In today’s 3D Printing News Briefs, we’re talking about business first, and then taking a turn into research, before ending on a heartwarming tale of inclusive 3D printing. First, PAMA has appointed STANLEY X president Michelle Bockman as a new executive advisory board member. Then, BOFA Americas is partnering with Würth Additive Group, while Sauber Technologies and Alfa Romeo F1 Team ORLEN have extended their partnership with Additive Industries. UCLA researchers are 3D printing entire microrobots, and finally, a teenage girl won a state design award in Tennessee for her 3D printed inclusive lunch tray.
Michelle Bockman Appointed to PAMA Advisory Board
The Photopolymer Additive Manufacturing Alliance, better known as PAMA, announced that it has appointed Michelle Bockman, the President of STANLEY X, as a new member of its Executive Advisory Board. The former CEO of 3D Control Systems and HP Inc.’s GM and Global Head of Automotive, 3D Printing and Digital Manufacturing, Bockman works to identify and build new sources of innovation and growth in main areas of Stanley Black & Decker, such as company partnerships, internal startup incubation, and ecosystem development. She’s been called one of the most influential women in the AM industry many times, was recently profiled in PAMA’s column in the UV+EB Technology Magazine, and won the Malcolm Baldridge National Quality Award. Bockman will be a big help as PAMA continues to form Working Committees, including on Market Research, Materials and Hardware Characterization, and others.
“We are excited to have Michelle’s energy and vision as part of our efforts. Michelle’s passion for innovation and 3D printing, and her commitment to advance women and girls in STEM and develop diverse workforce talent, are vital to our initiative,” said David Walker, Chair of the PAMA Executive Advisory Board.
BOFA Americas & Würth Additive Group Announce Collaboration
Illinois-based BOFA Americas Inc., part of BOFA International, and Würth Additive Group, an Indiana-based division of Würth Industry North America, announced that they are partnering up, which reinforces both of their strong positions in the AM industry and may lead to a collaboration on a global scale in the future. BOFA Americas provides fume and dust filtration systems, and is adding more and more products specifically to meet 3D printing needs, while Würth Additive Group is a distributor and reseller of AM consumables, equipment, and maintenance, repair, and operations (MRO) parts, as well as offering AM engineering services and training. Their partnership will enable the integration of BOFA’s filtration systems with 3D printers supplied by Würth, as well as add value to Würth Additive Group’s growing North American operations.
“BOFA is able to help support our customers’ strategy to promote safety and a more pleasant working environment around a variety of our equipment. Our partnership will make it easier for customers to find everything they need in one place,” said AJ Strandquist, CEO of Würth Additive Group. “Now the air you breathe isn’t an afterthought; it’s a part of the discussion from the start.”
Sauber Technologies Extends Partnership with Additive Industries
The ongoing technology partnership between Additive Industries and Sauber Technologies, along with Alfa Romeo F1 Team ORLEN, has been extended once again for another three years. Sauber has been using the MetalFAB metal AM platform since 2017, and currently has four of the systems in-house; both parties will celebrate the fifth anniversary this summer of their strategic partnership in pushing the boundaries of metal 3D printing. By investing in the MetalFAB systems, which feature unique open parameters, Sauber has been able to lower cycle times in manufacturing lightweight parts for F1 race cars and wind tunnel models.
“Over the course of our successful partnership, Additive Industries have become an essential ingredient in the offering of Sauber Technologies,” said Christoph Hansen, COO of Sauber Technologies. “Ever since we introduced the MetalFAB systems to our processes, our in-house capabilities have increased in a significant way: Additive Industries continues to provide us with the best way to manufacture the most advanced parts for our motorsport operations, as well as our growing cohort of customers, reducing lead times, costs and waste while pushing forward the boundaries of technology.”
UCLA 3D Printing Whole Microrobots in One Pass

A 3D printed meta-bot capable of moving, sensing, and making decisions all on its own. Photo via UCLA.
In a recently published study, a team of researchers from UCLA explained their new method of 3D printing entire microrobots in a single pass. 3D printable active metamaterials act as both the electronic and the mechanical systems making up the tiny “meta-bots,” which can crawl, jump, sense what’s around them, and make decisions based on programmed commands. Only a small external battery is needed to make these 3D printed robots go, as the internal structural, sensing, and movement components are all printed at once—ensuring that the pieces fit perfectly. The piezoelectric metamaterials are printed in lattice shapes, and when excited by an electric field, basically turn electrical energy into kinetic energy and move on their own. The team has 3D printed three autonomously operating meta-bots so far, one of which can maneuver around random obstacles and S-shaped corners, while another can escape from contact impacts and the third can walk and jump over rough terrain. The researchers hope their method can be applied to novel biomedical robot designs in the future, or even meta-bots for exploring hazardous environments.
