In a significant move within the evolving landscape of 3D printing for space applications, Agile Space Industries and 6K Additive join forces to propel space technology. The duo plans to certify and use 6K Additive’s Nickel 625 (Ni625) powder for customer space applications, focusing on crafting critical rocket components. First, 6K Additive’s superalloy powder is being certified for use at Agile Space’s manufacturing facility, where it will be harnessed to 3D print components destined for integration into Agile Space’s A2200 bipropellant hypergolic engine.
The two companies, operating from different corners of the United States, have joined forces to combine their knowledge and resources, working together to push the limits of space exploration technology. 6K Additive, based in Pittsburgh, Pennsylvania, specializes in producing sustainable materials for AM, while Agile Space, headquartered in Durango, Colorado, excels in advanced propulsion solutions.
The initial implementation of the Ni625 powder will take place within Agile Space’s A2200 bipropellant hypergolic engine. Unlike regular engines that need a spark to start burning fuel, the A2200 engine uses a special kind of fuel that starts burning when it comes into contact with another substance. This particular kind of fuel is known as hydrazine and is often used in rockets and spacecraft engines because it releases a lot of energy when it reacts. Working alongside hydrazine is another substance called MON3 (or Mixed Oxides of Nitrogen.), which provides the oxygen needed for the hydrazine fuel to burn. So, when hydrazine and MON3 come together, they create a controlled explosion, producing hot gases that jet out from the rocket engine’s nozzle and push the rocket forward. Thanks to the smart combination of hydrazine and MON3, the engine works without needing a traditional ignition spark.
According to Agile Space, even though the engine is really light—only weighing about 5.9 kilograms—it can create a powerful force of 500 pounds of thrust. This was possible thanks to additive manufacturing (AM).
Kyle Metsger, Agile Space’s director of additive technology, explained: “By weight, 85% of our engine components are additively manufactured, meaning we rely heavily on AM powders that can withstand the extreme temperatures and forces generated during take-off and flight. 6K Additive allows us to additively manufacture using high-quality powders that are required for our critical applications while also helping us meet our environmental goals through their recycling program and sustainably manufactured powders. 6K Additive can deliver extremely consistent powder that allows our production line to run the long build times required for these complex components.”
