There are multiple examples of 3D printing, 3D scanning, and other related technologies being used to help shed light on, and answer questions about, creatures that walked this planet long before we humans ever did. A pair of paleontologists from the University of Utah are just the latest to use 3D printed replicas and digital models to, as they put it, “de-fossilize” ancient animals in order to learn more about how they lived. David Peterman and Kathleen Ritterbush are part of a team of scientists that placed 3D printed reconstructions of fossil cephalopods (mollusks, like squids, with bilateral body symmetry and a set of tentacles) into water to better understand how the structure of their shells helped them swim.
“Thanks to these novel techniques, we can trudge into a largely unexplored frontier in paleobiology,” explained Peterman, a postdoctoral scholar in the university’s Department of Geology and Geophysics. “Through detailed modeling, these techniques help paint a clearer picture of the capabilities of these ecologically significant animals while they were alive.”
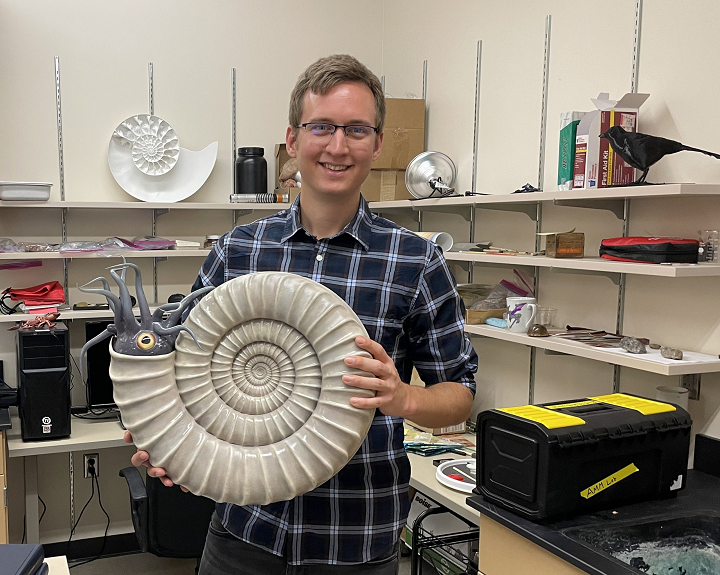
David Peterman in the Ammonoid Motility Modeling Laboratory (AMMLab) holding a 3D printed reconstruction of the planispiral ammonite, Paracoroniceras lyra.
Moving on from research about ammonoids with coiled shells, Peterman and Ritterbush, an assistant professor of Geology & Geophysics, focused this time on cephalopods with straight shells, or orthocones, and published a paper on their work. According to the fossil record, straight shells evolved multiple times, meaning they may have had what the researchers called “adaptive value.”
“This is important because orthocones span a huge chunk of time and are represented by hundreds of genera [plural of genus]. They were major components of marine ecosystems, yet we know very little about their swimming capabilities,” Peterman said.
Using 3D scans of Baculites compressus fossils—a species of orthocone from the Cretaceous period—the pair designed four different digital models with varying physical properties, using math to weight the structures of the models and represent the balance between soft tissue and air-filled voids that this orthocone likely had.
“The resultant model is balanced the same as the living animal, allowing very detailed analyses of their movement,” Peterman stated.
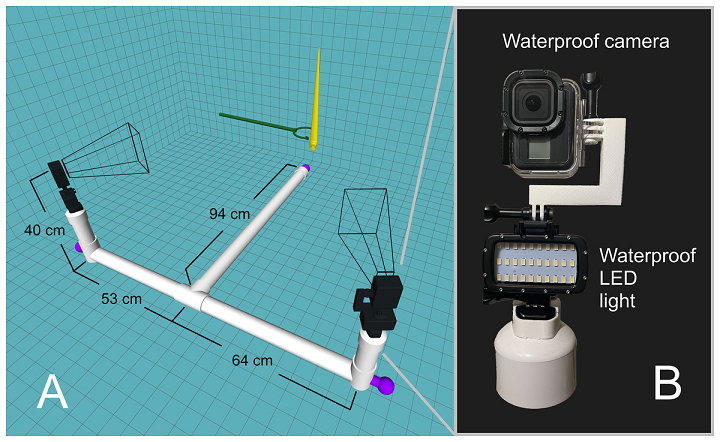
Figure 2: Underwater camera rig used for 3D motion tracking. (A) Schematic of the camera rig relative to the model (yellow) and release mechanism (green). The rig was made strongly negatively buoyant with three steel counterweights at the ends (purple). The wireframe shapes radiating from the cameras denote the approximate field of view. (B) Close-up view of waterproof camera and LED light with custom, 3D printed attachments.
With help from Mark Weiss and Emma Janusz at the university’s George S. Eccles Student Life Center, Peterman and Ritterbush set up a camera rig, featuring 3D printed attachments, in seven feet of water, and then released the two-foot-long models underwater to observe their natural movements. As side to side motions created drag, the most efficient way to move was vertically.
“I was surprised by how stable they are. Any amount of rotation away from their vertical orientation is met with a strong restoring moment so many species of living orthocones were likely unable to modify their own orientations,” Peterman said. “Furthermore, the source of jet thrust is situated so low that, during lateral movement, much energy would be lost due to rocking.”
