A new cultural frontier is emerging, one which will continue to shape the planet’s political and economic fate for the rest of this century and beyond. It is not a frontier between Earth and the rest of the physical universe, or one between the real and the virtual, nor even one between organic and artificial intelligence.
It is difficult to even find a single phrase to name exactly what the dividing line is, but for the sake of brevity we can think of it as the frontier between conservation and waste. Ultimately, whatever way you might describe it, it is primarily a symptom of the transition from a world where resources were plentiful and cheap, to one where they are scarce and expensive. If this sounds like too grandiose a lead-in to an article summarizing a 3D printing industry summit, then you clearly haven’t attended the Large Scale Additive Action Team (LSAAT) conference (June 22, 2023).
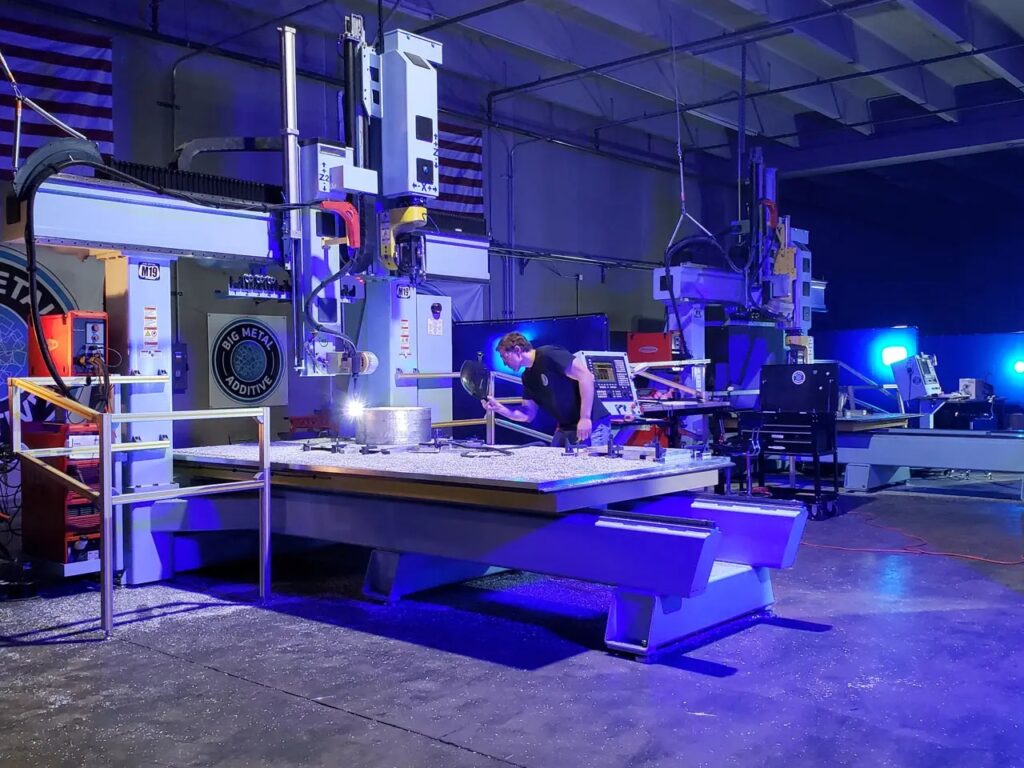
To be fair, relatively few people outside the relevant industries have been to LSAAT, which falls on the last day of a three-day event, the first two days being devoted to the Cold Spray Additive Action Team (CSAAT). Before attending, I found the use of the term “action team” a bit curious, wondering how it would fit in with the standing around and chatting, or sitting and listening, that I’ve become familiar with at additive manufacturing (AM) events. However, in less than an hour of my being at the DCU Center in Worcester, Massachusetts, the meaning behind the name of the organization became clear.
Small Events Breed Cohesion
For one thing, it is not a large event: it only took up the third floor of the DCU Center, and as I heard someone comment, only somewhat wryly, regarding the main conference room, “There’s probably more than half the entire cold spray industry in there.” Thus, in military terms — the terms most appropriate for an event where such a preponderance of the focus was on the Department of Defense (DoD) — it makes sense to think of this area of the AM sector as a “team”, the smallest unit making up an army’s organizational hierarchy.
