Leading headphone brand Sennheiser has announced that its latest earbuds, the IE 600, are to be made with 3D printing. This isn’t entirely surprising, given that Sennheiser’s consumer division is owned by Sonova, a large hearing aid company that is one of the largest users of 3D printing worldwide. What is a surprise is that the material from which the headphones are made is an amorphous metal, also called bulk metallic glasses.
I’m a huge Sennheiser fan and own bulkmetallicglasses.com, so this is completely wild to me. It’s like I’m being targeted as a demographic of one. Bulk metallic glasses are new, high-tech materials that are very strong and highly abrasion-resistant. For example, they’ve been used to make gears that will never require lubricant. Here we have an excellent interview explaining how bulk metallic glasses have helped NASA´s JPL.
Two startups, Amporphology in the U.S. and Exmet in Sweden, currently 3D print bulk metallic glasses. I haven’t been able to find out whose big win this is, but it is definitely a win for 3D printing. This is also big news for German tech group Hereaus. It is that firm’s bulk metallic glass materials that are being used for the headphones.
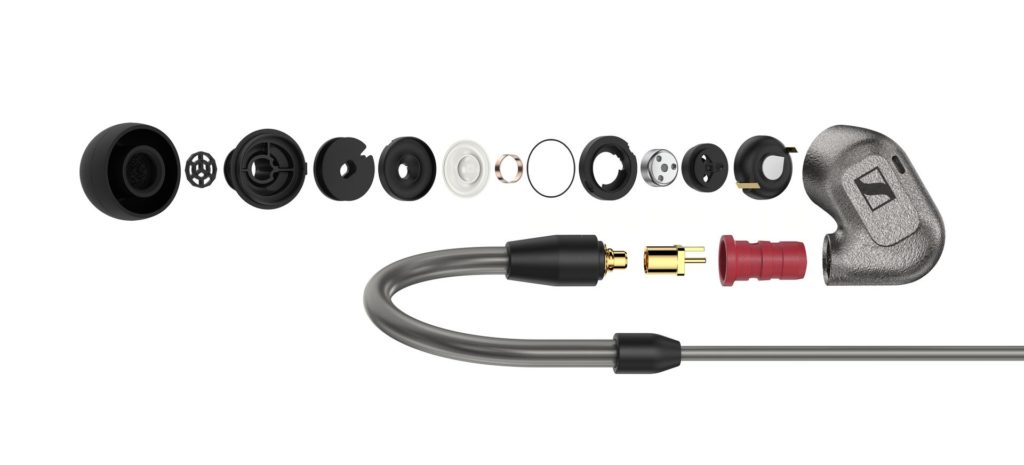
The Sennheiser IE-600 3D printed earbuds. Image courtesy of Sennheiser.
Sennheiser claims that the headphones offer ¨direct, neutral tuning with fast, accurate bass.” It further notes:
¨IE 600 has triple the hardness and flexural strength of high-performance steel. Shock-frozen during manufacturing, amorphous metals never have a chance to form a crystalline structure like conventional metals. The result is a lustrous, satiny surface that is extraordinary resistant against corrosion and scratches. The IE 600 housing is fabricated using metal-powder-based 3D printing that can create any shape imaginable within tight tolerances. Chambers and channels form as part of this additive manufacturing process with no milling required. However, cost does limit the potential applications of this new material. One of the only places you’ll find it — besides ultra-high-end products like the IE 600 — is in the drilling head of a NASA Mars Rover where extraordinary resilience in extreme conditions is required.¨
This could be a potentially big move for a segment that 3D printing has so far failed to penetrate. A big player in the in-the-ear (ITE) hearing aid market, Sonova uses ETEC (née EnvisionTEC) systems, along with some other brands, to 3D print hearing aid shells via digital light processing (DLP) technology.
Indeed, 3D printing has revolutionized the ITE segment in hearing aids. Users get a custom hearing aid shell that is more comfortable. Phonak can make these more cost effectively than with other processes. And the retailer relies on a digital process that allows them to upsell a simple hearing aid and turn it into something better for customers. It’s a great 3D printing success story that has upended this market and made us the default technology in custom hearing aids.
