German car firms have been working on 3D printing for decades. Many have extensive labs and have been doing research and product development at scale for many years now. Their proximity to early leading service bureaus and 3D printing original equipment manufacturers (OEMs), as well as the enviable capabilities of Germany’s Fraunhofer institutes, built on this lead until it seemed insurmountable. Additionally, many of these firms leveraged the true manufacturing experience with 3D printing through the extensive use of 3D printed parts in F1 and custom high-end car customization. In the U.S. and Asia, there were crickets. Recently, a rather dark horse contender—albeit one of the two largest auto manufacturers globally—threw its hat in the ring for technology leadership in 3D printing. The candidate was GM.
Choke on my coffee kind of moment, that was. GM recently told the world that it used 60,000 flexible ¨spoiler closeout seal” parts using HP MJF for the 2022 Tahoe model. The company had them produced via GKN´s Forecast 3D unit, using BASF Forward AM Ultrasint TPU 1. GM also relied on AMT’s vapor smoothing technology to finish the parts.
It’s refreshing that a car company came out and showed the world about a case in which 3D printing was used for bridge manufacturing with vehicles. It has been happening for a few decades now, but no one discusses it. Kudos to GM for its transparency/marketing campaign. It is also notable that the part is a flexible one, something that additive manufacturing has traditionally not been good at.
The company also announced that it will be putting over 100 3D printed parts, both metal and polymer, in its new Cadillac CELESTIQ model. GM has put up $81 million to manufacture the car at its Global Technical Center in its Additive Industrialization Center.
I like that GM is jockeying for 3D printing supremacy, since this will only make the Germans work even harder. I also want to contrast its approach with the road taken by Mercedes, BMW, and Volkswagen. These firms have focused on deep technical and process knowledge, via in-house capability enhancement. They’ve been working on materials, automation, post-processing, qualifying methodologies and more for years. Meanwhile, GM, late to the party, starting only in 2020 or so, orders 60,000 parts from a service. I’m sure that the German firms have deeper AM knowledge, but if GM can lean on services to get the right parts and press release out the door to steal a march on them, then this should be a valuable approach.
3D Printing Car Parts without Powder Bed Fusion
Similarly SOLIZE is using HP systems to make parts for Nissan’s NISMO cars. This could mean that we could see other car makers without much AM knowledge quickly come out with components via services. I’m surprised that Chinese firms have been so quiet as well, given the heavy push that the nation has for 3D printing. One could easily imagine Eplus 3D, BLT or Farsoon showcasing 3D printed car items soon. At the same, time emerging technologies, like metal binder jet and bound metal extrusion, could enable more car components still.
Germany’s heavy investment in powder bed fusion also slowed German adoption of 3D printing and made the technology needlessly expensive. Powder bed has a lot of margins on materials and machines, as well as a very high cost basis. It also is very complex, meaning that companies will take a few years to deploy it. Due to the fact that it is a sophisticated technology that looks like it may work in a factory, firms pour years into industrializing it. This has lead to a long time in the woods for a lot of automotive applications in Germany.
Now, with binder jet, lower part costs could be achievable, especially with superior automation. Software work would be needed to qualify new components and the technology is best for libraries of qualified items, rather than many unique ones, but there is potential there. Bound metal 3D printing with simple material extrusion systems could also offer low-cost components for some geometries, as well. Markforged and BASF will be sure to push such technologies further.
Simultaneously, some higher performance polymers, especially polyamides, could further the penetration of 3D printing into automotive parts. This could be very cost effective, if the industry work on reliable material extrusion machines. The considerable amounts of money invested in powder bed fusion metals and polymers should lead to some new components being printed at scale, as well.
Where Will Car Parts Be 3D Printed?
Service platforms aspiring to perform manufacturing, such as MakerVerse, could further deploy parts without as much needed capital as services like Morf3D, Azoth3D, and Sintavia. However, where is the future of 3D printing in car parts?