Relatedly, the companies involved, from market segments like cold spray, friction stir welding (FSW), and robotic arm-driven DED, do certainly compete with one another: nonetheless, they also cooperate more so than is probably the case in other areas of the sector these days. This is simply a necessity for a group of separate entities that are trying to maintain their separateness, while simultaneously establishing the aggregate of their operations into a fully-fledged market. Moreover, in this specific case, the competition is not so much other companies in the same, still rather finite, space.
Instead, the competition is against wastefulness, i.e., against the prevailing status quo of gigantic, slow, inefficient organizations, found most notoriously in the US defense industrial base, but obviously pervasive across all of global heavy industry. The competition is a fight to only make as much as we need, when we need it, while wasting as little material as possible in the production process and as little energy as possible in the shipping process. And everyone on the team that is large scale AM is itching to do battle on that fight’s frontlines.
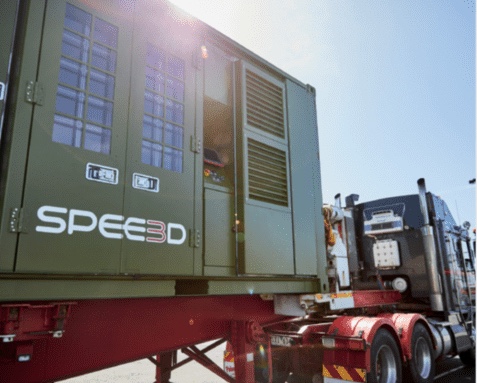
To be sure, broadly, eliminating industrial glut may be one of the handful of key motivating factors driving the whole AM sector. But it is most strikingly catalyzing the actions being taken by those concerned with printing the largest parts, if only because, in the fight against industrial wastefulness, that is where one will find the highest proportion of low-hanging fruit.
A New Transcontinental Railroad? Janice Bryant’s Keynote
Janice Bryant, the Expeditionary and Sustainment Technology Manager for the US Naval Sea Systems Command (NAVSEA), gave the keynote address, which began with Bryant doing an impersonation of an old-school carnival barker, imploring everyone to come see the amazing turtle girl. Even if her doing that didn’t end up having a point, I would’ve fully approved of it as a refreshingly attention-grabbing way to kick off an AM conference.
Of course, Bryant did have a point, which is that AM is still plagued by hype fatigue following the bust of the early 2010s desktop 3D printing boom. Rather than following up on this point with stern admonishments against getting too optimistic about AM’s potential — as is typically heard these days at AM conferences — Bryant did the opposite. She made the most convincingly realistic case I’ve heard for precisely why AM is worthy of all the hype, grounding her argument in a historical analogy I’ve also thought about frequently (albeit for different reasons) when thinking about the sector’s potential:
“What if I told you about another supply chain disruption, and this one took six-month delivery cycles and reduced them to six days?” Bryant prompted the audience. “It would create access to markets that had previously been inaccessible. [It reduced] shipping costs, not by 50 percent, not by 90 percent, but by 95 percent. I’m going to reduce your shipping costs to less than 5 percent of what you pay today — what kind of opportunity would that present for us? And when did something like that ever happen before? Has it? … Actually, it has, and it brought unimaginable change, an unimaginable opportunity. And ladies and gentleman, I believe that, this morning, is what we have in front of us: it’s that opportunity.”
It was a compelling way to start, and it got more compelling as she continued:
“So, what was that great disruptive change? The Transcontinental Railroad…In the 1860s, after the Civil War, with the nation divided not only from the Civil War…[but also] geographically by this great thing in the middle of our country called the Great Plains… We couldn’t get across it. Six months by wagon trip, if you were lucky, six months or more by ship to get around the backside — if you were lucky. But the Transcontinental Railroad managed to bridge those two parts of us together and created an opportunity and access to the Great Plains that changed our country and changed many things for others.”
