At Additive Manufacturing Strategies 2023, 3DPrint.com had the chance to sit down with Harshil Goel, CEO and founder of Seattle-based Dyndrite. Named one of the Forbes 30 under 30 in 2020, Goel presented at the event on the topic of Software and Automation. His scale-up is an interesting one for a number of reasons, not the least of which is the fact that its core technology is difficult to encapsulate. It’s exactly this difficulty that symbolizes how potentially game changing Dyndrite is to the additive manufacturing (AM) industry.
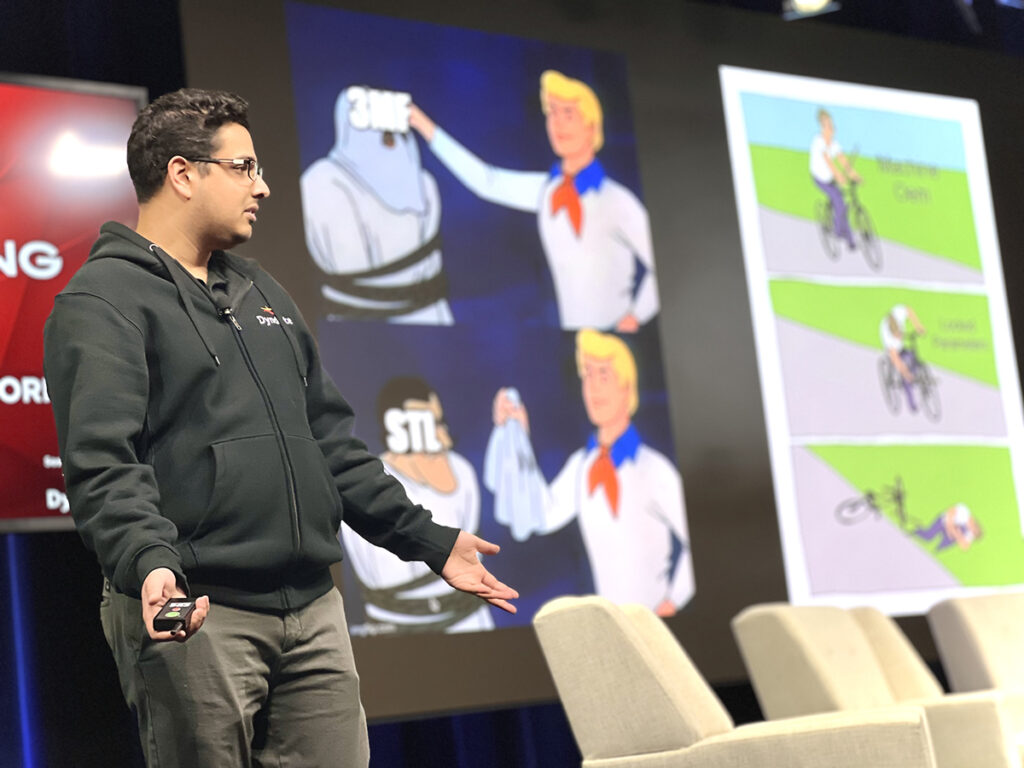
With a background in mathematics and mechanical engineering, Goel entered the 3D printing space only to find the state of software to be extremely lacking—not necessarily from the design side of the equation, but even at the point of transferring data from a computer to the machine itself. Not only was the process slow, but it didn’t offer a great deal of control or freedom over how the machine operated. Meanwhile, very qualified engineers were wasting time performing monotonous tasks like putting tensile specimens on a build plate or putting serial numbers on parts.
“While I was doing my research, I had this insight that we’re at this kind of weird point where the manufacturing hardware had actually surpassed the software. Meaning the machines were fantastic. They’re repeatable. They could do all kinds of cool stuff, but no one could actually send the data to the machine to actually make use of it,” Goel said. “And, well, whenever you start a company and you realize that the software is behind the hardware, it’s really a really good opportunity to go make a bunch of money.”
Dyndrite was formed at a time when the industry was just shifting from prototyping to production. As a result, original equipment manufacturers (OEMs) didn’t have software set up for managing multiple machines, let alone batches of parts.
“An easy way to immediately detect that the machine maker wasn’t making software for any production capacity was, if you look at it, the majority of machine makers do not have software that allows you to put a serial number on a part. If you talk to any engineer on the planet, a red flag will go off because, if it’s a production part it is traceable and needs a serial number,” Goel said. “So, there were all of these weird little things that we realized and we said, ‘Okay, we’re gonna go fix this.’”
