Forerunner 3D Printing (F3DP) is a pioneer in the 3D printed firearm industry. With special licenses that allow it to manufacture and test guns, including automatic weapons, the company navigates the complex waters of 3D printing for the firearms industry. In an interview with 3DPrint.com, founder Paul DeWys sheds light on the technology and the regulatory environment surrounding 3D printed firearms.
Catering primarily to military, law enforcement, and firearms manufacturers—expressly not selling to civilians—the company focuses on job shop and low-volume production services. Its arsenal of 3D printing technologies is vast, including stereolithography (SLA), HP Multi Jet Fusion (MJF), Stratasys PolyJet, fused deposition modeling (FDM), selective laser sintering (SLS), and Carbon’s continuous liquid interface production (CLIP). Beyond printing, the company offers various part finishing options, from sanding to Cerakote painting.
DeWys’s journey into this niche began with his interest in evolving tech. By 2009, he had set up DeWys Engineering (DE). However, by 2016, his shift towards 3D printing became evident. That year, he acquired assets from the closing of Select Manufacturing, which marked the birth of F3DP. By 2018, with a new HP MJF 4200 printer, the startup became one of a small number of 3D printing specialists in existence for automation and machine build firms nationwide. Always a firearms enthusiast, DeWys began investigating the world of 3D printed firearms upon recognizing the strength of parts from the MJF machine. After crafting a durable AR lower receiver from nylon 12, he showcased the material’s strength on YouTube.
While this stirred mixed reactions, notably from HP, the innovative approach to testing the strength and durability of a printed receiver highlighted the incredible potential of 3D printing for making firearm parts. After seeing the online feedback on his first 3D printed firearm, DeWys decided it was worth delving more deeply into researching this market. He found no polymer-based additive manufacturers with active federal firearm licenses. To him, this looked like an opportunity.
Digital disruption
Over the next year, DeWys pursued a federal firearms license (FFL 07) and received it. In the fall of 2022, he began talking to customers in the firearms industry. He quickly discovered that most parts clientsc wanted to print were non-serialized components, which the Bureau of Alcohol, Tobacco, Firearms, and Explosives (ATF) doesn’t regulate. However, being able to print serialized parts and demonstrate industry knowledge was a hit with potential customers. By the summer of 2023, customers requested DeWys for full auto-rated parts. This required that he build a machine gun for testing. Since his business had also received a Special Occupancy Taxpayer (SOT 02) license, he was able to build a machine gun for testing and decided to do it using 3D Printed parts.
“Machinegun production is exclusively the realm of manufacturers doing research and development for the military and law enforcement. We work with many of these defense companies and print parts for them that go into the firearms they build. We are also experimenting with 3D printing suppressors, but again, only working with suppressor manufacturers; none of this is for the civilian marketplace.”
Pioneering precision
With credentials like the FFL07 and SOT 02, DeWys recently tested a rifle to determine if its 3D printed parts, including the main body and hand guards, could handle rapid, continuous firing without malfunctioning. The team 3D printed the rifle’s lower receiver and handguard on the HP MJF 4200 using nylon 12. Afterward, they coated the parts with H series Cerakote for enhanced durability. This firearm has seen over 1,000 rounds of 5.56 ammunition without any issues.
The startup works primarily with nylon 12 for firearms customers. This material is renowned for its rigidity and resilience. It forms the backbone of most firearm-related prints. While there are other materials that F3DP uses for other applications, such as nylon with 40% glass fiber and TPU elastomer, the company cater to niche needs when it comes to firearms work, says DeWys.
The potential benefits of transitioning from traditional gun manufacturing to a modern, tech-driven method are vast but not without challenges. DeWys stresses the significance of testing these weapons in real-world environments, from extreme temperatures to rough terrains, such as sand and water exposure. This push for rigorous evaluation stems from a business standpoint and customer inquiries that drive innovation and understanding. It’s a practice that differentiates their business model from others in the field.
“We’ve become a hub for expertise, providing engineering services to firearms companies and assisting in the design of weapon systems and accessories. With a rich background in designing for additive processes, our team is constantly approached to quote projects that include the engineering, prototyping, and production as a turn-key package.”