“We envision that this design and printing methodology of smart robotic materials will help realize a class of autonomous materials that could replace the current complex assembly process for making a robot. With complex motions, multiple modes of sensing and programmable decision-making abilities all tightly integrated, it’s similar to a biological system with the nerves, bones, and tendons working in tandem to execute controlled motions,” explained Xiaoyu Zheng, principal investigator of the study.
3D Printed Inclusive Lunch Tray
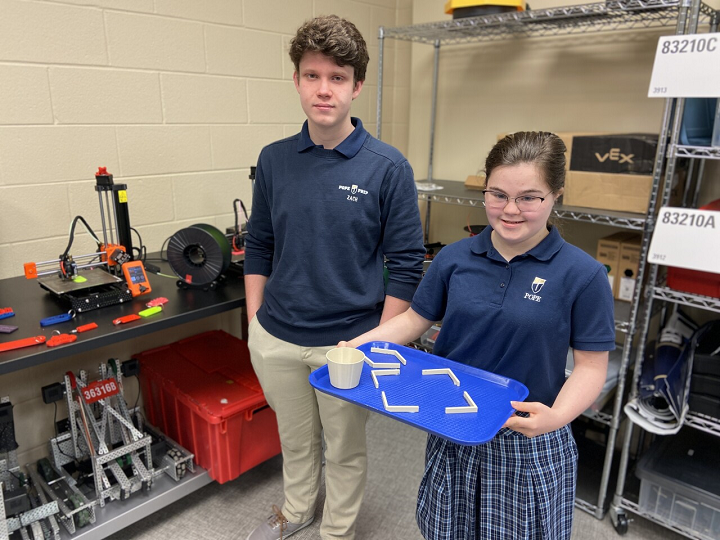
Once her prototype was finished, Adaline Hamlin worked with Pope John Paul II Preparatory School’s 3D printing club member Zach Lance to create brackets and a cup holder. Image courtesy of Claire Kopsky.
Finally, a Tennessee teenager won a state design award for her design of a 3D printed inclusive lunch tray, meant to help other students with disabilities keep their food from going everywhere. 15-year-old Adaline Hamlin, a student at Pope John Paul II Preparatory School in Hendersonville, and other students in the “Genius Hour” group she’s in, was challenged to think about things happening in the community that could be changed to benefit others. Hamlin noticed a friend, who had a hard time gripping the regular tray, accidentally spill her food all over the floor, and suggested the idea of an inclusive lunch tray to her teacher Jennifer Dye, Pope Prep Director of Innovation and Entrepreneurship. They worked on a prototype by adding different materials, like popsicle sticks and bendy straws, to a regular tray, and then Hamlin took her design to the school’s 3D printing club. An older student in the club designed the parts in study hall, sent the models to his teacher to print, and Hamlin attached the completed parts to a lunch tray, noting that it worked perfectly. For her design, called “Stop the Slide: A Lunch Tray for Students with Disabilities,” Hamlin won the Tennessee STEM and Innovation Network’s statewide design competition’s “STEM for ALL Award,” which recognizes that everyone has the ability to do STEM projects, and not just students in the gifted or AP classes.
“Her idea came from an experience she had where she saw someone spill their lunch into the floor. And she really used that first step of design thinking which is empathy,” Dye explained.
“I think it’s really important to stop and listen and look for needs within your community. And then move beyond just empathy. Really find ways to make a difference and make an impact. I think what Adeline did is she saw a need but she didn’t stop there. She said let’s fix it. Let’s make a difference. And then finding the people who can help you do that. So we worked with her other friends in Genius Hour. We worked with a 3D print club. So also finding the people you may not have the resources and the talents to make that change. But finding the people who can.”
Subscribe to Our Email Newsletter
Stay up-to-date on all the latest news from the 3D printing industry and receive information and offers from third party vendors.
Print Services
Upload your 3D Models and get them printed quickly and efficiently.
You May Also Like
3D Printing News Briefs, July 2, 2025: Copper Alloys, Defense Manufacturing, & More
We’re starting off with metals in today’s 3D Printing News Briefs, as Farsoon has unveiled a large-scale AM solution for copper alloys, and Meltio used its wire-laser metal solution to...
3DPOD 260: John Hart on VulcanForms, MIT, Desktop Metal and More
John Hart is a Professor at MIT; he´s also the director of the Laboratory for Manufacturing and Productivity as well as the director of the Center for Advanced Production Technologies....
3D Printing News Briefs, June 28, 2025: Defense Accelerator, Surgical Models, & More
In this weekend’s 3D Printing News Briefs, 3YOURMIND was selected to join an EU Defense Accelerator, and PTC has announced model-based definition (MBD) capabilities within Onshape. Finally, a study out...
EOS in India: AM’s Rising Star
EOS is doubling down on India. With a growing base of aerospace startups, new government policies, and a massive engineering workforce, India is quickly becoming one of the most important...