In the current phase of additive manufacturing (AM) industrialization, the sector is finding killer apps to see more widespread commercialization of the technology. The use cases being discovered are sometimes extremely niche, as evidenced by some of the startups invested in by AM Ventures. The German venture capital fund has contributed to firms whose work ranges from electric motors to heat exchangers.
Perhaps no company demonstrates this very focused view better than one firm within the AM Ventures’ portfolio, Vectoflow, a Germany company that specializes in 3D printed flow measurement systems. We spoke to Co-founder and Managing Partner Christian Haigermoser and learned how the segment Vectoflow has targeted has already proven to be a perfect sweet spot for the convergence of all of AM’s benefits.
Optimizing Flow Measurement with 3D Printing
It was while he was at GE that Haigermoser was first exposed to devices dedicated to measuring flow, but it wasn’t until he worked at BMW—where his co-founder, Managing Partner Katharina Kreitz, was completing her master’s thesis—that the two began laying the foundation for Vectoflow. The pair conceived of improving measurement tools with 3D printing so as to increase the accuracy robustness and flexibility of these probes in their various applications.
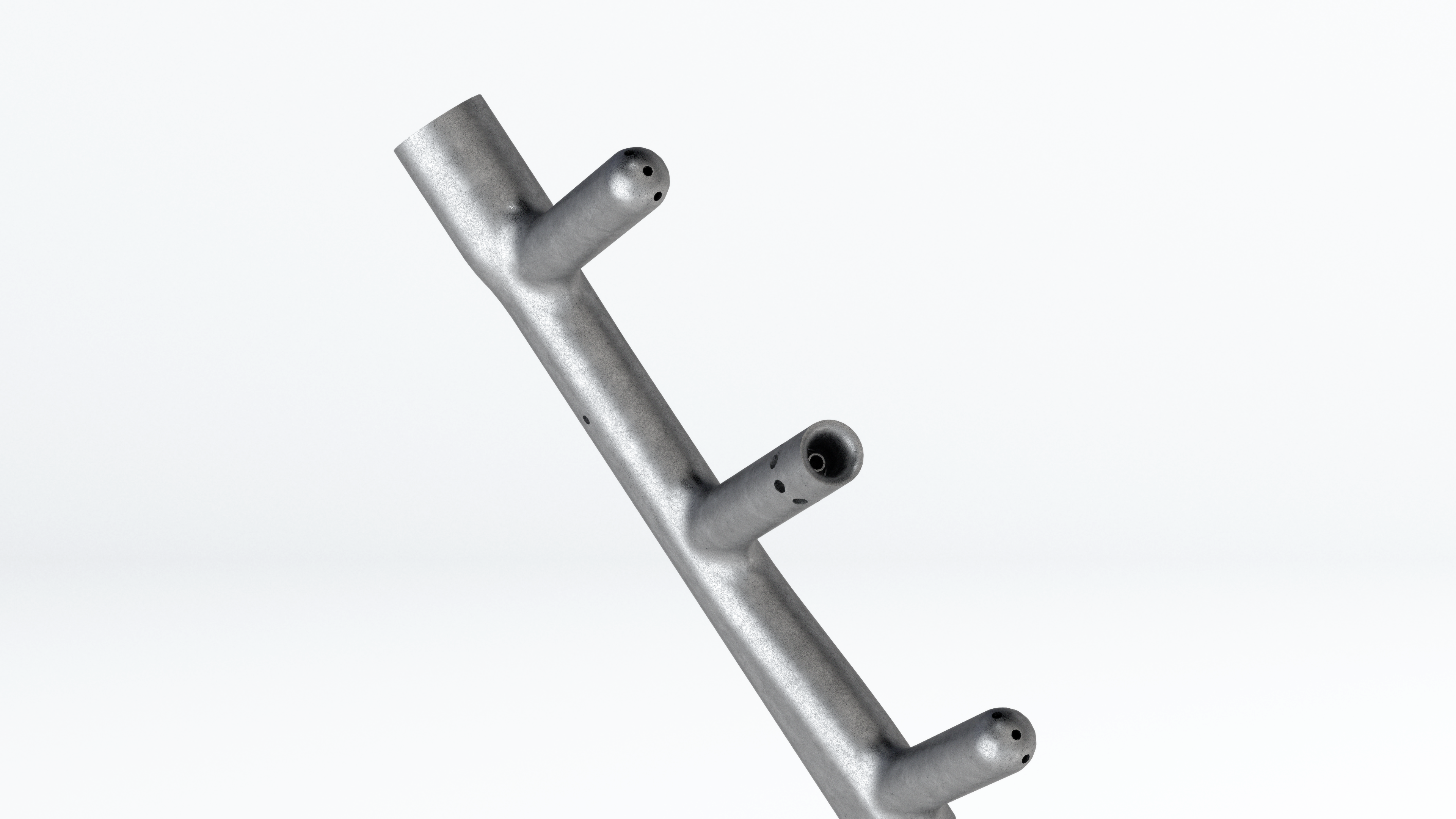
Multiple probes (multi-hole, static pressure, total pressure, temperature) combined into a single probe rake. Image courtesy of Vectoflow.
