Adoption is crucial for the success of metal powders made from recycled scrap in the additive manufacturing (AM) industry. The prevalent concerns about recycled powder—its perceived inferiority to new powder, doubts about achieving consistent properties from scrap-based powder, and skepticism about its suitability for critical applications like aircraft manufacturing—are significant barriers to its widespread acceptance. However, a partnership with Velo3D (NYSE: VLD), in which Continuum Powders‘ materials, derived from recycled scrap, are now qualified for use in Velo3D’s Sapphire systems, addresses these concerns directly.
Yes, Velo3D has had some stock price issues, but, in the broader scheme of things, Team USA needs a local powder bed fusion (PBF) company that can supply the submarine industrial base and more. For Continuum, this announcement is pivotal in establishing the firm’s recycled powder as reliable for even the most demanding applications.
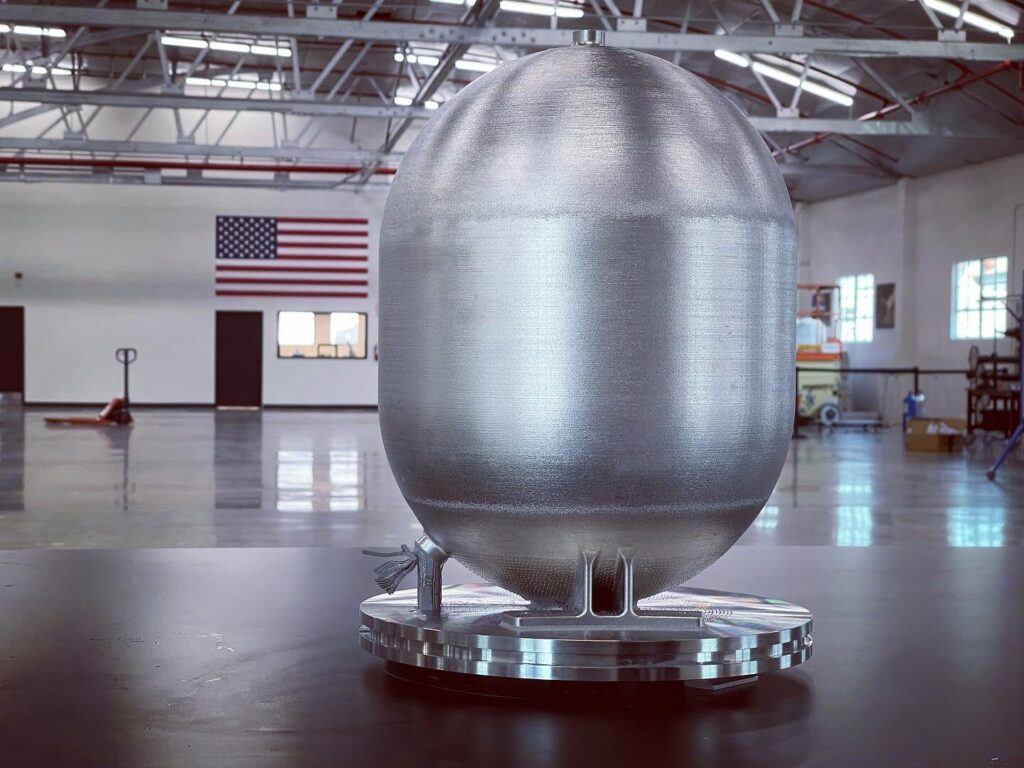
Launcher’s Orbiter propellant tank 3D printed out of Inconel using Velo3D’s Sapphire printer. Image courtesy of Velo3D.
Working with the contract manufacturer and Velo3D customer Knust-Godwin, Continuum Powders’ OptiPowder 718 (Inconel 718) has been qualified for use across the entire Velo3D Sapphire family. The companies have stated that the “extensive qualification confirms that the powder produced and supplied by Continuum Powders meets all material property requirements that are achieved with conventional powders in the same alloy when using specified parameters.” This qualification ensures that Continuum’s recycled powder is on par with conventional powders in terms of quality and performance. Inconel 718 is a big boy alloy used for oil and gas components, aerospace and defense in things like engines and structural components.
“For customers who are sustainability-minded, or have company objectives to reduce their carbon footprint, utilizing metal powders that are sourced through carbon-neutral means can streamline their adoption of additive manufacturing technology. We’re pleased to offer Continuum as a powder option and have validated that OptiPowder 718 delivers the performance and quality customers require from their powder while also meeting their decarbonization and sustainability goals,” stated Velo3D Vice President of Technology Zach Detweiler.
“Velo3D’s endorsement of OptiPowder as the first sustainable metal powder for Sapphire printers highlights the significant benefits Continuum brings to the market. We didn’t just want to raise the bar, we wanted to recreate the bar from the ground up to make sustainability core to the additive manufacturing process. Providing Velo3D’s customers with the first truly viable decarbonization option is a game changer for additive manufacturing – and the collaboration between Knust-Godwin, Velo3D and Continuum Powders is just the beginning,” contributed Phil Ward, CEO of Continuum Powders.
Continuum Powders, alongside 6K, Metal Powder Works, and IperionX, is working to convert scrap into reliable powder for metal powder bed fusion (PBF). Achieving this goal would unlock significant opportunities for them, positioning these companies at the crossroads of substantial challenges and equally significant prospects. There is a growing demand from brands and companies for more sustainable products to enhance their green credentials. Recycled metal 3D printed products could contribute to meeting this demand.
Moreover, there are companies aiming to produce low carbon pollution products; these efforts could be supported by the use of recycled powders. For the military and nations concerned about supply chain resilience, recycled powder could enable production under embargoes, independent of other countries, or in forward operating areas. Each of these trends is impactful and has strategic implications for nations and large corporations.
Consequently, if one or all of these companies manage to perfect the powder recycling process, they could experience significant growth. The potential effects of recycled powder make it a more substantial opportunity than the rest of the 3D printing industry as a whole. This positive development indeed sets a precedent that could inspire the broader additive industry. The successful qualification of recycled powders for high-end applications could spark a trend toward qualifying every single powder in recycled form for use in machines from other leading manufacturers such as AMCM, SLM, and EOS.
Subscribe to Our Email Newsletter
Stay up-to-date on all the latest news from the 3D printing industry and receive information and offers from third party vendors.
Print Services
Upload your 3D Models and get them printed quickly and efficiently.
You May Also Like
3D Printing News Briefs, June 11, 2025: Sustainability, Automotive Tooling, & More
We’re starting with sustainability news in today’s 3D Printing News Briefs, as EOS has strengthened its commitment on climate responsibility, and Zestep is making 3D printing filament out of eyewear...
3D Printing 50 Polymer Stand-In Parts for Tokamaks at the PPPL & Elytt Energy
Of all the world’s things, a tokamak is one of the hardest, most complex, expensive and exacting ones to make. These fusion energy devices make plasma, and use magnets to...
3D Printing News Briefs, May 17, 2025: Color-Changing Materials, Humanoid Robot, & More
We’re covering research innovations in today’s 3D Printing News Briefs! First, Penn Engineering developed 3D printed materials that change color under stress, and UC Berkeley researchers created an open source,...
Firehawk Aerospace Partners with JuggerBot 3D, Gets $1.25M from AFWERX for 3D Printed Propellants
Texas-based Firehawk Aerospace, an advanced energetic materials firm that works with aerospace and defense applications, announced a strategic partnership with JuggerBot 3D, an Ohio-based large-format 3D printer manufacturer. Together, the...