Siemens Digital Industries Software has partnered with Hyundai Motor Company and Kia Corporation to introduce Siemens’ Teamcenter and NX Xcelerator products as their authoring, design and management software. NX is the German tech giant’s CAD/CAM/CAE package, while Teamcenter is its product lifecycle management (PLM) platform. This is a big win for Siemens, as companies rarely if ever switch between CAD, PLM, and other core design software packages.
“Selecting NX software and the Teamcenter portfolio from Siemens’ Xcelerator portfolio for our core design and data management platforms will introduce a new working environment for our teams that will pave the way for a leap forward in future car development. This is the beginning of a huge transformation and an important point of change for Hyundai Motor Company and with Siemens as our trusted partner we will work together to achieve our goals through mutual cooperation and teamwork,” said Albert Bierman, Head of R&D Division, Hyundai Motor Company.
“Like so many of our customers, Hyundai and Kia is undergoing major transformations in its business and Siemens is honored to have been selected as a strategic partner to provide support and state of the art technologies that will help revolutionize how it develops its next generation products. The Xcelerator portfolio is delivering the tools and technologies for digital transformation that the future demands and our customers need today, so we look forward to collaborating with Hyundai and Kia on next generation Engineering and Product Data Management Systems that will speed digital transformation as we explore the future of mobility, together,” said Tony Hemmelgarn, President and Chief Executive Officer, Siemens Digital Industries Software.
The company stated that the two will work together to establish methods for considering the complete lifecycle of all vehicles, as well as the associated processes and activities. This includes production, purchase, and partner R&D. To pull it off, Siemens will be training Hyundai and Kia to effectively use Siemens software across its suppliers. Perhaps the switch to electrification would give car companies the opportunity for such a mid-stream shift to new core CAD and files management solutions.
Such switching is usually very painful for companies, employees, thousands of partners, and IT staff. Workflows, shortcuts, and processes don’t work and migration, training and implementation are very painful. So, for better or for worse, companies tend to stick with the CAD solution they chose once and then add on a smorgasbord of other mitigating solutions to that. So, when companies standardize or when they start developing products early on is usually the only time to really get involved. Here, a large twinned car company is switching to Siemens’ Digital Twin solution mid-stream. This is rare and a huge accomplishment for the company.
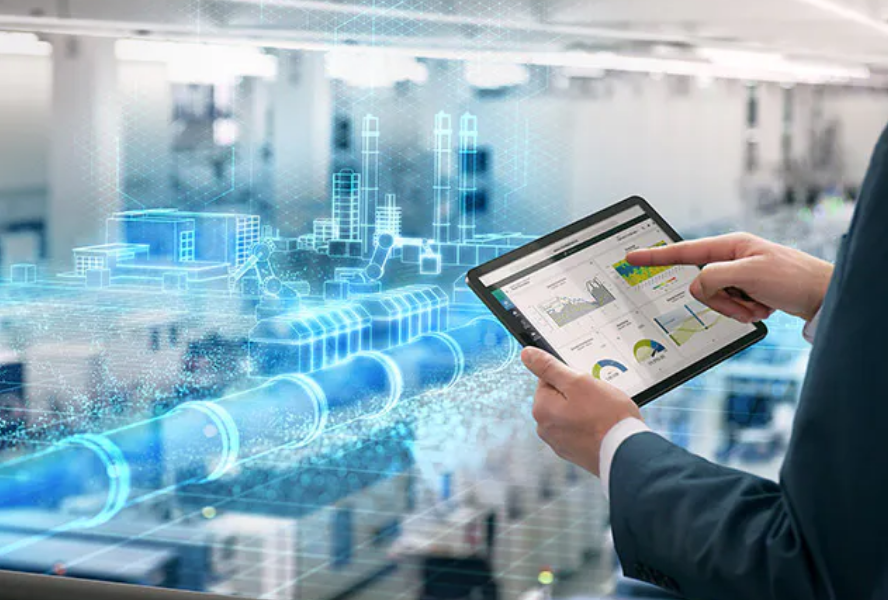
Siemens’ Xcelerator portfolio uses software to help companies innovate faster. (Image courtesy of Siemens)
Given the complexity and many actors in the automotive supply chain the training element alone could be gargantuan. Overall, the total support of this implementation will take a very long time. If Siemens pulls it off, however, they will have implemented its CAD solutions with a significant new client and be able to make the case for others to do so as well.
Siemens is keen to push its Digital Twin offering and the complete solution in managing files from inception to use across industrial firms. The Digital Twin is a key development that could grow out to become a completely new series of offerings, services, and functionalities that Siemens could build atop its existing offering, as well. Through the digital duplication of every part or perhaps even every input, they could track, analyze and optimize many manufacturing processes across the board. This would give manufacturing leaders more control over parts, processes and costs.
Digital Twins could, in theory, save companies considerably and may be the next frontier where the digital meets the actual world. But, even in the present world of CAD files, permissions, and collaboration being harnessed by PLM solutions like Teamcenter, there is a lot of opportunity to streamline collaboration and exchange. The task before Siemens and Hyundai and Kia is a difficult one but the rewards could be a more fluid collaboration for many decades.
Subscribe to Our Email Newsletter
Stay up-to-date on all the latest news from the 3D printing industry and receive information and offers from third party vendors.
Print Services
Upload your 3D Models and get them printed quickly and efficiently.
You May Also Like
3D Printing News Briefs, July 2, 2025: Copper Alloys, Defense Manufacturing, & More
We’re starting off with metals in today’s 3D Printing News Briefs, as Farsoon has unveiled a large-scale AM solution for copper alloys, and Meltio used its wire-laser metal solution to...
3DPOD 260: John Hart on VulcanForms, MIT, Desktop Metal and More
John Hart is a Professor at MIT; he´s also the director of the Laboratory for Manufacturing and Productivity as well as the director of the Center for Advanced Production Technologies....
3D Printing News Briefs, June 28, 2025: Defense Accelerator, Surgical Models, & More
In this weekend’s 3D Printing News Briefs, 3YOURMIND was selected to join an EU Defense Accelerator, and PTC has announced model-based definition (MBD) capabilities within Onshape. Finally, a study out...
EOS in India: AM’s Rising Star
EOS is doubling down on India. With a growing base of aerospace startups, new government policies, and a massive engineering workforce, India is quickly becoming one of the most important...