I thought about the railroad analogy for much of the rest of the day, and have continued to reflect on it here and there since I got back from LSAAT. Prior to that, the context I’ve most frequently considered it in is the EV market, specifically in terms of the transformation to the global power grid that will be required in order to logistically support the expected exponential increase in EV demand.
As Bryant also pointed out in her keynote, there in fact wasn’t enough available capital in the entire US to fund the construction of the Transcontinental Railroad. This aspect has always been what has interested me most about that particular historical development: it was a singularly consequential catalyst for the consolidation of international capital, which in turn was largely responsible for triggering the earliest stirrings of contemporary globalization.
To me at least, the most fascinating thing about the analogy is that, in many ways, the point of the 21st century transformation is to halt, to whatever extent possible, the destruction still being wrought by that of the 19th century. That is, the gains from globalization must be conserved in whatever way possible, while simultaneously minimizing the acceleration of waste unleashed by those same gains. Fossil fuel-powered transportation infrastructure used to seem fast. Now, it seems slow. Meanwhile, everyone’s time and energy is being wasted waiting around for parts that — still theoretically, at this point — could simply be produced at the point of need, with drastically minimized shipping emissions, only as much material used as was needed to make the parts produced, and the potential in place for genuine circular economies.
At the same time, many of the underlying conditions are much the same as they were in the 19th century. There is not enough capital in any one country for electrification to be a unilateral effort on behalf of a single entity. Massive structural changes in all areas of the economy need to take place for it to happen. And an infinite pool of differing attitudes and opinions on how the transition should take place is more or less spontaneously forming into separate blocs.
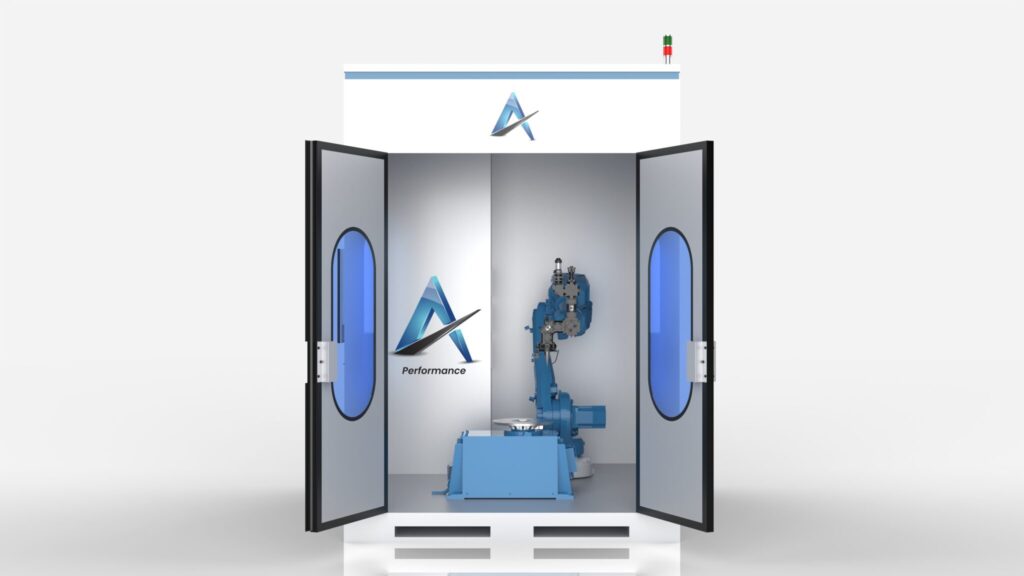
“I would suggest that [AM] is truly a new frontier. And unlike the Great Plains and what we saw with the railroad, this new frontier is really our last vestige where the physical world meets the digital world, where digits become dust. Partnerships and competitions are huge in this area. Let’s go take one more lesson learned from our friends in the past. You might remember the name Cornelius Vanderbilt — back to [the topic of] risk. Cornelius started as a small shipman in New York, used his savings to buy a rowboat, started faring things around, became the shipping magnate of New York…He saw the railroad movement coming and sold his entire shipping fleet and invested — just prior to the Transcontinental Railroad — in rail…”
Variations of everything involved in that past transformation are also happening today. The difference is, you used to have to use more energy to save time. Now, by speeding things up, humanity could somehow simultaneously also conserve energy.
