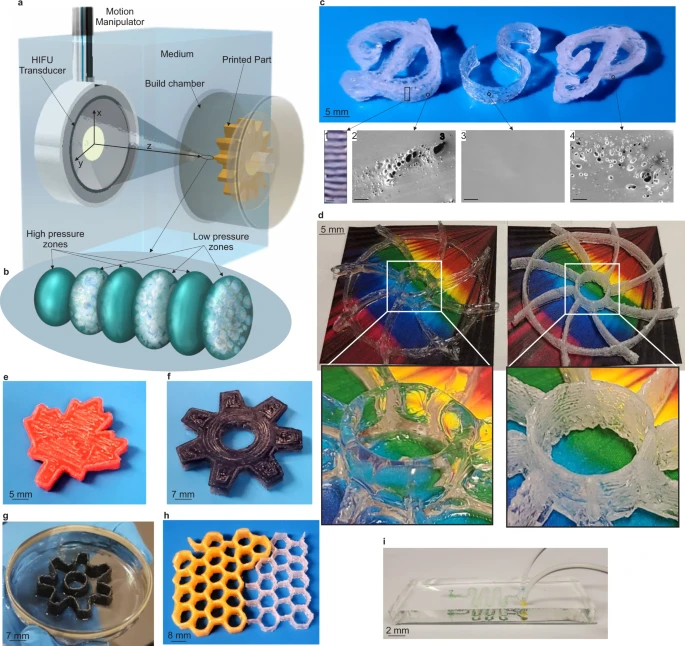
Direct Sound Printing (DSP) process schematic. Image courtesy of Habibi, M., Foroughi, S., Karamzadeh, V. et al. Direct sound printing/Nature Communications.
The “build chamber filled with the build material (monomer mixed with curing agent or different mixtures) through exposing to the focused ultrasonic field. We call this method Direct Sound Printing (DSP). The ultrasonic field, which is generated by a monolithic spherical focused transducer, reaches the build material after passing through the shell of the build chamber. At the focal location in the build material, as shown in Fig. 1a and detailed in Fig. 1b, the chemically active acoustic cavitation region solidifies the liquid resin or mixture and deposits it to the platform, or on top of previously deposited and solidified regions. We call this region as ultra-active micro reactor (UAMR) where generated bubbles and polymerized resin appear at the low-pressure zones and then they migrate momentarily to high-pressure zones until they reach to the platform or previous solidified pixel where they are deposited. The transducer is moved in the medium by a motion manipulator to locate the focal region along a calculated path in the build chamber to create the desired part pixel by pixel. Input parameters of DSP process affect the microstructure of the printed parts. These parameters are characteristics of the transducer driving pulse (such as electrical power, frequency and duty cycle which is the active fraction of the driving pulse period), build materials (such as the mixing ratio of monomer to curing agent, mixture ratio, viscosity and surface tension) and the transducer motion (such as velocity and acceleration of the transducer). Different micro structures result in optically transparent to opaque parts in DSP. The resultant opacity is due to the porous structure of the printed part, which can be controlled/by manipulating the DSP input parameters.”
A very exciting variant is Remote Distance Printing (RDP), where you can let the acoustic waves pass through a wall or skin, let’s say, to build an object on the other side of that wall without touching it. The team feels this could be used for “emote repairing or on-site maintenance of hidden parts in aerospace industries and in-vivo remote and noninvasive bioprinting of inside body parts in medical applications.”
They further go on to test printing as “noninvasive deep inside body printing.” Demonstrating that it could be possible, for example, to harden and build a structure inside the human body while the 3D printer was outside of it. This could potentially be a completely new approach whereby, for example, you could inject a material and then locally print it into a defined structure without surgery. You could get a facelift without getting cut open or do a transaction in a patient using an injected material that is then 3D printed in place, turning it from a liquid into a staple.
It remains to be seen if these applications will work at scale and find commercial venues. But, new technology is always very exciting and gives us new perspectives. Mohsen Habibi and Muthukumaran Packirisamy have filed a patent application and obtained a patent which means that this technology has been a long time coming and points to them seeking commercialisation in some way.
In their patents, they talk about two methods where “Selective Spatial Solidification forms the piece-part directly within the selected build material whilst Selective Spatial Trapping injects the build material into the chamber and selectively directs it to accretion points in a continuous manner.” This may point to them having an eminently controllable process that could in a layer less way produce controlled porosity or could selectively sinter powder in a new way.
Subscribe to Our Email Newsletter
Stay up-to-date on all the latest news from the 3D printing industry and receive information and offers from third party vendors.
Print Services
Upload your 3D Models and get them printed quickly and efficiently.
You May Also Like
Reinventing Reindustrialization: Why NAVWAR Project Manager Spencer Koroly Invented a Made-in-America 3D Printer
It has become virtually impossible to regularly follow additive manufacturing (AM) industry news and not stumble across the term “defense industrial base” (DIB), a concept encompassing all the many diverse...
Inside The Barnes Global Advisors’ Vision for a Stronger AM Ecosystem
As additive manufacturing (AM) continues to revolutionize the industrial landscape, Pittsburgh-based consultancy The Barnes Global Advisors (TBGA) is helping shape what that future looks like. As the largest independent AM...
Ruggedized: How USMC Innovation Officer Matt Pine Navigates 3D Printing in the Military
Disclaimer: Matt Pine’s views are not the views of the Department of Defense nor the U.S. Marine Corps Throughout this decade thus far, the military’s adoption of additive manufacturing (AM)...
U.S. Congress Calls Out 3D Printing in Proposal for Commercial Reserve Manufacturing Network
Last week, the U.S. House of Representatives’ Appropriations Committee moved the FY 2026 defense bill forward to the House floor. Included in the legislation is a $131 million proposal for...