At the end of 2023, we saw a lot of conjecture about the demise of 3D printing and rise of Additive Manufacturing (AM). Tim Simpson and I took the road where we delineated 3D printing from AM: One is about shapes and the other is about parts. This took a further turn which got us thinking about other topics like the notorious 7 AM families. When you take a step back to examine the original definitions, they have weathered time okay but exclude newer processes. This happens because people keep innovating and creating new hybrids that don’t necessarily conform to the existing definitions. To be fair, this is a good thing. We keep improving the processes until they are solved financially (and technically).
So, what’s an engineer to do? It is helpful to have some high-level descriptions if only to help make the start of any PowerPoint presentation to upper management. There is, however, another angle, again a very positive sign of industry maturation. If we take the example of vat photopolymerization, it started some 30 years ago with the invention of Chuck Hull. Then digital light processing (DLP) and Carbon came along to turn our world upside down and a new twist on the original process. More recently, Holo AM came into the scene and made what was always thought to be a polymeric process into a fine metal printing technology.
At the Barnes Global Advisors (TBGA), we created the Simplified View of AM for this reason. For an engineer, if you can answer three basic questions, you can summarize and start to form a process specification for any new process; How is the layer formed? How is the material applied? How is the energy applied?

Figure 1. TBGA’s Simplified View to describe AM process technologies
Fine…It’s in Details
We got a little curious because we saw that the design space for small parts, like the size of a fingertip, was not well supported with AM process technologies, and then mostly polymeric. We put the TBGA Laboratory to work to investigate further. We had the opportunity to get reacquainted with Holo AM in the last year, and they agreed to support our study and allowed us to dig into a bit more detail.
- How do they form a layer? They use a lithographic process (aka DLP)
- How do they use material? They use fine metal powders, like those used in Metal Injection Molding (MIM) and binder jetting, but the powders are suspended into a slurry.
- How do they use energy? They use thermal energy to debind and then sinter the metal powders into a solid shape.
It’s about making parts and what is interesting is this crossover from DLP, which has good software and process workflow software to support it. The software used for DLP processes is mature compared to that used for many other AM families. For example, supports (where necessary) are auto-generated by the software with high accuracy, and 3-D nesting of the parts to be built is also automated.
The slurry approach is interesting because using lithography would not impose the ballistic effect, or denudation effects that can be present in L-PBF and BJP. Specifically, in binder jetting, grooving of the surface can be deleterious to surface finish and fine dimensional capability. Papers, like one done by Carnegie Mellon University, have highlighted the ballistic impact the binder can impart as it strikes the surface of the powder bed, typically around 8 m/s. (Real-time observation of binder jetting printing process using high-speed X-ray imaging, Scientific Reports 9(1):2499). The DLP approach should be superior as a means to get a uniform layer of metal powders.
Because both BJP and Holo are sinter based process technologies, the shrinkage during sintering must be considered. With the DLP approach, X, Y, and Z directions should be similar in shrinkage whereas with BJP, we’d expect X and Y directions tend to be similar. The Z direction is different enough to require distorting the part differently to achieve accurate final dimensions. With the slurry approach, once the scaling factor for a material is known, it can be uniformly applied to each new part, simplifying the non-recurring engineering requirements for producing a new part.
Overall, the sintering is simplified a bit because the parts are small; however, maintaining the details and dimensions is always a challenge. With DLP, we would expect less distortion and uniform distortions, so there is less need for things like setters to keep dimensional tolerances. We also thought that because the powder is in the slurry, it won’t be susceptible to the denudation effects seen in pure powder bed technologies from the binder bombardment or laser effects, which erode the surface finish and dimensional detail.
After, we established some requirements for our study. We selected a few parts to make from the TBGA Exemplar library. In this study, we chose scaled versions of the impeller, and the vane segment, then added a heat sink with some fine detail. We used our process economic tools to assess the costs associated with part production via MIM, Binder Jetting, Laser Powder Bed Fusion (LPBF), and Holo (because it isn’t fair to label this just DLP (Maybe DLP + Sinter?).
