Defense giant Raytheon Technologies (NYSE: RTX) has partnered with software leader Hexagon (Nasdaq Stockholm: HEXA B) to release a breakthrough metal additive manufacturing process simulation software solution that helps predict thermal history (or heat flux) and defects at the scan vector and powder layer (meso) scale. As described by Hexagon’s director of global business development, Jeff Robertson, “the solver will run part level simulations in minutes – many orders of magnitude faster than existing solver technologies.”
Combining technologies from Hexagon’s Manufacturing Intelligence division, which empowers customers to put data to work, and Raytheon’s engine maker business, Pratt and Whitney, the new software will predict defects before the expensive and time-consuming printing process begins. This analysis will help designers and engineers evaluate the print outcome and test combinations of materials, geometries, and print processes.
The new simulation tool promises to put an end to some of the challenges in metal AM processes that can become very expensive. Defects such as keyholing, lack of fusion, balling-up, and surface roughness were a few of the issues that the software has overcome.
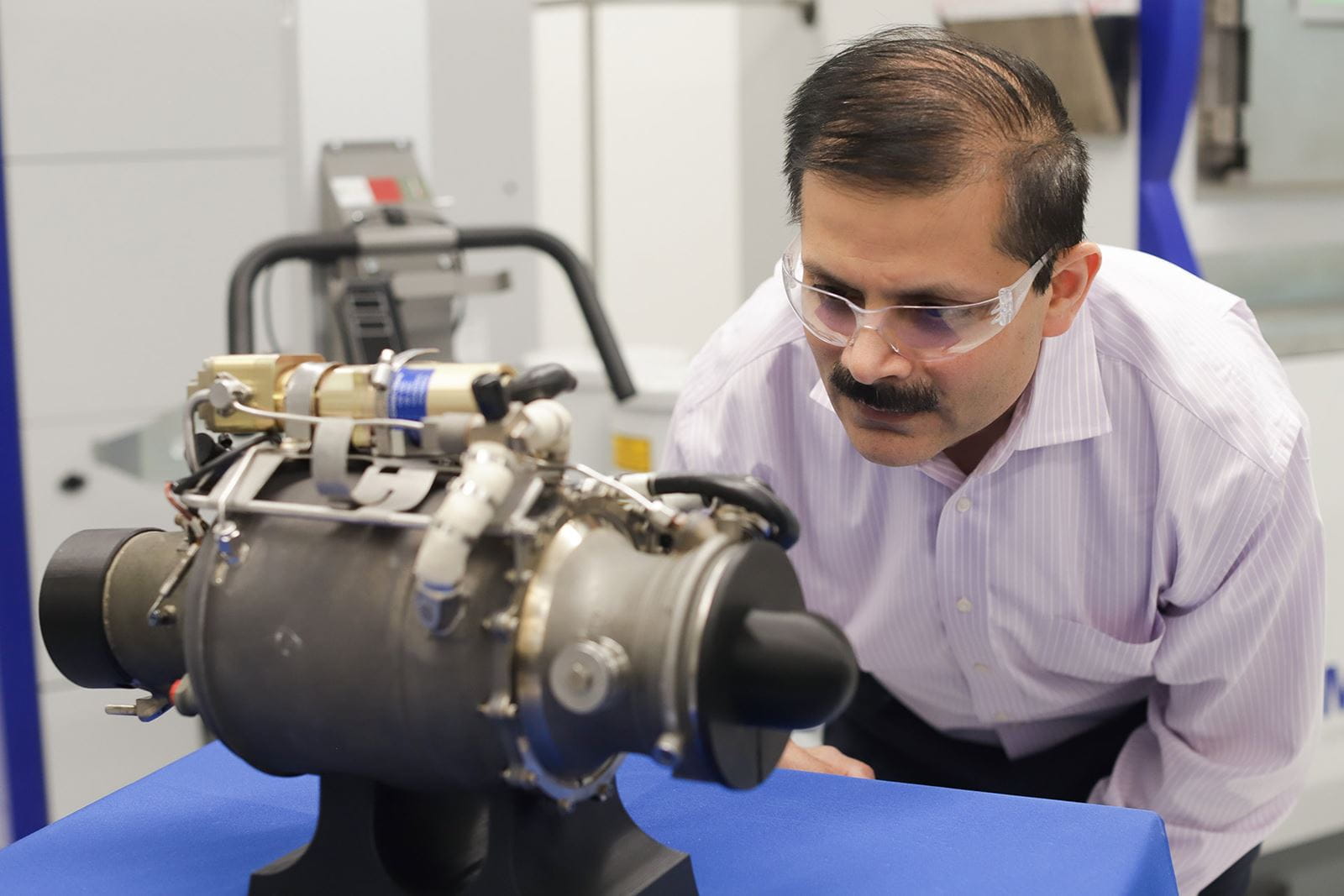
Commenting on the partnership with Raytheon, Robertson suggested that together, the two firms will “deliver an intuitive and accessible tool that will help engineers quickly predict and mitigate risks. The ability to evaluate full laser powder bed fusion (L-PBF) parts on the meso-scale will reduce the effort to achieve part certification and thereby support industrialization of metal 3D printing.”
