This year’s Additive Manufacturing Users Group (AMUG) Conference in Chicago, Illinois, promises to be an enlightening experience with Olaf Diegel, professor of Additive Manufacturing (AM) at the University of Auckland, New Zealand, as a keynote speaker. Known for his 3D printed guitars with ‘funky’ designs offered through his company ODD, Diegel brings a multifaceted expertise to the table, combining his roles as an academic, consultant, and product designer.
Diegel’s journey in the AM industry began in the early- to mid-1990s while working in the electromechanics sector for lighting and home health monitoring companies. His initial encounters with prototyping and the subsequent purchase of the first fused deposition modeling (FDM) machine in New Zealand marked the beginning of his deep involvement with 3D printing.
“I was developing products—doing the electromechanics, so mostly mechanical engineering, but a bit of electronics as well. As part of that, we were prototyping before committing to $10, $50, or $100 thousand in tooling. I’d have to prototype the mechanical parts. At the time, we had no machines at all in New Zealand, so I’d have to email my files to the guys in Australia who would 3D print them for me. Then, a week or two later, I’d get my parts back. It allowed us to save a lot of money on tooling. I was so impressed with it that I then bought the first Stratasys machine in New Zealand.”
Inside the Auckland Lab
This journey led him back to academia, where he focused on rapid product development and the integral role of additive manufacturing in this process. Diegel’s lab is comprised of a diverse team of students and staff working on AM projects. In total, the lab includes around 20 PhD students, master’s students, fourth-year students, and staff members who engage in hands-on work with various 3D printing technologies and projects, ranging from computational design to developing solutions for industrial problems. The lab’s approach is characterized by a practical, applied research focus, often working directly with industry partners.
Diegel regularly shares the unique work his lab has performed on social media, particularly LinkedIn. There, you can see projects that range from redesigning car parts for enhanced durability to automating vacuum forming patterns and optimizing casting processes, all while integrating advanced design principles and software tools to address real-world manufacturing challenges.
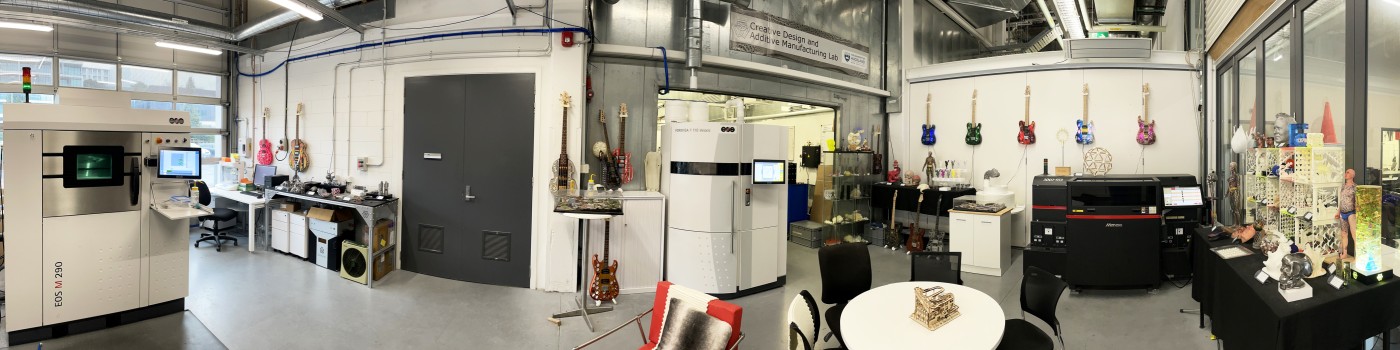
Olaf Diegel’s University of Auckland 3D printing lab. Image courtesy of Olaf Diegel on LinkedIn.
Altogether, the lab is outfitted with an M290 for production parts, a Sharebot MetalONE for experimenting with metal powders like copper, a selective laser sintering machine for nylon, a Mimaki inkjet system for full-color prints, some binder jetting systems to explore food printing and conductive materials, as well as desktop stereolithography and material extrusion machines. One intern has converted a robot arm into a pellet extruder-based system.
Remote Manufacturing in New Zealand
Given its size and remote location, New Zealand may be particularly interested in the wave of advanced manufacturing efforts that are being executed globally. In fact, the Productivity Commission of New Zealand was tasked with an inquiry into the resilience of the New Zealand economy to supply chain disruptions. Additionally, in 2023, the Ministry of Business, Innovation & Employment launched the Advanced Manufacturing Industry Transformation Plan to boost productivity and performance in vital economic sectors.
