3D printing is playing an increasing role in the production of spare parts for public transportation and mass transit, particularly in countries outside of the U.S., where those sectors are critical for the livelihood of their residents. Among the technologies being used is fused deposition modeling (FDM) from Stratasys (Nasdaq: SSYS), which is now being deployed for passenger trains in the U.K. and high-speed rail in Russia. The latest case study comes from Italian engineering company 3DnA S.r.l, which is using FDM to 3D print replacement parts on-demand for Neapolitan public transport company Azienda Napoletana Mobilità S.p.A (ANM).
ANM is responsible for controlling all of public transportation for Napoli, including its trolleybuses. When a critical part for linking the vehicles to the aerial power supply lines were found to be broken, the company turned to 3DnA and 3D printing. Replacements for the buses’ trolley heads could not be found on the market as the vehicle fleet has been in operation for such an extended period of time.
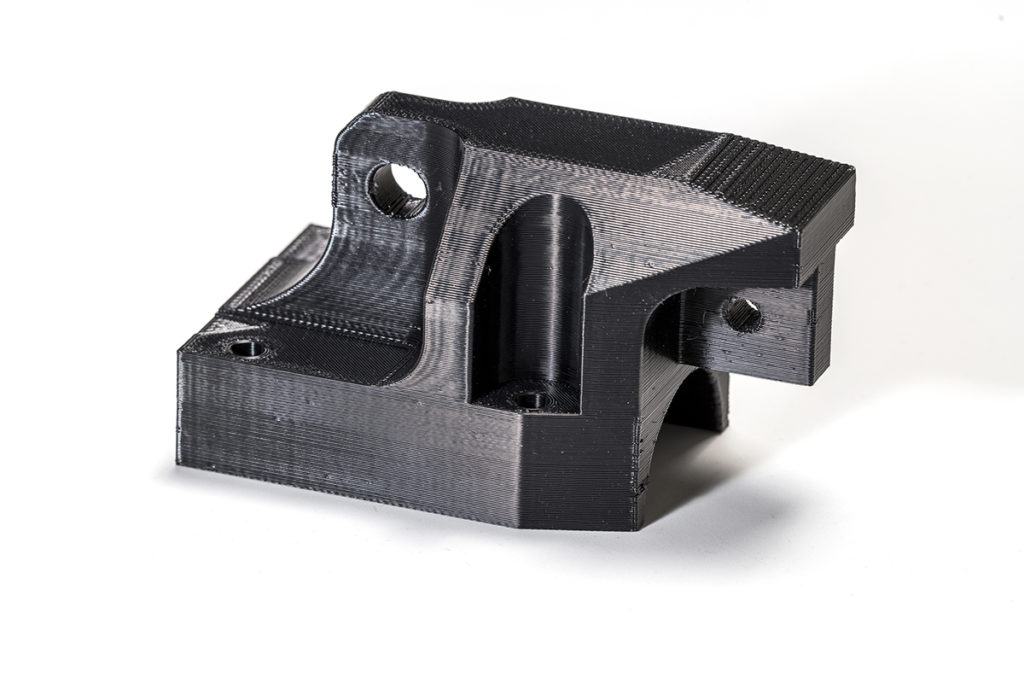
3D printed spare to replace trolley head component. Made from ULTEM to withstand daily rigor and maintain electrical insulation. Image courtesy of Stratasys.
To avoid significant downtime for the trolleybus line, 3DnA relied on the large-scale Stratasys F900 3D printer to produce replacement parts more quickly than would be possible with traditional technologies. In fact, by using 3D printing to produce spare parts, 3DnA and ANM demonstrated that vehicle downtime could be cut by 95% compared to conventional methods of obtaining spares.
“Creating the trolley heads with traditional manufacturing processes would have taken up to 12 months, resulting in a lengthy downtime for the vehicle that is simply not an option,” explains Alessandro Manzo, 3DnA’s General Director. “Using our F900, we were able to produce and deliver about 20 of the most critical parts of the trolley head in two weeks, enabling ANM to eliminate further risk of downtime to its fleet and ensure reliable transportation for the three million citizens of Naples. Overall, having this level of production flexibility is extremely important to ANM, as it can now order parts based on actual needs as opposed to warehousing large quantities of costly inventory.”
To create the replacements, 3DnA reverse engineered the trolley heads with 3D scanning. Moreover, the company redesigned the component such that, in the case of future damage, only a small piece would need to be replaced and not the complete part. The new design features a core metal structure and a 3D printed exterior casing to link the trolley head to the aerial wires.