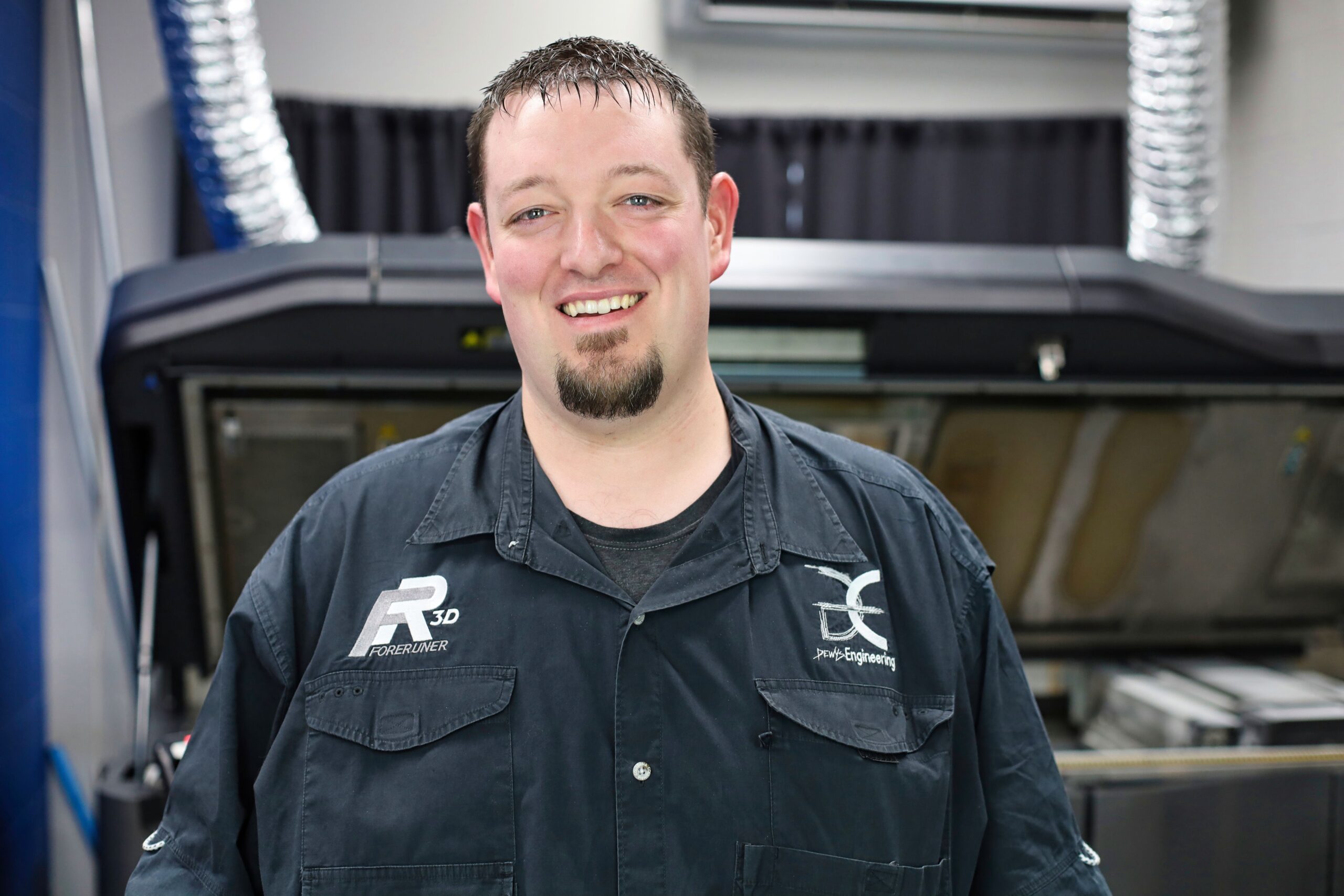
One of the major challenges DeWys faces with 3D printing is maintaining the accuracy of the parts, compared to traditional CNC machining. This results in hybrid solutions, printing parts, and then post-machining them to achieve the desired tolerances. DeWys also said that while the parts might be pricier, there are no upfront tooling costs, offering significant design flexibility and short lead times, a unique technology trait. This flexibility aids businesses in launching new products and deciding between traditional injection molding or 3D printing based on their volume and niche.