As these efforts get underway, Diegel’s lab will likely be seen as an increasingly relevant resource for government and industry partners. One of the site’s already significant contributions has been improving traditional manufacturing processes with additive technologies, like creating more efficient tooling for injection molding.
“Most of the reshoring work we’re doing, strangely enough, is in traditional manufacturing. The injection molding industry in New Zealand’s pretty much gone to China. In fact, the companies I used to work for used to get all their parts molded in China. One of my colleagues in the lab is a toolmaker by trade and he’s been working on 3D printing tools with conformal cooling channels that’ll allow you to cut your cooling time in half. We’ve been doing a lot of work in that area for local tooling companies to effectively tooling back to New Zealand by making it more efficient, rather than due to distance.”
Because companies can have their tooling made in two to three weeks rather than two to three months, they’ve been turning to AM. In one case, Diegel’s lab was able to redesign an eight-cavity tool for injection molding bottle caps. The professor noted that, whereas tools in his days at traditional manufacturers might pay for themselves in six months to two years, the 3D printed bottle cap tool paid for itself in just 27 days of operation due to improved cooling time.
“If you look at most injection molding tools, the bottom half of the tool is a boring lump of steel, and you don’t want to be printing that,” Diegel explained. “So, he’s been machining the substrate, the base of the tool, and then printing the complex part with the cooling channel directly on top of that. It’s a way of getting the cost and the print time down to make it more affordable. Using additive for traditional manufacturing is an area that’s been undervalued—and that includes sand casting and injection molding.”