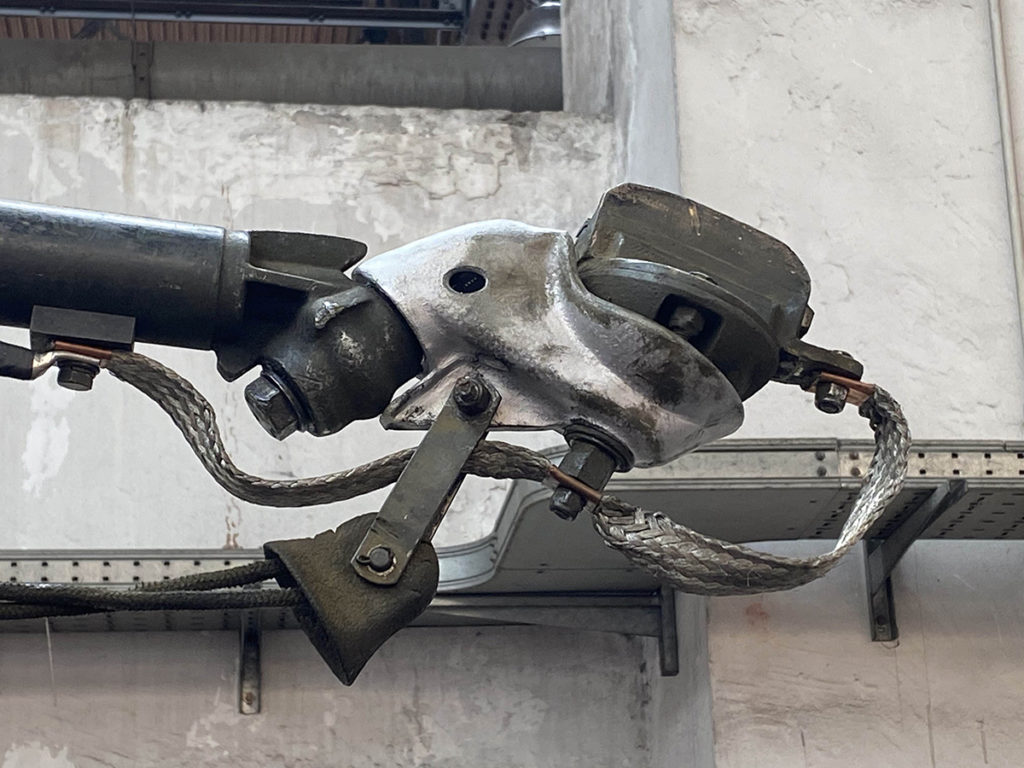
New 3D printed trolley head in action, connecting the trolleybus to the supply line. Image courtesy of Stratasys.
“The innovative new design was so well received that ANM has now decided to replace the trolley heads across the entire trolleybus fleet with the new 3D printed version,” continues Manzo. “Without the ability to produce parts with such a high-level of accuracy this would not have been possible. That is where the beauty of the F900 comes in – not only do you get supreme part accuracy, but it’s backed up by a level of repeatability unrivaled in the industry.”
The casing was made using ULTEM 9085, giving it the structural integrity needed for rigorous daily use as well as the electrical insulation required to meet the standards of trolleybus operation.
Manzo explained: “The part cannot conduct electricity, so having this material is essential. In addition, ULTEMTM 9085 resin provides us three key criteria required for end-use transportation applications: excellent heat resistance with a heat deflection temperature of 153°C, it is a flame-retardant thermoplastic, and offers a very high strength-to-weight ratio.”
Due to the success of the project, 3DnA believes that 3D printing could be used to produce spares across Italy and in other transportation applications. In fact, it already has been used in a variety of public transit cases. In addition to the two Stratasys stories linked to above, additive is growing in adoption across the railway industry, in part thanks to the Mobility Goes Additive in Europe, which has linked together numerous stakeholders in rail to ensure 3D printing is used where appropriate and that standards are properly developed. Wabtec is also pushing the use of the technology, both in the U.S., as well as abroad.
Subscribe to Our Email Newsletter
Stay up-to-date on all the latest news from the 3D printing industry and receive information and offers from third party vendors.
Print Services
Upload your 3D Models and get them printed quickly and efficiently.
You May Also Like
U.S. Navy Lab Uses 3D Printing to Reduce Tooling Lead Time By Over 90%
The F-35 Lightning II Joint Program Office (JPO), responsible for life-cycle management of the key fifth-generation joint strike fighter (JSF) system used by the U.S., its allies, and its partners,...
Etsy Design Rule Change Reduces Selection of 3D Printed Goods
Online marketplace Etsy has implemented a rule change requiring all 3D printed goods on the site to be original designs. The update to the site’s Creativity Standards states, ¨Items produced using...
Honeywell Qualifies 6K Additive’s Nickel 718 for 3D Printed Aerospace & Defense Parts
6K Additive is renowned for manufacturing sustainable additive manufacturing (AM) powder, and offers a wide portfolio of premium metal and alloy powders that include titanium, copper, stainless steel, and nickel,...
MetalWorm Sells WAAM Systems to Research Institutes in Brazil and Malaysia
Turkish WAAM firm MetalWorm has sold a system in Malaysia and another in Brazil. This is an excellent example of a few emerging trends in additive. Firstly, WAAM was experimented...