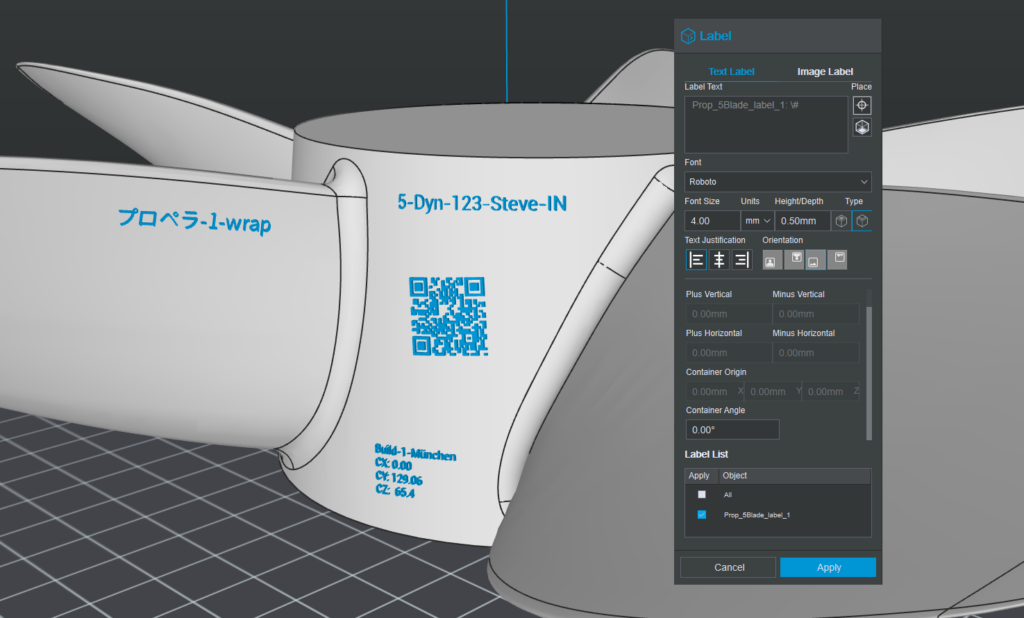
The first step was the development of the Dyndrite Accelerated Computation Engine (ACE). Not quite an operating system (OS), nor a manufacturing execution system (MES), the Dyndrite ACE is a GPU-driven geometry engine that drives tools like these. The ACE processes large-scale 3D models and complex geometries, in turn increasing the speed and efficiency of AM systems.
To start, the company built a user interface (UI) development environment atop the engine that enabled its customers, including large companies like HP, as well as emerging companies such as Impossible Objects, Azul3D, and Meteor to leverage Dyndrite so that they can focus on developing their unique IP and unlocking what makes their machine special rather than reinventing the wheel to drive it themselves.
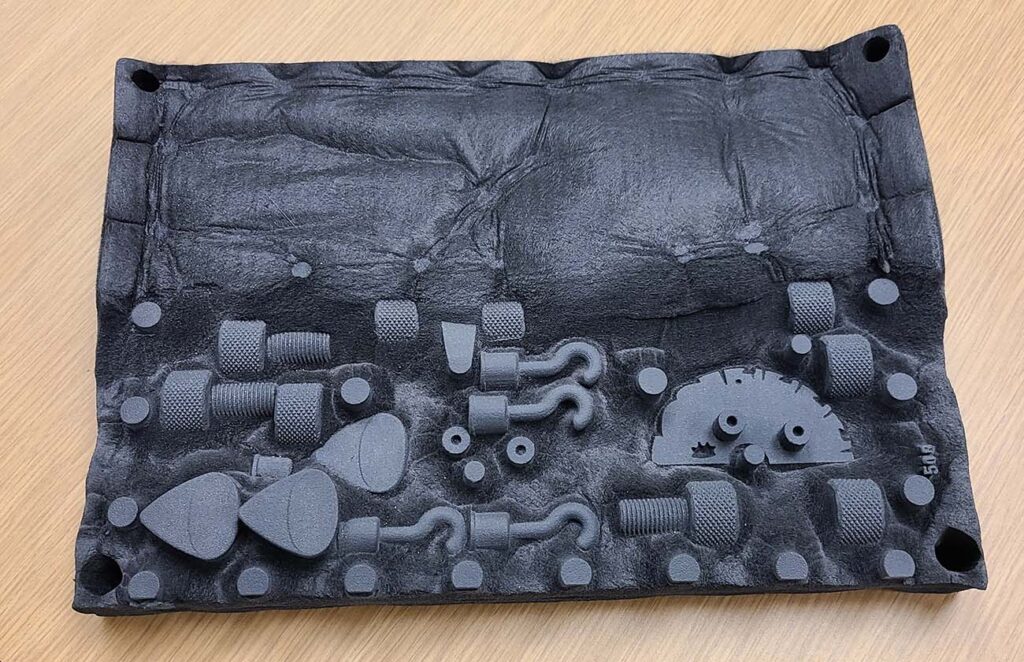

As Dyndrite adoption progressed, users began requesting specific functions be added to the UI. To address this, the firm created the Dyndrite App Development Kit (ADK), that would give OEMs the ability to create their own features for the software using a user-friendly, drag-and-drop UI that can be connected to the Dyndrite engine in a low-code or no-code manner. This can all be done with developers embedding their own IP into the software in a way that neither Dyndrite nor users can access.
