When we think of mass customization and 3D printing, we often think of personalizing an object’s shape. Shape alone, however, doesn’t often make a good business case. Frequently, additive manufacturing (AM) is simply too expensive. And a manufacturer can usually use alternative technologies that are less expensive, including CNC, laser cutting, and water jetting.
If AM is the only technology that can make that shape or if the item is small enough, then it may make sense to 3D print it. This is true for hearing aids, bridges, and crowns, where the small mass of the customized objects is one of the factors that makes 3D printing attractive. The ability to enable certain physical properties is another area where 3D printing has a decided advantage. For example, unique textures and internal lattice structures aid in osseointegration and the reduction of stress-shearing in orthopedic implants.
However, the ultimate dream of 3D Printing is much deeper still.
Voxel Level Manufacturing
Image: Wikipedia.
Ultimately we’d like to 3D print individual voxels, each with different properties. How we do so doesn’t matter much at the theoretical level. We’d have 3D pixels (i.e., voxels) of determined sizes with different sets of properties that could be mixed at different ratios. We’d then jet (or sinter or extrude) the right voxel exactly at the right location, enabling gradient parts. We could make items softer at some points and harder at others. Something could be more or less rigid at various locations throughout the structure. We could then build complete devices, electronics, magnets, and everything (Neil Gershenfeld has been working on this in various forms for years now). Obvious are the advantages to the complete assembly of most objects up to the wall thickness of a voxel, as opposed to making only certain items 1mm thin and with a limited geometry (what we do now).
Factory in a Tool
Making electronics and printing the casing in a single process could bring very decided advantages. nScrypt´s Factory in a Tool approach is one of the few currently showcasing the advantages of extrusion, pick and place, milling and more in one printer. Their machines are now being used to make almost an entire nanosat inside a single printer. It is easy to see how any 3D printing set up could combine aerosol jet, CNC, extrusion, and many other different tools to make very complex and complicated objects.
Right now, members of the AM industry are all thinking very much inside of their technology silos. However, a more open approach would see more people look at blending many tools inside one machine. This device could then also be a clean room in itself and take care of every step from packaging to product. Albeit, the factory in a tool approach is not the only one.
Pellet Mixing
Imagine a material extrusion system that intelligently combines different proportions of pellets on the fly. It can then print them into different cell like infill structures. The walls, shapes and overall variation of these structures would be dynamically programmed according to part properties. Some cells would be filled with air, while others would be completely packed with material. Infill patterns wouldn’t just be different at different layers but vary throughout, resulting in structures with programmed rigidity, softness, and other properties at specific locations. Either via infill design or pellet, mixing different properties can be assigned to different voxels, offering a high degree of variability.
Other Variants
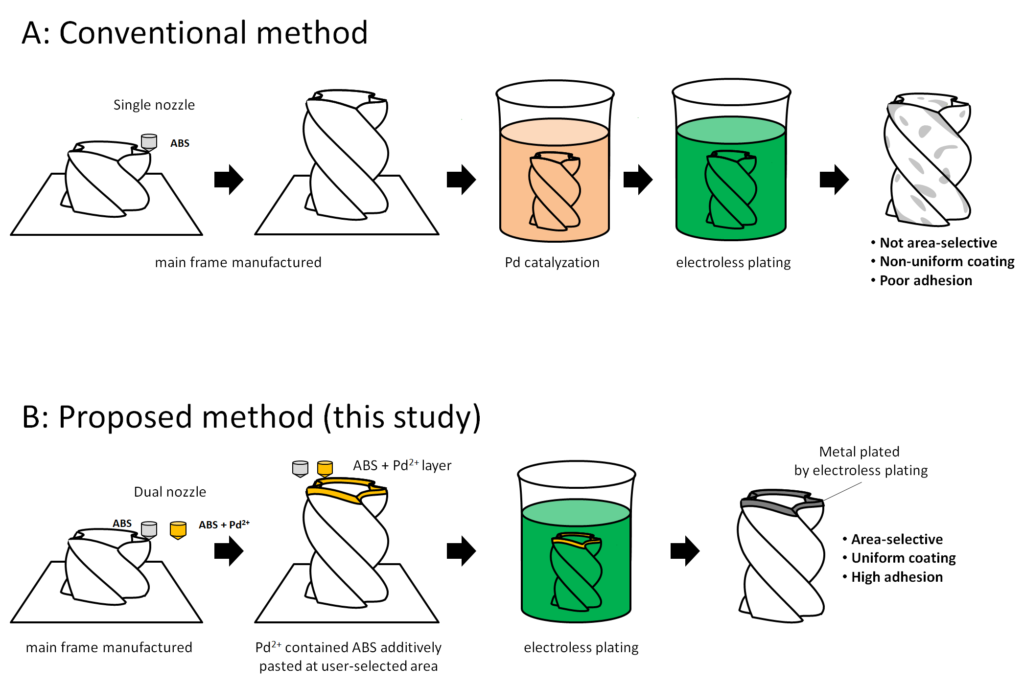
Of course, with material jetting, we could selectively deposit materials of different properties at the same time. This could allow one to deposit billions of droplets with varying characteristics quickly and precisely. Gradient properties and parts with many different materials and qualities could result from this process.