Hurdles on the Path to Efficiency: Expert Panel Discusses Workforce Obstacles
Of course, even as the possible future alluded to thus far seems closer than ever, it is still very much in the future. The discussion/Q&A session with six large-scale AM insiders, which wrapped up the event, made clear what so many other observers have emphasized over the last few years: the way forward depends on workforce development.
The panel included Steven Camilleri, the CTO of cold spray AM original equipment manufacturer (OEM) SPEE3D; consultant John Barnes, of The Barnes Global Advisors; Dave Hofferbert, president of FSW OEM Bond Technologies; Slade Gardner, the president and founder of Denver service bureau Big Metal Additive; Dennis Harwig, professor of materials science and engineering at Ohio State University; and Dr. Tim Eden, head of the material science division at the Applied Research Laboratory at Penn State University.
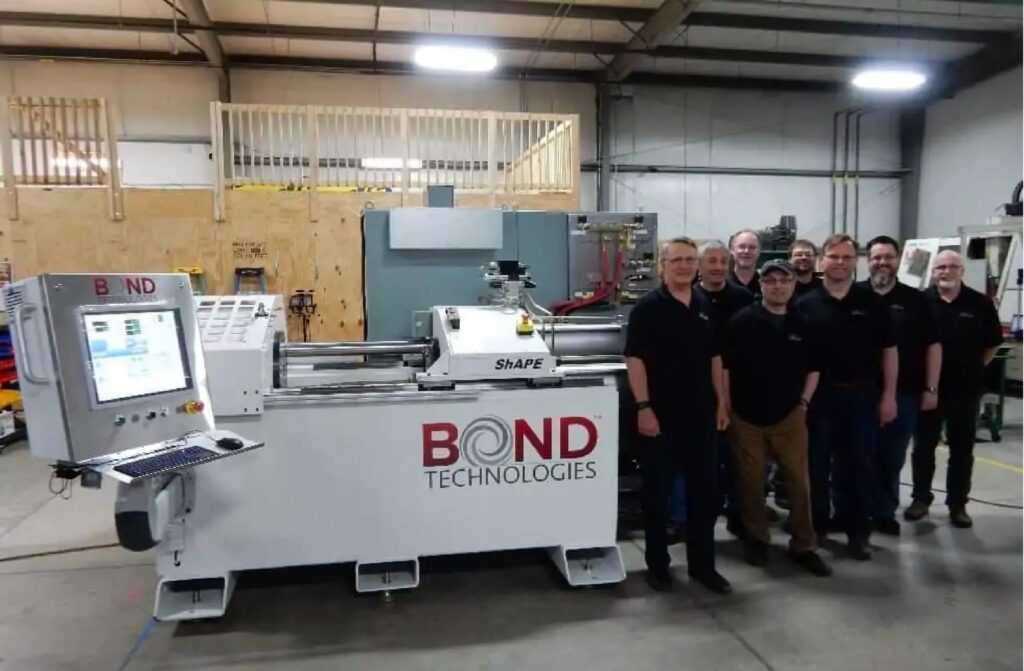
While the panel may have been from all different areas of the AM sector, both theoretical and practical, there was universal, resounding agreement that there are simply not enough manufacturing laborers in the US, and that this will remain an intractable problem without aggressive action. In this context, the sheer lack of metallurgists that aren’t nearing retirement age is perhaps the single most alarming factor to contemplate, when you consider the impact this could have on just about every major 21st century national economic objective:
“Universities chase money,” said Dr. Tim Eden, “[so] the metallurgy programs went away. And I think there’s a lot of schools in this country that are fairly big schools who really don’t have a good metallurgy program. Some of the largest universities, you’d be surprised that they don’t have a steel metallurgist on their faculty. And the average age of a metallurgist in this country, I think, is somewhere in the fifties. And so we need to have good investment — money — in order to get people to become metallurgists and get back to some of the basics…I think additive manufacturing is bringing it back, but there is really a big lack of metallurgists in this country.”