Advancing the Field of DfAM
To be able to harness AM technologies, however, requires new ways of thinking and, perhaps, new design tools. This is a particular area of interest for his lab, where the team is look into automating aspects of the design process.
New software like nTopology, Hyperganic, and Leap71 enable the creation of total optimized, 3D printed parts. However, when the same element is modified for 20 different use cases, these changes can become a significant suck of time and resources. For that reason, the lab has developed methods for quickly tailoring a model to new input. This makes it possible for Diegel’s lab to produce items like user-specific splints, insoles, and sandcasting molds much more efficiently. For instance, the lab can scan a person’s arm and generate a ready-to-print splint in two minutes. The same can be performed for creating insoles from a pressure map.
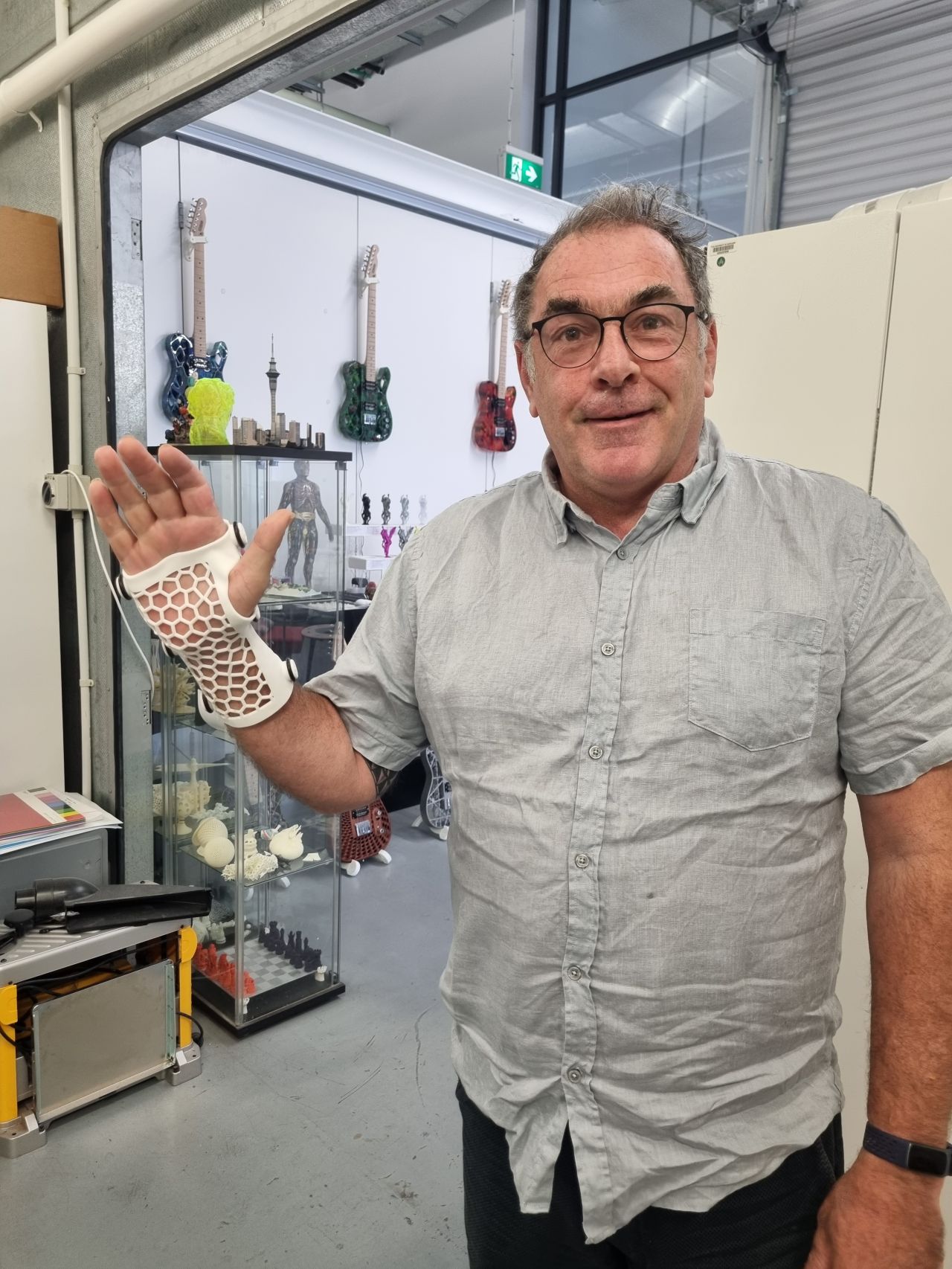
After New Zealand Product Accelerator Co-Director Mark Jones suffered a hand injury, Diegel’s team scanned the injured hand and 3D printed a bespoke wrist support.
“I think that’s going to be a game changer for a lot of industries who want to use additive but don’t quite know how to do it when they’ve got 20 different products that are each slightly different. I think our automated design process is a big value add,” Diegel said.
