Starting with space news in today’s 3D Printing News Briefs, a Kansas City startup is building 3D printed re-entry capsules for on-demand cargo return from space. In research, a 3D printed biodegradable seed-robot, which can change shape in response to humidity, was created by researchers in Italy. Materialise completed its first materiality assessment and matrix, and Canadian Filaments and Oco created a new carbon captured filament. Finally, an MIT hardware startup with a focus on inclusivity launched a 3D printed device that allows people to control devices with their tongue, and Earfab’s custom in-ear products are live.
Raven Space Systems 3D Printing Re-Entry Capsules for Space Cargo
Kansas City startup Raven Space Systems is one of 14 companies chosen for a technical, business, and mentorship program from Amazon Web Services that will work to transform the future of space. Raven’s automated factory is building 3D printed re-entry capsules for on-demand cargo return from space for less money, at a faster pace, and with adaptability for missions, and the 2023 AWS Space Accelerator is helping it, and the other startups, speed up their growth and advance their solutions. Participants get AWS training, business development and strategy support, mentoring from AWS space domain and technical subject matter experts, and up to $100,000 in AWS Promotional Credit, as well as opportunities to work with AWS customers and AWS Partner Network (APN) Partners. Raven initially focused on material formulations to 3D print aerospace-grade thermoset composite materials at scale, but the co-founders realized that no one was improving the production of re-entry vehicles.
“We are developing large-scale 3D printing of structures as strong as aluminum at half the weight and heat shields with higher performance than the state-of-the-art. While developing this revolutionary innovation, we discovered a growing need in the space industry to increase the frequency and lower the cost of returning cargo from space,” said Raven Space Systems Co-Founder Blake Herren.
“We determined that 3D printing entire reentry capsules with our novel technology will enable us to build an automated factory to manufacture capsules 10-times faster at 95 percent lower cost with a software-driven approach enabling adaptability for any mission.”
3D Printed Biodegradable Shape-Changing Seed Robot
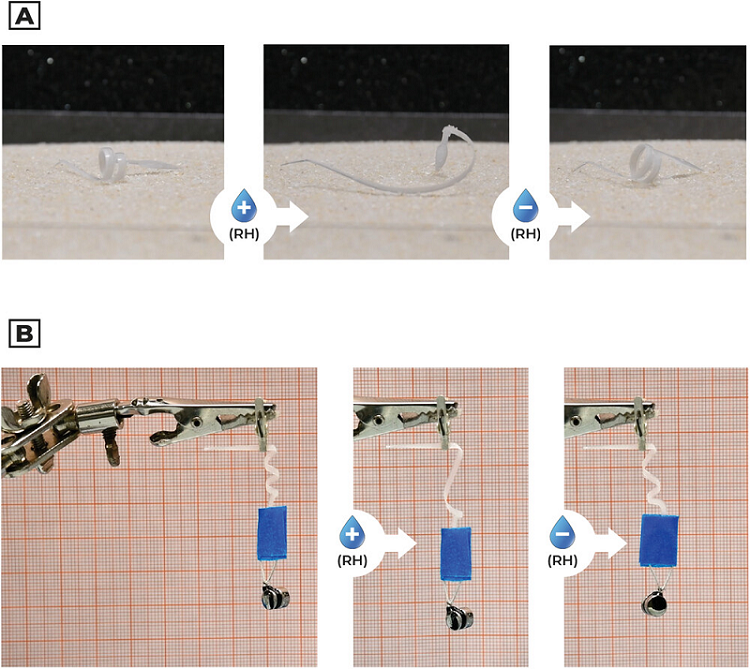
Lifting performances of the artificial seed-like robot. a) Example of the artificial seed self-lifting (Video S4, Supporting Information). b) From idle conditions (RH = 35%) the artificial seed is subjected to abrupt variation of humidity with water aerosol (RH = 90%). Water desorption is then promoted by environmental humidity.
Researchers from the Italian Institute of Technology (IIT) and the University of Trento were inspired by the seeds of the South African geranium, or Pelargonium appendiculatum, in their creation of the I-Seed, a biomimetic robot 3D printed out of biodegradable materials, in the shape of a seed, with the ability to change shape and autonomously explore the soil in response to changes in humidity, which makes it a 4D printed artificial seed prototype. The I-Seed project, funded by the EU and coordinated by IIT, is working to create robots that can be used as sensors to monitor soil quality parameters and air metrics. The group studied the movement and dispersal features of seed-carrying structures in these plants, and found that, under the right environmental conditions, the seeds detach and, “exploiting the hygroscopic properties” of the materials that compose them, change shape and move on their own to penetrate the soil. The seeds exploit dead cellulose-based tissues that have no metabolism and can deform through humidity changes, and after histological analysis of these tissues, the team was able to mimic the seed design through the use of 3D printing and electrospinning.
“These biodegradable and energy-autonomous robots will be used as wireless, battery-free tools for surface soil exploration and monitoring,” said Luca Cecchini, a PhD student at IIT in collaboration with the University of Trento and first author of the study. “This bioinspired approach has allowed us to create low-cost instruments that can be used to collect in-situ data with high spatial and temporal resolution, especially in remote areas where no monitoring data are available.”
Materialise Releases Materiality Assessment and Matrix
As a signatory of the UN Global Compact, Materialise has been annually reporting on its sustainability initiatives and progress since 2017, and says that sustainability is a major element of both its mission and shared vision to create a healthier, overall better world. But what’s new with its sustainability strategy is the completion of its first materiality assessment and matrix. In it, Materialise identifies six priority topics for sustainability: carbon footprint; material use efficiency and waste reduction; eco-design and innovation for sustainability; sustainable procurement; diversity and inclusion; and employee engagement and well-being.
