Significant developments in materials science enable 3D printing companies to perfect their offerings by creating new and improved products that are stronger, more durable, and more versatile than ever before, allowing for the production of higher-quality and more complex 3D printed objects. At the forefront of these advancements are companies like Zortrax, Henkel, Essentium, Uniformity Labs, and Mechnano, who recently introduced new 3D printing materials at RAPID + TCT 2023, one of North America’s most influential additive manufacturing (AM) event held at McCormick Place in Chicago from May 2 to 4. So let’s delve into the details.
Leading adhesive technologies provider Henkel released a new industrial resin for production applications such as mold tooling and manufacturing aids. Called Loctite 3D IND249, this high-temperature, high-strength material was created to print challenging geometries with fine feature resolution. At the time of launch, Loctite 3D IND249 has several validated workflows on printers from Nexa3D, Rapid Shape, and Stratasys, with additional platforms to be onboarded in the near future.
Those attending RAPID + TCT can see the new material, which will be featured in Henkel’s booth (#1947) alongside its broader portfolio of photopolymer materials.
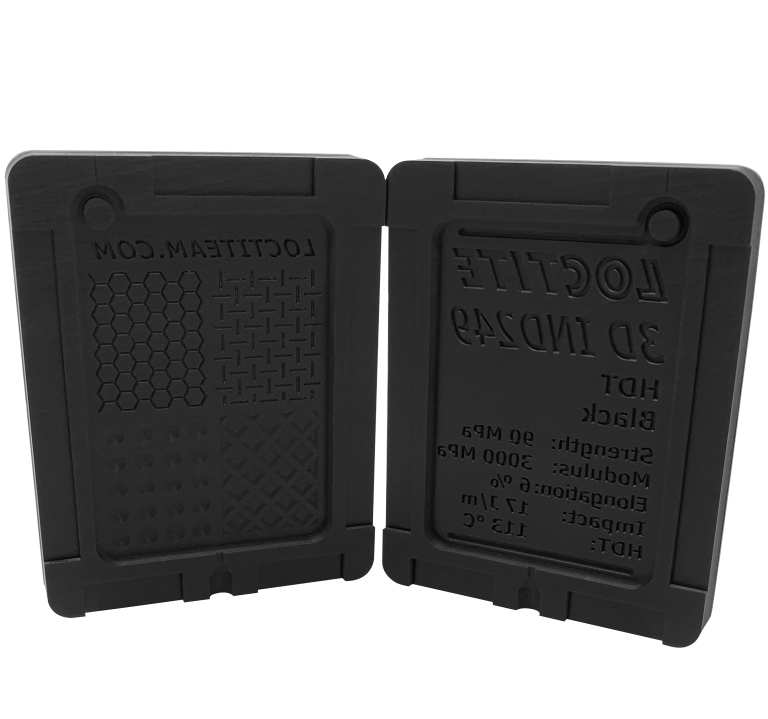
Mechnano showcased its first laser sintering powder PK ESD (electrostatic dissipative), which utilizes its proprietary D’Func technology. This newest offering to Mechnano’s growing portfolio of ESD material solutions for AM is based on Jabil’s high-performance photopolymer-engineered Jabil PK 5000 powder combined with a D’Func-based formulation to introduce ESD properties to laser-sintered parts.
“We are thrilled about this latest solution that leverages our D’Func technology in Laser Sintering materials,” says Mechnano President Bryce Keeler. “D’Func-enhanced powders will expand the AM market’s ability to respond to the growing need for quick-turn, static-dissipative, end-use parts that support an ever-increasing array of applications made more widely available as AM materials continue to advance.”
According to the company, PK ESD retains the unique advantages of Jabil PK 5000 to withstand functional testing and use. But thanks to D’Func, Mechnano says PK ESD is designed to prevent the build-up of static electricity and is suitable for use in applications where electrostatic discharge is a concern, such as in electronic manufacturing or other sensitive environments.
In other material news, a new low-temperature polycarbonate by Essentium will be ideal for 3D printing high-altitude applications, such as drones and drone bodies, outdoor housing, panel covers, electrical and transformer housings and covers, electrical line protections, and outdoor maintenance. In addition, the new product called Essentium Altitude is also ideal for use in cold outdoor environments in countries such as Norway and Alaska, thanks to its extreme cold resistance properties.
Designed for use on any open-source 3D printer, including the Essentium High-Speed Extrusion (HSE) 180 and HSE 280i 3D printing platforms, Essentium Altitude allows manufacturers to rapidly produce parts that can withstand cold temperatures on-demand, ultraviolet rays, and flames states the firm.