To start, available 3D printers weren’t capable of producing with the detail that the firm needed to manufacture their optimized probe designs. To achieve the necessary requirements for 3D printing such small objects, Vectoflow and its partner network had to tune an EOS machine to its exact specifications, also developing specialty post-processing steps for ensuring that powder is fully removed and that the probe pads are protected during finishing.
One partner, 3D MicroPrint, also enables the printing of probes that are even smaller than the 3mm probes made by traditional laser powder bed fusion systems. In September, however, Vectoflow will be purchasing an EOS machine tuned to obtain extremely good results, even without 3D MicroPrint. In-house production will both improve overall quality and decrease delivery time. As a result, Vectoflow is able to 3D print extremely small, finely featured parts that improve the way these measurement devices operate.
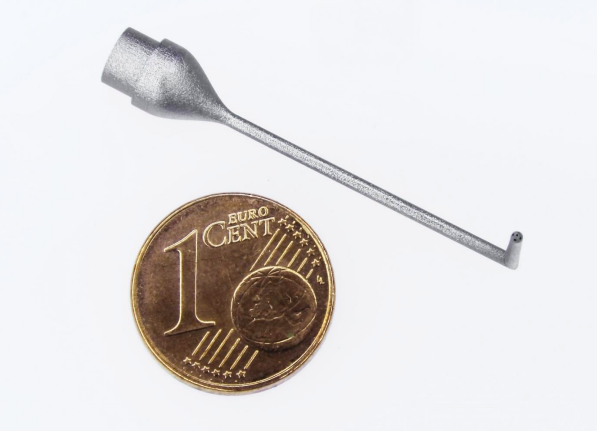
A probe 3D printed using 3D MicroPrint’s technology. Image courtesy of 3D MicroPrint.
One product offered by the firm features a 3D printed metal tip that measures just 3mm in diameter. Inside of that element are five channels which have 0.2 mm diameters. The tip is then connected to a pressure measurement tool, also developed in-house, to track the velocity and direction of air inside the compressor blade of a turbomachine.
Because of the fine details Vectoflow is able to achieve, the company is able to capture more accurate data, made that much more reliable because the probe is actually integrated into the final part—whether that be a compressor blade of a flight engine or the outer skin of a drone. In the automotive space, Vectoflow customers use these probes in wind tunnels to measure the drag of a car, while in other areas, they might be used to track the flow of cooling air within a system.
Continued Growth
Upon establishing Vectoflow in 2015, Kreitz and Haigermoser obtained their first two investors in 2016, building up a team of 17 people—all engineers with backgrounds in aerospace, electronics, and more. From the jump, Vectoflow has been striving for diversity and equity in its business operations, with management that is 50 percent male and 50 percent female and employees that hail from such widespread nations as Brazil, India, Nigeria, Spain, the U.S., and Germany.
To test its probes before they ship out, Vectoflow even has its own wind tunnel, where it is able to calibrate its probes in speeds of up to Mach 1.3. With demand so high, the startup is even in the process of establishing a second wind tunnel.
