The first mission to Jupiter’s Trojan asteroids is finally underway after NASA’s solar-powered spacecraft Lucy launched on an Atlas V rocket from Cape Canaveral Space Force Station in Florida on October 16, 2021. Designed, built, and tested by Lockheed Martin, the spacecraft is outfitted with a suite of advanced remote sensing instruments, autonomous software that enables tracking asteroid targets, and several 3D printed parts.
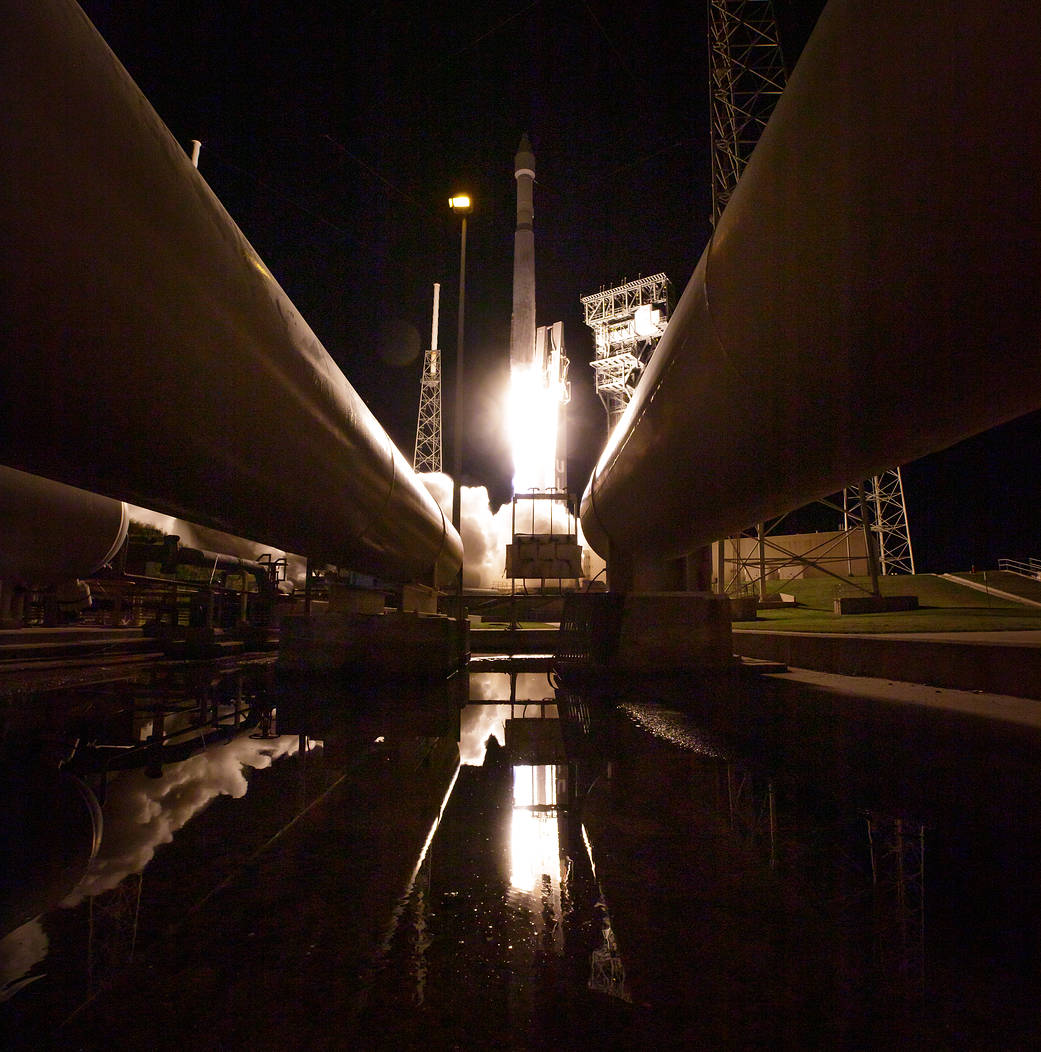
A United Launch Alliance Atlas V rocket with the Lucy spacecraft aboard launches from Space Launch Complex 41, Saturday, Oct. 16, 2021, at Cape Canaveral Space Force Station in Florida. Image courtesy of NASA/Bill Ingalls
Over the next 12 years, Lucy will travel four billion miles to explore a record-breaking number of asteroids, flying by one main-belt asteroid and seven Trojan asteroids that lead and trail Jupiter in its orbit. Named after the fossilized skeleton of one of the earliest known hominin (pre-human ancestors) found in Ethiopia in 1974, the Lucy mission will explore two swarms of Trojan asteroids that share an orbit around the Sun with Jupiter.
