When we last caught up with Luke Rodgers, senior director of R&D at Jabil (NYSE: JBL), the manufacturing solutions provider was in the process of releasing a new material for powder bed fusion (PBF) that was derived from sequestered carbon monoxide. At RAPID + TCT 2023, the materials scientist was back with a new carbon-capturing polymer for PBF—this time, PLA.
The First PLA for PBF
Speaking to Rodgers at the tradeshow, we learned how this polymer, ubiquitous in material extrusion, introduces new benefits to the world of PBF. Developed in collaboration with NatureWorks, the world’s largest maker of PLA, Jabil’s PLA 3110P combines the printability of this typically corn-starch-based plastic with the high throughput and complexity enabled with PBF. Because Jabil is vertically integrated, it has everything from compounding to cryogenic grinding, allowing partners like NatureWorks to access all of these capabilities from a single supplier.
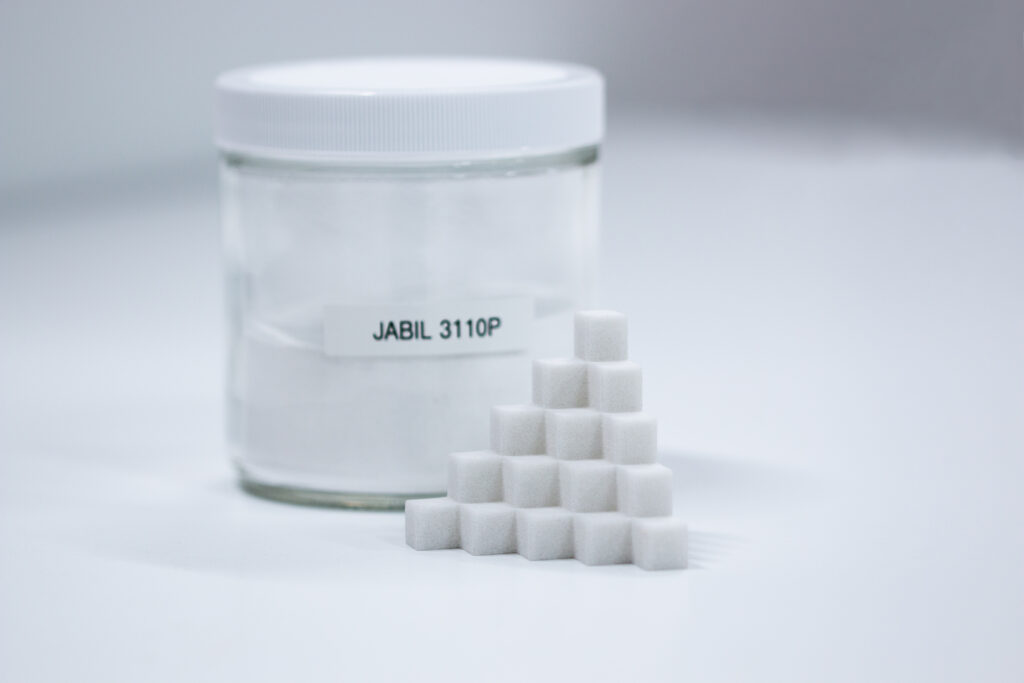
Jabil PLA 3110P, based on NatureWorks’ Ingeo™ PLA-based powder, offers 89% smaller carbon footprint compared to PA 12 when used in powder-bed fusion technologies. Image courtesy of Jabil.
“We’ve got a bunch of home compostable programs within the company that we’re looking at. And, overall, sustainability is a huge focus within Jabil,” Rodgers said. “We just have a lot of conversations with NatureWorks, and this came out about as a natural collaboration. We have all of the technologies and know-how to create PBF materials and they have all the expertise for making a good PLA resin system.”
At the jump, Jabil has several applications in mind for the material, including vacuum and thermoforming, casting, and as a more sustainable substitute for fossil fuel-based polymers. As for thermoforming, in which a material is heated and shaped around a mold, the material has the compression strength and temperature resistance ideal for manipulating materials like polycarbonate, PETG, and polypropylene.
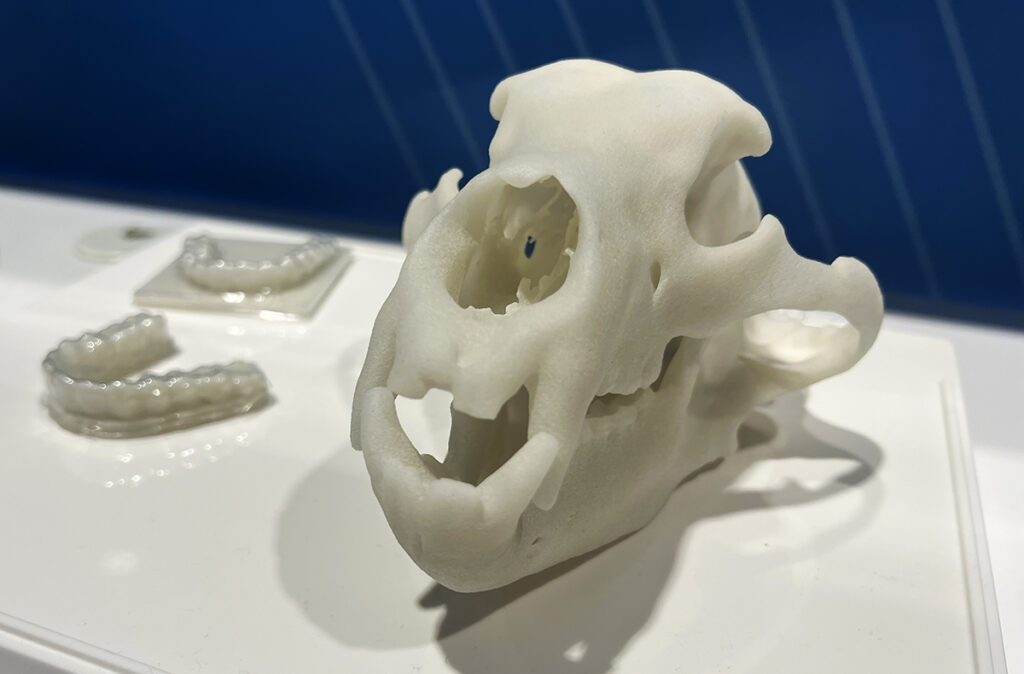
Captured at RAPID + TCT, this image shows a thermoformed dental aligner with 3D printed PLA mold alongside an educational model, also made from Jabil’s new material.