Engineered materials company Uniformity Labs launched UniFuse IN625 Nickel Alloy for laser powder bed fusion (L-PBF) printing. The company announced at RAPID + TCT the availability of its Inconel 625 powder and optimized parameters for L-PBF printing at 60um layer thickness with laser power at 400W. Uniformity’s powder is designed to provide more repeatable and reproducible mechanical properties across the build bed and was successfully used to produce a propulsion exhaust manifold.
Uniformity Founder and CEO Adam Hopkins said: “We continue to demonstrate outsized value to our customers, harmonizing AM materials and processes to deliver production-scale additive manufacturing. Our powders deliver repeatable mechanical properties and surface finish uniformly across the print bed, even when printing at throughputs that greatly exceed those possible with other materials. Our No Compromise approach to AM enables our customers to realize cost-effective serial production.”
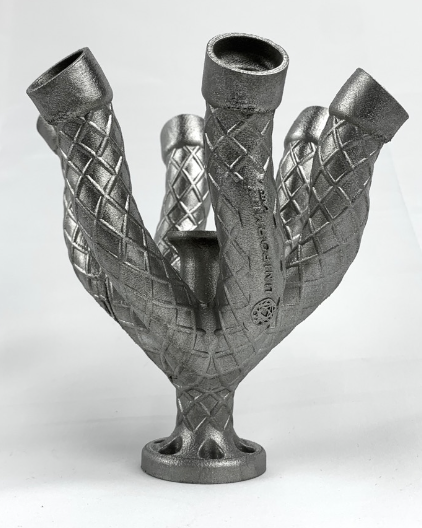
Finally, Polish 3D printer manufacturer Zortrax is introducing an industrial-grade, ceramic-filled 3D printing resin for its Zortrax Inkspire 2. Manufactured by BASF Forward AM, the BASF Ultracur3D® RG 3280 joins a broad range of photopolymers available for Zortrax Inkspire 2 UV LCD 3D printer. The material is characterized by its exceptional hardness, high stiffness, and excellent resistance to temperatures, reaching up to 536ºF (280ºC). It also has a stable particle dispersion and low viscosity, which makes it easy to handle and print.
Despite the high content of ceramic particles, the resin has low viscosity, and its sedimentation in the vat is limited, translating into maximized ease of use and print quality, highlights Artur Chendoszko, Zortrax Resin Technology Leader. According to the company, the parts 3D printed on Zortrax Inkspire 2, and post-processed on Zortrax Cleaning Station and Zortrax Curing Station, feature ceramic-like characteristics without the need to use special furnaces.
Initially announced in 2019, the partnership between Zortrax and BASF led to collaborations on developing and optimizing new materials for use with Zortrax’s 3D printers. Some examples include proprietary materials like Ultrafuse TPU 85A and Ultrafuse ABS Fusion+, designed to work seamlessly with Zortrax’s 3D printers.

The RAPID + TCT event is a powerful platform for 3D printing companies to unveil new materials and other innovations. Between 2016 and 2019, an average of 28 materials were introduced at the event each year. For example, in 2018, high-performance thermoplastics and advanced composites were among the over 30 new materials launched, while in 2019, more than 40 materials debuted. Introducing these new materials has expanded the capabilities of 3D printing technology, creating new possibilities for designers, engineers, and manufacturers.
Subscribe to Our Email Newsletter
Stay up-to-date on all the latest news from the 3D printing industry and receive information and offers from third party vendors.
Print Services
Upload your 3D Models and get them printed quickly and efficiently.
You May Also Like
The Market and Industry Potential of Multi-Material 3D and 4D Printing in Additive Electronics
Additive manufacturing leverages computer-based software to create components for products by depositing either dielectric or conductive materials, layer by layer, into different geometric shapes. Since its birth in the 1980s,...
3DPOD 262: Bio-inspired Design for AM with Dhruv Bhate, Arizona State University
Dhruv Bhate is an associate professor at Arizona State University. There, he looks at structures, materials, and design. Previously, he worked at PADT as well as in the semiconductor and...
3DPOD 261: Tooling and Cooling for AM with Jason Murphy, NXC MFG
Jason Murphy´s NXC MFG (Next Chapter Manufacturing) is not a generalist service; instead, the company specializes in making tooling. Using LPBF and binder jet, the company produces some of the...
3DPOD 260: John Hart on VulcanForms, MIT, Desktop Metal and More
John Hart is a Professor at MIT; he´s also the director of the Laboratory for Manufacturing and Productivity as well as the director of the Center for Advanced Production Technologies....