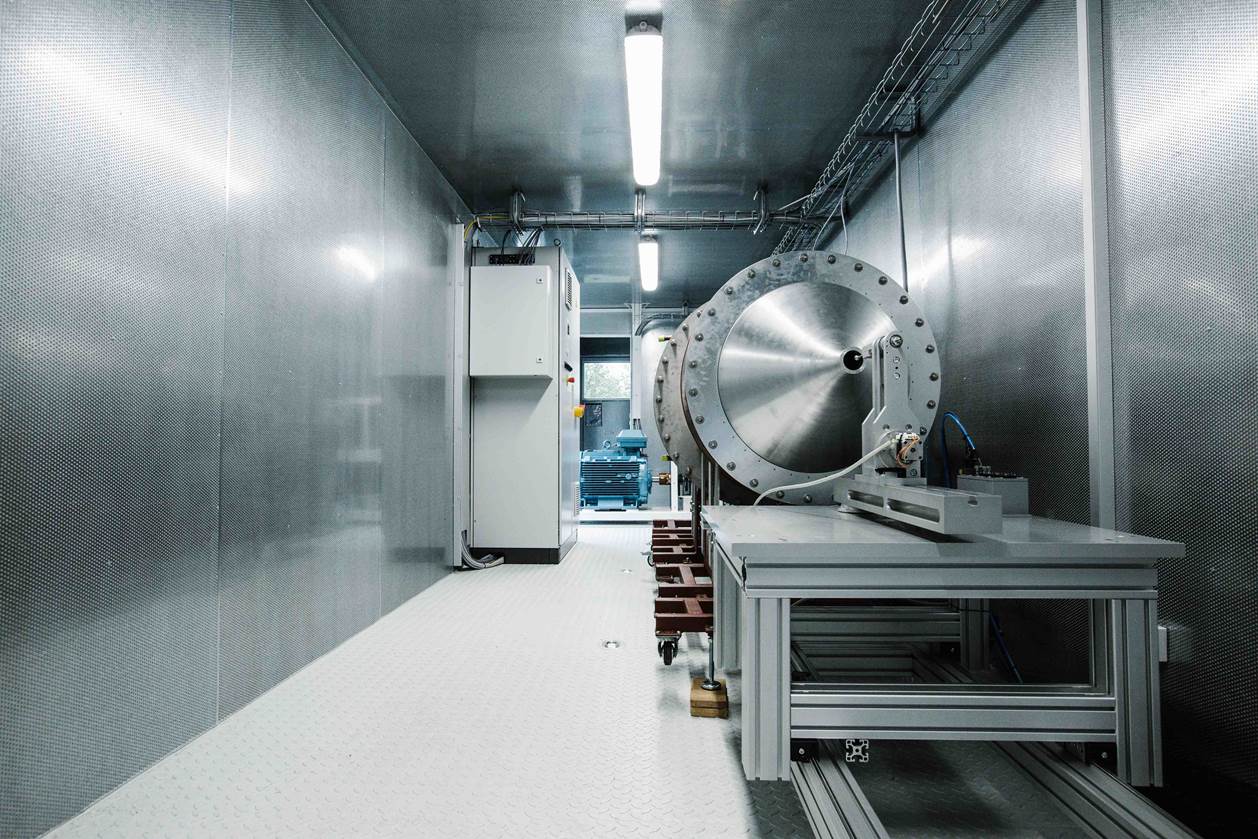
Vectoflow’s in-house wind tunnel for probe calibration. Image courtesy of Vectoflow.
“We now perform everything, including the engineering and design, the simulation, the building, post-processing, and testing of the probes. And then, we do the calibration in the wind tunnel,” Haigermoser said. “We also deliver the software.”
Key Markets to Probe
So far, Vectoflow has had some 300 customers from 70 countries and 80 research institutes, primarily in three verticals: automotive, industrial machinery, and aerospace. They include some of the biggest names in manufacturing, such as Siemens, Toyota, and Airbus. Though the lion’s share of Vectoflow probes are sold for testing purposes, the company is ultimately striving to become a serial supplier for in-operation applications.
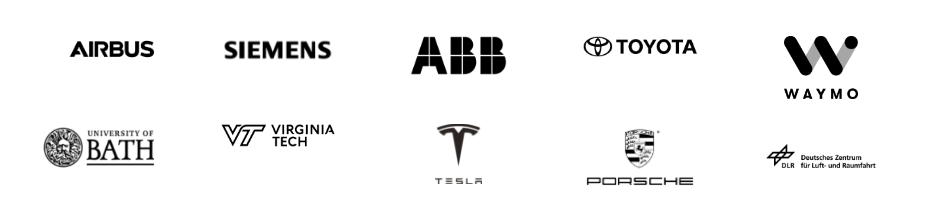
A selection of Vectoflow customers, as displayed on the company website.
After exploring a wide variety of measurements in wind tunnels, on cars and aircraft, inside and outside of jet engines, the company has narrowed its primary focus to two specific markets: aeronautics, particularly drones, and wind turbines. Haigermoser explained that the speed of an aircraft is not the same as ground speed. It has to account for wind speed and other variables that impact how it flies.
“When you operate a drone, like a delivery drone, you want to measure the flow velocity of that drone. Medium-sized drones would definitely need a rough measurement of the velocity, while bigger drones, like military drones, would need to measure more precisely the angle of attack, the flow towards the drone, the flight altitude and speed,” Haigermoser said. “Every aircraft has such sensors on it. And we provide two solutions with our low-cost and high-end module.”

