Last week, while discussing a new printing filament partially made from wheat bran waste, I mentioned that greater exploration of biodegradable printing materials could be the best long-term solution for improving the net sustainability of additive manufacturing (AM) technologies. Another recent project — this one involving a biodegradable ink used to make robots with soft bodies, created by a research team at Johannes Kepler University Linz in Austria — illustrates even more clearly how crucial such considerations will be, the more that general adoption of AM continues to increase.
The project, the results of which were published in Science Robotics, involves technology that has seen growing interest in the past few years: soft robotics made from gelatin-based materials. Soft or “squishy” robots may be useful when flexibility of movement is a priority, something that’s far more difficult to achieve with harder-bodied, traditional robots. They’re often designed with inspiration from natural phenomena—one example in the ever-growing class of engineering techniques referred to as biomimicry. For instance, some of the earliest examples of 3D printed soft robotics were directly modeled after the way octopus’ bodies move. The video below (courtesy of Popular Science) shows a similar project worked on by another research team.
The latest phase in the field of soft robotics, the aforementioned move towards biodegradable materials, has been somewhat stalled by problems associated with gelatin, the main component researchers have used in the manufacture of more eco-friendly robots. For one thing, gelatin easily becomes moldy. For another, as physicist Florian Hartmann (who worked on the project with the Linz team) explained, the drier the gelatin gets, the more brittle it becomes, leading the gelatin-based robots to break with even minor amounts of stretching.
These were the main problems the researchers in Austria addressed. Taking the baseline recipe of gelatin and sugar previously used by other engineers on similar projects, the Linz team added citric acid and glycerol. The former modification took care of the mold problem, while the latter one allowed the material to be much stretchier without breaking. Moreover, as earlier researchers have also shown, gelatin has a significant advantage over polymers used for 3D-printing soft robots in terms of how quickly it’s able to solidify and thus be ready for use.
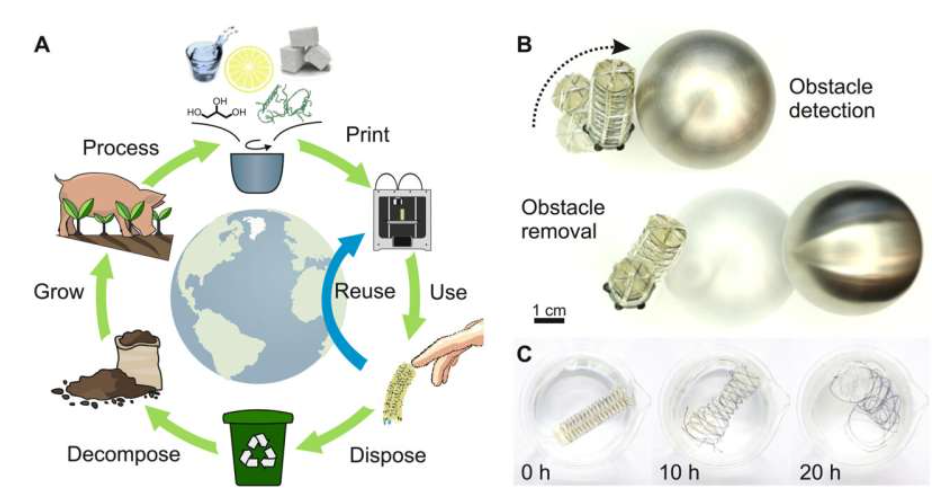
After 3D printing a robotic finger, the team wrapped it in strips of material composed mostly of ethanol and shellac, and containing LEDs and light sensors. This made the finger sensitive to light, which allowed the engineers to control the robot by blowing compressed air at it. The air changed the angle of the lights hitting the robot, the outer material responded to the shift in light, and resultantly, the finger moved in the directions desired by its operators. This is a fairly standard setup for this type of experiment. The Linz researchers in particular simply constructed their system out of a Raspberry Pi and a PlayStation 4 controller. In the experiment, the researchers showed how the robotic finger could be directed to knock objects away from it.
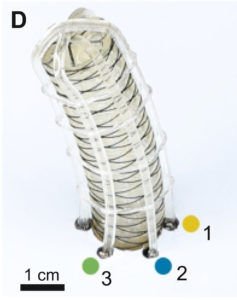
The 3D printed robot finger. Image courtesy of Science Robotics.
According to the study published in Science Robotics, the material the team formulated can be melted and reused five more times before it becomes useless, and it completely dissolves after several hours once it’s placed in water, compost, or sewage. Although the technology is still in a very early stage, this most recent study is significant because of the two major problems it solved, as the solution makes it more likely that future researchers will take the idea seriously and consider it worthwhile to continue building upon.
Subscribe to Our Email Newsletter
Stay up-to-date on all the latest news from the 3D printing industry and receive information and offers from third party vendors.
Print Services
Upload your 3D Models and get them printed quickly and efficiently.
You May Also Like
The Dental Additive Manufacturing Market Could Nearly Double by 2033, According to AM Research
According to an AM Research report from 2024, the medical device industry, specifically in dentistry, prosthetics, and audiology, is expected to see significant growth as these segments continue to benefit from...
Heating Up: 3D Systems’ Scott Green Discusses 3D Printing’s Potential in the Data Center Industry
The relentless rise of NVIDIA, the steadily increasing pledges of major private and public investments in national infrastructure projects around the world, and the general cultural obsession with AI have...
AM Research Webinar Explores Continuum’s Sustainable Metal Additive Manufacturing Powders
Metal additive manufacturing (AM) powder supplier Continuum Powders is working to develop solutions that empower industries to reduce waste and optimize their resources. An independent life cycle assessment (LCA) of...
3D Printed Footwear Startup Koobz Lands $7.2M in Seed Round
California-based Koobz is focused on reshoring the U.S. footwear supply chain with advanced manufacturing processes, including 3D printing. The startup just announced that it has added $6 million to its...