Jason Jones, Co-Founder & CEO of Hybrid Manufacturing Technologies, will be participating in Additive Manufacturing Strategies 2022, Panel 2: Future role of hybrid machines.
The word “hybrid” is a highly flexible word today. In some contexts, it is used to describe the combining of alternatives. For example one can participate in a “hybrid event” virtually or in-person. While there are pros and cons to each type of attendance, the same content can largely be delivered in either way.
Another common example of this is a “hybrid vehicle” that can be propelled by fuel or battery. Again, the vehicle can move using either method (in spite of the pros and cons of each). Often the combining of alternatives increases the cost, weight, or complexity of a system resulting in compromise.
While acknowledging the above-mentioned meaning of “hybrid,” when it comes to 3D printing, hybridization is a very different value proposition. It becomes most evident as post-processing intensifies. A significant number of 3D printing materials require extensive post-processing steps before parts made of them are finished. These steps most often occur in separate machines (or stations), however they can and increasingly are being brought together.
This latter use of the word “hybrid” refers to the combining of complements. There is no choice between either or any of the complementary process steps since each contributes a fundamentally different capability. In this sense any of the hybrid elements is incomplete without its counterparts. It is only when they are brought all together that they form a complete set. Beyond just addressing the different aspects needed to complete the job, synergy can often be achieved in this type of union that is not possible through the elements used independently. A decade ago, the introduction of the term “hybrid manufacturing” to industry started with this intended meaning, of combining techniques that become better together.
The backstory to the wider introduction of the term “hybrid manufacturing” gives insight into its intended meaning. As the additive industry widened is purview from primarily printing polymers to also embrace metal printing in the 2000’s to 2010’s, post processing surfaced as a non-trivial element to its successful adoption. As still practiced today, post-processing of printed metal parts typically involves heat treatment, surface finishing, and inspection (see figure).
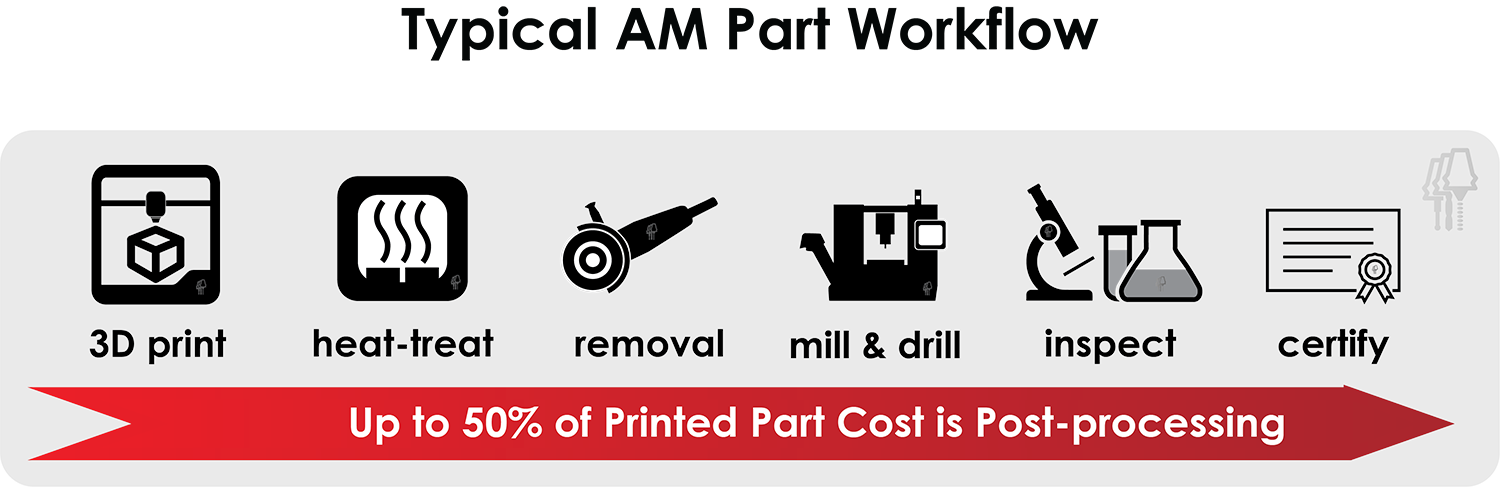
Figure showing typical post-print processing steps for printed metal parts
While post-processing of polymer parts was already widespread practice, the post-print requirements for metal parts and their intended use environments gravitated to far more serious endeavors. Early adoption revealed that post-processing costs often exceed 25-50% of finished printed part production costs. As the relative cost of printing was rivaled by post-processing steps this called for exploration into additional deployment options for finishing and inspecting parts.
One answer to this need was to increase the capability of the “printer” to also include finishing and inspection technology resulting in “hybrid machines.” While hybrid all-in-one architecture not only enables automation of post-processing steps, often at significant time and cost savings, it also delivers capabilities that cannot be realized by using any of the technologies independently. For example, hybrid machines enable finishing of internal features mid-build before access to them is lost due to additional building. Additionally inspection of key features can be undertaken layer-by-layer in ways that are not practical after the part is finished.