Dyndrite has also begun using the ADK to develop its own suite of software tools, beginning with an app called Materials and Process Development for Laser Powder Bed Fusion (LPBF). From the sound of it, the program is impressive, while also highlighting just how far behind LPBF manufacturers have been lagging in printer control.

With the ability to bring in native CAD data, the tool enables sophisticated materials and process development including the ability to perform “volumetric segmentation,” in which a part is automatically divided into pieces with 256 different parameter sets per part. For instance, the laser speed and power can be varied throughout the component, with thin areas being printed one way and thick parts another. If the build includes multiple items, each of those gets its own collection of 256 parameters. According to Goel, one customer has dialed in over 100 parameters per part and has achieved “the best microstructure they’ve ever gotten.”
According to Sam Miller, Director of AM Software, at an automotive customer, “Dyndrite toolpathing unlocked a new dimension of flexibility for our additive manufacturing processes. The additional control over our SLM machines enables us to achieve better material performance and cost productivity in a high-quality manufacturing environment.”
Because every LPBF machine is unique in its own way, Dyndrite also designed the app such that it’s possible to ensure that every printer in a fleet is able to create the same component with repeatable quality, and traceability, in an automated manner. In this way, the user grows with the software, from printing a part on one machine to optimizing the parameters for it and obtaining repeatability across multiple printers. As they get more advanced in their adoption of the technology, they can begin taking advantage of different capabilities within the tool. For instance, one might color a CAD surface and set it up so that the software recognizes all of the green surfaces and automatically puts serial numbers on them or adds ribbon support structures to them.
Dyndrite’s LPBF product works with all the leading metal machine OEMS, including SLM, EOS, Renishaw and other “open” systems. The company currently offers an early adopter program for LPBF users interested in materials and process development.
All of this paints a picture of a company that differentiates itself significantly from the rest of the software developers in the AM industry in a variety of ways. Rather than develop and sell software modules based on specific tools, Dyndrite has created a powerful development engine on which those tools can run. To showcase just what’s possible with such an engine, the Materials and Process Development for LPBF app gives LPBF users a toolbox for vastly improving the efficiency and capabilities of their machines, including the ability to expand available materials, speed build rates, print more intricate geometry such as fins and small features, controls for improving part quality and ensuring material homogeneity, and surface roughness, while maximizing flexibility for determining areas such as support or support-free requirements.
With the Dyndrite App Development Kit, OEMs can determine new, unique ways for leveraging their equipment in ways previously impossible. As a new company with growing adoption, the possibilities Dyndrite has introduced to the AM market are only now beginning to be understood. However, as users fully grasp what they can achieve by taking advantage of a powerful engine, the technology is only going to become more complex. As a result, more tools will need to be created to adequately be able to take advantage of the geometry kernel, including artificial intelligence. Goel put it this way:
“Our tool is as dumb as the person who uses it. What’s the purpose of automation and AI in this industry? It’s to not to create lights-out factories or anything like that in the short term. It’s to aid in the search for the right thing to do. What Dyndrite has built, complements artificial intelligence as AI needs a query and execution system like Dyndrite in order to succeed in industrial applications. AI needs tools for geometry creation, transformation and transmission. Dyndrite ACE provides that. What Dyndrite has created is a major problem. We’ve created the problem of optionality and we’ve created so many options now that AI has to be smart enough to go figure out what to do with it all.”
Subscribe to Our Email Newsletter
Stay up-to-date on all the latest news from the 3D printing industry and receive information and offers from third party vendors.
Print Services
Upload your 3D Models and get them printed quickly and efficiently.
You May Also Like
The Dental Additive Manufacturing Market Could Nearly Double by 2033, According to AM Research
According to an AM Research report from 2024, the medical device industry, specifically in dentistry, prosthetics, and audiology, is expected to see significant growth as these segments continue to benefit from...
Heating Up: 3D Systems’ Scott Green Discusses 3D Printing’s Potential in the Data Center Industry
The relentless rise of NVIDIA, the steadily increasing pledges of major private and public investments in national infrastructure projects around the world, and the general cultural obsession with AI have...
AM Research Webinar Explores Continuum’s Sustainable Metal Additive Manufacturing Powders
Metal additive manufacturing (AM) powder supplier Continuum Powders is working to develop solutions that empower industries to reduce waste and optimize their resources. An independent life cycle assessment (LCA) of...
3D Printed Footwear Startup Koobz Lands $7.2M in Seed Round
California-based Koobz is focused on reshoring the U.S. footwear supply chain with advanced manufacturing processes, including 3D printing. The startup just announced that it has added $6 million to its...