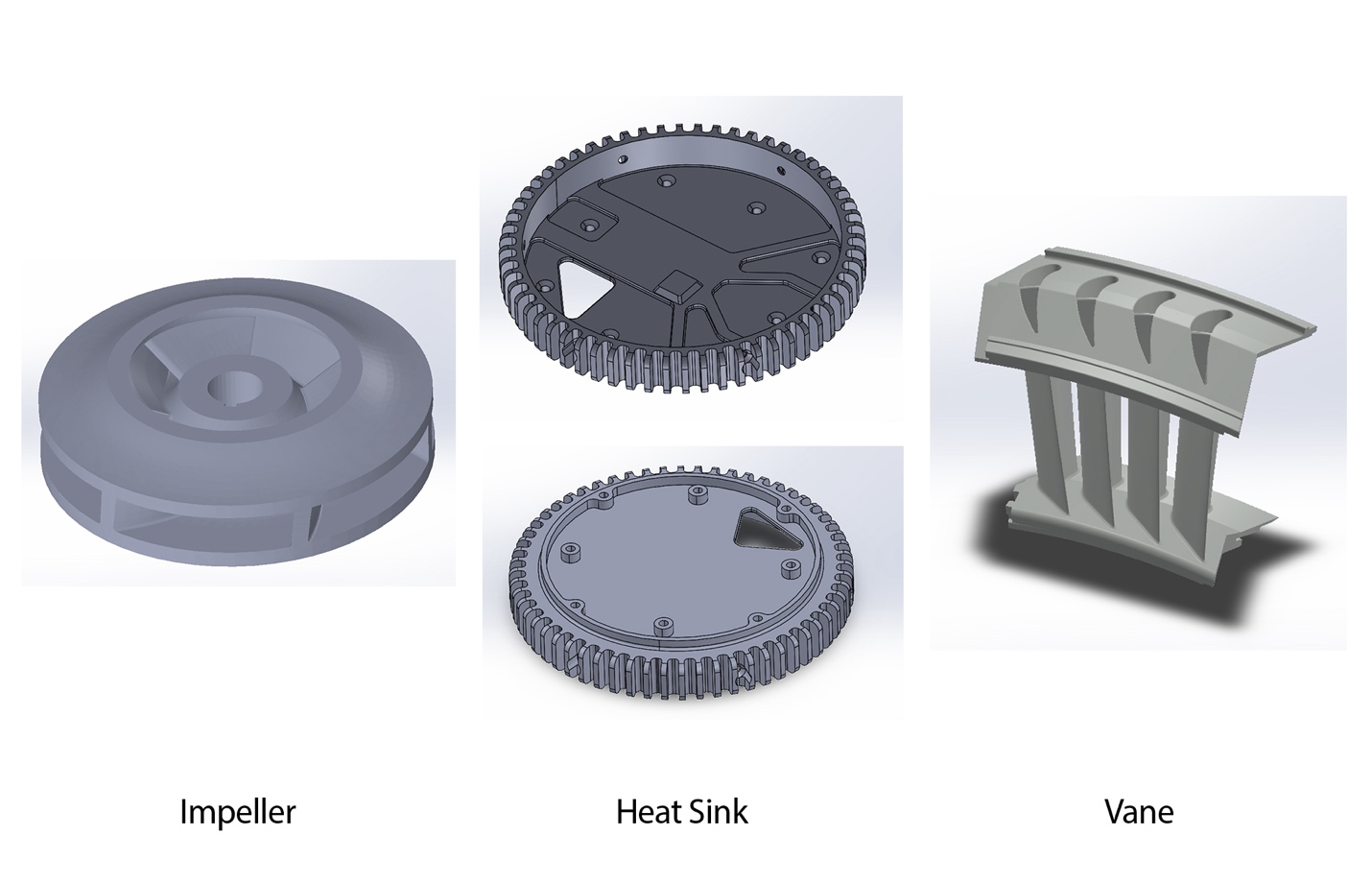
Figure 2. TBGA exemplar geometries used in this study
Process Economics
We established the costs to produce the parts with various processing methods. We established the per part costs along with the investment required to make the parts. Think of this as the recurring costs versus the non-recurring costs, where non-recurring items are the cost of the printers, tooling, etc. Within this calculation we then assessed the number of parts it would take to overcome the non-recurring. This factors in because if the production numbers have to be high, it would be hard to justify. Taking this notion further, we looked at the ability to hold tolerance, essentially, does every process make the same thing. (i.e. are they all capable of hitting the dimensions?)
