After the aerospace and medical sectors, industrial manufacturing is the largest segment using 3D printing, according to the “Market Opportunities for Additive Manufacturing in the General Industry and Tooling Sector-2020-2029” report from SmarTech Analysis. For that reason, the additive manufacturing (AM) market research firm anticipates steady growth in the sector amounting to approximately $5.48 billion in revenues by 2029.
It is, therefore, no surprise that the Australian Meat Processor Corporation (AMPC) is now working with Markforged and Konica Minolta to establish a 3D printing service for red meat processors across the Australian continent. The service is meant to allow these companies to quickly 3D print equipment parts to improve maintenance procedures and prevent factory downtime. Specifically, AMPC will be 3D printing bolts and rollers, replacing spares, but also improving on existing designs.
The AMPC is a research and development corporation dedicated to the red meat processing industry in the country. As such, it uses processor taxes, private funds, and financing from the Australian government to run its R&D and marketing programs. Such a company has an outsized role in a country like Australia, which is the largest exporter of goat meat and second largest exporter of beef and sheep in the world. In 2018 to 2019, the nation generated $17.6 billion in the red meat and livestock trade, about 1.4 percent of GDP.
Konica Minolta (TYO: 4902) is an approximately $9 billion Japanese multinational that manufactures industrial printers and other imaging-related equipment, such as 3D measurement tools. Its main activity in the 3D printing space has been as a reseller of equipment from companies like 3D Systems and Markforged. It has a substantial global footprint, with several locations in Australia.
The three-year program will see the three businesses working together to see how AM can be used at meat processing plants around the continent. Two mobile Markforged X7 carbon fiber 3D printers will be sent to plants around Australia for four to eight weeks at a time, where staff will be trained in their use and determine whether buying the machines will be worthwhile. Konica Minolta staff will be on-site to provide support as they test out the equipment, which will include the production of non-metal parts and pre-metal prototypes.
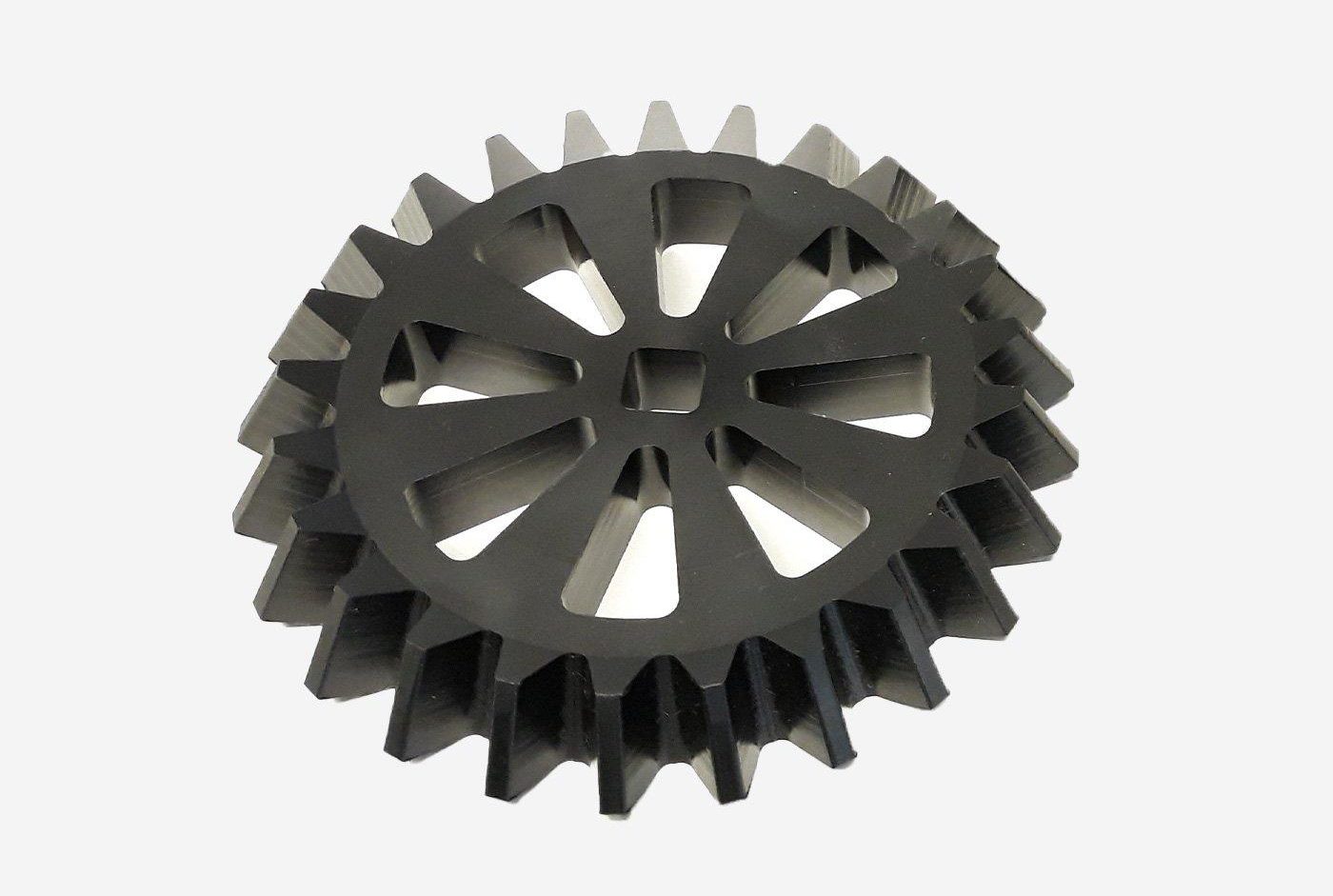
A 3D printed gear made from continuous carbon fiber using Markforged technology. Image courtesy of Markforged.
