Metal printing in 3D has been, and for the most part still is, the bailiwick of brilliant technicians working with the bleeding edge in technology, devices, and materials.
We’re talking actual rocket science stuff here; aerospace stuff, additive manufacturing.
But a few academics and garage-bound inventors are trying to take on the problem of 3D printing with metals on their own terms, and on budgets that make sense for hobbyists and makers, while startups like MatterFab are confronting the problem as well.
The mountain they have to climb on the way is enormous. Limited material options, hugely expensive equipment, and brutal production costs mean artists, small and medium-sized enterprises, and mechanics are on the outs when it comes to using 3D printing to prototype and manufacture their dream objects. Most of the home-based solutions to metal 3D printing have been limited by the fact that this technology requires access to pricey cutting tools needed to remove the resulting parts from the metal substrate on which they’re built.
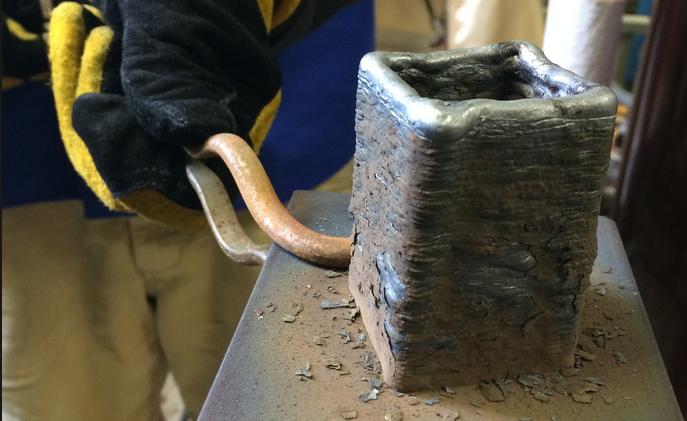
Image courtesy of Fred Carter, Mechanical Engineering PhD student at Lehigh University
But a professor in the Departments of Material Science and Engineering and Electrical and Material Engineering at Michigan Technological University in northern Michigan, Joshua M. Pearce, built a low-cost, open-source 3D metal printer which utilizes gas metal arc welding technology to change the game for the average consumer.
Now Pearce and a team of researchers have written up the findings of an investigation they made into several substrate treatments which may represent a low-cost method to remove 3D printed 1100 aluminum parts from a reusable substrate.
It involves the use of coatings of aluminum oxide and boron nitride. The method has been tested on 1100 aluminum, and A36 low-carbon steel substrates, and the team did “lap shear tests” to assess the interlayer adhesion between the printed metal part and the print substrate.
Their method may well have found breakthrough-level success as the parts they created during their testing didn’t warp the substrate and allowed them to easily remove parts without using additional coating or cutting steps.
The first substrate release mechanism, a control group, examined the adhesion strength between commercially pure aluminum printed on commercially pure aluminum. In this instance, good joining between the printed and substrate materials was observed. This result was expected because no compounds or coatings were applied to prevent adhesion.
Pearce says he found a method of weakening the bond seen in the control group, and it works because “intermetallic phases” form between solid metals which have a crystal structure different from each individual solid solution phase. He says that while manufacturers suppress the formation of aluminum–iron intermetallic compounds to avoid creating brittle compounds, the formation of the intermetallics worked like a charm to form a “brittle interface” between the printed part and the substrate in his examples. It’s this brittle interface which allowed aluminum samples to be removed from the low-carbon steel substrate with little more than a few taps from a hammer and chisel.
According to Pearce and his team, a mass of aluminum will diffuse heat more quickly than the same mass of steel due to the higher thermal conductivity of aluminum, and aluminum also has a higher heat capacity allowing it to store more thermal energy before reaching temperatures yielding weld penetration in steel.
He adds that a third substrate release mechanism, sacrificial aluminum oxide, and boron nitride coatings, have shown promise as well. Pearce says the application of boron nitride coatings to a print substrate cuts back on adhesion between 3D printed metallic parts and metallic substrates, allowing the parts to be removed with relative ease.
And the best news of all? The aluminum oxide and boron nitride coatings the researchers used can be scraped, sanded, or simply washed off with water to prepare the printer’s substrate surface for reuse, and you don’t get that when 3D printing with laser melting and laser welding of metals.
Working with Pearce on the research project were Amberlee S. Haselhuhn, Eli J. Gooding, Alexandra G. Glover, Gerald C. Anzalone, Bas Wijnen, and Paul G. Sanders, co-authors of the findings. If you wish to read the full details of the technique, you can read the paper the team wrote on their work, Substrate Release Mechanisms for Gas Metal Arc Weld 3D Aluminum Metal Printing, here.
Do you think 3D printing with metals will ever reach a level of development where it’s accessible to hobbyists, artists, and mechanics? Please offer your take in the DIY Metal 3D Printing forum thread on 3DPB.com.
[Image Source: Fred Carter and Lehigh University]Subscribe to Our Email Newsletter
Stay up-to-date on all the latest news from the 3D printing industry and receive information and offers from third party vendors.
Print Services
Upload your 3D Models and get them printed quickly and efficiently.
You May Also Like
The Market and Industry Potential of Multi-Material 3D and 4D Printing in Additive Electronics
Additive manufacturing leverages computer-based software to create components for products by depositing either dielectric or conductive materials, layer by layer, into different geometric shapes. Since its birth in the 1980s,...
3DPOD 262: Bio-inspired Design for AM with Dhruv Bhate, Arizona State University
Dhruv Bhate is an associate professor at Arizona State University. There, he looks at structures, materials, and design. Previously, he worked at PADT as well as in the semiconductor and...
3DPOD 261: Tooling and Cooling for AM with Jason Murphy, NXC MFG
Jason Murphy´s NXC MFG (Next Chapter Manufacturing) is not a generalist service; instead, the company specializes in making tooling. Using LPBF and binder jet, the company produces some of the...
3DPOD 260: John Hart on VulcanForms, MIT, Desktop Metal and More
John Hart is a Professor at MIT; he´s also the director of the Laboratory for Manufacturing and Productivity as well as the director of the Center for Advanced Production Technologies....