“The combination of 3D printing and the spirit of continuous innovation in the firearms industry constantly brings up new challenges when working within existing laws. Standard gun laws, which until recently were written only to regulate traditionally manufactured guns, aren’t always 100% clear in how they apply to 3D printed firearms. Moreover, the firearm community is historically known for its skill in pushing the boundaries of regulations. Because of this, we have had to move very carefully as we start to work more and more with serialized firearms components. This includes contacting the ATF to get feedback on what they want to see from companies like us. We want to play by the rules and stay legal while still being able to help our customers meet their goals.”
Public opinion divided
Discussions about how to regulate 3D printed guns while respecting gun ownership rights under the Second Amendment are ongoing. DeWys points out that many within the subculture of 3D printed firearms often engage in the practice not out of malice. They’re driven by a desire to push boundaries, innovate, and occasionally provoke. He notes that the culture isn’t necessarily about contributing to crime but often “centers around design, innovation, and challenging the traditional ways of thinking.”
“At the end of the day, 3D printing is a tool. Even if it seems more out in the open and less controlled, it’s not automatically more risky than other production methods like subtractive manufacturing. We always do our absolute best to play by the rules and work with regulatory bodies like the ATF,” says DeWys.
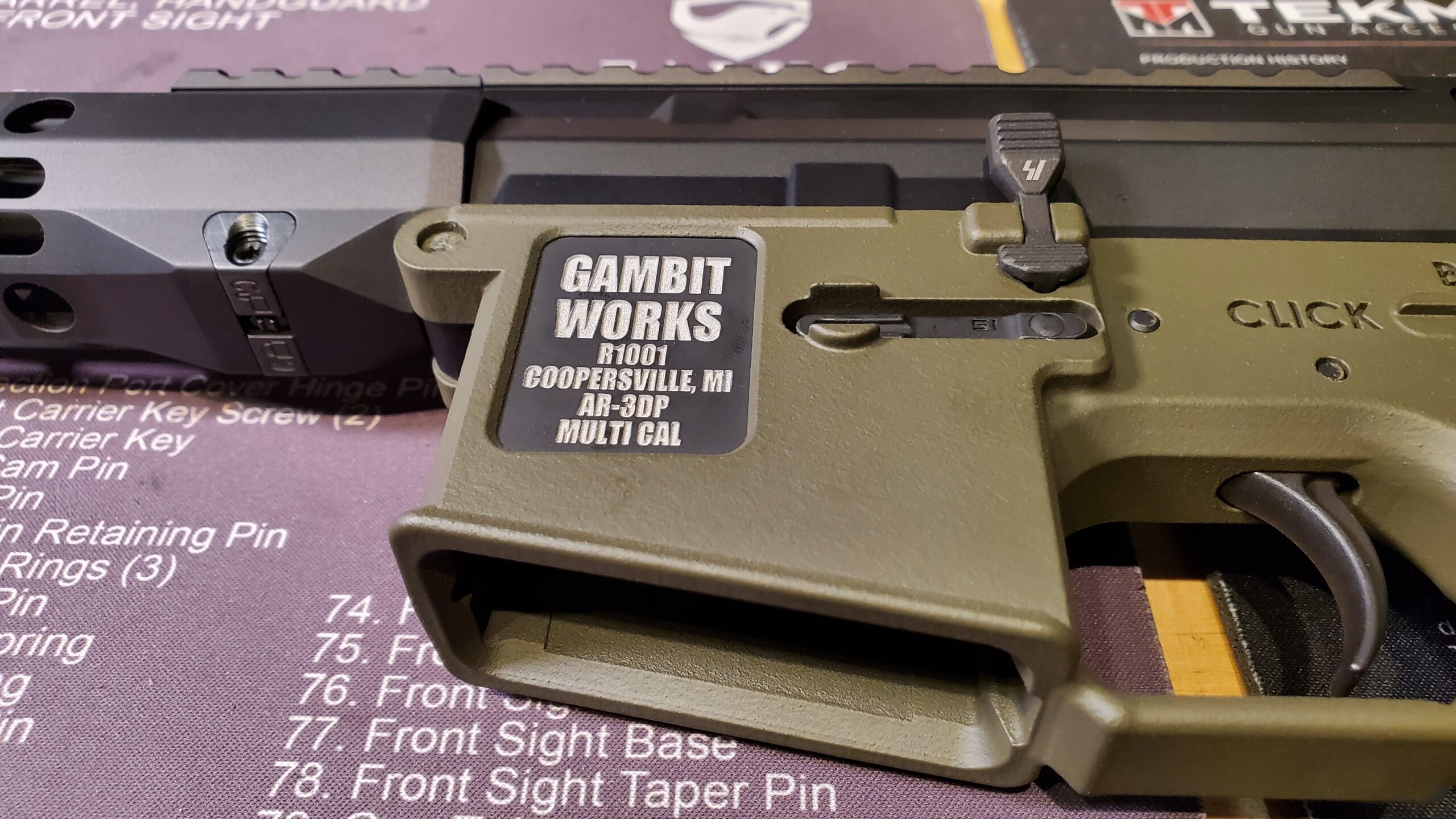
“Ghost guns often come up when talking about 3D printed weapons. In my opinion, as a firearm builder and enthusiast, there are quicker and easier ways to get a dodgy gun in the US than buying a desktop 3D printer and trying to figure out how to print a usable firearm receiver on it. This year, the ATF changed the game. They introduced new rules about manufacturing homemade guns, especially how these guns must be marked and serialized. As 3D printing technology continues to expand, the old laws will need to catch up. Open communication between the industry and the ATF is necessary. It ensures innovation isn’t stifled while still allowing law enforcement to do their jobs effectively.”
The growing trend in arrests linked to 3D printed guns doesn’t go unnoticed. DeWys mentions that in 2020, many law enforcement agencies didn’t distinctly categorize these weapons, leading to limited data. As awareness grew, data collection improved, highlighting the technology’s implications.
