A new partnership has formed between one of Germany’s leading makers of gardening equipment and patio furniture, Siena Garden, and Replique, a division of BASF, based on a project to provide what the companies are whimsically referring to as the “Eternal Spare Part”.
The co-founder and CEO of Replique, Dr. Max Siebert, noted in a press release, “Offering spare parts over a longer period of time is currently hardly possible due to high minimum order quantities, storage costs and one-sided procurement strategies.”
Peter Benthues, CDO of H. Gautzsche Firmengruppe, the parent company of Siena Garden, elaborated that, “Product life cycles are thus shorter than they could be. This not only leads to immense costs, but also contradicts the ethical principle of sustainability that Siena Garden has set.”
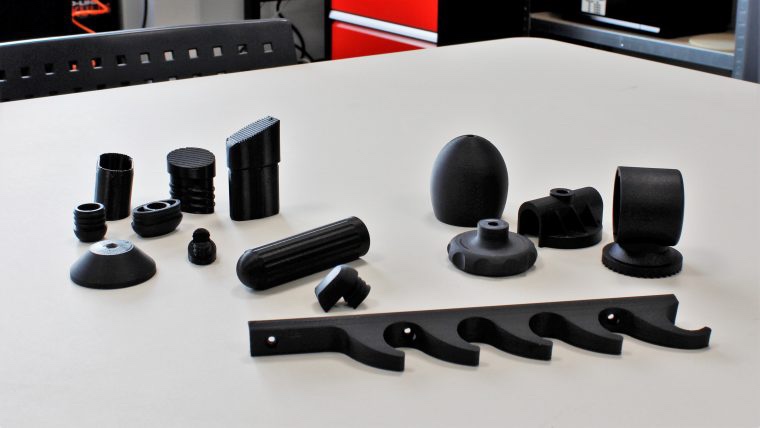
The way it works is simple: parts are stored digitally on Replique’s platform, and produced on demand. Anyone placing an order with Siena Garden for the part(s) will automatically have the order manufactured and delivered by one of Replique’s in-network producers. Storing the parts digitally means that even if the particular piece of furniture you order gets discontinued, certain parts that comprise the furniture—especially those most likely to become lost or damaged with normal use—can still be replaced. No more buying an entire replacement chair all because you lost one of the scratch-proof caps, or broke an arm rest because you were “sitting wrong” as my parents used to chastise me for doing.
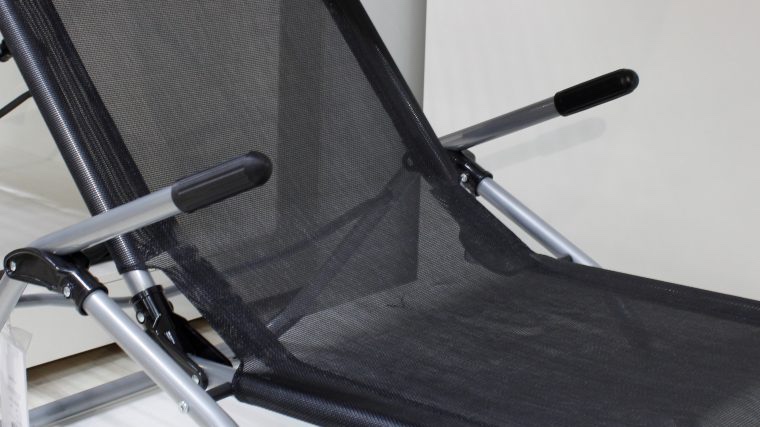
Stories about the supply chain and 3D printing have been multiplying since the very first days of the pandemic, and as the issues have increased, so too has the focus of leaders in the industry on precisely this advantage of 3D printing . In this respect, the greatest potential for upending the old/current way of doing business involves the steps towards creating networks of local hubs for on-demand production. So while this is a small step by a single company related to just one of its product lines, it’s likely that the model Siena Garden is applying here will be watched and replicated by plenty of other companies, sooner rather than later—especially given the involvement of BASF, by way of Replique. It starts with things like replacement parts, but you can easily imagine this spreading to the design model for patio furniture in general, not to mention other, more explicitly “essential” manufactures like cars. I see no reason why, if IKEA, for instance, insists on continuing to exist, it can’t at least eventually make all of its products on-demand, entirely using the eternal spare parts.

(Images courtesy of Incus Media)
Subscribe to Our Email Newsletter
Stay up-to-date on all the latest news from the 3D printing industry and receive information and offers from third party vendors.
Print Services
Upload your 3D Models and get them printed quickly and efficiently.
You May Also Like
Reinventing Reindustrialization: Why NAVWAR Project Manager Spencer Koroly Invented a Made-in-America 3D Printer
It has become virtually impossible to regularly follow additive manufacturing (AM) industry news and not stumble across the term “defense industrial base” (DIB), a concept encompassing all the many diverse...
Inside The Barnes Global Advisors’ Vision for a Stronger AM Ecosystem
As additive manufacturing (AM) continues to revolutionize the industrial landscape, Pittsburgh-based consultancy The Barnes Global Advisors (TBGA) is helping shape what that future looks like. As the largest independent AM...
Ruggedized: How USMC Innovation Officer Matt Pine Navigates 3D Printing in the Military
Disclaimer: Matt Pine’s views are not the views of the Department of Defense nor the U.S. Marine Corps Throughout this decade thus far, the military’s adoption of additive manufacturing (AM)...
U.S. Congress Calls Out 3D Printing in Proposal for Commercial Reserve Manufacturing Network
Last week, the U.S. House of Representatives’ Appropriations Committee moved the FY 2026 defense bill forward to the House floor. Included in the legislation is a $131 million proposal for...