A Metal X 3D printer will also be housed at Konica Minolta’s Sydney location where it will be used to produce parts for the red meat industry. Plastic prototypes made at the processing plants can be delivered to this facility for Konica experts to produce metal counterparts, including stainless steel, in just two days. This will also result in a 3D printable parts database for the red meat industry that will be quality controlled.
“The need for sovereign capability for the Australian supply chain coupled with Australian government support for local food and beverage manufacturing has resulted organisations looking to adopt innovative practices. Konica Minolta Australia is proud to partner with AMPC in getting this world-first capability off the ground,” said Matthew Hunter, Innovation Product Marketing Manager at Konica Minolta. “When it comes to meat processing, there are a number of challenges for equipment maintenance. This includes the use of old equipment with limited spare part availability and the need to produce custom parts. 3D printing helps address these challenges. Through the database, AMPC’s member organisations will have access to intellectual property to expediate and streamline their repairs processes.”
“Meat processors rely on a multitude of equipment, with multiple components. Even a small component failure can be a costly exercise. The ability to simply print a replacement part could drastically reduce downtime and minimise the need to wait for parts, reducing the chance of supply being at risk,” said Chris Taylor, CEO of AMPC. “The processing sector is part of an ecosystem that performs best when all parts are optimised. Although established and dedicated for Australian red meat processors, AMPC will make the 3D printing hub available for other Australian food, agriculture, and manufacturing sectors to evaluate their needs and opportunities for 3D printing within their supply chains.”
The meat industry accounts for 15 percent of total greenhouse gasses (GHG), largely from the methane released by livestock, which is roughly equal to the amount of CO2 generated by gas vehicles globally. Given the importance of the industry in Australia, a nation that is being hit by extreme heat and fires exacerbated by global warming by about 30 percent, the red meat and livestock industry has set a goal to be carbon neutral by 2030.
Carbon neutrality is, of course, a concept fraught with problems, as it often involves offsetting emissions by planting trees, unproven technologies, or other schemes that don’t exactly balance out industrial GHG production. Unlike transportation, which can more easily replace problem technologies with renewables, it is the animals themselves that account for the methane from the meat trade.
So, while 3D printing may aid in modernizing what often appears to be an outdated industry, it will likely not contribute greatly to the modernization necessary to reduce that segment’s emissions. However, it is quite interesting that such a sector is adopting AM with such a unique model, one that could be exported to other sectors where 3D printing could have a greater impact on emissions.
AMPC will first test the waters by sending 3D printers around the country, but it will also build up a quality-controlled database of relevant parts. Meanwhile, a metal 3D printer at Konica will be able to produce spares on the fly as they are needed. Konica and Markforged could deploy a similar strategy to other industries, such as the transportation sector, which will result in customers buying the equipment. And, who knows, maybe, as the meat industry increases investments into alternative meat production, maybe they will similarly use 3D printing for their meat 3D printers and bioreactors, as well.
Subscribe to Our Email Newsletter
Stay up-to-date on all the latest news from the 3D printing industry and receive information and offers from third party vendors.
Print Services
Upload your 3D Models and get them printed quickly and efficiently.
You May Also Like
Making 3D Printing Personal: How Faraz Faruqi Is Rethinking Digital Design at MIT CSAIL
What if your 3D printer could think more like an intelligent assistant, able to reason through a design idea, ask questions, and deliver something that works exactly the way the...
Reinventing Reindustrialization: Why NAVWAR Project Manager Spencer Koroly Invented a Made-in-America 3D Printer
It has become virtually impossible to regularly follow additive manufacturing (AM) industry news and not stumble across the term “defense industrial base” (DIB), a concept encompassing all the many diverse...
Heating Up: 3D Systems’ Scott Green Discusses 3D Printing’s Potential in the Data Center Industry
The relentless rise of NVIDIA, the steadily increasing pledges of major private and public investments in national infrastructure projects around the world, and the general cultural obsession with AI have...
Formlabs Teams Up with DMG MORI in Japan
In late June, Nick Graham, Chief Revenue Officer at Formlabs, announced on LinkedIn that the company had partnered with DMG MORI, one of the world’s leading machine tool companies, to...