The e-Genius-Mod drone, powered by a purely electrically operated wing tip propulsion system, and equipped with the Vectoflow VectoDAQ Air Data System. Image courtesy of University of Stuttgart.
Naturally, variables related to wind are crucial to turbines. With precise probes, Vectoflow aims to optimize these energy-generating systems by measuring turbine misalignment.
“What you want is for the wind direction to align completely with the axis of the wind turbine, because if it doesn’t, you lose efficiency. That’s a big problem in the wind turbine business and it is something we want to solve with our measurement technology,” Haigermoser said.
Alexander Schmoeckel, Associate at AM Ventures, sees these verticals as primed for the implementation of 3D printed probes, saying, “We have great confidence in the future success of Vectoflow’s probes, which we expect to soar to new heights with their highly cost-effective and minimally data-reliant solution. Their innovation will speed up the use of unmanned air transportation, making it more accessible, efficient, and enable the measurement of what was once considered immeasurable. In addition, Vectoflow’s cutting-edge technology has huge potential in the wind energy market. Their high-performance system can optimize clean energy production and enhance wind turbine operation. With such a revolutionary technology in place, Vectoflow is well-positioned to lead the path to high-volume manufacturing of probes for drones and wind turbines.”
Probes: An Ideal Use Case for 3D Printing
Not only has additive proven to be the ideal technology for producing Vectoflow probes, but Vectoflow probes have proven to be an ideal use case for 3D printing. Because of the size of the products, large numbers of parts can be printed in a single job. In turn, the price point of the products is sufficiently low where it might not be for other items.
“The really nice thing about our products is that we can use additive on one side to produce very customized, complex parts, but, on the other side, the probes we produce for serial applications can also be produced with a 3D printer in sufficiently high numbers for a very reasonable cost. This allows us to produce both customized but also single products. And that’s really the strength we have,” Haigermoser explained.
At the moment, about 80 percent of the probes made by the company custom, while 20 percent are standard, but Haigermoser believes those numbers will be flipped as Vectoflow grows. Given the sweet spot that the Vectoflow team has discovered with 3D printing, it makes perfect sense that AM Ventures chose to invest in the firm. Alois Hotter, Senior Associate for the venture capital fund, explained:
“Vectoflow is an outstanding example of how additive manufacturing can be used to build highly scalable and reliable flow measurement technology. The founders, Katharina Kreitz and Dr. Christian Haigermoser, recognized the shortcomings of traditional probes that broke easily and confidently concluded that 3D printing was the best solution for optimizing fluid-dynamic metrology devices. Their impressive educational background in fluid dynamics and engineering provided them with the expertise to create a revolutionary solution, which has quickly propelled Vectoflow to become a rapidly growing company. We take immense pride in having supported Vectoflow from its early developmental stages.”
Vectoflow products are currently sold both directly, mostly local to Germany, and through distributors around the world. However, the company is growing quickly, which led to a recently established U.S. subsidiary. With the majority of Vectoflow customers located in the U.S., the company plans to perform production, calibration, development, and other key activities in the nation, as well.
AM Ventures is the Networking Sponsor for the Bavarian Beer & Pretzels Networking Reception at the Additive Manufacturing Strategies business summit on February 6-8, 2024.
Subscribe to Our Email Newsletter
Stay up-to-date on all the latest news from the 3D printing industry and receive information and offers from third party vendors.
Print Services
Upload your 3D Models and get them printed quickly and efficiently.
You May Also Like
3D Printing News Briefs, July 2, 2025: Copper Alloys, Defense Manufacturing, & More
We’re starting off with metals in today’s 3D Printing News Briefs, as Farsoon has unveiled a large-scale AM solution for copper alloys, and Meltio used its wire-laser metal solution to...
3DPOD 260: John Hart on VulcanForms, MIT, Desktop Metal and More
John Hart is a Professor at MIT; he´s also the director of the Laboratory for Manufacturing and Productivity as well as the director of the Center for Advanced Production Technologies....
3D Printing News Briefs, June 28, 2025: Defense Accelerator, Surgical Models, & More
In this weekend’s 3D Printing News Briefs, 3YOURMIND was selected to join an EU Defense Accelerator, and PTC has announced model-based definition (MBD) capabilities within Onshape. Finally, a study out...
EOS in India: AM’s Rising Star
EOS is doubling down on India. With a growing base of aerospace startups, new government policies, and a massive engineering workforce, India is quickly becoming one of the most important...