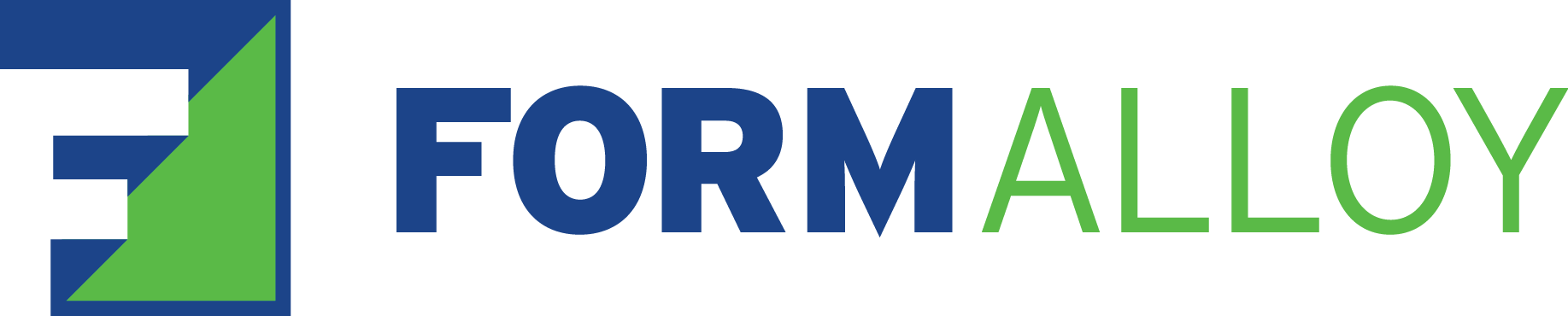
Directed energy deposition (DED) has emerged as a transformative technology, with its inherent ability to build new components, repair existing components, and enhance performance through multi-material solutions. This technology operates on the principle of precisely depositing material layer by layer, enabling the creation of intricate geometries with a wide range of materials. The feedstock includes both powder and wire that can be sourced commercially, typically at a significant cost advantage over other AM process feedstocks. At the forefront of the DED evolution stands FormAlloy, a pioneering force leveraging smart DED systems to reshape industries and set new benchmarks in performance and durability.
While multi-material and functionally graded components are being explored and researched, FormAlloy’s current end-use applications for DED include the defense industrial base (DIB), aerospace, energy, and consumer goods companies. High-value parts (due to material or simply availability) such as large brackets and aircraft landing gear components are utilizing DED to keep up with demand by manufacturing and repairing existing components. Both powder and wire are currently used as feedstock, depending on the performance requirements, cost, and availability of material.
But what makes DED so special beyond the versatility of application and material? The ability to sense and utilize in-situ machine and build data, not only real-time during the build, but for post-build analysis to support qualification and certification, is also possible with smart DED systems. FormAlloy developed a framework to sense and export data during the initial machine design and production over 8 years ago, and has continued to follow that framework as new sensors and hardware modules have become available. Today, FormAlloy’s DEDSmart® systems are arguably the only metal additive manufacturing (AM) systems that provide full time-stamped, open-source build data direct to the users.
The Future: Unveiling the Potential of Functionally Graded Materials (FGMs) and Custom Alloys
While FormAlloy’s current applications of DED are already revolutionizing manufacturing, the horizon holds even more promising advancements in materials. Looking ahead, the company foresees a transformative shift towards the adoption of Functionally Graded Materials (FGMs) in various industries. This includes consumer goods applications currently in development that will enhance the performance and lifetime for product end-users, and ultimately a competitive advantage for the companies producing the goods. When compared to traditional methods of applying an alternative material to an existing part, DED has outperformed due to the metalurgical bond achieved with the process, and the ability to slowly transition to the new material. Custom alloys are also being developed at a record pace, including one DED user who is now able to synthesize and evaluate up to 100 different alloys in a 24-hour period.
Unlike conventional materials treated as discrete entities, FGMs unlock an array of possibilities where material properties gradually transition, catering to specific performance requirements throughout a component. To visualize this concept, consider a turbine blade. As you move along a turbine blade in operation, different areas are experiencing different stress factors and environments. In a heat exchanger application, specific control over thermal properties can be exhibited. So, why not tailor the build of the blade or heat exchanger to account for that reality? In the future, it will.
As industries seek advancements to meet evolving demands, FormAlloy’s smart DED systems hold promise not only today, but for the future. In the future, the manufacturing landscape will entail the ability to build and repair, but also built with tailored material properties, revolutionizing performance, and durability across defense and industrial sectors.
Melanie Lang, Co-Founder and CEO of FormAlloy, will be participating at the upcoming Additive Manufacturing Strategies business summit in New York, February 6 to 8, 2024. Lang will be speaking a panel on Large-Format Metal AM.
Subscribe to Our Email Newsletter
Stay up-to-date on all the latest news from the 3D printing industry and receive information and offers from third party vendors.
Print Services
Upload your 3D Models and get them printed quickly and efficiently.
You May Also Like
The Market and Industry Potential of Multi-Material 3D and 4D Printing in Additive Electronics
Additive manufacturing leverages computer-based software to create components for products by depositing either dielectric or conductive materials, layer by layer, into different geometric shapes. Since its birth in the 1980s,...
3DPOD 262: Bio-inspired Design for AM with Dhruv Bhate, Arizona State University
Dhruv Bhate is an associate professor at Arizona State University. There, he looks at structures, materials, and design. Previously, he worked at PADT as well as in the semiconductor and...
3DPOD 261: Tooling and Cooling for AM with Jason Murphy, NXC MFG
Jason Murphy´s NXC MFG (Next Chapter Manufacturing) is not a generalist service; instead, the company specializes in making tooling. Using LPBF and binder jet, the company produces some of the...
3DPOD 260: John Hart on VulcanForms, MIT, Desktop Metal and More
John Hart is a Professor at MIT; he´s also the director of the Laboratory for Manufacturing and Productivity as well as the director of the Center for Advanced Production Technologies....