Rize‘s technology, which united material extrusion and inkjet, is also another way to achieve this. A process similar to that of Aerosint could also work. A selective metallization process that combines extrusion and vacuum forming may be used as well, as could the Waseda’s method for multi-material DLP or CalTech’s hydrogel infusion technology with carbonization. Super accurate drop-on-demand could be another inkjet path, as could be a variant on electro spinning At the nano level, companies like UpNano, BMF and Femtoprint are performing exciting frontier work also. Atlant3D´s atom-by-atom manufacturing may well be the ultimate technology for this. So, the above examples are just some to illustrate that there are several technology routes that could all lead to accurate, voxel-level manufacturing.
Where is this Frontier?
Obviously, if we get one of these processes up and running in an industrial setting, it would open up a considerable amount of applications. However, it is a mistake to look at this as some far-off, Star Trek Replicator frontier that we shouldn’t worry about. I would agree that it will take many years to see which technology would work to what extent and to industrialize it. Even if you get part of the way there, however, you could have a very marketable technology.
Imagine a voxel-level customization of tennis racket handles that reduce vibration, strain, and injury, while allowing players hit more with a more comfortable racket through mixing a few polymers and lattice structures. This could revolutionize tennis, golf, and any other racket or club sport. Imagine just having a higher comfort, wicking surface for mattresses, gloves, or steering wheels. There are many surfaces and products that we can significantly improve through a semi-functional, voxel-level system.
3D printing companies are making materials. The industry only needs one “Styrofoam” type product to be very successful. However, the industry can develop many styrofoams all with different properties. Many products are shifting from the use of metals to polymers. Just to make those goods more comfortable would be a huge opportunity. At the same time, items like industrial filters, membranes, and surfaces are open for improvement. So, even with part of a working solution, the industry could derive significant revenue that could drive it forward.
True Mass Customization?
Then, of course, we could use trinckle and Twikit to mass customize things true to customers. One could buy an insole unique to their walk, needs, and feet at every single voxel. 3D printing could make the most functional and most comfortable of everything. And that would be a significant step on the path to the integrated manufacturing of everything—absolutely everything.
Subscribe to Our Email Newsletter
Stay up-to-date on all the latest news from the 3D printing industry and receive information and offers from third party vendors.
Print Services
Upload your 3D Models and get them printed quickly and efficiently.
You May Also Like
3D Printing News Briefs, July 2, 2025: Copper Alloys, Defense Manufacturing, & More
We’re starting off with metals in today’s 3D Printing News Briefs, as Farsoon has unveiled a large-scale AM solution for copper alloys, and Meltio used its wire-laser metal solution to...
3DPOD 260: John Hart on VulcanForms, MIT, Desktop Metal and More
John Hart is a Professor at MIT; he´s also the director of the Laboratory for Manufacturing and Productivity as well as the director of the Center for Advanced Production Technologies....
3D Printing News Briefs, June 28, 2025: Defense Accelerator, Surgical Models, & More
In this weekend’s 3D Printing News Briefs, 3YOURMIND was selected to join an EU Defense Accelerator, and PTC has announced model-based definition (MBD) capabilities within Onshape. Finally, a study out...
EOS in India: AM’s Rising Star
EOS is doubling down on India. With a growing base of aerospace startups, new government policies, and a massive engineering workforce, India is quickly becoming one of the most important...