While we rule that category, we have not yet made much headway in consumer headphones. Even with people wearing headphones many hours a day for work, music, and Netflix, our penetration in consumer headphones has been practically non-existent. One Phonak headphone tried to blaze the way years ago with 3D printing and the other also has some consumer-facing possibilities in hearing protection for workers, but there is little else.
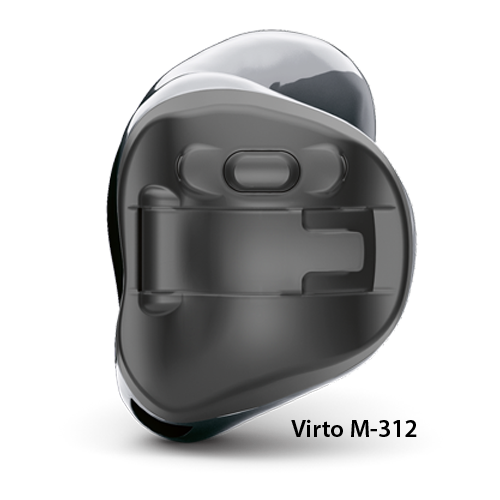
An Ultimate Ears monitor. Image courtesy of Ultimate Ears.
There was Normal, a startup that didn’t last long. We’ve also seen companies like Ultimate Ears use 3D printing manufacture high-end, in-ear monitors for audio technicians and recording artists. However, all in all, it’s niche. We’re talking about 100,000 3D printed monitors in the case of Ultimate Ears, not the millions that Phonak does for hearing aids.

A Phonak hearing aid with 3D printed shell. Image courtesy of Phonak.
Hearing aids and earbuds use the same 3D printing technologies and the same processes to realize a part. Generally, a scan of a wax impression of one’s ear is digitized and repaired. An employee orients it and places the electronics virtually in the 3D scan. This is then sent to an EnvisionTEC Perfactory, a 3D Systems stereolithography machine, or maybe an ASIGA system, and then printed. Supports are removed by hand and the employee works desk side with the printer to file, flash, wash and assemble the hearing aid.
This may be rather more artisan than you thought, perhaps, but, at the same time, tens of millions of cost-effective hearing aids have been made this way. Meanwhile, in headphones, people casually buy non-functioning Beats status symbols for hundreds of dollars. Audiophiles may spend thousands on headphones, as well. With people wearing them for work and play, including sports, many individuals now own several headphones, more of them likely to be premium nowadays.
However, the headphone market has been a killing field with new entrants, fickle consumer behavior, and big players making it a supremely competitive space to be in. This is what prompted Sennheiser´s exit from the consumer space in the first place (Sennheiser still exists, making excellent microphones and other solutions for professionals).
I’m salivating. We’ve yet to see if this is a cool one-off design that is meant to titillate audiophiles or if we will be seeing more of 3D printed headphones made from bulk metallic glasses in the future. I’m seriously thinking of getting them, but at a price of over $600, I’m not sure how many others will sell. To me, a process whereby 3D printed, custom polymer headphones will give us all high comfort. That is a surefire way to the future of 3D printed headphones. Let’s see if this is in the offing in the future!
Subscribe to Our Email Newsletter
Stay up-to-date on all the latest news from the 3D printing industry and receive information and offers from third party vendors.
Print Services
Upload your 3D Models and get them printed quickly and efficiently.
You May Also Like
Making 3D Printing Personal: How Faraz Faruqi Is Rethinking Digital Design at MIT CSAIL
What if your 3D printer could think more like an intelligent assistant, able to reason through a design idea, ask questions, and deliver something that works exactly the way the...
Reinventing Reindustrialization: Why NAVWAR Project Manager Spencer Koroly Invented a Made-in-America 3D Printer
It has become virtually impossible to regularly follow additive manufacturing (AM) industry news and not stumble across the term “defense industrial base” (DIB), a concept encompassing all the many diverse...
Heating Up: 3D Systems’ Scott Green Discusses 3D Printing’s Potential in the Data Center Industry
The relentless rise of NVIDIA, the steadily increasing pledges of major private and public investments in national infrastructure projects around the world, and the general cultural obsession with AI have...
Formlabs Teams Up with DMG MORI in Japan
In late June, Nick Graham, Chief Revenue Officer at Formlabs, announced on LinkedIn that the company had partnered with DMG MORI, one of the world’s leading machine tool companies, to...