Gardner, from Big Metal Additive, sees everyday how this lack of relevant workforce development is holding back progress in the AM sector:
“We’ve been looking for employees for project management. We end up with donut [nothing]…We’ve been looking for quality engineers. We end up with different industries that don’t apply to aerospace quality metrics. We just published a job requisition for business analyst. …We need someone to collect manufacturing process data on the shop floor and feed it into our [Sales, Inventory & Operations Planning]. We can’t get anyone to apply for these roles. We’ve changed the title of these job requisitions four times and we can’t find business professionals to engage in manufacturing a production management to run the fundamentals. And that’s a huge gap.”
Barnes made the excellent point that, long-term, the problem can probably only be solved by adding workers from groups traditionally left out of the engineering and manufacturing labor pools:
“I’ve got two daughters. So, in 1966, roughly, 1 percent of engineering degrees went to women. Today, it’s like 20 percent. So it’s a huge improvement, but — is it really? …When you just think about the number of brains that are sitting out there, we’re not getting them into the colleges to study the right things, to code, to do the work that we need to get done… We’ve got to figure out how to change the language to get more people involved in engineering.” Harwig echoed this sentiment later in the discussion, saying, “Everybody needs to kind of take ownership of this problem and then invite school children, have tours of their plants and facilities, and somehow get involved in schools and encourage STEM programs…[and] help teachers come create experiences for students to get involved, to get a skill.”
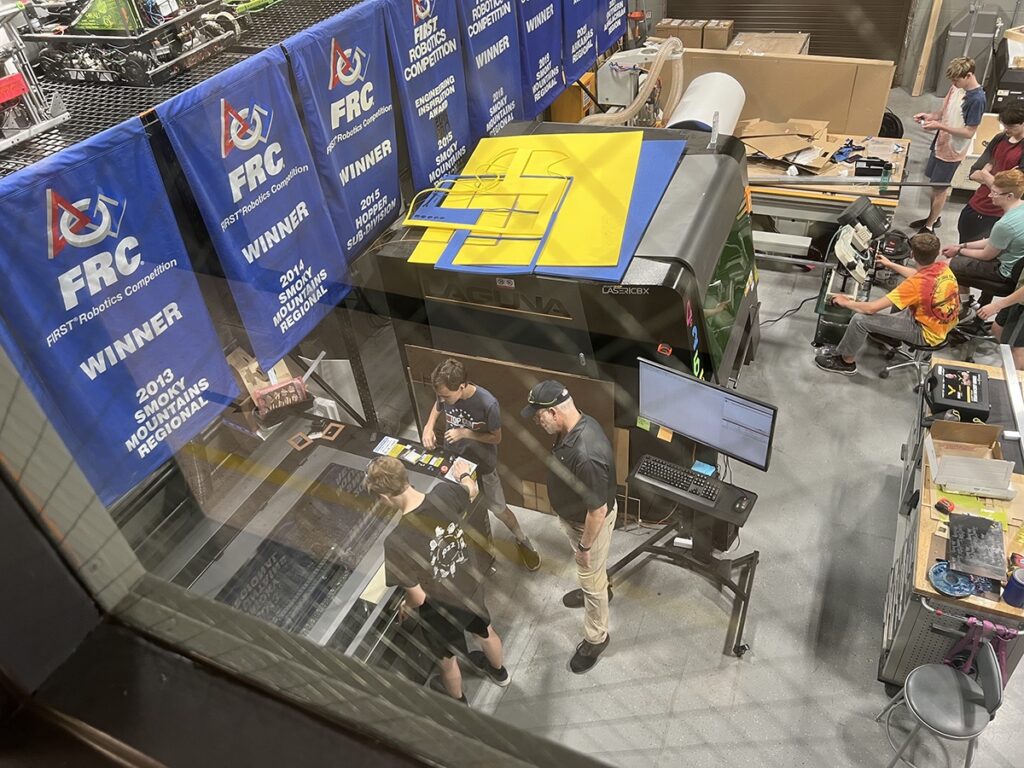
In his characteristically philosophical fashion, Camilleri diagnosed the issue as a cultural one:
“If a child [interested in manufacturing in the Anglosphere] takes all the advice they’re ever given, and they score incredibly well on tests, etc., what do they become? And the answer, according to our society, is they become a university professor. But we don’t actually need everyone to become a university professor. We need people to become all sorts of things… If you go into manufacturing in Germany, or in Japan, you get treated with respect. And we don’t do that here. Manufacturing is a ‘dirty’ job.”