“We’re always asking, ‘What can we do to make 3D printing more sustainable?’ By reducing the environmental impact of our operations, innovating continuously to advance 3D printing in a sustainable way, and empowering our customers to embed sustainability into their business models, we aim to drive positive outcomes for the environment, business, and society as a whole,” Materialise wrote on its website.
In addition to finishing its new materiality assessment and matrix, Materialise is also in the middle of developing a new sustainability dashboard, which should be published soon.
Canadian Companies Create Carbon Captured Filament for 3D Printing
Canadian Filaments, which manufactures high-quality 3D printer filaments, and fellow Canada-based company Oco, a climate ambassador that offers businesses the chance to upcycle collected Co2 material, have partnered to create a unique carbon captured filament for 3D printing. The two wanted to provide other AM companies with a more climate-friendly production material to help lower their carbon footprint, and the partners have also begun a take-back and recycle project, in which they will give 3D printing companies the chance to transform printed material back into reusable filament. Their new carbon captured filament has been released under the CUT product name, and is made from Co2 emissions and recycled graphite, processed through Oco’s CUT mechanism. The sustainable, engineering-grade PLA and PETG filaments feature high resilience and durability, and the first company to implement the material is Canadian company CleanO2, which will be 3D printing parts for its CarbinX device that captures carbon and transforms it into materials used to produce other products, like fertilizers, glass, and soap.
“We’re impressed by CUT PETG. It extrudes cleanly, and we are able to get consistently high resolution. In fact, we use it to produce finished components for our CarbinX units,” stated Jaeson Cardiff, CEO of CleanO2. “In some ways, it’s the ultimate circular economy story. We’re using captured carbon to produce carbon capture devices.”
Augmental’s Device for Hands-Free Computing Using the Tongue
Hardware startup Augmental, an MIT Media Lab spinoff, is pushing the limits of hands-free computing with its MouthPad^ device, which allows people to interact with and control their devices using only their tongue, which the startup considers “the 11th finger.” There are options for disabled people without the use of their hands to access the digital world, such as eye-tracking technology and lip-controlled joysticks, but the MouthPad^ is a far better option. This smart intraoral interface, customized to each user’s mouth, converts the user’s tongue position and pressure into cursor actions by processing signals through a machine learning algorithm and sending them via Bluetooth to the connected device. Plus, users can seamlessly switch between speech and tongue-driven screen navigation. Intraoral scanning is used to generate a 3D model of the user’s mouth, which helps to create a custom design that’s 3D printed using dental resin. The personalized MouthPad^ encapsulates a processing unit, Bluetooth radio, and flexible circuit board with sensors inside a watertight casing, allowing users to do everything from turning on the lights and sending an email to playing a video game. The goal is to scale up the device so it can be used by the broadest audience—not just disabled people, but also astronauts, surgeons, factory line workers, and more.
“Universal design has the power to greatly expand digital access for everyone, not just those lacking mobility,” explained Corten Singer, Co-Founder and engineer at Augmental. “In exploring hands-busy scenarios and contexts in which users have limited hand control, we have developed an in-mouth platform that enables convenient device interaction today, while also setting the stage for a future of more human and less distracting heads-up displays. Our technology should meet us where we are — not the other way around.”
Earfab’s Custom In-Ear Products Now Available to Order
Danish company Earfab has officially gone live with its custom in-ear products. The company offers custom products for traveling, sleeping, and hearing protection for activities like hunting, racing, industry work, and concerts. Earfab developed its earfabSCAN app and associated production technology, which are used to digitally create custom in-ear plugs. The process is quick and simple: first, purchase your preferred product, and you will then receive a unique QR code, along with instructions. Next, download the earfabSCAN app (products only work with iPhone x Series, 11 Series or 12 Series), and then scan your ears with your phone and complete your order. In less than ten days, you should receive your custom ear plugs, 3D printed out of biodegradable TPE resin.
“Earfab was launched in August 2020, and has developed earfabSCAN app and associated production technology. Today we offer a solution where the end customer can order their custom-made in-ear products regardless of location. We ship your custom-made in-ear products within 5 working days and deliver all over the world,” the website states.
“All earfab products are local manufactured, via an interconnected distributed manufacturing network, which bring down CO2 emissions.”
Subscribe to Our Email Newsletter
Stay up-to-date on all the latest news from the 3D printing industry and receive information and offers from third party vendors.
Print Services
Upload your 3D Models and get them printed quickly and efficiently.
You May Also Like
Consolidation in AM: How 2025 Is Shaping the Industry’s New Normal
The first half of 2025 has been marked by a clear shift in the additive manufacturing (AM) industry. Companies are no longer just focused on developing new tech by themselves....
Etsy Design Rule Change Reduces Selection of 3D Printed Goods
Online marketplace Etsy has implemented a rule change requiring all 3D printed goods on the site to be original designs. The update to the site’s Creativity Standards states, ¨Items produced using...
U.S. Congress Calls Out 3D Printing in Proposal for Commercial Reserve Manufacturing Network
Last week, the U.S. House of Representatives’ Appropriations Committee moved the FY 2026 defense bill forward to the House floor. Included in the legislation is a $131 million proposal for...
Transforming From Tourist to Native: Duro CEO Michael Corr Explains Why the Company Rebuilt its PLM Software on AI
In these early innings of the AI boom, many market analysts have expressed concern that AI spend has gotten too far ahead of the technology’s proven ability to deliver significant...