digital Design at MIT CSAIL
What if your 3D printer could think more like an intelligent assistant, able to reason through a design idea, ask questions, and deliver something that works exactly the way the...
Reinventing Reindustrialization: Why NAVWAR Project Manager Spencer Koroly Invented a Made-in-America 3D Printer
It has become virtually impossible to regularly follow additive manufacturing (AM) industry news and not stumble across the term “defense industrial base” (DIB), a concept encompassing all the many diverse...
Heating Up: 3D Systems’ Scott Green Discusses 3D Printing’s Potential in the Data Center Industry
The relentless rise of NVIDIA, the steadily increasing pledges of major private and public investments in national infrastructure projects around the world, and the general cultural obsession with AI have...
Formlabs Teams Up with DMG MORI in Japan
In late June, Nick Graham, Chief Revenue Officer at Formlabs, announced on LinkedIn that the company had partnered with DMG MORI, one of the world’s leading machine tool companies, to...