Despite all the challenges, the tone wasn’t entirely pessimistic. I asked the panelists what types of things they were doing to draw more workers into the industry, and none of them were stumped by the question. They were all armed and ready with ideas on how to address the problem, and they’re all frequently in the process of implementing those ideas in practice. The most promising consensus solution was simply to reach out to students, at universities, in trade schools, high schools, local clubs, and the like. It’s slow work, but the only way that AM labor pool growth is going to accelerate is if more and more people in the industry get on board with similar efforts:
“We’ve had success speaking at universities and in hosting high school STEM programs,” said Gardner. “We’re outwardly communicating that we have a very specific company culture. We’re founded on integrity, we’re founded on kindness and respect to all people in the building. If you come to work, you’re going to work very hard, but you’re going to have a good day’s work. You’re going to get to appreciate the integrity of your own work, you get to build metal parts with your computer, and chances are you’re going to get to have a very active role in engineering functions that you’ll never get an opportunity for anywhere else on the planet.”
Barnes summed it all up succinctly:
“Kids think [this stuff] is cool. You show ‘em, ‘Hey, this is made out of titanium.’ It blows their mind… 3D printing’s cool. I mean, they don’t even think that it’s manufacturing. So, you know, maybe we change the language to match what we want as a result.”
How Far Is the Future?
So, the conference left me more convinced that large-scale metal AM is the sector’s future. The only question is, how far from now is that future?
You get the sense that if the individuals at LSAAT had their druthers, the future would be tomorrow. At the same time, everyone I talked to and listened to had no illusions about how much work is left to be done. They all seem to have one foot on either side of the frontier: eager for newcomers to join them on the side of efficiency, though anxious that the newcomers might not arrive quickly enough in sufficient numbers.
Optimistically, however, the problems are at least being correctly identified, and the solutions are constantly being refined, evermore quickly. To try to put things simply, the LSAAT conference currently occupies the third floor of the DCU. I wouldn’t be surprised if, by next year, it needs another floor. It is only a matter of time before it requires the whole building.
Featured image courtesy of LSAAT
Subscribe to Our Email Newsletter
Stay up-to-date on all the latest news from the 3D printing industry and receive information and offers from third party vendors.
Print Services
Upload your 3D Models and get them printed quickly and efficiently.
You May Also Like
Nikon SLM Solutions Sells SLM 500 to Primary Weapon Systems to Expand Suppressor Production
Primary Weapons Systems (PWS) is a Boise, Idaho-based manufacturer of suppressors, firearms, and related components. A subsidiary of Vigilant Gear and a sister company to aftermarket Glock slide manufacturer Lone...
3DPOD 261: Tooling and Cooling for AM with Jason Murphy, NXC MFG
Jason Murphy´s NXC MFG (Next Chapter Manufacturing) is not a generalist service; instead, the company specializes in making tooling. Using LPBF and binder jet, the company produces some of the...
HP and Firestorm Labs Form Partnership to Use Multi Jet Fusion 3D Printers in Deployable Factories
HP Inc., maker of a range of additive manufacturing (AM) solutions including the Multi Jet Fusion (MJF) ecosystem, has announced a partnership with Firestorm Labs, a developer of containerized, deployable...
3D Printing News Briefs, July 2, 2025: Copper Alloys, Defense Manufacturing, & More
We’re starting off with metals in today’s 3D Printing News Briefs, as Farsoon has unveiled a large-scale AM solution for copper alloys, and Meltio used its wire-laser metal solution to...