It seems to be the right time to go from prototypes to end use components. Indeed, we would expect many more firms to 3D print car parts in the future. Will they print them via services? Or will they ask their existing Tier 1, 2, and 3 partners to print these items? While Auto OEMs have 3D printing knowledge and experience their suppliers currently do not. These suppliers also have little room financially to perform deep, fanciful investments into 3D printing.
Will car companies, then, 3D print parts themselves? For some of these components, it would make sense. OEMs could offer high-value, custom items, from which they capture all of the margins. Or they could have capacity to quickly perform bridge manufacturing, or create new models in-house. It remains to be seen who will 3D print car parts and where.
Which Car Parts Will Be 3D Printed?
Which components will be made for the auto industry with 3D printing is also going to be a bit of a conundrum. We’ve seen custom SLA, titanium, FDM, visible, hidden, and weight-saving parts, as well as parts with integrated functionality. Everyone is playing with different materials, technologies, and applications.
Aside from jigs and fixtures, mold tooling is an obvious area. Mass-customized polymer parts also seem obvious. In some cases, we could see integrated low-part-count, weight-saving elements made, as well. Directed energy deposition (DED) and wire arc AM-style processes for chassis and larger components would be very exciting, but seem very further off.
The big opportunity is in the maintenance, repair, and overhaul (MRO) business for the millions of car components worldwide. It’s also in the design of essential performance-enhancing items on new car platforms. Additionally, we should realize that there is a still a huge gulf between the cost of car parts made by other manufacturing methods and what the 3D printing industry is charging for its parts. This will need to be resolved for us to progress.
CELESTIQ
The one thing that I like most about the CELESTIQ is the fact that GM is going to hand-build the limited edition car itself, inside of its Global Technical Center. We often see 3D printing projects get stuck because people running production don’t want to spend time introducing a new technology to the manufacturing operations. Constructing this car by hand, will allow GM to learn about 3D printing parts and installing them on cars in defined and walled-off manner.
In this case, AM doesn’t have to ride roughshod over the company’s many fiefdoms. Additive will only be performed for components on this specific series of cars. What I think is potentially very significant is what could happen should GM be very effective with this.
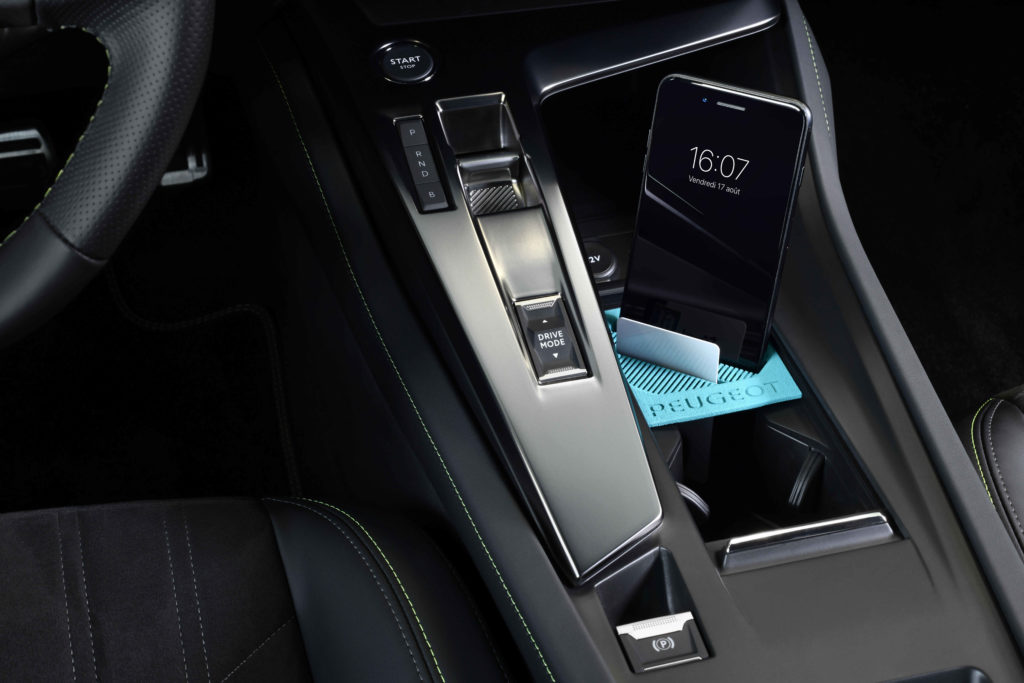
Peugeot’s 3D printed phone or card holder. Image courtesy of Stellantis.