“Contrary to what many believe, most criminals only 3D print the gun’s receiver, not the entire weapon. This part is pivotal since in the US, one can legally purchase every piece of most firearms except this serialized component.”
DeWys works with the ATF to ensure he follows all the rules regarding 3D printing guns. This guarantees the company’s stance is both pioneering and regulatory-compliant. But there are still issues. The unique challenge here is ensuring the markings, which identify each firearm, are durable and resistant to tampering. When the part in question is not considered a serialized firearms component, the range of companies F3DP will work with is wide open since these are not regulated components.
Beyond the blueprint
When it comes to 3D printed guns, DeWys observes a clear division, mirroring typical disagreements on gun rights in America. Many in the gun community are supportive, but there’s still resistance. He says, “The complexities of 3D printing make the topic tough for many to get their heads around.”
Planning the path for future 3D gun legislation is tricky, especially given the different gun laws across states. With 3D printing, the ease of sharing and obtaining gun designs challenges traditional methods of gun control. DeWys stresses the need to deepen our understanding and adapt to this transformative technology.
Subscribe to Our Email Newsletter
Stay up-to-date on all the latest news from the 3D printing industry and receive information and offers from third party vendors.
Print Services
Upload your 3D Models and get them printed quickly and efficiently.
You May Also Like
The Market and Industry Potential of Multi-Material 3D and 4D Printing in Additive Electronics
Additive manufacturing leverages computer-based software to create components for products by depositing either dielectric or conductive materials, layer by layer, into different geometric shapes. Since its birth in the 1980s,...
3DPOD 262: Bio-inspired Design for AM with Dhruv Bhate, Arizona State University
Dhruv Bhate is an associate professor at Arizona State University. There, he looks at structures, materials, and design. Previously, he worked at PADT as well as in the semiconductor and...
3DPOD 261: Tooling and Cooling for AM with Jason Murphy, NXC MFG
Jason Murphy´s NXC MFG (Next Chapter Manufacturing) is not a generalist service; instead, the company specializes in making tooling. Using LPBF and binder jet, the company produces some of the...
3DPOD 260: John Hart on VulcanForms, MIT, Desktop Metal and More
John Hart is a Professor at MIT; he´s also the director of the Laboratory for Manufacturing and Productivity as well as the director of the Center for Advanced Production Technologies....