In the first part of this series, we looked at the example of a building facade, that may be comparatively expensive to 3D print, and placed it in the context of installation cost. We concluded that, if we optimize the design to reduce the installation cost, we could make a 3D printed facade much more price-competitive in the end.
On the whole, I have the feeling that there are design methodologies out there that are not considered enough. If they were, they could really aid us in disrupting traditional industry more thoroughly. We have a technology that is generally more expensive but much more plastic and versatile. By designing for our strengths, we can really be more competitive against mass manufacturing verticals. In this series, I’ll look at some design approaches that are not acted upon often enough in my opinion but could yet do much for us.
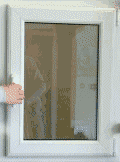
A tilt turn window.
Let’s consider as an example a hopper, also called tilted window, dual-action window, or tilt-and-turn window. First popularized in Europe these windows are made of a deceptively simple extruded aluminum or polymer design. However, a surprisingly complex mechanism ensures that, by changing your handle direction, you can open the window entirely to one side or just tilt it forward to open the top to let some air in. This means that a burglar can’t enter your house, but you can crack the window open to ventilate. At the same time, you can open it normally, should you need to.
This has two huge advantages over a window that would only be able to tilt: one, you could escape through it if you needed to evacuate your house in case of a fire, and, two, you can easily clean it. Through the magic of tilt-and-turn, you can turn the window inward and open it into your house. This means that you can very easily clean the inside and, more importantly, also safely clean the outside of your window from inside your house. This advantage is something that many older windows lack because they may only open outward. Not all tilt-and-turn windows open inward, but by opening sideways, they’re easier to clean than those that slide or don’t open fully. I love these windows because they are nice to use and also a great example of Design for Maintenance.

As this drawing shows contemporary windows are much more complex than one may consider. Often spaces in between double glazing are filled with Argon.
Here, we have an innovation that obscures complexity to give a homeowner an advantage of quicker and safer maintenance. These windows found wide-scale adoption because of the tilting feature and increased insulation in terms of reduced noise and reduced heat loss in the home. They will not immediately be cheaper, but in the long run will become less expensive.
With 3D printing, some mechanisms and design elements for these windows are being prototyped. We are seeing some small series use 3D printing in final products, as well. Our total part weight will never be a large proportion of something made of inexpensive aluminum profiles and glass. We can’t really deliver value in this application yet, outside of testing.
But what if we want to install such a new window in a very old house with uneven walls and issues related to the general levelness of things? Then, we will have a problem fitting our straight, extruded aluminum profiles into highly variable holes for windows that old houses have. Unless, of course, we can deploy 3D printing to make unique end caps for these profiles so they can change the angles of the window sides. We can also 3D print frames that make it so that the windows can be flush with the cavity.
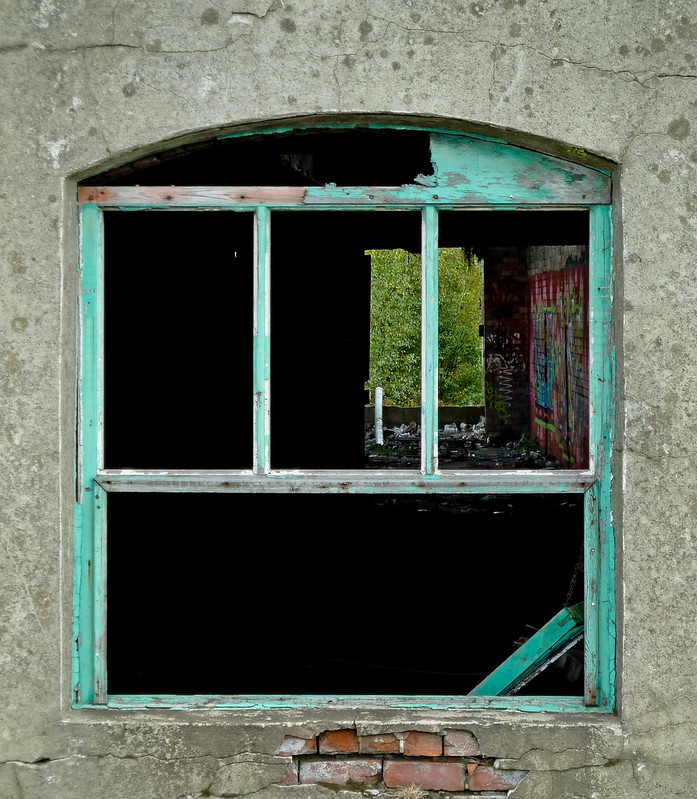
Image Tim Green.