Car companies make little money on volume cars, but do well on expensive options and fully-loaded expensive vehicle lines. OEMs also have sidelines in building customized autos, such as Bentley Mulliner, Porsche Individual, and Mercedes Guard. These are low-volume, but highly profitable.
Ideally, a manufacturer might like to make customization commonplace via high-volume, profitable, unique parts sold to millions of people. To do this, you need a great deal of confidence and institutional change. This situation is ideal, but also extremely difficult to implement.
Meanwhile, the ultimate custom car is the one-off concept car. This is a frightfully expensive vehicle, which costs millions, but showcases design futures. Concept cars are technical toys for all the world to see. Other auto brands sell low-volume super sports cars that cost $1 million or more.
So, what if GM now starts to make low-volume, hand-built cars in-house all of the time? The company reportedly wants to charge $300,000 for the CELESTIQ. If the company uses 3D printing and complementary technologies, this could actually be very profitable.
Rather than lose money on a concept car, GM could make working vehicle accessible every year in a limited number. These could be highly profitable for the firm, while wooing journalists and car aficionados alike. The cars could create a halo effect for the brand in a manageable and profitable manner.
I’m not sure yet if this is the company’s intention. The CELESTIQ could be a one-off testbed to familiarize itself with 3D printing. But, imagine the marketing excitement you could create by making completely crazy, drivable cars sporting your brand before onlookers on the street. Imagine if customers paid up-front for your design exploration, generating brand excitement in the process. Imagine what you could do financially if you sold 300 cars for $1.5 million a piece to car collectors each year? Such an approach would leverage 3D printing well.
AM is the key technology that could allow a company produce a lot of the components for such a car, in addition to a large amount of molds and tooling. Imagine, if the CELESTIQ was not just a one-off but a future method for creating buzz, excitement, and finding out what the world wanted. Then for GM $300,000 a pop it would be an ultimate marketing tool, a cost effective marketing tool and a showcase that drives around. And for collectors? The CELESTIQ is the limit.
Subscribe to Our Email Newsletter
Stay up-to-date on all the latest news from the 3D printing industry and receive information and offers from third party vendors.
Print Services
Upload your 3D Models and get them printed quickly and efficiently.
You May Also Like
Metal Powder Supplier Elementum 3D Added to $46B Air Force Contract
Elementum 3D, a Colorado-based developer and supplier of metal powders used in additive manufacturing (AM), announced that the company has been added to the vendors list in the fourth on-ramp...
Ursa Major Lands $28.6M AFRL Deal for 3D Printed Draper Engine Flight Demo
The US Air Force Research Laboratory’s (AFRL’s) Rocket Propulsion Division at Edwards Air Force Base has awarded a $28.6 million contract to Ursa Major for follow-on work related to the...
3D Printing Financials: Rocket Lab’s Record-Breaking Year and Over 20 Launches Coming in 2025
Rocket Lab (Nasdaq: RKLB) closed 2024 with its best year yet. The company launched more rockets, signed more contracts, and expanded deeper into spacecraft and satellite production than ever before....
US Air Force Taps Beehive to Study 3D Printed Jet Engines
Propulsion 3D printing firm Beehive Industries secured a contract from the U.S. Air Force Life Cycle Management Center through SOSSEC. SOSSEC is a company that manages Other Transactions Authority (OTA)...