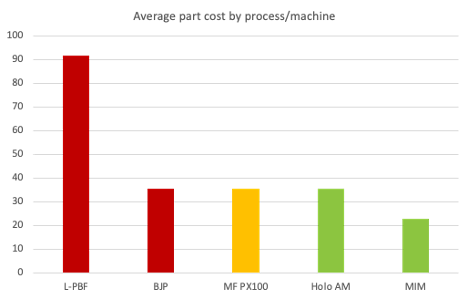
Figure 3. The average cost to make the exemplar parts by process technologies. The color of our assessment of being able to meet the required resolution or dimensions (Red = Low, Green = High)
Figure 3 is the average part cost for the exemplar geometry as processed by L-PBF, DLP, and BJP. The L-PBF was selected as a competitive PBF entry in a quad laser configuration, even though the finest features it’s capable of creating are significantly larger than DLP-based processes. Perhaps a better L-PBF comparison would be the 3DMircroprinting GmbH DMP 70 for making smaller, more detailed parts. However, we do not yet have process economics data for this system.
We assessed several common BJP approaches, which all produced similar costs (HP S100 Metal Jet, Desktop Metal P1, and Desktop Metal X160 Pro) & averaged them to represent industry typical costs. While about the same costs as the Holo machine, they cannot represent the feature size, repeatability, and accuracy of the DLP-based method. We also note that the MarkForged® PX100 (formerly Digital Metal) uses a finer pixel pitch in printing, making this the best BJP technical comparison. We noted the ability to meet the technical requirements of resolution and dimensions with a qualitative green (meets), amber (might meet), or red (does not meet).
Non-Recurring Expenses and Part Volume

Figure 4. Non-recurring and volume of parts comparison
Figure 4 shows the non-recurring costs divided by the number of parts to be made. Simply put, the conventional manufacturing cost for MIM is initially high because of the tooling costs, but once the tooling is made, it can produce a lot of parts. It seems obvious but worth noting, that if you do not require a lot of parts, MIM is not a good choice. AM approaches will be less expensive overall, even if slightly higher on a $/part basis. The AM approach also avoids a fixed tooling solution, so in situations where the design is not fixed or may change, the AM approach will be more competitive. We present this extra bit of information to enable one to have a comprehensive view.
When compared to traditional high-resolution part-making manufacturing process like MIM, both AM techniques are significantly easier to amortize the non-recurring costs (Engineering + Tooling) due to the cost associated with injection mold tooling. Holo appears to be even less expensive than BJP due to the automated software available for DLP and the process consistency already noted above.
Time is Money
It is said often enough that time is money, but in manufacturing, this is most certainly true. To that end, we did a time analysis to see how long it might take to enter Low Rate Initial Production (LRIP) shown in Figure 5. Note that MIM tooling typically takes 4+ weeks so it is not included on the graph. As can easily be seen, the need to iterate for BJP and L-PBF extends the time to LRIP, whereas Holo and the DLP + Sinter approach is much faster. The software tools are well integrated and automated for DLP and therefore, Holo benefits from this legacy. For both BJP and L-PBF processes, the software tools are not yet as mature. Our experience indicates that the large majority of preliminary prototypes made for BJP and L-PBF fail the first prototype. Issues like the sintering setters were not designed appropriately, uneven shrinkage was observed for BJP, and/or build orientation and support design could be improved to further minimize distortion in L-PBF. Thus, two or more Design –> Simulate -> Build Prototypes -> Inspect cycles are required for every new part, as represented in Figure 5 for BJP and L-PBF.
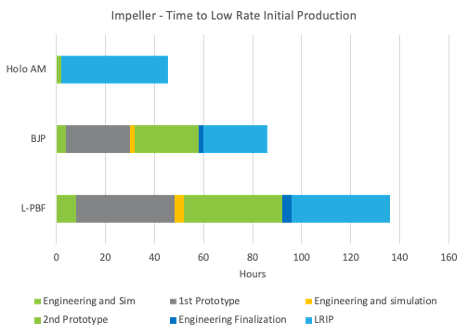
Figure 5. Estimated time to Low Rate Initial Production for the selected processes
I Need Some Space – Some Design Space
We all need our space at times. Most of us appreciate the design space for different processes. There is some overlap, but this small, detailed part world is relatively new to AM. In this design space, we need to be concerned about factors that can affect surface finish and the precision ability to hit a resolution and feature size. To expand into this small space further, we investigated the resolution and minimum feature size of several processes, not just the ones included in the prior analyses. Based on this information, the DLP + Sinter approach (Holo) has the smallest minimum feature size. Table 1 also adds a dimension to the economic analysis because, after all, parts have requirements, and if you can’t meet the requirement, the cost is somewhat irrelevant.
