For another year running, I survived the bustling insanity that is formnext. With a reported 859 exhibitors, 196 speakers, 32,851 visitors (50% international), and 54,000 m² of exhibition space, Europe’s largest additive manufacturing (AM) trade show was as busy and interesting as ever. I visited with a lot of firms, and learned about the latest innovations in 3D printing materials, software, post-processing, and much more, including metal 3D printing.
Brian Birkmeyer, Product Line Leader for Binder Jet, and Chris Schuppe, General Manager of Engineering and Technology, at GE Additive invited 3DPrint.com for a chat to learn what’s been going with the company’s metal binder jet technology since the Series 3 was unveiled last year.
The update is that there’s actually not much of an update. I don’t mean that negatively. The team has been continuing to tweak the machine so that it’s entirely production-ready, and wanted to be totally transparent about the process. Birkmeyer said they’ve “continued to work through validation with 316L on the machines,” and that they ran into “a snag or two along the way, which slowed us down a little.”
“We took the time to actually reengineer those subsystems correctly, and now we’re retesting and things like that, ” he explained. “We’re getting some really good data off the machines.”
He said they’re pleased with the quality of parts they’re printing on the Series 3, and happy with the dimensional tolerance of sintering they’re getting downstream through the system. The casting tolerance (CT) scale classifies the precision level of cast parts, ranging from lower grades with more variability to higher grades demanding tighter precision. So far, according to Birkmeyer, GE’s data shows that sintering of its metal binder jet parts falls largely at CT6, indicating a moderate level of precision.
“It’s better than what we thought we would even be able to achieve, to be frank,” he said. “We’re very comfortably between CT7 and CT8 still, but when you look at a lot of the statistical data, it’s within CT6, inclusive of larger parts and inclusive of parts throughout varying heights in the build box, which is important.”
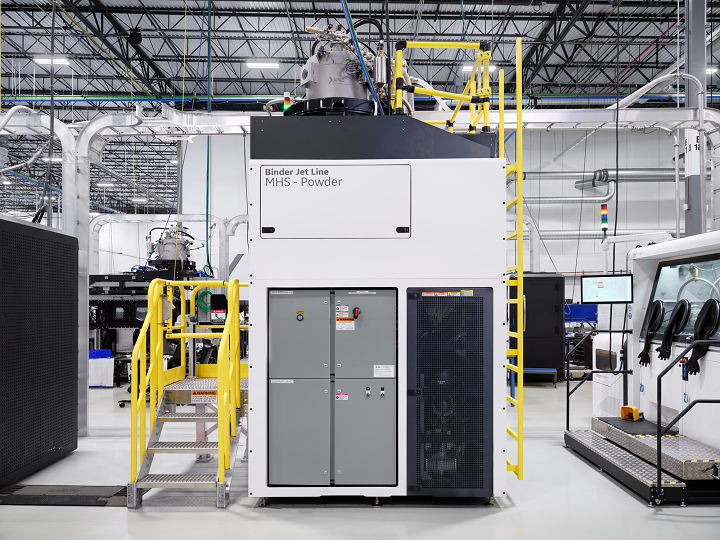
Birkmeyer also said the batch cycle has been validated to transfer over to a continuous sintering cycle—good news, as there was some concern in the broader marketplace that it couldn’t survive the cycle in a continuous furnace environment. The team recently demonstrated this achievement at its Cincinnati, Ohio facility.
“We don’t want to rush a product to the marketplace. We want to make sure that whatever we deliver is a production-quality machine, and not a piece of lab equipment. We’re not going to rush it out until we’re there.”
I asked if the company had a more decisive timeline for when the Series 3 might be ready, and Birkmeyer said “there will definitely be more that comes out next year.”
“We’re trying to figure out the right way to roll that out to the broader marketplace,” he continued. “Once we feel that we have a wide enough statistical data set that we can comfortably stand behind, and machines we can comfortably stand behind, that will be good build after build after build…once we get there, basically. And we’re getting closer every day to building that statistical database to prove that we have it.”