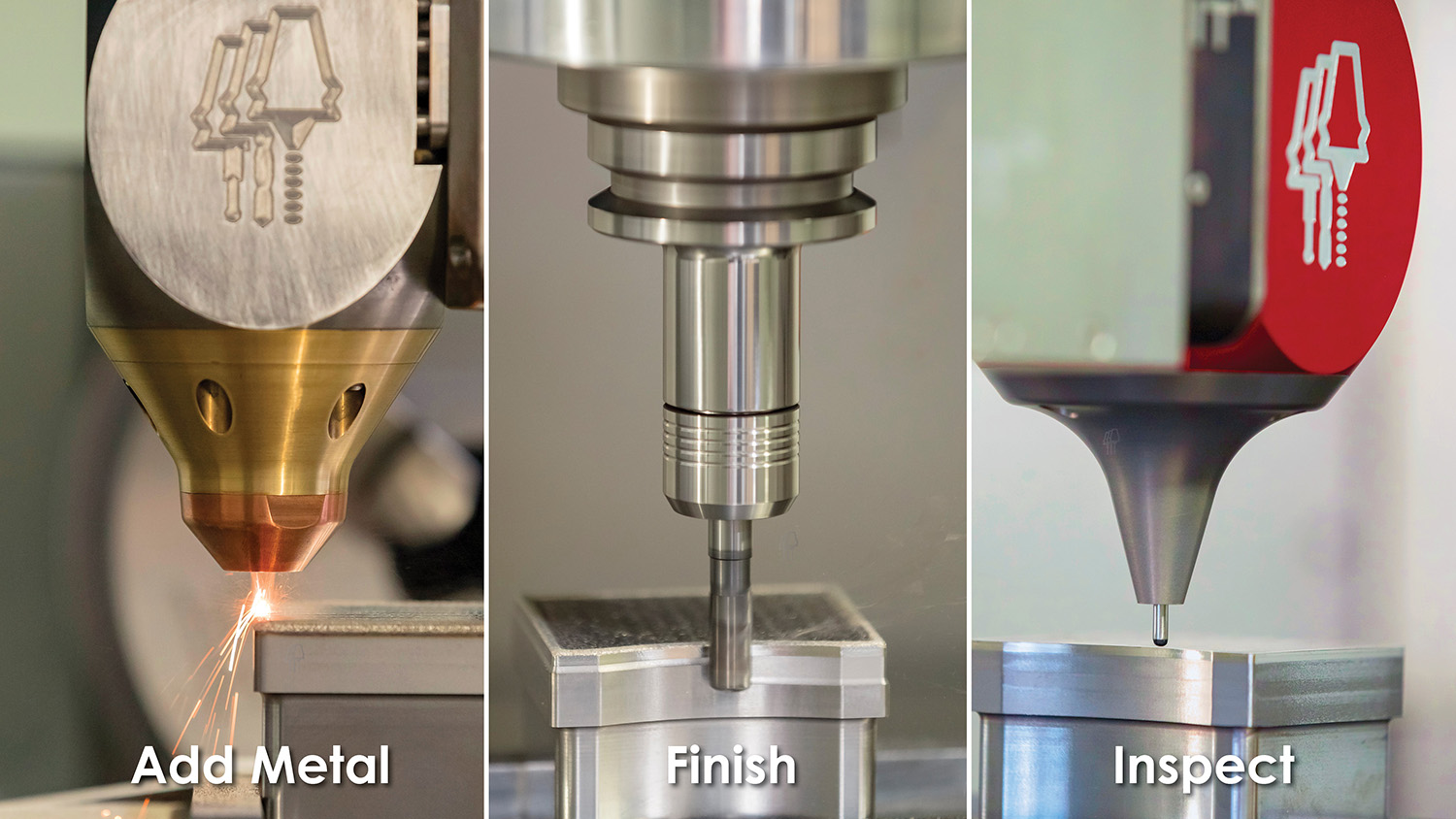
Figure showing metal additive manufacturing steps in a single setup
For metals and other high performance materials, hybridization of additive, subtractive, and inspection is an automation feat that should not be misinterpreted as a compromise. This is the merging of complements, not the merging of alternatives. Hybrid machines delivery complementary technologies in a holistic system, all controlled in the same way. This approach can reduce post-processing costs by more than half, nearly eliminate work in progress, and practically achieve no fault forward production.
Just as a gymnast masters more than one fundamental skill in order to truly compete. The same is true for many additive manufacturing process chains that rely on multiple manufacturing disciplines to deliver finished parts. The further development and adoption of hybrid manufacturing complements and completes 3D printing, helping to realize its full manufacturing potential.
Subscribe to Our Email Newsletter
Stay up-to-date on all the latest news from the 3D printing industry and receive information and offers from third party vendors.
Print Services
Upload your 3D Models and get them printed quickly and efficiently.
You May Also Like
The Market and Industry Potential of Multi-Material 3D and 4D Printing in Additive Electronics
Additive manufacturing leverages computer-based software to create components for products by depositing either dielectric or conductive materials, layer by layer, into different geometric shapes. Since its birth in the 1980s,...
3DPOD 262: Bio-inspired Design for AM with Dhruv Bhate, Arizona State University
Dhruv Bhate is an associate professor at Arizona State University. There, he looks at structures, materials, and design. Previously, he worked at PADT as well as in the semiconductor and...
3DPOD 261: Tooling and Cooling for AM with Jason Murphy, NXC MFG
Jason Murphy´s NXC MFG (Next Chapter Manufacturing) is not a generalist service; instead, the company specializes in making tooling. Using LPBF and binder jet, the company produces some of the...
3DPOD 260: John Hart on VulcanForms, MIT, Desktop Metal and More
John Hart is a Professor at MIT; he´s also the director of the Laboratory for Manufacturing and Productivity as well as the director of the Center for Advanced Production Technologies....