Machine | Resolution | Min Feature size |
BJP (DM P1) | 21 µm | 200 µm |
L -PBF (SLM® 500 Quad) | 70 µm | 125 µm |
BJP (Markforged® PX100) | 16 µm | 100 µm |
L-PBF (3D Microprint GmbH DMP70) | 30 µm | 30 µm |
DLP + Sinter (Holo AM) | 25 µm | 25 µm |
Table 1. Resolution and Feature Size of Various AM Printers
Requirements, Requirements, Requirements
Can we make the requirement? From the parts that we have shown, it would be contrived to say we did, as they are exemplar parts. However, we were able to run some actual parts and it appears that the first several parts match the requirement with the DLP + Sinter approach. Based on prior work, it is our opinion that the DLP approach will provide a better surface finish and dimensional tolerance than the BJP – for the money. It may be possible to reduce layer thickness and voxel conditions to improve feature resolution, but this will come at a consequence of cost. The lithography approach is fundamentally better for making small, detailed parts.
Can we make a business case? Time and money tend to sharpen the focus. DLP + Sinter and BJP are close to the same cost per part. DLP + Sinter has the advantage on being able to make a smaller volume of parts at a lower cost due to the legacy DLP software that exists. Both BJP and DLP + Sinter have the advantage of avoiding a significant upfront and fixed tooling cost. In the end, the $/part cost at high volume essentially converges for DLP, BJP and MIM.
The time to LRIP, however, is strongly in favor of AM approaches, and within AM, the DLP legacy helps.
The Age Old Question: Does Size Matter?
The details matter…and with smaller parts, they matter more. We are excited we were able to validate our process economics with Holo but wish we had more time to investigate the dimensions more thoroughly. Once you open the door to more details, especially internal details like the impeller and heat sink, it becomes important to be able to measure them to ensure compliance. With smaller parts and smaller features, the problem tends to compound – but this is a good problem to have really. It would be interesting to CT scan the parts to examine features and dimensions. Assessing the mechanical properties are also difficult and expensive on small samples but it is an area where we would appreciate more data.
The slurry-based approach with lithography assists in better surface finish and less likely need for setters. We avoided all of the issues typically associated with fine powder which has a deeper story. Being in a slurry avoids free powder floating around and the associated safety issues. It is easier to move the slurry around than fine powders, so getting it to print into a shape should be less effort.
It’s exciting to see the design space for AM expand again. The small and detailed parts space was underrepresented in metals. The economics of the space also enable good ‘time to first part’ and AM enables the user to get initial parts made without the outlay of cash in tooling. With tooling comes other burdens, namely that the design is then very hard to change or modify and tools have to be maintained and stored.
Let’s make some parts. Long live AM!
Subscribe to Our Email Newsletter
Stay up-to-date on all the latest news from the 3D printing industry and receive information and offers from third party vendors.
Print Services
Upload your 3D Models and get them printed quickly and efficiently.
You May Also Like
Reinventing Reindustrialization: Why NAVWAR Project Manager Spencer Koroly Invented a Made-in-America 3D Printer
It has become virtually impossible to regularly follow additive manufacturing (AM) industry news and not stumble across the term “defense industrial base” (DIB), a concept encompassing all the many diverse...
Inside The Barnes Global Advisors’ Vision for a Stronger AM Ecosystem
As additive manufacturing (AM) continues to revolutionize the industrial landscape, Pittsburgh-based consultancy The Barnes Global Advisors (TBGA) is helping shape what that future looks like. As the largest independent AM...
Ruggedized: How USMC Innovation Officer Matt Pine Navigates 3D Printing in the Military
Disclaimer: Matt Pine’s views are not the views of the Department of Defense nor the U.S. Marine Corps Throughout this decade thus far, the military’s adoption of additive manufacturing (AM)...
U.S. Congress Calls Out 3D Printing in Proposal for Commercial Reserve Manufacturing Network
Last week, the U.S. House of Representatives’ Appropriations Committee moved the FY 2026 defense bill forward to the House floor. Included in the legislation is a $131 million proposal for...