So, now we can take a 3D printed form and solve problems for end customers. By making a standard product more plastic, we can get it to fit the needs of customers better. We could then also have a real design-for-installation optimization by making the windows faster to install, as well. This could be particularly useful for custom or non-standard window sizes, where 3D printing could play further roles in customizing the frames and installations.
In the case of the window, will we really accrue a design-for-maintenance benefit? Probably not. But, what if, for example, we looked at how these windows were washed. And we could see that, during washing, water splashed down on the windowsill and accumulated there. It would leave stains and may harm the paint in time. We could design a custom splash guard under the window to ameliorate this. Or we could make a runoff guide that would channel rain and other water off the window in an optimal way for each and every window. We could even 3D print custom squeegee rails, handles, and bars. Why would we do this? If, for the lifetime of the building, an individual comes and washes it for 20 hours every week for 50 years, this cost will add up.
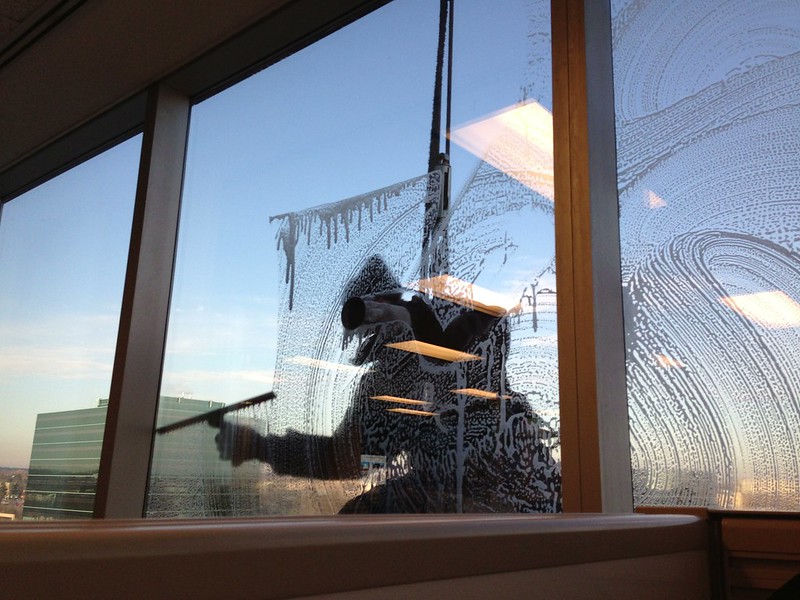
Image Chucka_NC
Normally, we’d never take that individual into account really, but imagine we did. We could offer a custom squeegee rail size that would cover the entire window in one swoop. Or we could make the squeegee exactly the right proportions so that the washer can clean it in two, smooth movements, saving them considerable time. This really would add up across the 52,000 hours of total window washing time. We could customize the grip to make them feel less tired or make the bar exactly the right size to speed up their work. We could add bumps to the bosuns chair to help speed up the lowering of the platform or add little markers on every window so that the worker can easily tell where to stop their platform at what height. We could add in a small grip on each window sill so they could steady themselves and be quicker to start and work harder. We could add a little whistle to the window so that wind rushing by would make a noise that deters birds from sitting and pooping there. We could add in small parts that give off a lot of UV light to deter birds from flying into the windows.
With 3D printing’s improvisational nature we can bring a lot of efficiency and improvements to maintenance situations in even the most common applications. Even when not taking inflation into account, we’re looking at $60 an hour, of over $3 million to wash the windows of the entire building. So, there is real scope for us to do something phenomenal with the very mundane.
Subscribe to Our Email Newsletter
Stay up-to-date on all the latest news from the 3D printing industry and receive information and offers from third party vendors.
Print Services
Upload your 3D Models and get them printed quickly and efficiently.
You May Also Like
Making Space: Stratasys Global Director of Aerospace & Defense Conrad Smith Discusses the Space Supply Chain Council
Of all the many verticals that have been significant additive manufacturing (AM) adopters, few have been more deeply influenced by the incorporation of AM into their workflows than the space...
EOS in India: AM’s Rising Star
EOS is doubling down on India. With a growing base of aerospace startups, new government policies, and a massive engineering workforce, India is quickly becoming one of the most important...
PostProcess CEO on Why the “Dirty Little Secret” of 3D Printing Can’t Be Ignored Anymore
If you’ve ever peeked behind the scenes of a 3D printing lab, you might have caught a glimpse of the post-processing room; maybe it’s messy, maybe hidden behind a mysterious...
Stratasys & Automation Intelligence Open North American Tooling Center in Flint
Stratasys has opened the North American Stratasys Tooling Center (NASTC) in Flint, Michigan, together with automation integrator and software firm Automation Intelligence. Stratasys wants the new center to help reduce...