Roland Fischer is the CEO of Oerlikon, a 10,000-employee group with revenues in excess of $2 billion and active in a range of industrial areas. The conglomerate has a significant surface coating division, as well as one that manufactures fibers. Oerlikon has also invested deeply in additive.
The company makes powders for additive manufacturing (AM), but it also has a service for producing prototype parts and another to help you industrialize these prototypes. Oerlikon can also manufacture parts at scale for you at its U.S. and Swiss locations. The combination of deep knowledge of AM and deep knowledge of surface coating means that the company can be a key partner for those wishing to produce the most demanding of components.
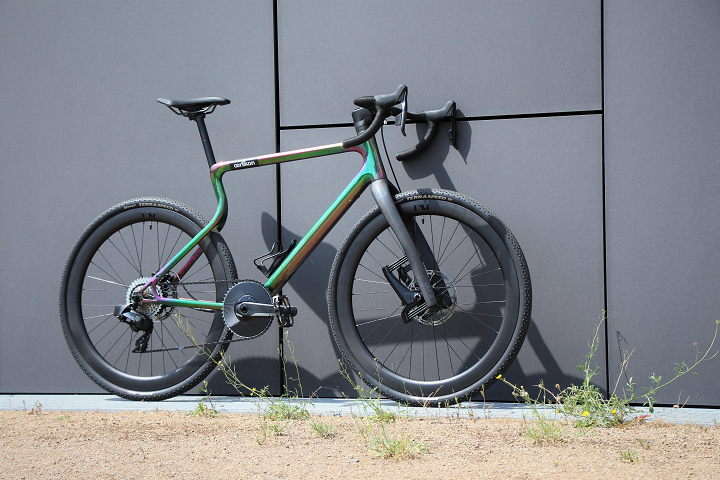
The Urwahn bike has Oerlikon-made components on it.
We interviewed Roland Fisher to find out more about the firm. Roland explains that it was a strategic decision that led them to enter the AM business, an extension of Oerlikon’s core competencies.
“It made perfect sense for us. In metals, it is not purely about the materials, but about applications. The combination of understanding the material, the component, the business itself, markets like aerospace, and the coating business made it a logical decision. In the future, we aim to pursue projects such as including sensors in a coating to make more interesting AM parts,” Fisher said. “We’ve now built factories for materials and part production. We primarily focus on aerospace, but have a wider landscape of clients. And the focus is on metals, although we do make polymer parts, as well. We’ve taken our production from primarily prototyping to manufacturing. We are moving from 10 to a 100 pieces to thousands of pieces”
I was curious to know what the firm sees as its key challenges to face and solve. Like individuals in many businesses, he noted that qualification and regulations were important obstacles to mass production. However, progress is being made, as evidence by the type of attendance he has seen at Oerlikon’s Advanced Manufacturing Technology Conference, begun in 2017.
“We’re moving more to serial production, going from accessible parts to acceptable ones. We’re working on optimizations in powder bed and excited about multi-laser powder bed fusion and binder jetting. There are lots of challenges today: qualification, approvals, regulation. There is lots of hesitancy to accepting risks and this differs in different industries. If I could close my eyes and dream and wish one thing it is speed,” Fischer said. “A few years ago at our conference, we had the additive nerds. Now, we see the heads of production; CTOs attend; it has become strategic. There are now real applications and real challenges. The community has become more diverse, as well, there were 650 startups in the space of 12 months.”
As much as the additive industry has been advancing, it, like other sectors, were severely impacted by COVID-19, as well as the resulting supply chain issues. Of all of the verticals that Oerlikon serves, Fischer said that aviation, where the company has deals with such firms as Lufthansa and Boeing, was hit hardest. However, the company continues to grow its 3D printing business across a number of segments, including aerospace.
“Aviation was heavily hit by the pandemic, so this is at a lower level. But, aerospace is progressing nicely overall. Space and satellite parts, antennas, the defense business, oil and gas, and subsea have progressed nicely. In energy, there are a lot of projects ongoing. General industry is also now important. We’re also making parts for bags and belts in the luxury goods segment. We’re seeing additive open up a deeper functionality. In a lot of areas, there is a need for things that we cannot produce without additive—that need to have the highest quality,” Roland explained. “There are also cases where additive can add a new feature or new dimension to a product. A cooling effect on an industrial part. Additive is hardly something to replace existing technology but it works when you can do something that you couldn’t do before.”
When I asked him what components Oerlikon is bullish about, he named spare parts, particularly where functionality can be combined, using sensors for example. He also noted the ability of AM to disrupt e-mobility, including fuel cells, weight and more. However, Fischer was careful not to be overly excited discussing specific components. He likened his view of AM to the way physician examines a patient.
“I’m an engineer, conditioned in a certain way. Take a doctor, for example. They don’t talk about the parts. What is relevant is the patient, when they can get better and be released. It’s not about optimizing the part. It’s about optimizing the process. About applying our knowhow to something completely different. We must be careful when we talk about mass production.”
For this reason, he highlighted the benefit of 3D printing in very specific, high-performance applications, such as the space, in which Oerlikon has worked with RUAG, and subsea sectors.
“Right now, space and aerospace where we produce a 100 parts with a limited size, low defects, good surface, low weight, we’re much more relevant. Here it has to work. For the satellite people it has to work and save weight. For a pumping station 1,000 meters below sea level, failure is not an option. In some cases, we have parts that now have cooling features and can last ten years. The field of applications is beginning to widen.”
On the whole, Fischer is optimistic about the market and its development. “It used to be a German play, with most of the big printer companies being located there. Lots of industry picked it up as well. But, now there is strong development in the US, especially in the defense business and Asia is picking up. For us it’s important we don’t miss a big play and that we stay focused on growth and the future.”
It important that Oerlikon use its production prowess and materials knowledge to improve materials. That is where its biggest differentiator lies. If it continues to do this it will help accelerate not only its own growth but that of many firms simultaneously.
Subscribe to Our Email Newsletter
Stay up-to-date on all the latest news from the 3D printing industry and receive information and offers from third party vendors.
Print Services
Upload your 3D Models and get them printed quickly and efficiently.
You May Also Like
Johns Hopkins University Researchers Develop HyFAM Technology
Two scientists from Johns Hopkins University, Nathan C. Brown and Jochen Mueller, have developed a hybrid manufacturing technology they call HyFam, or Hybrid Formative Additive Manufacturing. Their work on this technology...
3D Printing G-Code Gets an Upgrade: T-Code
Good old G-Code still manages many 3D printers, great and small. Just like the STL, it’s a standard that enables collaboration while also holding the additive manufacturing (AM) industry back....
AM Rewind: The Biggest News and Trends of 2024
After a sluggish 2023, driven by persistent inflation and geopolitical tensions, 2024 has seen some recovery. Economic growth climbed from about 2.8 percent in 2023 to a modest 3.2 percent...
Metal Wire 3D Printer OEM ValCUN Announces Plans for 2025 Expansion
ValCUN, a Belgian original equipment manufacturer (OEM) of wire-based metal additive manufacturing (AM) hardware, has announced that the company has entered the next phase of its growth trajectory, making key...