Preparing to discuss the details of the upcoming software, the Hexagon team – led by Robertson – will be at the ASTM International Conference on Additive Manufacturing (ICAM) that began on October 31 and runs through November 4, 2022. Following the event, the software will be made available to a range of companies engaged in additive manufacturing. It will be complementary to Hexagon’s existing Simufact Additive tool, a scalable software solution for virtual testing and process design for optimization of metal-based additive manufacturing processes, like L- PBF and metal binder jetting (MBJ). In addition, the similarity to the existing user interface will allow easy integration into existing manufacturing processes by users without the need for extensive training, indicated Hexagon.
A few of the 800 commercial companies, universities, and research institutions that use the Simufact Additive tool for simulated manufacturing are automotive OEMs such as Audi, Daimler, Jaguar, Porsche, and Volkswagen, Tier 1 suppliers like Bosch and Magna as well as other highly specialized customers from the aerospace sector, the shipbuilding industry, and medical engineering.
“By combining our additive manufacturing expertise with Hexagon’s, we are bringing a solution to market that helps manufacturers with all levels of experience make better products with greater efficiency,” said David Furrer, Pratt & Whitney senior fellow for materials and processes.

Detecting design issues early on in the AM process can be a game changer for metal additive manufactured parts. Other companies have also been involved in software simulation developments. For example, Stratasys recently acquired quality assurance software company Riven and integrated the software into its GrabCAD AM platform to help customers inspect, diagnose, and automatically correct deviations between CAD files and printed parts. Creating more accurate parts is also on the agenda for companies like Desktop Metal, which started a collaboration with Siemens last October to use its Advanta software for simulating all levels of the binder jetting process and global plant planning.
With simulation software verifying, simulating, and optimizing programs before they reach the shop floor, companies are eager to implement them to make additive manufacturing more feasible and sustainable. AM teams producing metal printed parts can ensure software simulation will drive their design and production processes, changes that could save customers money and time.
Subscribe to Our Email Newsletter
Stay up-to-date on all the latest news from the 3D printing industry and receive information and offers from third party vendors.
Print Services
Upload your 3D Models and get them printed quickly and efficiently.
You May Also Like
Reinventing Reindustrialization: Why NAVWAR Project Manager Spencer Koroly Invented a Made-in-America 3D Printer
It has become virtually impossible to regularly follow additive manufacturing (AM) industry news and not stumble across the term “defense industrial base” (DIB), a concept encompassing all the many diverse...
Inside The Barnes Global Advisors’ Vision for a Stronger AM Ecosystem
As additive manufacturing (AM) continues to revolutionize the industrial landscape, Pittsburgh-based consultancy The Barnes Global Advisors (TBGA) is helping shape what that future looks like. As the largest independent AM...
Ruggedized: How USMC Innovation Officer Matt Pine Navigates 3D Printing in the Military
Disclaimer: Matt Pine’s views are not the views of the Department of Defense nor the U.S. Marine Corps Throughout this decade thus far, the military’s adoption of additive manufacturing (AM)...
U.S. Congress Calls Out 3D Printing in Proposal for Commercial Reserve Manufacturing Network
Last week, the U.S. House of Representatives’ Appropriations Committee moved the FY 2026 defense bill forward to the House floor. Included in the legislation is a $131 million proposal for...