In January, researchers from the Massachusetts Institute of Technology’s (MIT’s) Computer Science and Artificial Intelligence Laboratory (CSAIL) published a study in the journal Science Advances, which details an algorithm they developed for automating material qualification of 3D printed parts. The specific aim of the project is encapsulated in the study’s title, “Computational Discovery of Microstructured Composites with Optimal Stiffness-Toughness Trade-Offs”:
As the journal article’s introduction notes, “Stiffness — the ability to resist deformation in response to an applied force, and toughness — the ability to resist cracks, are two quintessential properties in most engineering materials, since these materials must resist non-recoverable deformation and prevent catastrophic failure under external loading in structural applications. Unfortunately, stiffness and toughness are often mutually exclusive because, in order to be tough, a material must be ductile enough to tolerate long cracks and absorb more energy before fracturing. Although a few exceptions have been discovered among microstructured composites through trial-and-error approaches or biomimcry, there is no systematic way to design and fabricate such materials.”
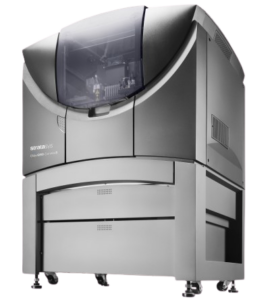
Thus, the CSAIL team’s goal wasn’t so much to find the optimal equilibrium between stiffness and toughness for a given material, but rather to create an automated process for discovering that equilibrium. Using a Stratasys Objet 260 Connex multi-material 3D printer, the researchers fabricated test objects from two different acrylic-based materials, combining the feedstocks into composites with different ratios of the base materials.
In the next phase of the project, the team subjected the materials — printed into objects “roughly the size of a smartphone but slimmer” — to tensile testing on an Instron 5984 Universal Testing Machine (UTM). The results from those tests were used to inform a finite element method (FEM)-based simulation, with the combined results of real-world and virtual testing then fed into the algorithm the researchers developed, called “Neural-Network Accelerated Multi-Objective Optimization” (NMO).
As the paper notes, “In early iterations, the predictor is very inaccurate due to limited training data. …Nonetheless, as the algorithm proceeds the predictor becomes more accurate by virtue of accumulating training data from the simulator.” The team concluded that a method incorporating three qualitatively different datasets gradually brought the simulation closer to reality, a process which was greatly accelerated by the use of machine learning. The researchers expect that the versatility of the underlying approach should allow the study’s results to be applied in many areas outside the scope of the original experiment:
One of the study’s lead researchers, MIT CSAIL PhD student Beichen Li, told MIT News, “Composite design and fabrication is fundamental to engineering. The implications of our work will hopefully extend far beyond the realm of solid mechanics. Our methodology provides a blueprint for a computational design that can be adapted to diverse fields such as polymer chemistry, fluid dynamics, meteorology, and even robotics. This evolutionary algorithm, accelerated by neural networks, guides our exploration, allowing us to find the best-performing samples efficiently.”
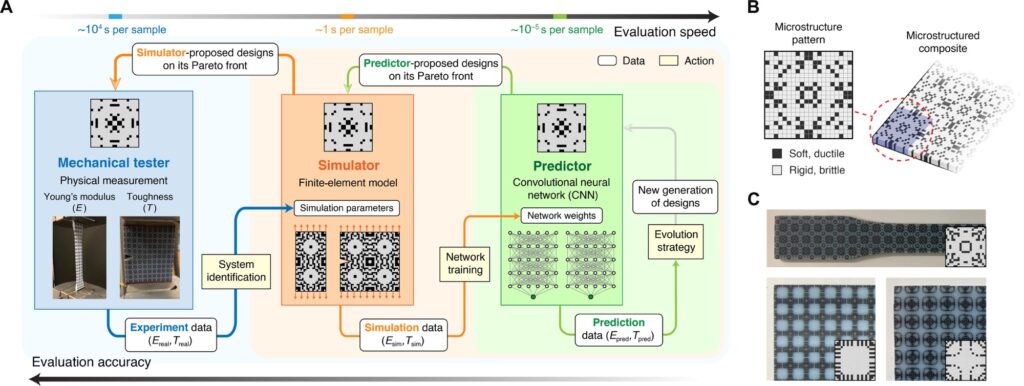
The researchers rightly point out in the journal article that one of the most crucial results of the study is the demonstration that an AI-based approach may enable non-experts to effectively and quickly characterize and qualify materials. It is easy to imagine organizations like America Makes testing the approach to simultaneously enhance both material qualification and workforce development.
It is also easy to see how a company like Inkbit, with its specialization in deploying machine vision for additive manufacturing (AM) optimization, emerged out of the CSAIL. Inkbit’s multi-material, precision engineering approach seems like an ideal platform for future research into the NMO.
Finally, the most intriguing aspect to the study may be its potential to take the same method and incorporate other parameters — most namely, cost. Markforged, for instance, just released a product called Performance Advisor, which relies on a physics-based approach to recommend optimized balances between part strength and cost. In any case, the increasing exploration into physics-based approaches for AM quality control suggests that this is more than just a trend, and will likely become more and more integral to the industry’s overall process of materials development.
Subscribe to Our Email Newsletter
Stay up-to-date on all the latest news from the 3D printing industry and receive information and offers from third party vendors.
Print Services
Upload your 3D Models and get them printed quickly and efficiently.
You May Also Like
Reinventing Reindustrialization: Why NAVWAR Project Manager Spencer Koroly Invented a Made-in-America 3D Printer
It has become virtually impossible to regularly follow additive manufacturing (AM) industry news and not stumble across the term “defense industrial base” (DIB), a concept encompassing all the many diverse...
Inside The Barnes Global Advisors’ Vision for a Stronger AM Ecosystem
As additive manufacturing (AM) continues to revolutionize the industrial landscape, Pittsburgh-based consultancy The Barnes Global Advisors (TBGA) is helping shape what that future looks like. As the largest independent AM...
Ruggedized: How USMC Innovation Officer Matt Pine Navigates 3D Printing in the Military
Disclaimer: Matt Pine’s views are not the views of the Department of Defense nor the U.S. Marine Corps Throughout this decade thus far, the military’s adoption of additive manufacturing (AM)...
U.S. Congress Calls Out 3D Printing in Proposal for Commercial Reserve Manufacturing Network
Last week, the U.S. House of Representatives’ Appropriations Committee moved the FY 2026 defense bill forward to the House floor. Included in the legislation is a $131 million proposal for...