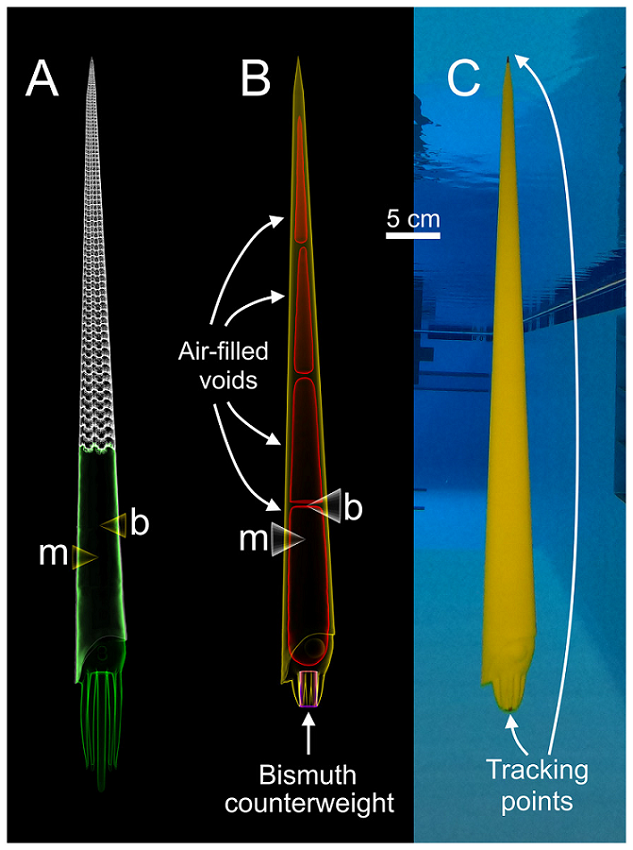
Figure 1: Construction of a physical, 3D printed model of Baculites compressus from a virtual hydrostatic model. (A) Virtual model used to determine hydrostatic properties (modified from Peterman et al., 2019). (B) Virtual model with simplified internal geometry that allows for 3D printing. The total model mass was manipulated to impart an upward buoyant force, simulating downward thrust. The total center of mass (m) relative to the center of buoyancy (b) was maintained with an adorally placed counterweight and various internal voids. (C) Physical, 3D printed model with tracking points placed at the distal ends of the arms and apex used for 3D motion tracking.
These experiments in the pool showed that orthocones could reach high enough velocities that they were likely able to rapidly jet up and away from slower-moving predators, as well as catch food more easily. The results also showed that most orthocone species would have been unable to live a lifestyle that required horizontal swimming.
Additionally, the two paleontologists worked with recent graduate Nicholas Hebdon, along with Ryan Shell from the Cincinnati Museum Center, on experiments revolving around the underwater motion of torticones, which are smaller cephalopods with spiral shells; the results will be published in the American Association of Petroleum Geologists and a memorial volume of the Wyoming Geological Association for late paleontologist William Cobban, who died in 2015.
“While orthocones were masters of vertical movement, torticones were masters of rotation,” Peterman explained.
Torticones probably also swam vertically, but with a slight spin. As opposed to crawling along the ocean floor like present-day mollusks, the shape of their chambered shells led to a different result in the water. The researchers released the 3D printed, six-inch-long torticone models into a 50-gallon water tank and discovered that they rotated naturally, efficiently spinning face-first when swimming down and switching directions when going back up.
“I was surprised at how easily torticones could rotate. Even small thrusts such as breathing [gill ventilation] could have produced rotation of 20 degrees per second,” Peterman said.
Because they spun while descending, torticones were likely able to more easily graze on food this way.
“These experiments transform our understanding of ancient ecosystems. Rather than crawling along the seafloor like snails, or swiftly swimming like modern squid, these animals were assuming rather unique lifestyles,” Peterman concluded. “These experiments refine our understanding of these animals by painting a picture of ancient seascapes dotted with pirouetting helical cephalopods and vertically-oriented orthocones.”
(Source/Images: University of Utah)
Subscribe to Our Email Newsletter
Stay up-to-date on all the latest news from the 3D printing industry and receive information and offers from third party vendors.
Print Services
Upload your 3D Models and get them printed quickly and efficiently.
You May Also Like
Reinventing Reindustrialization: Why NAVWAR Project Manager Spencer Koroly Invented a Made-in-America 3D Printer
It has become virtually impossible to regularly follow additive manufacturing (AM) industry news and not stumble across the term “defense industrial base” (DIB), a concept encompassing all the many diverse...
Inside The Barnes Global Advisors’ Vision for a Stronger AM Ecosystem
As additive manufacturing (AM) continues to revolutionize the industrial landscape, Pittsburgh-based consultancy The Barnes Global Advisors (TBGA) is helping shape what that future looks like. As the largest independent AM...
Ruggedized: How USMC Innovation Officer Matt Pine Navigates 3D Printing in the Military
Disclaimer: Matt Pine’s views are not the views of the Department of Defense nor the U.S. Marine Corps Throughout this decade thus far, the military’s adoption of additive manufacturing (AM)...
U.S. Congress Calls Out 3D Printing in Proposal for Commercial Reserve Manufacturing Network
Last week, the U.S. House of Representatives’ Appropriations Committee moved the FY 2026 defense bill forward to the House floor. Included in the legislation is a $131 million proposal for...