Another design area that the lab has been exploring for three to four years are triply periodic minimal surface (TPMS) gyroids that couldn’t be produced traditionally. By 3D printing parts with TPMS shapes, it’s possible to improve the efficiency of heat exchangers, radiators, and other automotive parts. This has led Diegel to work with the university’s formula student race car team to create electric motors wrapped in cooling jackets.
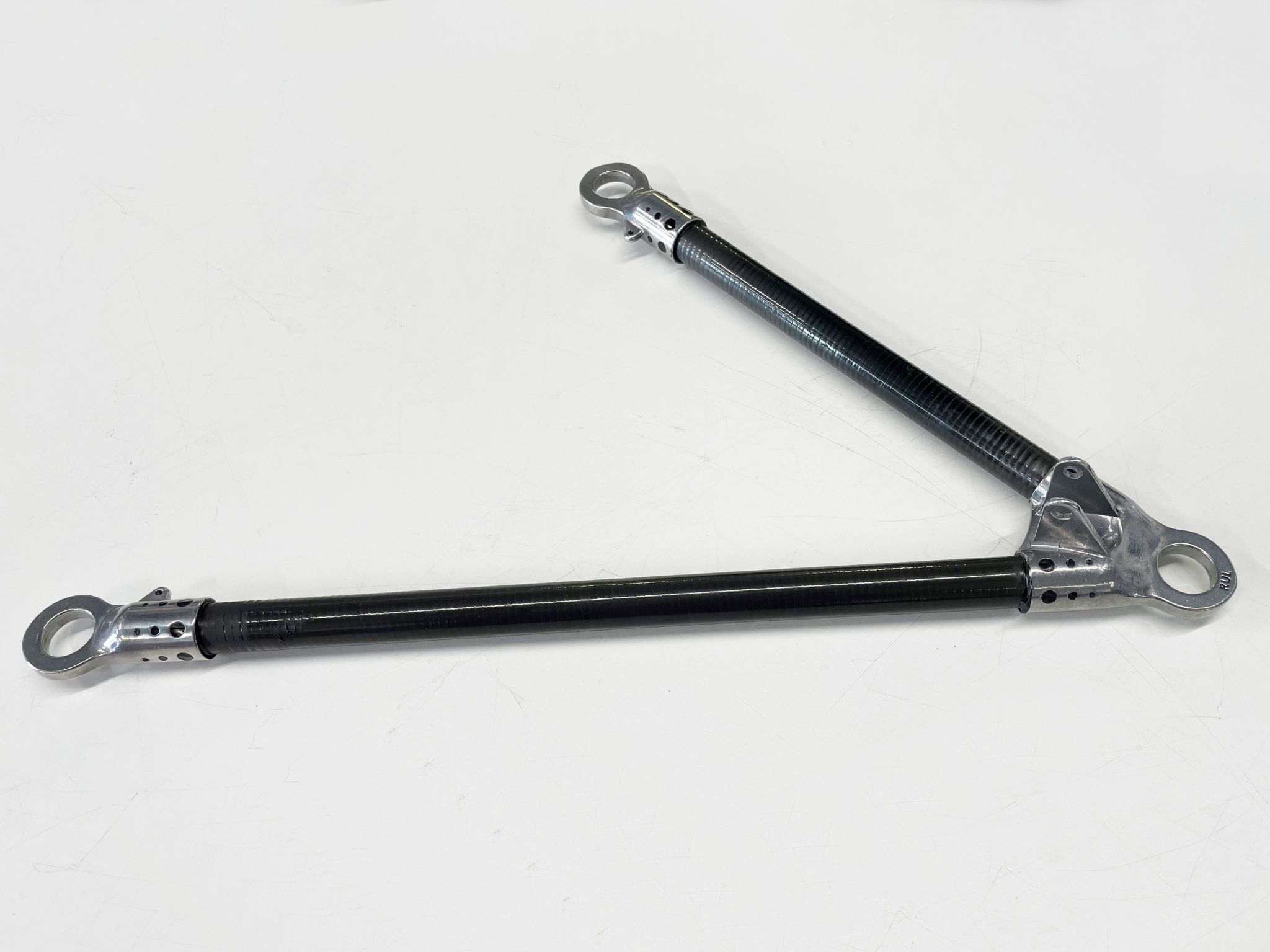
The University of Auckland FSAE race car suspension, made up of aluminum nodes (AlSi10Mg) on the lab’s EOS M290 metal powder bed fusion system. Image courtesy of Olaf Diegel on LinkedIn.
Diegel’s group is additionally researching the concept of nodal design, which is reminiscent of Divergent’s early efforts in 3D printed vehicles. By breaking a large object into small nodes connected by carbon fiber, steel, or aluminum tubes, it’s possible to assemble individual elements into sizable structures.
“We’ve been doing a lot of work with the formula student race car suspension. The whole suspension is made up of printed, aluminum nodes joined together with carbon fiber tubes. In fact, just this past year, they raced across Australia and won.” Diegel joked, “So, we take full credit for that, of course. No, we don’t actually, but every gram of weight they save is a huge advantage.”
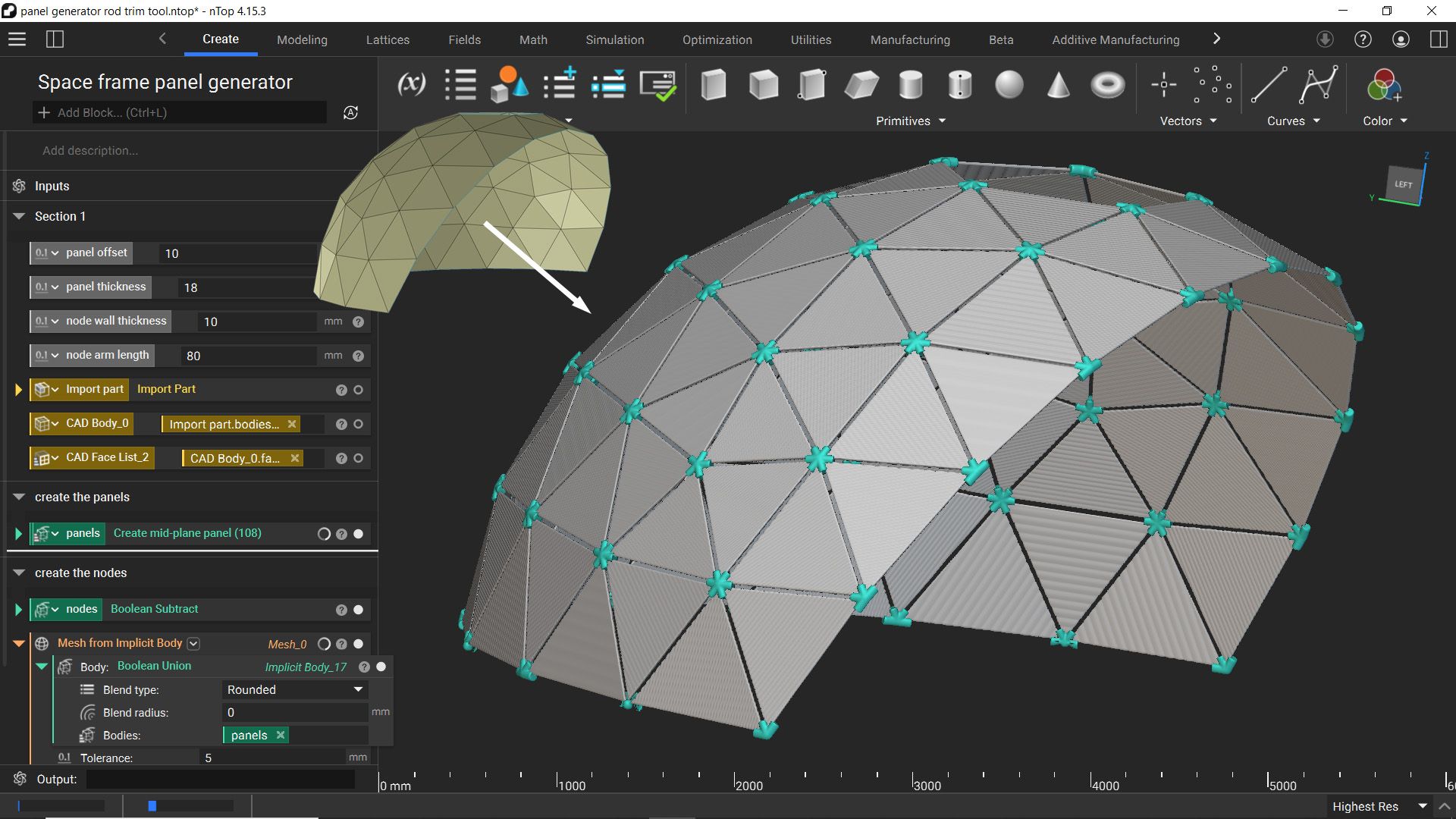
The automated space frame generator at Diegel’s lab can automatically produce flat panels that can slide in between nodes. Each node gets automatically numbered to instruct builders how everything gets assembled. Image courtesy of Olaf Diegel on LinkedIn.
DfAM at AMUG