One of the most remarkable aspects of Agile Space’s approach is its rapid development cycle. Traditionally, aerospace component development has been known to span over two decades. However, Agile Space has harnessed the agility of AM to reduce this timeline to just 12 months.
“A year-long development cycle still sounds like a very long time in many industries, but we are showing the primes in the aerospace industry what the future looks like. Moving to the larger TruPrint 5000 machine gave us the ability to qualify the new parameters for the machine and material simultaneously. In this way, AM allows us to be ‘Agile’ in name and practice,” went on Metsger.
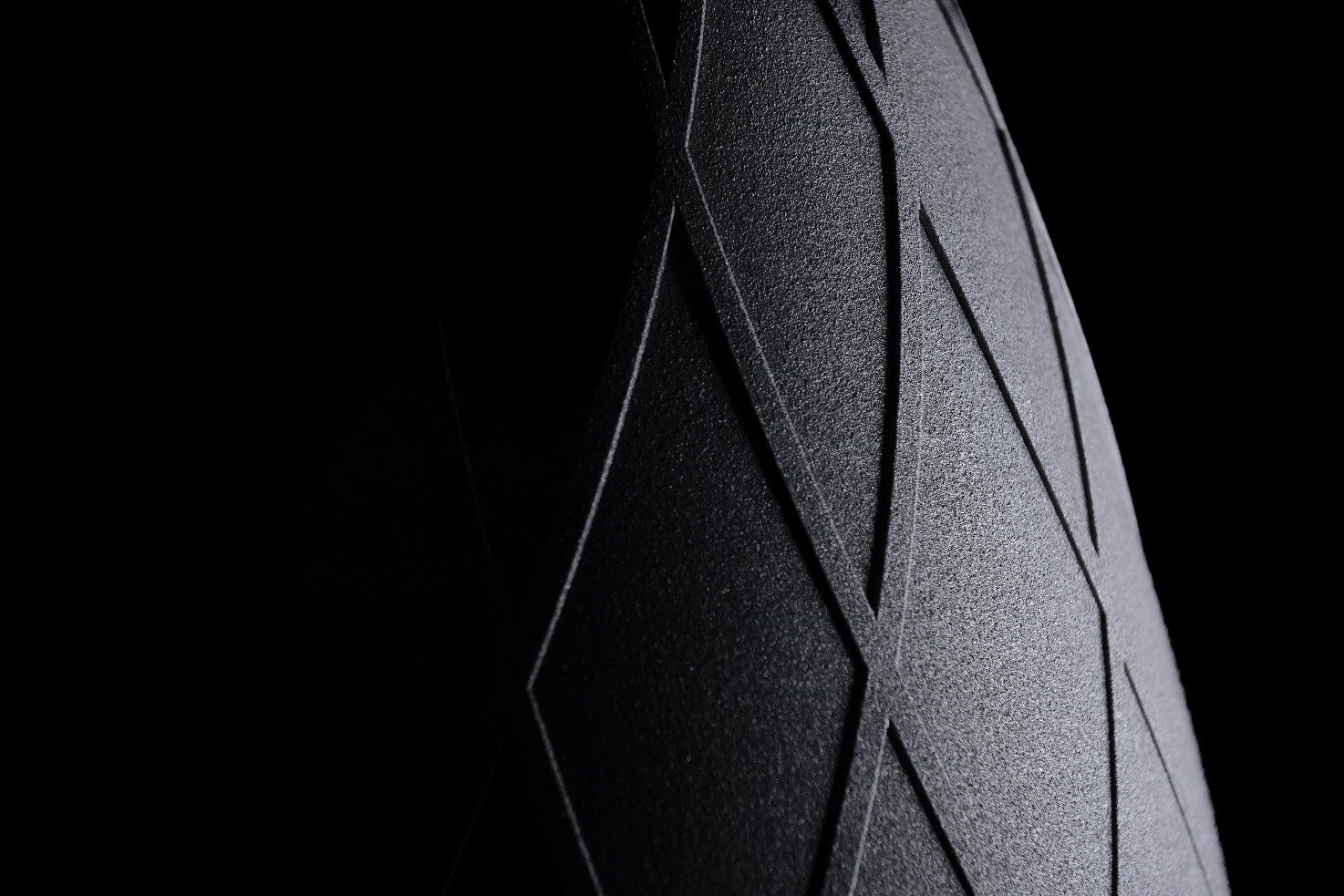
Furthermore, the A2200 engines, incorporating 6K Additive’s Ni625 powder, are ready to find their place on a lunar lander vehicle. Engineered to excel in the rigors of demanding lunar missions, the A2200 engine boasts a specific impulse exceeding 318 seconds, claims Agile Space. The engine has a special part called a pintle sleeve that helps control its power. This special part allows the engine to change how much power it uses very quickly, becoming useful for missions to the moon where the rocket needs to ensure smooth and precise control during the mission. The engine can quickly go from using half its power to using all of it in less than a second, making it the perfect choice for intricate maneuvering sequences that lunar missions demand.
Frank Roberts, president of 6K Additive, commented: “We are always excited to partner with customers like Agile which leverages our high-quality powders to produce critical rocket parts to land on the moon. The fact that we can enable space exploration while continuing to lead the way with sustainability at home on Earth is the best of both worlds. Agile has a cradle-to-grave mentality around its products, and having 6K Additive supply the company with high-quality, sustainably produced Ni625 and provide an established waste stream to help with its environmental stewardship speaks to our mission of going beyond expectations for our customers.”
Overall, the qualification of 6K Additive’s Ni625 powder for Agile Space’s A2200 engine not only holds the promise of advancing lunar missions but also demonstrates the power of partnerships to drive transformative change. As Agile Space harnesses the potential of AM to change the aerospace industry, 6K Additive continues to provide high-quality materials that propel space exploration into a new era while staying true to its commitment to sustainability.