For metal casting, the PLA is able to melt without expanding or leaving very little residue. When printed with PBF, it also has the surface finish necessary for casting. There have been numerous stories in which desktop 3D printing users 3D print PLA models, wrapping them in a ceramic mold and burning out the models with molten metal. Unlike desktop material extrusion machines, PBF doesn’t suffer from obvious layer lines, thus resulting in smoother metal components.
Perhaps more importantly, PLA 3110P is also much more sustainable, with a carbon footprint that is 89 percent smaller than PA 12, according to NatureWorks. At the same time, it is comparatively inexpensive. This means that, when it comes to thermoforming, casting, or even printing models, prototypes, jigs, and fixtures, users now have a renewable alternative to petrochemicals. As companies seek to reduce their emissions, they can substitute their legacy materials with PLA.
“The entire industry is focusing more and more on sustainability. We’re doing our part by investing in technologies that introduce sustainability as an option for our customers. This PLA product is absolutely suitable for many of the thermoforming applications out there. If they’re currently performing thermoforming today, I hope they consider looking at a sustainable solution,” Rodgers said.
New Materials Partnerships
In addition to the new PLA, Jabil also announced a collaboration with Nexa3D in which its PK5000 material, the aforementioned polyketone (PK) derived from sequestered carbon monoxide, was made available for Nexa3D’s QLS 236 and QLS 820 SLS printers.
Along with that collaboration, Jabil was also involved in the development of a material that protects against electrostatic discharge (ESD). Created with Mechnano, the powder combines Jabil’s polyketone (PK) with Mechnano’s carbon nanotubes for use in PBF 3D printing. This allows for parts that can withstand functional testing and use in areas where ESD is an issue, such as in electronics manufacturing.
“Mechnano really likes the polyketone product because of its high elongation at break and high level of repeatability,” Rodgers said. “There are a lot of other companies out there that are just making polymers into powders and then calling them PBF products. And that’s not a product. We make sure that our powders can go into PBF. They make mechanically and dimensionally good parts.”

Line trimmer gas tank printed in Jabil’s PK 5000, an eco-friendly, powder-based additive material engineered to deliver improved strength, chemical resistance and resilience in comparison to general-purpose nylon materials, such as PA 12. Image courtesy of Jabil.
The manufacturing solutions provider is planning to continue its formulation of more sustainable polymers. Jesse Sumstad, Senior Product Manager at Jabil, put it this way during our interview:
“Our customers know that, the way that the market is right now, they’re not going to have everything in some sustainable alternative, but every little bit helps. It may be that one product fits this little need and save 10% in carbon emissions here, or they turn to our PK and save carbon emissions there. I don’t think that anyone is realistic in thinking that they can have everything 100 percent sustainable, but everyone is looking to get a little bit greener here and a little bit greener there.”
Rodgers concurred, adding, “Everyone has to just start their journey. You never get anywhere unless you start, so it’s the little steps that enable the ecosystem to evolve, to mature into something that’s really sustainable.”
Subscribe to Our Email Newsletter
Stay up-to-date on all the latest news from the 3D printing industry and receive information and offers from third party vendors.
Print Services
Upload your 3D Models and get them printed quickly and efficiently.
You May Also Like
Havaianas Collaborates with Zellerfeld to Launch 3D Printed Flip-Flops
The shoe of the summer is undoubtedly the flip-flop. Easy on, easy off, your feet won’t get sweaty because there’s not much material, and they’re available in a veritable rainbow...
UCLA Researchers Develop 3D Printed Pen that May Help Detect Parkinson’s Disease
Diagnosing Parkinson’s disease is difficult. Often, early symptoms of the progressive neurological condition may be overlooked, or mistaken for signs of aging. Early diagnosis can help save lives and improve...
Printing Money Episode 30: Q1 2025 Public 3D Printing Earnings Review with Troy Jensen, Cantor Fitzgerald
Printing Money is back with Episode 30, and it’s that quarterly time, so we are happy and thankful to welcome back Troy Jensen (Managing Director, Cantor Fitzgerald) to review the...
Heating Up: 3D Systems’ Scott Green Discusses 3D Printing’s Potential in the Data Center Industry
The relentless rise of NVIDIA, the steadily increasing pledges of major private and public investments in national infrastructure projects around the world, and the general cultural obsession with AI have...