Day four is fantastic. Lots of people have left and stands remain almost devoid of annoying individuals. The Americans have gone to eat gravy, so its much quieter, as well. It’s the perfect time to examine the big stands, look at new parts, and inspect machines. I think of it kind of as the Trade Show Golden Hour. This is also the perfect time to catch up, reflect, ask people about what they’ve seen, and make sure that you didn’t miss that one new thing. Everyone is in a good mood, you can joke around with them, and it’s just a cozy afternoon still surrounded by machines. It’s perfect and I meet so many people again and I wish it will never end.
That’s a wrap at @formnext_expo! What a feeling to be back together as an industry, advancing #3Dprinting. BigRep was proud to be part of #formnext2021 and look forward to next year!#additivemanufacturing pic.twitter.com/n6iDqEaw2A
— BigRep – #3DPrinting (@BigRep) November 19, 2021
And over there, for the cost of $200,000 for four days at $5,550 an hour is a completely empty stand. And this stand has has been cleared out at mid-day with five hours to go because everyone wanted to catch a flight. I understand that. A.) its Friday and, B.) you may want to go home—but, still, this is a rather costly thing, to leave early. It’s a great way to check employee engagement, by the way—see who is still there and who has gone home.
Materials Trends
#Formnext saw us as protagonists among the #italian excellence: our samples in bio-compatible #ULTEM, large format #prototypes and end-use components.
_#3ntr #notoyshere #madeinitaly #piemontexcels #internationalization #additivemanufacturing #aerospace #mechatronics #3dprint pic.twitter.com/NRDjvFmYvL— 3ntr (@3ntr_Official) November 20, 2021
There was a lot more attention paid to polypropylene (PP) and the material kept coming up much more often than in previous years. In large scale printing, desktop fused deposition modeling (FDM), and powder bed fusion (PBF). I kept hearing about PP over and over again.
Arkema’s Rilsan PA 11 was the most mentioned and popular branded material. Again and again, I heard examples referring to it—the HEXR helmet and the castor beans. People love mentioning this material and the branding and recognition is excellent now. Companies are also asking about it by name because of its environmental credentials.
Filled materials are also still all the rage, especially polyamides. New polyamide grades are also entering into the market. Most requested materials came from people looking at biocompatible and safer photopolymers.
Granulate extrusion is discussed more, but precious few actually use it in manufacturing. However, given the cost differences, for some parts this could be a fast-advancing trend. Large-format 3D printing people seem utterly clueless about materials.
There are dozens of people selling the same Ti64 powders without any differentiation or explanation as to why you’d choose them. I understand that sphericality is good (to a certain extent), but why you?
Nobody takes bound metal extrusion seriously as a production technology. I really love it as a super low-cost method to make some parts. I see 3D printing as a portfolio of technologies where you’ll use powder bed for some parts, DED for others, binder jet for some, and bound metal extrusion for others. I know this doesn’t fit tidily into the visions of materials companies, but there is no one-size-fits-all technology and, by using them together, you can significantly reduce costs.
Maintenance, repair, and overhaul (MRO)—including maintenance generally, spare parts, and the redesigning out-of-production items—was something that I saw a lot of companies come for and mention. I met several businesses who were attending the fair to specifically buy equipment to produce low-volume, metal spare parts.
Bike helmets represent a key application, but aren’t there a lot more helmets we can be looking at? We should look much more broadly at sports equipment and safety gear.
Lattice structures are everywhere—even though they are inconvenient because they can be penetrated by pebbles and the like and we can’t predict their behavior.
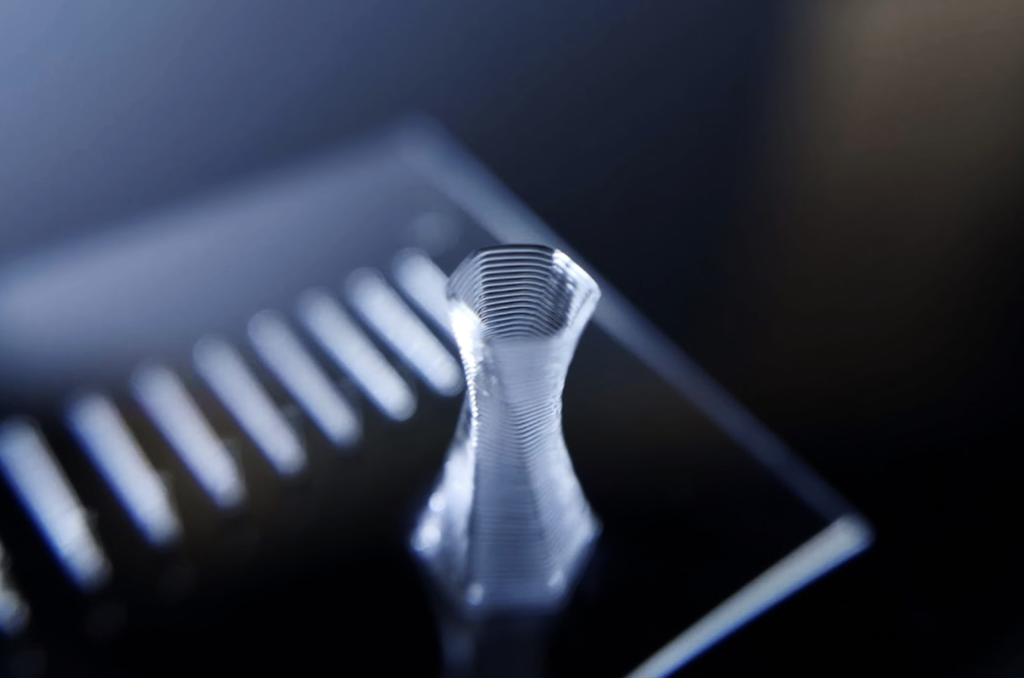
3D printed glass from Nobula. Image courtesy of Nobula.