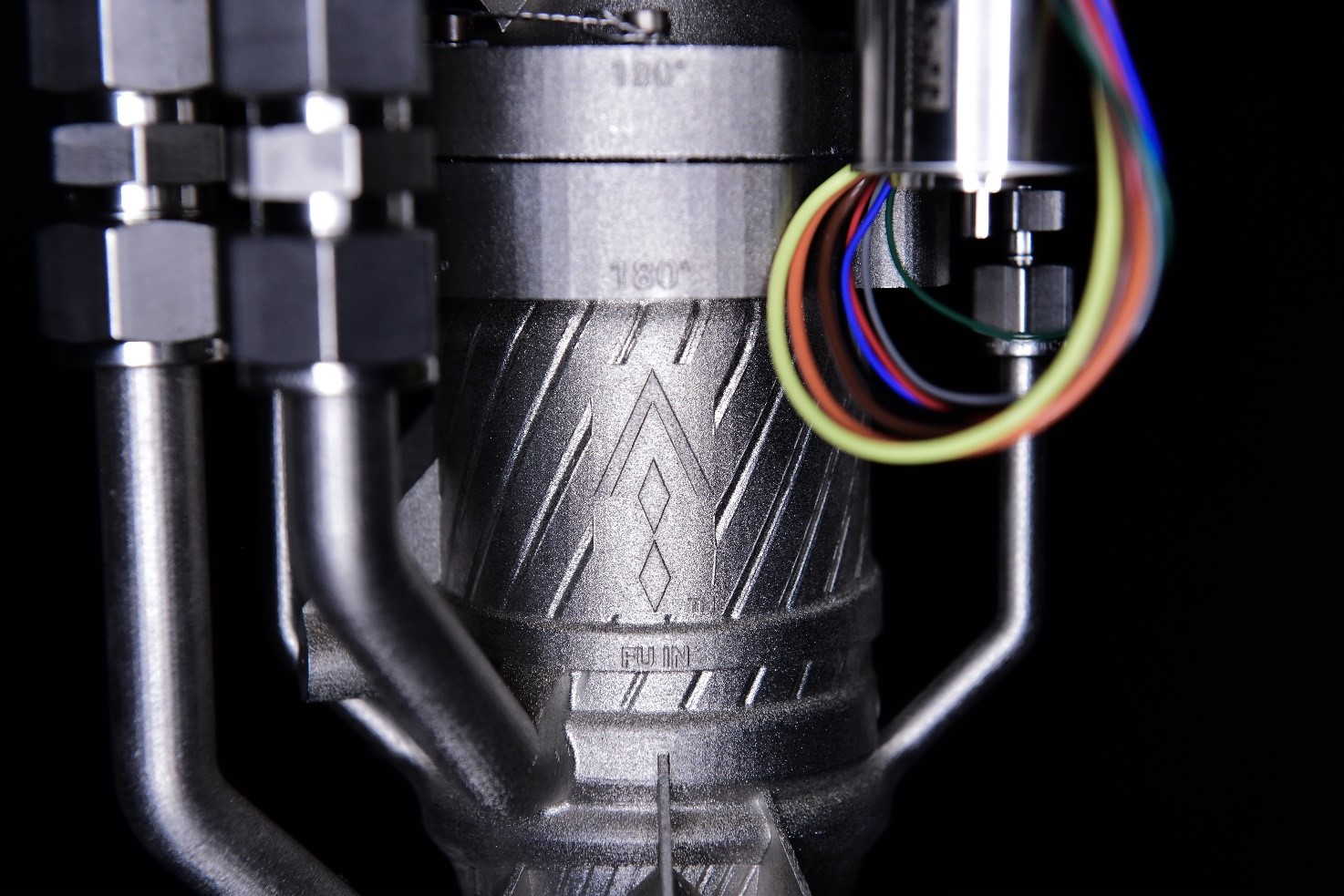
Both 6K Additive and Agile Space have been at the forefront of advancing 3D printing in space applications. In 2020, 6K Additive partnered with Relativity Space to create a closed-loop supply chain, converting certified scrap materials from Relativity into 3D printing powder through 6K. This innovative initiative also explored the development of new materials customized for rocket manufacturing and space exploration.
In a similar effort, Agile Space has taken strategic steps to ramp up its 3D printing capabilities. Acquiring the 3D printing service bureau Tronix3D, now Agile Additive, helped the company accelerate the aerospace supply chain while driving advancements in metal 3D printing. In addition, Agile Space recently closed a $13 million seed funding round to advance metal AM capabilities. Together, the companies reinforce their commitment to pushing the boundaries of 3D printing in the ever-evolving space technology landscape.
Subscribe to Our Email Newsletter
Stay up-to-date on all the latest news from the 3D printing industry and receive information and offers from third party vendors.
Print Services
Upload your 3D Models and get them printed quickly and efficiently.
You May Also Like
Making Space: Stratasys Global Director of Aerospace & Defense Conrad Smith Discusses the Space Supply Chain Council
Of all the many verticals that have been significant additive manufacturing (AM) adopters, few have been more deeply influenced by the incorporation of AM into their workflows than the space...
EOS in India: AM’s Rising Star
EOS is doubling down on India. With a growing base of aerospace startups, new government policies, and a massive engineering workforce, India is quickly becoming one of the most important...
PostProcess CEO on Why the “Dirty Little Secret” of 3D Printing Can’t Be Ignored Anymore
If you’ve ever peeked behind the scenes of a 3D printing lab, you might have caught a glimpse of the post-processing room; maybe it’s messy, maybe hidden behind a mysterious...
Stratasys & Automation Intelligence Open North American Tooling Center in Flint
Stratasys has opened the North American Stratasys Tooling Center (NASTC) in Flint, Michigan, together with automation integrator and software firm Automation Intelligence. Stratasys wants the new center to help reduce...