In October 2023, US Army Reserve Soldiers assigned to the 102nd Training Division (Maneuver Support) attended a two-week Combat Engineer Reclassification Course at Fort Leonard Wood in Missouri, where they participated in testing conducted on 3D printed containers designed for enhanced explosives effects. Fort Leonard Wood’s Counter Explosive Hazards Center (CEHC) facilitated the testing, which was a continuation of work done by EagleWerx Applied Tactical Innovation Center at Fort Campbell, Kentucky.
Using nearly 20 different 3D printed containers filled with explosive charges from the inventory that combat engineers are currently trained in, members of the 102nd measured the width and depth of the holes produced in order to quantify the different effects of each container. As with more or less everything the military does with additive manufacturing (AM), the project serves not only as R&D, but also as an invaluable training tool for educating service-members in the DoD’s latest, highest-priority technological advancements.
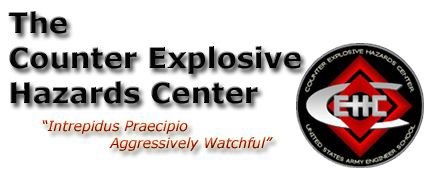
In a US Army press release about the 3D printed explosives containers testing at Fort Leonard Wood, Jon Toth, a CEHC training specialist and Reserve Soldier in the 102nd, explained, “EagleWerx originally did testing with their own 3D-printed designs and briefed their findings to the (US Army Engineer School). After that briefing, CEHC was tasked with taking the lead on determining if we could use our ongoing 3D printing projects to assist in getting a better explosive effect using our designs.
One of the things we try to emphasize is teaching Soldiers not what to think, because that’s very regimented, but teaching them how to think. When they understand the theory behind it, then they can apply it in different ways. Another advantage to showing it here in the schoolhouse environment is almost every major (US Army Forces Command) installation has an innovation lab or a 3D printing lab. And so, when they see some of the ideas here, with CEHC partnering with training units here, then they can go back to those FORSCOM installations and already have ideas in their head of what they can use that innovation lab for.”
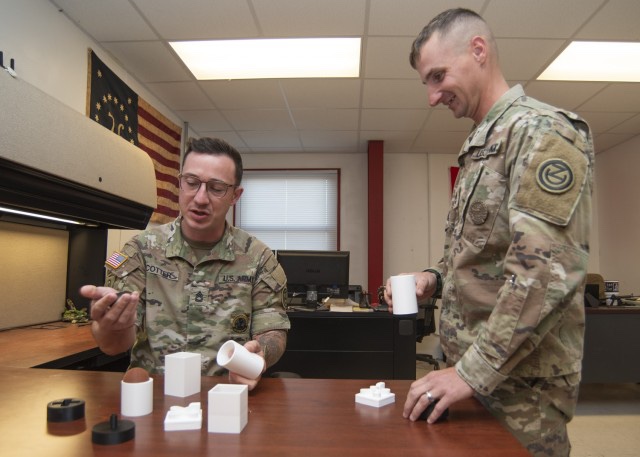
The CEHC project at Fort Leonard Wood fits into precisely the same context as the additive construction (AC) exercise at Camp Atterbury that I wrote about a couple of days ago. Aside from the central role of detonation testing, both examples bear out the theme of including members of the US armed forces reserves more prominently in the DoD’s buildup of its AM capabilities.
AM is of course just one component in a whole set of Industry 4.0 objectives: but, for reasons such as those mentioned above by CEHC training specialist/reservist Jon Toth, AM is an especially crucial aspect. Moreover, the fact that 3D printing is being deployed as a force multiplier makes it particularly compatible with the role that is being cultivated for reservists to play in the US military’s future.
In the long-term, the training of reserve forces in advanced manufacturing techniques should enable the US military to keep as many reservists as possible in support roles — as opposed to active combat roles — which should help the military avoid overburdening its reservists. Simultaneously, the same techniques tested by reservists, once they’re proven successful, can help the military lessen some of the burden on its maintenance, repair, and overhaul (MRO) personnel who are serving in active combat. Projects like this one, then, contain useful lessons for how militaries can realistically use AM to kill at least two birds with one stone.
Images courtesy of US Army/Fort Leonard Wood
Subscribe to Our Email Newsletter
Stay up-to-date on all the latest news from the 3D printing industry and receive information and offers from third party vendors.
Print Services
Upload your 3D Models and get them printed quickly and efficiently.
You May Also Like
3D Printing News Briefs, July 2, 2025: Copper Alloys, Defense Manufacturing, & More
We’re starting off with metals in today’s 3D Printing News Briefs, as Farsoon has unveiled a large-scale AM solution for copper alloys, and Meltio used its wire-laser metal solution to...
3DPOD 260: John Hart on VulcanForms, MIT, Desktop Metal and More
John Hart is a Professor at MIT; he´s also the director of the Laboratory for Manufacturing and Productivity as well as the director of the Center for Advanced Production Technologies....
3D Printing News Briefs, June 28, 2025: Defense Accelerator, Surgical Models, & More
In this weekend’s 3D Printing News Briefs, 3YOURMIND was selected to join an EU Defense Accelerator, and PTC has announced model-based definition (MBD) capabilities within Onshape. Finally, a study out...
EOS in India: AM’s Rising Star
EOS is doubling down on India. With a growing base of aerospace startups, new government policies, and a massive engineering workforce, India is quickly becoming one of the most important...