Scientists are keen for an up-close look at these ancient rocks, which are believed to be pristinely preserved leftovers from the formation of our outer solar system four billion years ago; studying them can reveal previously unknown information about their formation and our solar system’s evolution. By end-of-mission in 2033, Lucy will have visited a record number of destinations in independent orbits around the Sun.
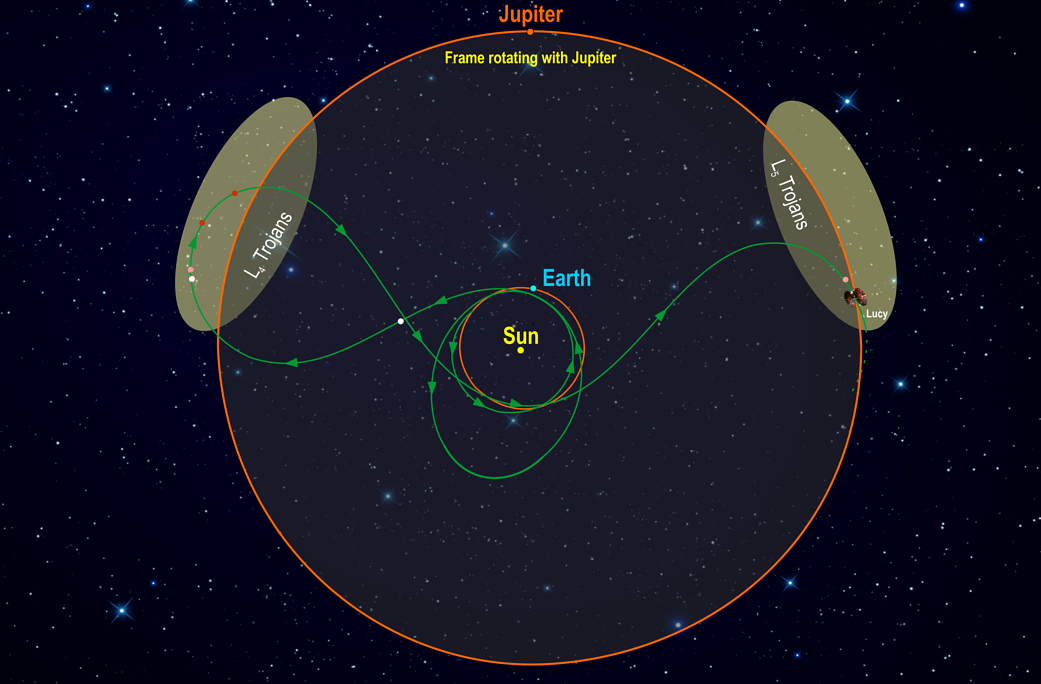
Lucy’s orbital trajectory is one of the most complex of any Discovery mission: 12 years, eight asteroids, and two Earth-gravity slingshots. Image courtesy of NASA/Southwest Research Institute
With such a long, unforgiving journey through space, Lucy’s engineers designed the spacecraft to be ready for anything. First off, the size is overwhelming: Lucy is over 52 feet (16 meters) from tip to tip. Still, most of that is the huge solar panels made by Northrop Grumman, each close to 24 feet, or over 7 meters, in diameter, and necessary to power the spacecraft’s systems as it flies out to the orbit of Jupiter. All the instruments, and the 6.5 feet (2 meters) high gain antenna needed to communicate with Earth, will be located on the much smaller spacecraft body.
Lucy draws on heritage design elements from previous Lockheed Martin-built missions like OSIRIS-REx, a NASA asteroid-study and sample-return mission, and MAVEN, an American spacecraft orbiting Mars to study the loss of its atmospheric gases to space. For this project, the team of experts at Lockheed Martin Space in Littleton, Colorado, that built the spacecraft included some 430 unique components, brought together by more than two miles of wire, 170 square feet of composite structure, and more than 12,800 electrical connections.
Lockheed made sure a robust thermal design protects Lucy from extreme space temperatures ranging from -250⁰F to 300⁰F, and that she is decked out with three powerful primary instruments to study geology, composition, and structure of the Trojan asteroids. Moreover, the team included advanced production parts like 3D printed brackets and harness clamps made from three different materials.