Glass now seems much more attainable due to the new firm Nobula and the growing startup Glassomer. Both could usher in many new devices in the future.
#Formnext saw us as protagonists among the #italian excellence: our samples in bio-compatible #ULTEM, large format #prototypes and end-use components.
_#3ntr #notoyshere #madeinitaly #piemontexcels #internationalization #additivemanufacturing #aerospace #mechatronics #3dprint pic.twitter.com/NRDjvFmYvL— 3ntr (@3ntr_Official) November 20, 2021
Best New Material
The best new material was the Liquid Crystal Polymer filament made by NematX. Really excited by the potential this material has in RF shielding applications and parts such as antennae and radars.
Worry
People seem to worry about Desktop Metal’s ability to sustain its share price. There is concern that a collapse of DM could have retail investors sour on 3D printing forever or for a long time.
Optimism
Meanwhile, money seems to be cheap and free-flowing and people speak very easily about raising $5, $10 or $20 million. Loans are in the offing and people see an endless supply of capital on the horizon. This is unrealistic, but I am telling people to raise now because we’re unlikely to remain as popular as we are now forever.
Most Significant Development: Silicone
I love Spectroplast. Adore it, love it, love what it brings. WACKER’s ACEO could have done half of their applications years ago, but didn’t, leaving open a broad horizon of 3D printing applications in silicone for the this Swiss company. The parts look great, the properties look great and there are a lot of super exciting business development going on in medical, industrial and other areas. Elkem was also at the show offering extruded silicone. This means that there are now several ways to get silicone parts. I’m incredibly excited about the possibilities in medical, mass customization, gaskets, filtration, connectors and more. This is a huge volume opportunity that we have been unable to fulfill and Spectroplast is leading the charge.
New Development: Small Things
I was very impressed by the startup Atlant and their nanoprinting technique. But, I was also amazed by the many applications of UpNano‘s 2PP technology. We’re used to 3D Micro Print, mSLA and other techniques, but there are millions of devices and significant new advantages that can be gotten through nanoprinting. I really think that this scale has not gotten the attention it deserves.
Best Development at Formnext
The best development at Formnext was 4DBiomaterials. This British startup is developing a biocompatible, reabsorbable photopolymer with 800 MPa in tensile strength (no, not a typo). The material can be tweaked to be soft and flexible or stiff and could perhaps replace some bone or soft tissue. You could perhaps change the degradation as well so it could degrade in one month or five. The potential of this novel class of material is significant and it could lead to safer procedures, better orthopedic hardware, a replacement of PEEK and other polymer implants or new classes of devices and implants. Really significant development.
Subscribe to Our Email Newsletter
Stay up-to-date on all the latest news from the 3D printing industry and receive information and offers from third party vendors.
Print Services
Upload your 3D Models and get them printed quickly and efficiently.
You May Also Like
3D Printing News Briefs, July 2, 2025: Copper Alloys, Defense Manufacturing, & More
We’re starting off with metals in today’s 3D Printing News Briefs, as Farsoon has unveiled a large-scale AM solution for copper alloys, and Meltio used its wire-laser metal solution to...
3DPOD 260: John Hart on VulcanForms, MIT, Desktop Metal and More
John Hart is a Professor at MIT; he´s also the director of the Laboratory for Manufacturing and Productivity as well as the director of the Center for Advanced Production Technologies....
3D Printing News Briefs, June 28, 2025: Defense Accelerator, Surgical Models, & More
In this weekend’s 3D Printing News Briefs, 3YOURMIND was selected to join an EU Defense Accelerator, and PTC has announced model-based definition (MBD) capabilities within Onshape. Finally, a study out...
EOS in India: AM’s Rising Star
EOS is doubling down on India. With a growing base of aerospace startups, new government policies, and a massive engineering workforce, India is quickly becoming one of the most important...