Diegel will be sharing more insights into these novel advances at the AMUG Conference. At his first year in attendance, the Kiwi professor will be presenting a keynote on design for AM (DfAM). He plans emphasize how DfAM can transform products by adding value-enhancing features and illustrate how AM serves as a catalyst for innovation. Because the event is unlike any other in the industry, it likely won’t be his last.
For those interested in attending, direct owners of industrial AM equipment using it for professional applications can visit the AMUG registration page.
Subscribe to Our Email Newsletter
Stay up-to-date on all the latest news from the 3D printing industry and receive information and offers from third party vendors.
Print Services
Upload your 3D Models and get them printed quickly and efficiently.
You May Also Like
Johns Hopkins University Researchers Develop HyFAM Technology
Two scientists from Johns Hopkins University, Nathan C. Brown and Jochen Mueller, have developed a hybrid manufacturing technology they call HyFam, or Hybrid Formative Additive Manufacturing. Their work on this technology...
3D Printing G-Code Gets an Upgrade: T-Code
Good old G-Code still manages many 3D printers, great and small. Just like the STL, it’s a standard that enables collaboration while also holding the additive manufacturing (AM) industry back....
AM Rewind: The Biggest News and Trends of 2024
After a sluggish 2023, driven by persistent inflation and geopolitical tensions, 2024 has seen some recovery. Economic growth climbed from about 2.8 percent in 2023 to a modest 3.2 percent...
Metal Wire 3D Printer OEM ValCUN Announces Plans for 2025 Expansion
ValCUN, a Belgian original equipment manufacturer (OEM) of wire-based metal additive manufacturing (AM) hardware, has announced that the company has entered the next phase of its growth trajectory, making key...