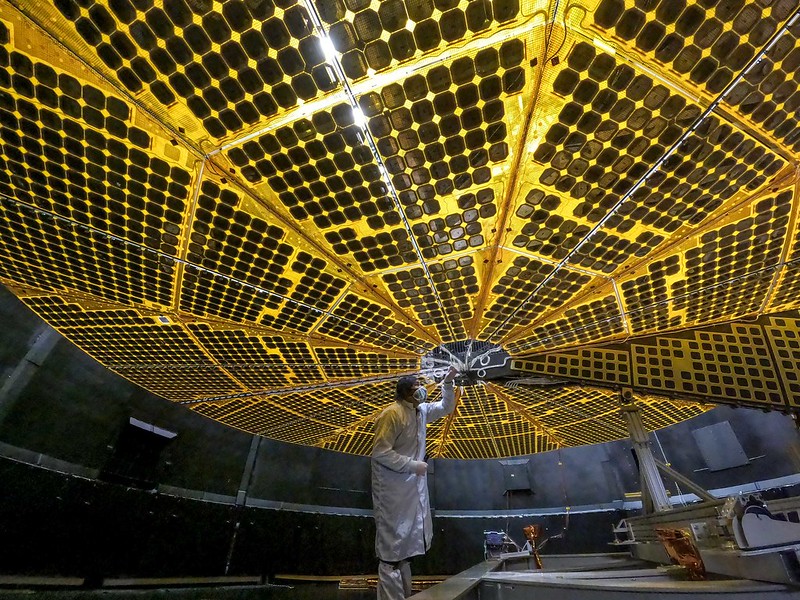
Lockheed Martin designed, built, and tested Lucy, here showing the spacecraft’s massive solar arrays after completing their first deployment tests. Image courtesy of Lockheed Martin.
However, Lucy is not the first interplanetary spacecraft to fly 3D printed parts. In 2011, another Lockheed-built planetary orbiter called Juno set out to explore and study Jupiter, fitted with a dozen 3D printed waveguide brackets made out of titanium alloy. The agency’s most distant planetary orbiter—until now—is still journeying through space and will continue its investigation of the solar system’s largest planet through September 2025.
For years, Lockheed has incorporated smart manufacturing components into its main factories across the US. The aerospace company even has its own dedicated 3D printing manufacturing center in California, the Additive Design and Manufacturing Center (ADMC). Created to bridge the gap between research and manufacturing, the ADMC has been using 3D technologies to build components for humanity’s continued exploration of space, including military satellites, 3D printed domes for high-pressure fuel tanks onboard satellites, and flight-worthy parts for space missions, like NASA’s Orion spacecraft that’s set to take humans to Mars. In 2018, the 6,775-square-foot 3D printing research center became the first to achieve its UL 3400 certification for additive manufacturing, having met all the safety and hazard-mitigation procedures for using and handling 3D printers and materials.
As part of its ongoing investment in 3D printing, Lockheed spent $350 million in a state-of-the-art satellite production facility, dubbed Gateway Center, complete with industrial-grade 3D printers and virtual reality design. Even the company’s Skunk Works division—in charge of building the world’s most experimental aircraft and breakthrough technologies in total secrecy—uses AM to improve processes and performance while lowering cost. In addition, the team has pioneered a variety of advanced materials and manufacturing technologies to create its high-speed and hypersonic concepts.
After working on the Lucy mission for more than six years, the spacecraft’s odyssey finally began. It is now traveling at roughly 67,000 miles per hour (108,000 kilometers per hour) on a trajectory that will orbit the Sun and bring it back toward Earth in October 2022 for a gravity assist. It will then take several years before Lucy gets to the first Trojan asteroid, but the mission’s principal investigator Hal Levison says these objects are “worth the wait and effort”: because of their immense scientific value, “they are like diamonds in the sky.”
Much like the 3.2-million-year-old Lucy skeleton fundamentally changed our understanding of human evolution, this mission aims to change the way we understand how the planets—including Earth—formed. No other space mission in history has been launched to as many different destinations in independent orbit around our sun, and the fact that it is leveraging AM is continued proof of the importance of additive technologies for the space industry and for eventually revolutionizing off-Earth exploration.
At the time of writing this article, NASA announced that only one of the solar arrays had fully deployed, while the other one only partially deployed. As a result, Lucy was settling into an Earth-orbiting cruise speed while top NASA experts tried to figure out how to solve the problem.
Subscribe to Our Email Newsletter
Stay up-to-date on all the latest news from the 3D printing industry and receive information and offers from third party vendors.
Print Services
Upload your 3D Models and get them printed quickly and efficiently.
You May Also Like
The Dental Additive Manufacturing Market Could Nearly Double by 2033, According to AM Research
According to an AM Research report from 2024, the medical device industry, specifically in dentistry, prosthetics, and audiology, is expected to see significant growth as these segments continue to benefit from...
Heating Up: 3D Systems’ Scott Green Discusses 3D Printing’s Potential in the Data Center Industry
The relentless rise of NVIDIA, the steadily increasing pledges of major private and public investments in national infrastructure projects around the world, and the general cultural obsession with AI have...
AM Research Webinar Explores Continuum’s Sustainable Metal Additive Manufacturing Powders
Metal additive manufacturing (AM) powder supplier Continuum Powders is working to develop solutions that empower industries to reduce waste and optimize their resources. An independent life cycle assessment (LCA) of...
3D Printed Footwear Startup Koobz Lands $7.2M in Seed Round
California-based Koobz is focused on reshoring the U.S. footwear supply chain with advanced manufacturing processes, including 3D printing. The startup just announced that it has added $6 million to its...