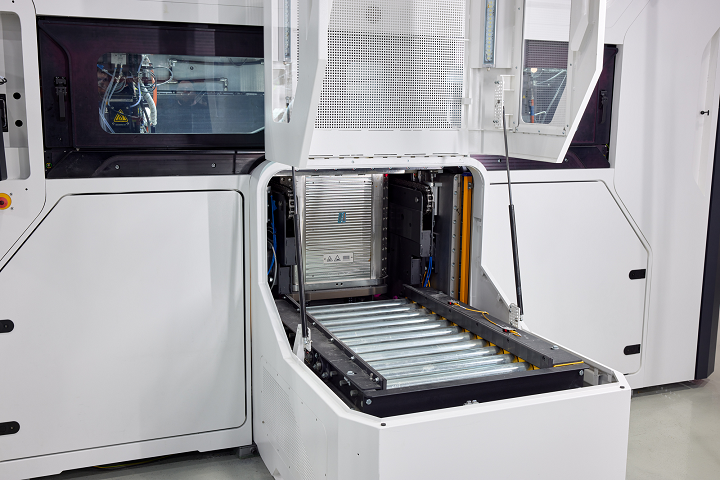
Back in 2022, when the Series 3 was first unveiled to the press, we learned that GE Additive was still taking customers for the current Series 2 development platform, and Birkmeyer confirmed that the company is working “hand-in-hand” with clients on the Series 2. Eventually, these users will transition over to the Series 3. However, the company is still taking on new customers looking for new materials and new applications for the company’s binder jet technology.
“Our AddWorks team has been a huge benefit for us in binder jet,” he said, referencing GE Additive’s metal AM consulting team. “The thing you have to consider with binder jet is you’re really designing for sintering, as long as your machine’s capable, and your part’s strong enough to de-powder, which [our machine is]. Anything that doesn’t include the thought process of sintering on the back end is not going to yield a productive process.”
He said GE Additive is still focused on helping customers learn, as well as learning from new customers about expectations, part geometries, and more. While he was unable to tell me the name of the company, Birkmeyer did share that they are now working with a customer in a new industry for them: the medical sector.
“It’s a customer that is coming in and helping drive that adoption curve for binder jet in medical,” he said. “We continue to try and expand our horizons in new industries, while still continuing to work with our parent company GE Aerospace to try and get binder jet components on aerospace platforms.”
Schuppe chimed in, noting that every aerospace company visiting GE Additive’s booth is “complaining about the availability of castings.”
“Binder jet is specifically targeted to go after small to medium castings. Three different aerospace companies, unsolicited, showed up here today and asked, ‘What can you do for castings?’ Those companies can’t get castings, even existing castings on existing platforms. That’s exactly what binder jet is aimed at displacing, or providing a secondary manufacturing method in the event you have a supply chain problem.”
The bottom line is that it’s taking GE Additive a little longer than originally thought to get the Series 3 ready for the market, but they are “making great strides.” As Birkmeyer explained, it can’t be anything less than production quality.
“We may evolve into more of a production slot reservation system, and/or more of a full court press,” he said. “We’re trying to balance right now industry customers versus supply chain, and how much we lean into that. So as we figure out exactly the right methodology for garnering more customers, you’ll be the first to know.”
Stay tuned to 3DPrint.com for any further updates on the Series 3 as GE Additive works to get it ready for the broader marketplace!
Subscribe to Our Email Newsletter
Stay up-to-date on all the latest news from the 3D printing industry and receive information and offers from third party vendors.
Print Services
Upload your 3D Models and get them printed quickly and efficiently.
You May Also Like
Making 3D Printing Personal: How Faraz Faruqi Is Rethinking Digital Design at MIT CSAIL
What if your 3D printer could think more like an intelligent assistant, able to reason through a design idea, ask questions, and deliver something that works exactly the way the...
Reinventing Reindustrialization: Why NAVWAR Project Manager Spencer Koroly Invented a Made-in-America 3D Printer
It has become virtually impossible to regularly follow additive manufacturing (AM) industry news and not stumble across the term “defense industrial base” (DIB), a concept encompassing all the many diverse...
Heating Up: 3D Systems’ Scott Green Discusses 3D Printing’s Potential in the Data Center Industry
The relentless rise of NVIDIA, the steadily increasing pledges of major private and public investments in national infrastructure projects around the world, and the general cultural obsession with AI have...
Formlabs Teams Up with DMG MORI in Japan
In late June, Nick Graham, Chief Revenue Officer at Formlabs, announced on LinkedIn that the company had partnered with DMG MORI, one of the world’s leading machine tool companies, to...